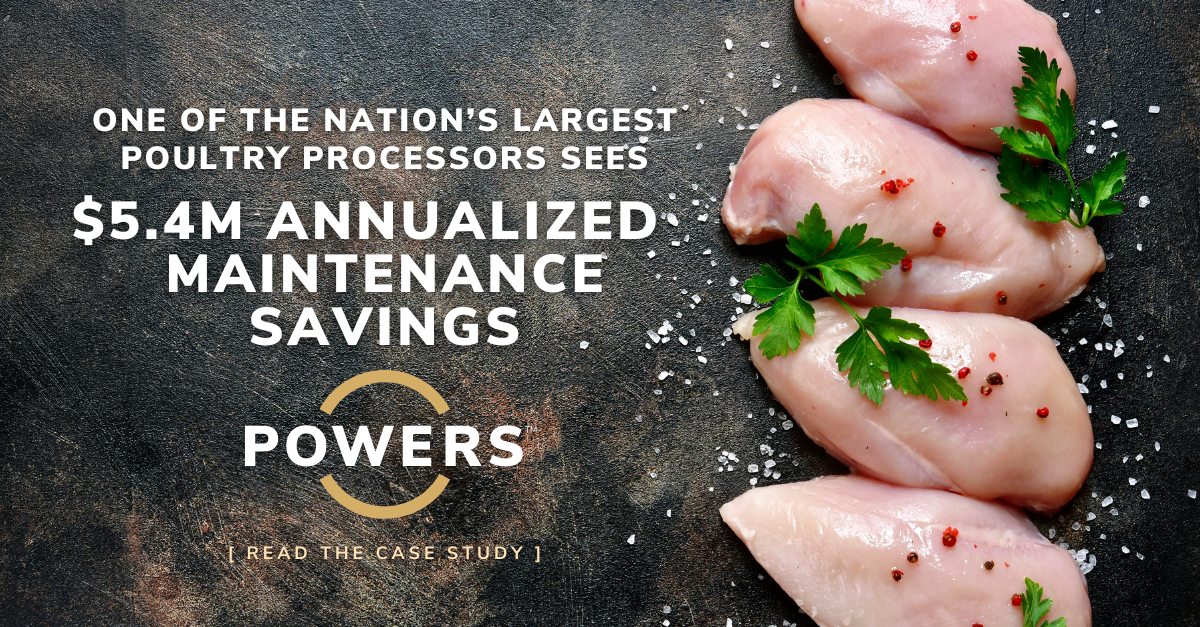
Our client faced significant maintenance improvement and performance issues: hiring qualified technicians, high turnover, poor practices, unqualified management promotions, and an overall negative workplace culture.
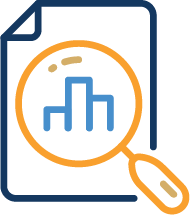
Project Overview
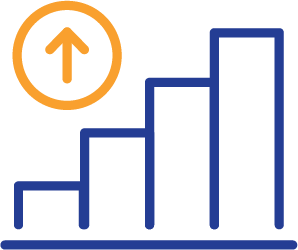
Performance Results
Situation
Our client, one of the nation’s leading poultry processors, broke ground on a new production facility in the middle of the country in late 2019.
Unfortunately, the new plant immediately experienced difficulties filling positions, in small-town America, in a tight job market.
Finding qualified maintenance technicians an hour away from the closest metropolitan area proved to be a challenging task. As a result, the company’s COO lamented, “we are hiring electricians who are unable to wire up a motor.”
In addition to having a relatively untrained maintenance staff, the supervisors and managers were promoted into their positions because they did have maintenance skills. However, they were not selected because of their management skills.
This promotion strategy resulted in a gap in the effectiveness of follow-up and coaching. Supervisors tended to “do” rather than coach and train their teams.
The culture within the facility was also negative in nature. Ineffective communication of the mission statement and goals of the organization resulted in people coming to work every day and doing what they thought was best, with no understanding of the desired results. Some prioritized their individual goals over those of the team.
Due to the lack of maintenance skills and supervisory follow-up, turnover at the facility was above 58% in 2022, resulting in a constant cycle of hiring and training.
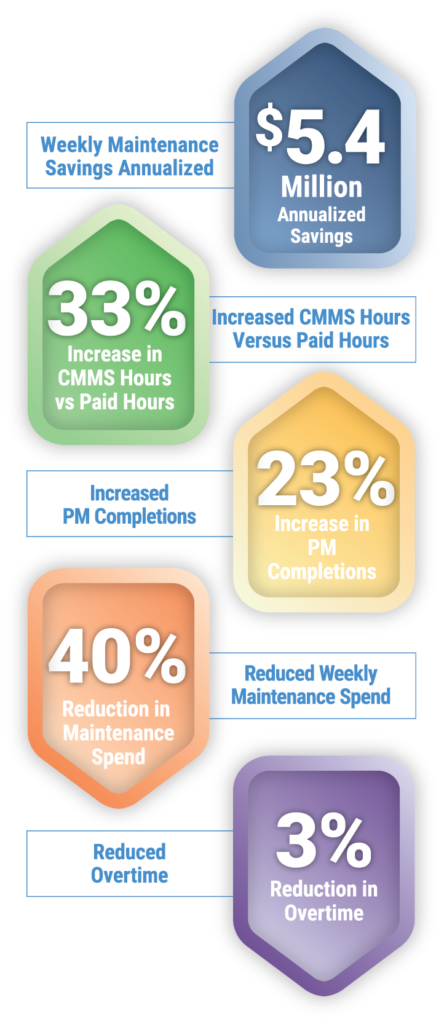
Maintenance Improvement Proves to Be Much-Needed Performance Boost for One of the Nation’s Largest Poultry Processors
Our client faced significant maintenance performance issues: hiring qualified technicians, high turnover, poor practices, unqualified management promotions, and an overall negative culture.
Background
Our client is a large-scale poultry processor for one of the largest mass-market retailers in the world. Their recently completed, state-of-the-art facility was brought on line to serve the retailer’s commitment to providing only the highest quality products for its customers.
Despite its relatively short time in business, this facility has grown to be one of the region’s largest poultry producers and a welcome boon to the surrounding community.
Situation
Our client broke ground on this new production facility in the middle of the country in late 2019.
Unfortunately, the new plant immediately experienced difficulties filling positions, in small-town America, in a tight job market.
Finding qualified maintenance technicians an hour away from the closest metropolitan area proved to be a challenging task. As a result, the company’s COO lamented, “we are hiring electricians who are unable to wire up a motor.”
In addition to having a relatively untrained maintenance staff, the supervisors and managers were promoted into their positions because they did have maintenance skills. However, they were not selected because of their management skills.
This promotion strategy resulted in a gap in the effectiveness of follow-up and coaching. Supervisors tended to “do” rather than coach and train their teams.
The culture within the facility was also negative in nature. Ineffective communication of the mission statement and goals of the organization resulted in people coming to work every day and doing what they thought was best, with no understanding of the desired results. Some prioritized their individual goals over those of the team.
Due to the lack of maintenance skills and supervisory follow-up, turnover at the facility was above 58% in 2022, resulting in a constant cycle of hiring and training.
Discovery
During our initial Project Discovery phase, the POWERS team observed that supervisors were only spending 18% of their day supervising their technicians actively, which resulted in low technician productivity and inefficient use of time.
Technicians were assigned a weekly bucket of PM Work Orders and allowed to make decisions on what work to prioritize and perform. As a result, technicians self-managed the workload and received little feedback on their performance from their supervisors.
If PM work orders were not completed, they were closed by the Supervisor at the end of the week and reopened at the next scheduled frequency by the CMMS system.
Before the project's start time, maintenance management had abandoned all startup and shutdown checklists. This behavior was surprising, considering the $450 million investment in automated equipment just three years earlier.
Technicians came to work every day and did what they thought was best. Every day was based on tribal knowledge and best intentions.
The Plan
To address these issues, the maintenance organization implemented a significant number of changes based on coaching from POWERS.
The elephant in the room needed to be addressed. Establishing a link to the goals and strategies of the organization was a critical step. All leadership contributed to a group workshop in which they designed the organization’s new Mission Statement and Key Tenets.
This vital process gave them a direct link to the company’s goals and strategies and helped them build energy when establishing the desired culture within their teams.
One of the critical Key Tenets the team agreed to implement is called “Robust Dialogue.” This communication structure established the core beliefs that we are all on the same team and comfortable talking about difficult subjects because we all want to win together.
POWERS increased the frequency of supervisor check-ins with technicians, established clear job expectations and responsibilities, and provided additional training and support to improve technician skill sets.
The organization also implemented a new scheduling system to improve the allocation of resources and streamline work processes, with a weekend crew dedicated to performing Preventative Work Orders during windows of availability.
Maintenance Spend was transformed from a rear-view mirror approach to one that looked at open POs in the coming months. Reactive decisions were transitioned to a proactive understanding of budgets aligned with available resources.
The Results
- 100% Safety Training Compliance: Improved 9.1%
- Startup Success Greater Than 90%: Improved 7%
- Maintenance Spend Less Than $187,000 Per Week: Improved 39.5%
- Achieve PM Completion of 80%: Improved 22.6%
- Audit more than 10% of PM Work Orders: Improved 0.3%
- Complete 60% of Corrective Work Orders: Improved 17.0%
- Achieve 60% CMMS Hours vs Paid Hours: Improved 33.4%
- Overtime Less Than 10%: Improved 3.0%