AMP Up Your Approach to Maintenance Performance Improvement
“Unexpected maintenance issues result in downtime, lost capacity, and cost our company a lot of time and money. How can we improve our maintenance performance?”
The POWERS AMP (Advanced Maintenance Performance) Program Increases OEE and Reliability, Reduces Labor Costs, and Improves the Bottom Line
Transforming manufacturing operational performance requires analyzing the systems, processes, and behaviors woven into the fabric of an organization, from inputs to outputs, from the top floor to the shop floor. One area that should be on every organization’s radar for improvement is maintenance performance or MRO (Maintenance, Repair, and Operations). No other area of your operation can take such a big bite out of the bottom line. That’s why we’ve launched a new end-to-end solution for maintenance performance improvement.
Our AMP (Advanced Maintenance Performance) Program improves both the tactical and technical aspects of maintenance in your operation. On the tactical side, we focus on improving your strategic approach to maintenance and your Maintenance Management Operating System: how you manage the people and resources devoted to maintaining your assets and equipment.
We also focus on the technical aspects of maintenance and provide hands-on training in Maintenance Fundamentals, Mechanical Concepts, Electrical Power, and Electrical Control. Nearly 60% of the current manufacturing maintenance workforce does not possess the skills and training necessary to keep the assets and equipment functioning at optimum levels. Improving your maintenance team’s skills unlocks OEE (Overall Equipment Effectiveness) bottlenecks in uptime, throughput, capacity, quality, and more.
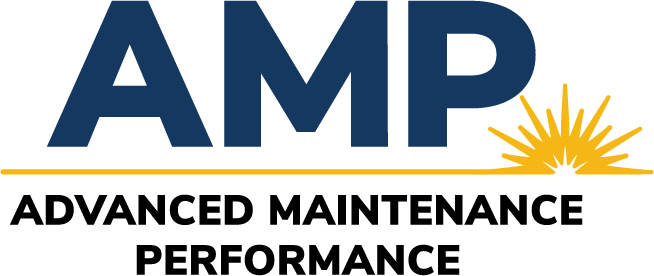
Our AMP Program is a Tactical and Technical Deep Dive into Improving OEE by Energizing Your Maintenance Team
We Start With the Tactical: Your Teamwork Skills and Maintenance Management Operating System
The tactical side of our AMP (Advanced Maintenance Performance) Program focuses on improving how your maintenance team works together and your overall MMOS (Maintenance Management Operating System) to drive long-term OEE improvement. With our AMP Program, your maintenance team will learn more effective leadership and communication skills, such as short-term interval follow-up, driving accountability, positive conflict resolution, and more. We also improve your overall MMOS fundamentals like better planning, scheduling, labor assignment, and resource allocation.
These so-called soft skills and tactical thinking skills are often weak areas for maintenance department personnel and frontline leadership. So we teach, train, and coach on fundamentals like effective communication, accountability, inspiring higher performance, and more.
Our MMOS improvement plan digs deep into how your maintenance department operates. Our assessment uncovers opportunities to improve systems and processes, as well as the overarching management system, to achieve critical performance improvements that are rapid, sustainable, and scalable. When our team’s time on your shop floor ends, you’ll have a highly-detailed and fully implemented MMOS to deliver peak performance and optimize OEE.
Tactical Training
- Leadership Skills & Behaviors
- Training & Growth
- Maintenance Management Operating System (MMOS)
- CMMS, Technology & Systems
- Maintenance Staffing
- Asset & Equipment Analysis
- Planning & Scheduling
- Work Cycle
- Communication & Teamwork
- Change Management
- Maintenance Impact
Then We Integrate Technical Skills Training for an End-to-End Solution for Maintenance Improvement
Often, any performance improvement initiative fails in an organization because the people required to implement the changes do not possess the fundamental skills necessary to do their job. In the critical area of manufacturing maintenance, this can be a productivity killer. A recent survey finds that as much as 60% of the manufacturing maintenance workforce needs to improve their fundamental technical skills and abilities. And as highly tenured workers continue to retire and take their valuable training and experience with them, the problem is only getting worse.
That’s why our AMP Program also focuses on assessing and providing training to improve your maintenance team’s technical skills. We focus on four critical areas of Maintenance Technical Skills Training: Maintenance Fundamentals, Mechanical Concepts, Electrical Power, and Electrical Control.
Through a deep analysis of your current and planned assets and equipment and a rigorous workforce skills assessment, we’ll develop a technical training program that immediately fills any skills gaps and begins improving your maintenance performance immediately. This intensive and fundamental technical maintenance training is an integral part of our AMP Program, and only POWERS has it.
Technical Training
- Maintenance Fundamentals
- Mechanical Concepts
- Electrical Power
- Electrical Control
- Safety
- Understanding Drawings & Blueprints
- Predictive Maintenance
- Preventative Maintenance
- Equipment & Tools
- Parts Management
- Lubrication & Consumables
We Begin With Our 3-Step Maintenance Discovery Process to Uncover All Improvement Opportunities and Skills Gaps to Radically AMP Up Performance
Step 1. Maintenance Performance Assessment
There are three areas we look at during our assessment. We do a comprehensive OEE analysis uncovering your operation’s assets and equipment maintenance effectiveness, your current systems and processes for maintenace management, and the training and skill level of your maintenance team.
- OEE Analysis
- MMOS Effectiveness
- Team Skills & Training Assessment
This deep-dive assessment is why outside experience and resources like POWERS brings to the table are crucial for rapid, sustainable, and scalable improvement.
If you’re like many manufacturers today, your maintenance team is understaffed and overworked. On top of that, they may not possess the skills and training necessary to do the job.
That’s why adding an assessment of this magnitude may be unrealistic with your current resources. And that’s why we’ve introduced our AMP (Advanced Maintenance Performance) Program.
Step 2. Develop an Action Plan
Overall, downtime costs most factories somewhere between 5% and 20% of their productive capacity. – PTC
Unplanned downtime costs industrial manufacturers an estimated $50 billion annually. Equipment failure is the cause of 42% of this unplanned downtime. – IndustryWeek
In order to improve maintenance performance, the first thing you need to do is develop a plan for improvement. The purpose of this development is the highest maintenance optimization. Perhaps you want to minimize downtime of equipment or maybe you want to reorganize your assets. To see the maintenance performance improvement you want to see, you will first need to develop a plan and a timetable.
At POWERS, we aren’t your typical consultant or advisor. We analyze your current maintenance processes to develop a plan customized to meet the needs of your organization. We help you to implement the plan so that your maintenance team can become accustomed to any new processes. With the improvement of maintenance performance and the implementation of best practices, overall productivity will increase.
Step 3. Updated MMOS and Technology
Updating maintenance department systems, processes, and technology is especially important if your organization relies on pen and paper, a whiteboard, or spreadsheets to track your assets and work orders across the enterprise.
For example, optimizing your Maintenance Management Operating System (MMOS) may require implementing a more robust and technology-driven solution such as a Computerized Maintenance Management System (CMMS).
CMMS is software that helps streamline maintenance processes, manage your organization’s assets, schedule maintenance, and track work orders.
Implementing a new MMOS, often involving a new CMMS system, creates a more straightforward process for work orders, accurate time maintenance information, preventive maintenance scheduling, and labor reports, increasing productivity, reducing labor hours, reducing downtime, and improving performance.
The Final Step To AMP Up Your Maintenance Performance is Implementation. Let’s Talk About Starting Today.
The POWERS Difference
Our team has deep experience in manufacturing maintenance operations. Through our new AMP (Advanced Maintenance Performance) Program, we provide an objective analysis and prescriptive tactical and technical improvement plan to drive rapid, sustainable, and scalable improvement. No one else offers this end-to-end solution for transforming maintenance performance.
When navigating any significant organizational change, you may need to talk to an expert. We hold a mirror up to your organization, providing an unbiased view of your current processes. We then identify the areas where your maintenance department is performing well and where there could be some improvement.
With our AMP Program, you’ll have a deep OEE analysis, uncover any skills and training gaps, develop a plan, and implement it across your operation to AMP up your maintenance workforce and drive performance improvement.
Please download our FREE Maintenance Assessment Guide by completing the form to learn more about our maintenance assessment and improvement process.
AMP up your maintenance performance starting today! Schedule an initial discovery and analysis by calling +1 678-971-4711, or emailing us at info@thepowerscompany.com.
Download our Free
Maintenance Assessment Guide
Take the first steps in assessing and improving your maintenance performance. Download our free Maintenance Assessment Guide to begin asking the right questions in critical areas of your maintenance program.
- Work Order System
- Work Estimates
- Backlog
- Staffing
- Work Assignments
- And More
Get Actionable Performance Improvement Insights Every Month
Why Do We Focus on Maintenance? Maintenance Performance Has a Significant Impact on Productivity, Capacity, Downtime, Throughput, and More.
Transforming manufacturing operational performance requires analyzing the systems, processes, and behaviors woven into the fabric of an organization, from inputs to outputs, from the top floor to the shop floor. One element that should be on every organization’s radar for improvement is maintenance performance or MRO.
MRO stands for Maintenance, Repair, and Operations (or sometimes Maintenance, Repair, and Overhaul). MRO refers to the equipment, tools, and activities associated with performing daily business operations. MRO doesn’t include materials, products, and services used directly in production but instead acts as the glue that holds everything together.
MRO is often divided into four repair and maintenance categories:
- Infrastructure, which is typically focused on keeping the organization’s facilities up and running.
- Production equipment used to process the inputs and outputs throughout the value chain.
- Material handling equipment and systems involved in transporting raw materials and final products to and from production lines.
- Tooling and consumables, which are any smaller, handheld tools required in day-to-day operations.
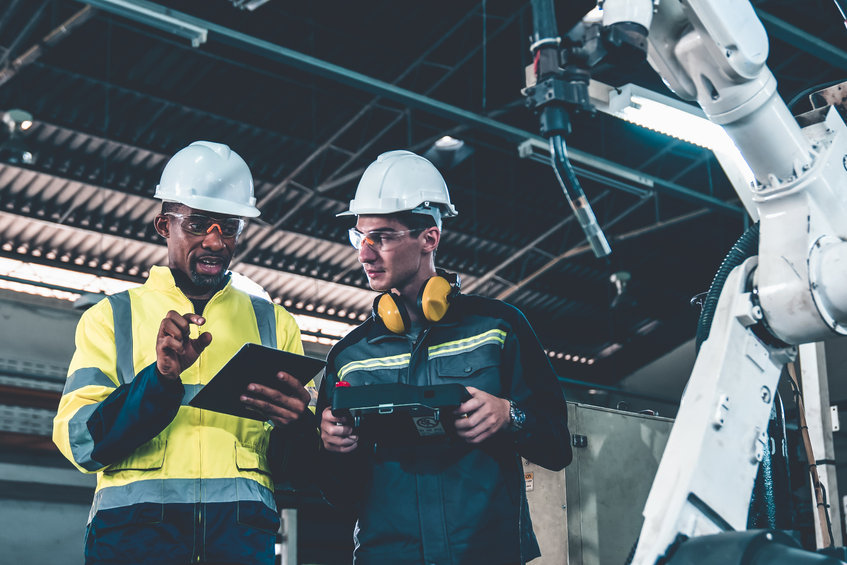
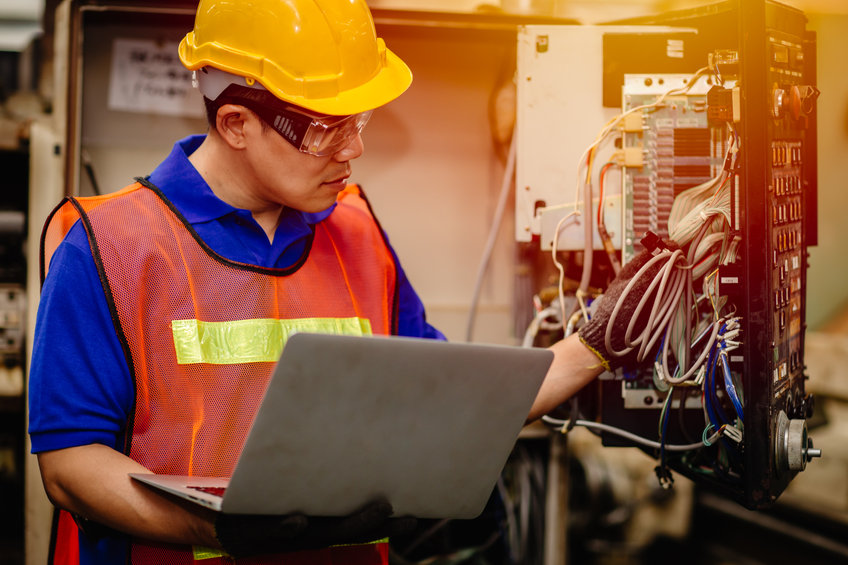
Maintenance management falls into these four categories, whether planned or unplanned:
- Corrective maintenance – Replace components upon failure. Only repair when there are errors.
- Preventive maintenance – Replace components before failure, repair equipment before the date of expected failure, prevent errors before they happen.
- Predictive maintenance – Monitor components, often with the advent of technological advancements like CMMS (Computerized Maintenance Management System), IIoT (Industrial Internet of Things), and Digital Twins. When problems are detected, take corrective action.
- Proactive maintenance – Identify and correct root causes of failure to help avoid maintenance issues.
Expertly managing the reliability of every asset along each link in your value chain involves transforming your maintenance mindset from reactive to proactive to excellence. But how do you prioritize maintenance with each department and production line straining under the current global supply chain and market demand pressures?
We’ve found that maintenance performance excellence can be a key to unlocking supply chain bottlenecks and uncovering added capacity and throughput. Getting maintenance performance right can be like “found” money and dramatically impact ROA (Return on Assets).
In this economic climate, manufacturing facilities and operations managers constantly battle to increase profitability and minimize costs. Increasing production is often one of the corrective measures taken to decrease the unit cost. Unfortunately, this “lever” is sometimes pulled without considering the added maintenance requirements or impact on reliability. Instead, production is ramped up without considering how long the equipment can sustain the increased output without going down or breaking entirely.
According to data from WSJ, unplanned downtime costs industrial manufacturers an estimated $50 billion annually. Equipment failure is the cause of 42% of this unplanned downtime.
When downtime and production losses increase, management sees it as a maintenance problem. However, the issue originated in management’s failure to assess the risk before the production increase and act accordingly. Whether senior managers realize it or not, minimizing cost while maximizing profit depends on equipment operating safely and reliably. That’s why maintenance has a big part to play in the overall health of your organization.
In a world where supply chain, cost reduction, and market demand pressures are through the roof, doesn’t it make sense to find any additional reliable and safe capacity and throughput from your existing assets? Maintenance performance excellence can be that key. But where do you start?
FROM OUR BLOG
Featured Maintenance Performance Improvement Articles
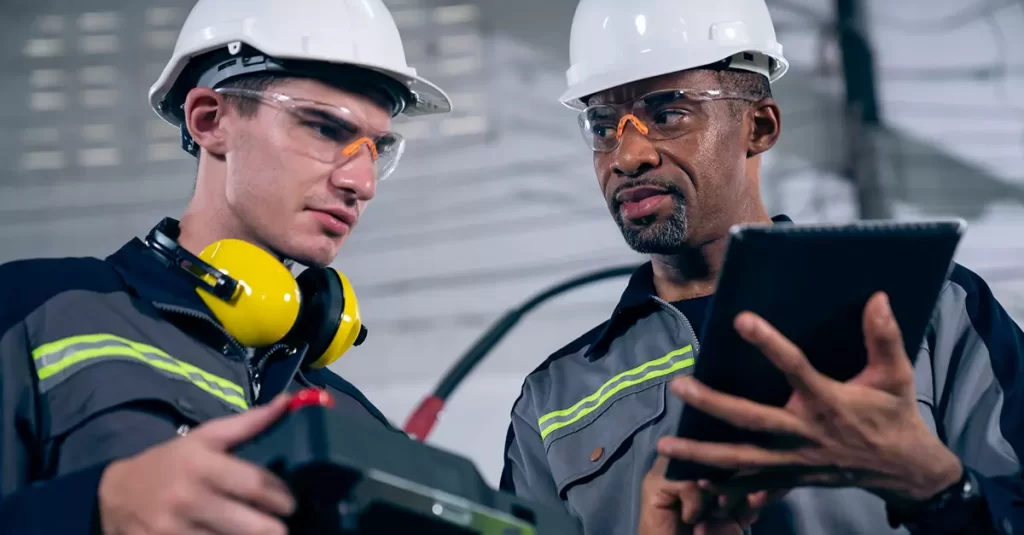
Your Maintenance Department is One of the Most Critical Areas for Increasing Productivity and Improving OEE.
Let’s Zero in on the Fundamentals of Total Productive Maintenance to Increase Maintenance Department Productivity, Reliability, and Drive OEE Maintenance Reliability or Total Productive Maintenance is a significant contributor to peak operational performance in manufacturing, impacting critical KPIs like uptime, throughput, capacity, and much more. This is especially true as the unpredictability of the global economy stresses assets and equipment to new levels to stay ahead of demand. The “run until
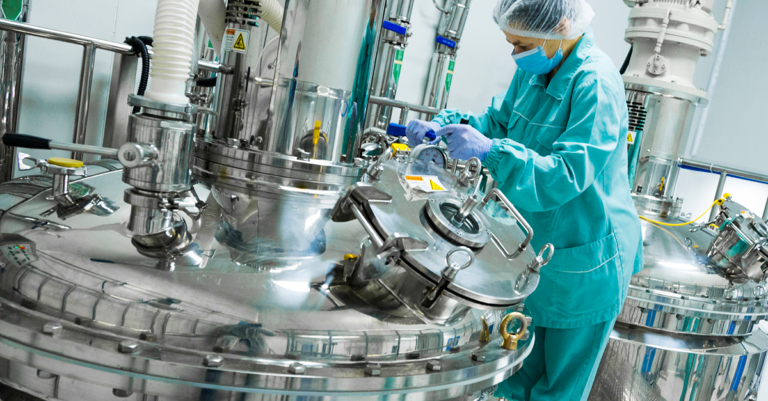
The Importance of Maintenance Performance in Pharmaceutical Manufacturing
AMP Up Your Approach to Maintenance Performance Improvement Unplanned Downtime Mastery Series : The Silent Thief Stealing Your Productivity and Profitability Unplanned Downtime Mastery Series
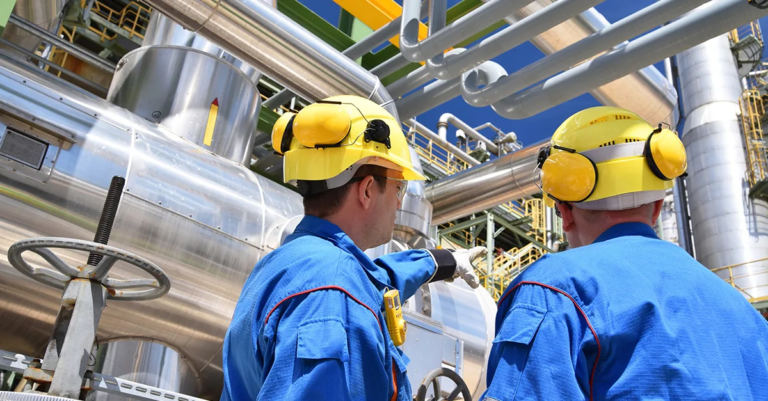
Maintenance Performance Excellence Can Be the Key To “Found” Money for Manufacturers: Minimizing Cost, Maximizing Profit
Maintenance performance excellence can be a key to unlocking supply chain bottlenecks and uncovering added capacity and throughput. Getting maintenance performance right can be like