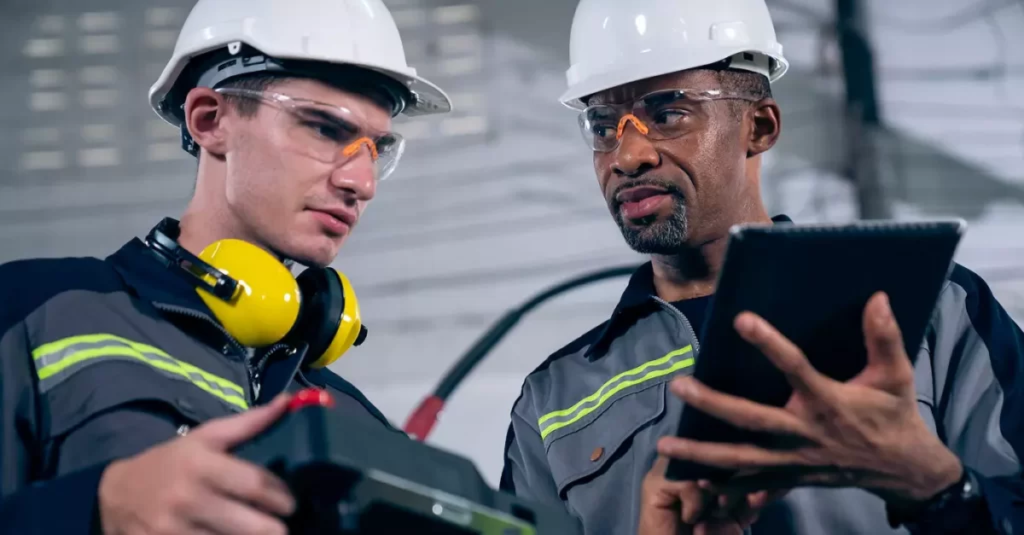
Let’s Zero in on the Fundamentals of Total Productive Maintenance to Increase Maintenance Department Productivity, Reliability, and Drive OEE
Maintenance Reliability or Total Productive Maintenance is a significant contributor to peak operational performance in manufacturing, impacting critical KPIs like uptime, throughput, capacity, and much more. This is especially true as the unpredictability of the global economy stresses assets and equipment to new levels to stay ahead of demand. The “run until it breaks” mentality just doesn’t cut it. Instead, you need to look at your entire approach to maintenance and its impact on your operation’s performance. Let’s dig into our comprehensive approach to increasing the productivity and reliability of your maintenance department.
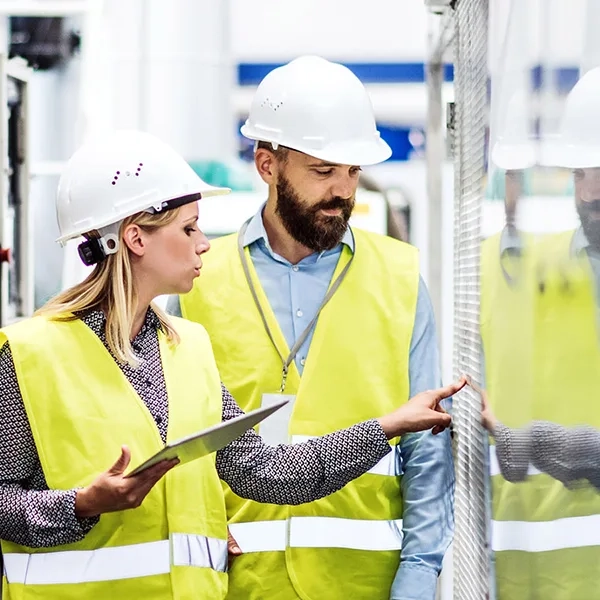
POWERS has developed a proven Maintenance Management Operating System (MMOS), with a strong central core, to deliver the optimium results for immediate improvement and long-term sustainability. Our Plan vs. Actual vs. Variance approach drives the heartbeat of a strong Maintenance Operating System. We focus on the following core elements:
- Planning and Scheduling
- Frontline Leadership Training & Development
- Contractor Spend
- Crewing
- Maintenance Systems Utilization
- KPI Reporting
- Parts Purchasing
- Supervisor Training
Importance of Planning and Scheduling
The first element in a solid Maintenance Reliability System is Planning and Scheduling. This is the foundation of the any effective Management System. Planning and Scheduling leads to accountability: Who is doing the work? What is being worked on? When will this activity take place and how long it will take to accomplish? This results in increased mechanic utilization and productivity, better coordination between departments, and ultimately, more “wrench time”.
Frontline Leadership Training and Development
Leadership skills must be developed in people. Frequently, the most skilled worker is promoted to be the new supervisor. Lacking extensive training, the individuals fend for themselves, often repeating the approach of a previous supervisor. Enhanced approaches to leading, guiding, directing, and following-up are needed. The future retirement bubble also may lead to a loss of valuable experiential knowledge for the organization.
Unique Approach to Supervisory Training
The majority of the training (greater than 95%) is delivered in real-time as the action of the day unfolds. Our team provides coaching and mentoring side-by-side with your frontline leadership team to illustrate not only the supervisory skills, but how those abilities and tools impact actual performance, avoiding problems and motivating employees.
By applying fundamental concepts to real life problems and situations, retention levels are high and behaviors are sustained because they are connected with specific benefits. Moreover, repetition is necessary to change deeply rooted behaviors and instill the culture that you need to run your operations most effectively.
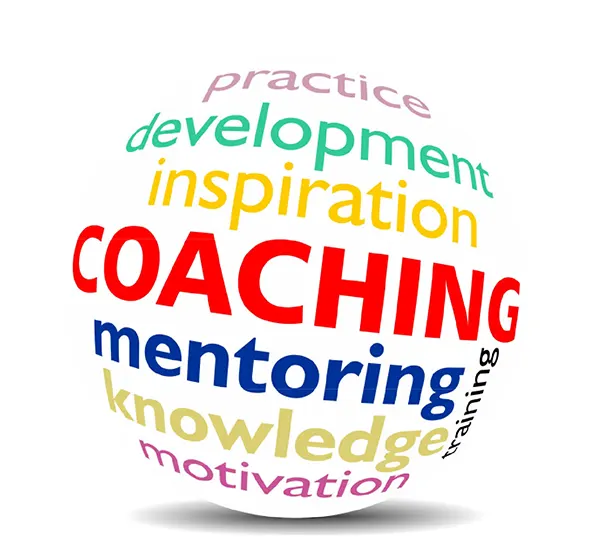
Management Development Workshops
While skill and behavior development is conducted side-by-side on the plant floor or in the work environment, we do provide workshops to introduce each frontline leadership concept. After each brief course, the team applies the concept as a focal point of development during day to day activities with the supervisors. The final exam is the measurable quality and productivity improvements in the work environment.
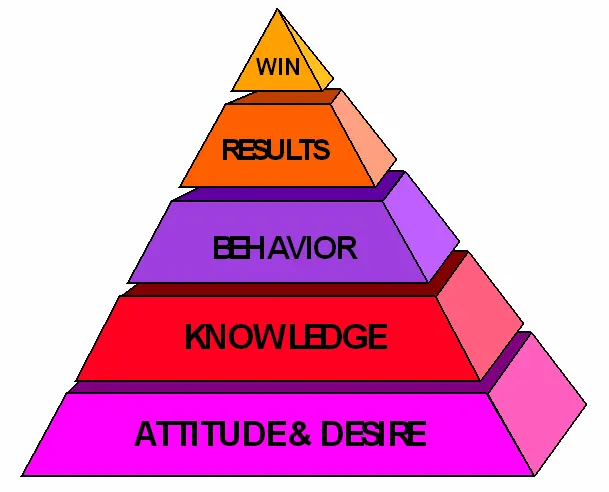
- Roles & Responsibilities
- Line Balance / Capacity
- Culture / Change
- Lost Time / Opportunity
- Work System Process (MOS)
- Follow up & Coaching
- Problem Solving / Roof Cause
- Organization – Time Management
- Reporting & Data Analysis
- Attitudes and Behaviors
- Coaching & Confrontation
- Continuous Improvement
Outside Contractor Management
As many facilities install advanced equipment or lose experience due to turnover or promotions, the use of outside contractors increases. With a total Maintenance Reliability system, your organization will manage those resources in concert with our own to support production needs. Our approach begins with maintaining skills inventories, identifying potential need for outside assistance, implementing an approval process, then integrating the resources into Preventative Maintenance planning and scheduling.
Proper Crewing Management
Properly crewing your maintenance department is a key element of Maintenance Reliability and is often overlooked. Do you have the right number of mechanics? TPM studies indicate that some companies do not have enough resources. Our team will assess the current crewing and determine the optimal number to perform all required work to keep your operation running to its full potential.
Key elements to implement include planning and scheduling, skills identification, training plans, overtime control, potential concurrent activities, and accurate work estimates. Together these give you the tools to identify the optimum crewing for your facility.
Current Maintenance Systems Utilization
POWERS works side-by-side with your management team and builds upon your current computerized maintenance systems (CMMS or EAM).
We implement tools to supplement that system and create the ultimate Maintenance Reliability System: An optimized integration of the people, processes, and systems involved in maintenance.
This approach improves and optimizes your current systems and drives the proper behaviors and desired results.
Key Performance Indicators and Reporting
An essential element to running your Maintenance Reliability System is measuring key metrics and evaluating any variances. Designing and executing the ideal corrective action for a negative variance and supportive behaviors for a positive variance drive results. These metrics are communicated in a structured manner daily and weekly:
- Schedule Attainment/Adherence
- PM Compliance
- Utilization
- Labor Hours
- Overtime %
- Contractor Spending
- Parts Usage
- Downtime Accountability
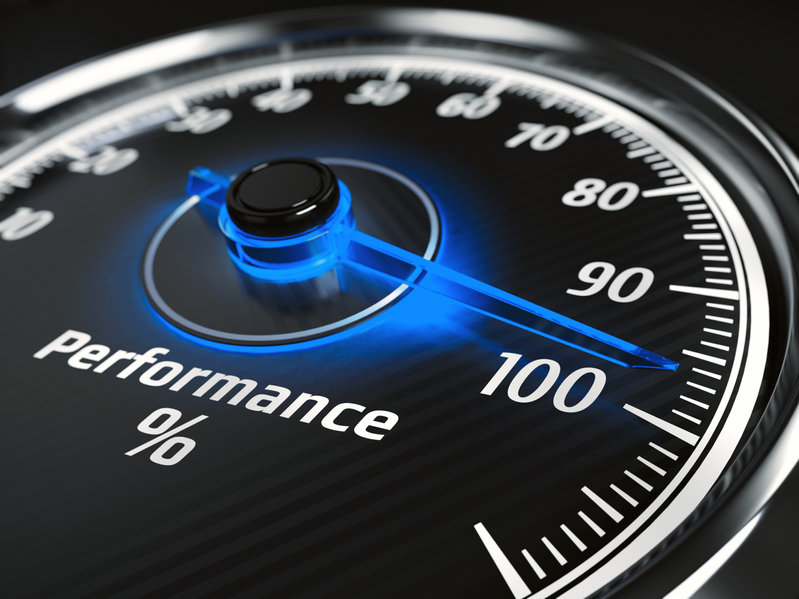
Parts Purchasing (MRO Spend)
Parts Purchasing (MRO Spend) is a key element in any successful Maintenance Reliability System. This is where the right parts are available at the right time to keep the facility operating to its full potential. This element is dependent upon a number of essential factors.
We provide tools and develop processes to maintain accurate equipment histories derived from corrective work as well as Preventative Maintenance. These determine what parts are needed to have on hand.
Some of the key metrics that drive a well managed Purchasing and Parts department are as follows:
- Spend Reporting
- Spend Variance
- Coordination (Parts Kitting)
- Parts Usage
- Inventory Control (Cycle Counting)
- Cycle Counting Accuracy
- Parts Delivery / lead time tracking / correct parts
- Obsolete parts reporting
- Vendor Scorecard / Performance review
MOS Specific Leadership Elements
Maintenance Reliability or Total Productive Maintenance and the resultant efficiency of your minute-by-minute manufacturing operations is dependent upon the custom designed Management Operating System (MOS) that your leaders employ to run their area without problems and to its full operational potential. This approach to maintenance excellence encompasses forecasting, planning, scheduling, preparation, coordination with other departments, execution, follow-up, measurement, and evaluation. It is supported by skills, behaviors, tools, controls, KPI’s, Standard Operating Procedures, and the daily, weekly, and monthly cadence that sustains the MOS. We design your custom leadership training and development program around the skills needed to operate your unique MOS.
Culture Performance Management
Your culture is the sum of the behaviors and attitudes of your entire team. It drives the actions of individuals to deliver upon your mission statement, and to achieve corporate goals and strategies. It helps employees and leaders understand the reasons behind their job responsibilities, priorities, processes and measurements, as well as their importance in the overall success of the company.
Culture is the approach that people bring with them to start the day, and it is the way they perceive their accomplishments at the end of the day. A key element of our approach to Frontline Leadership Training and Development comes from implementing key metrics that measure and promote the behaviors necessary to sustain your culture. Good results without the proper behaviors are a fortunate accident that may not repeat itself tomorrow.
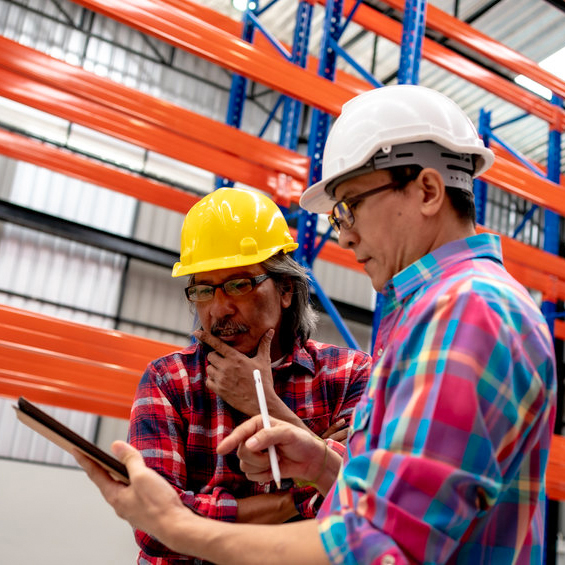
Sustainability and Scalability is Built Into Our Approach
Sustaining and scaling the skills and behaviors that are developed during a Frontline Leadership Training and Development program is a hallmark of our unique approach. Classroom training alone rarely sustains beyond the end of the slide deck. By working side-by-side with your frontline leaders and applying the skills in the context of fixing issues, avoiding problems, and improving performance, they internalize these new practices.
A series of metrics are installed that measure leading behaviors as well as financial results. We further this effort by installing a cadence of meetings with specific objectives and content. These are led by senior management with the specific objective of sustaining the newly developed skills. Another product of our engagements is a set of skill and behavior lists for all leadership roles that become tools for on-boarding, skill/gap assessment, and future training needs. We also provide a set of tools that help you audit the compliance of leaders to their new expectations.
What is the Expected ROI?
Through multiple client engagements, POWERS has helped companies reduce their maintenance and repair expenditures and their parts inventories while improving maintenance effectiveness. It is an area of focus where substantial financial benefits can be realized quickly. The success we’ve helped companies all around the country achieve stems from four key factors:
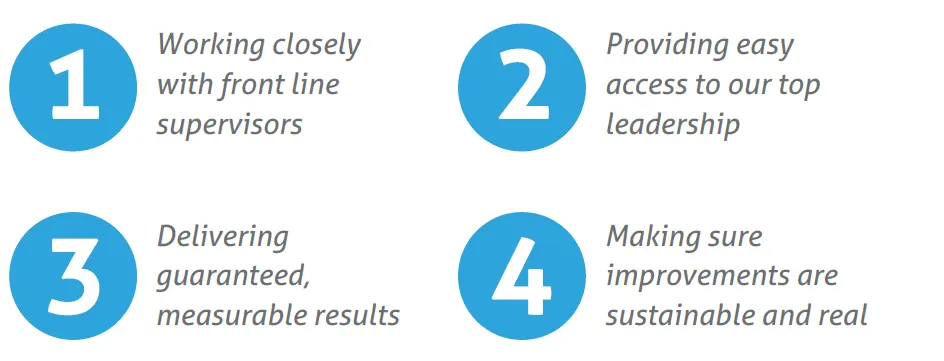
Our Efforts Have Produced the Following Results on Average Within a Matter of Months:
- 30-40% reduction in annual rate of M&R spend
- 20-30% decrease in parts inventories
- 50-60% drop in outside maintenance services expense
- 20-30% reduction in overall maintenance cost
- 40-50% improvement in maintenance utilization and reliability
The POWERS Difference
POWERS management consulting’s unique Culture Performance Management™ methodology connects the dots between optimized company culture and your desired operational performance outcomes. Improving and optimizing Maintenance Performance is one of our critical areas of focus for our clients.
POWERS has helped global leaders across many industries train and develop their frontline leaders to create rapid and sustained performance improvement, increased competitive advantage, greater value, and a stronger bottom line.
Put our experienced team and proven track record to work in your organization. Schedule an initial discovery and analysis by calling +1 678-971-4711 or emailing us at info@thepowerscompany.com.