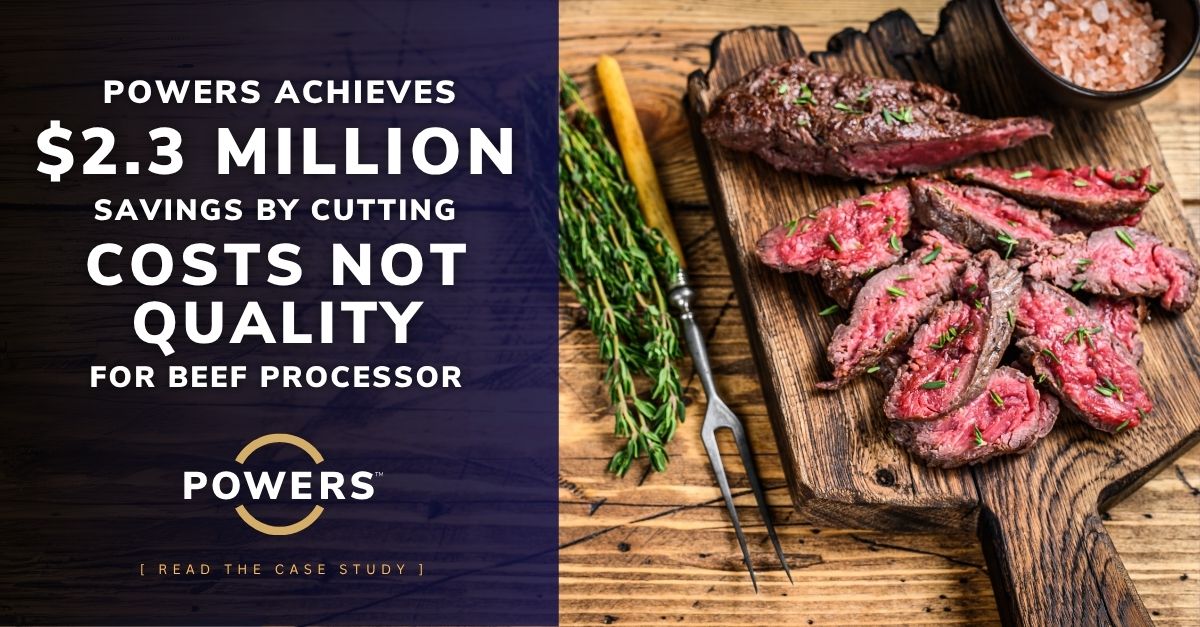
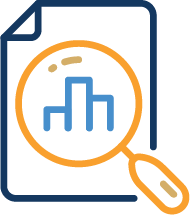
Project Overview
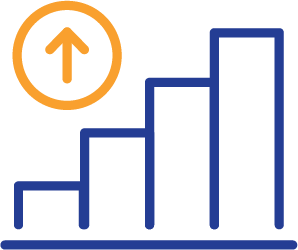
Performance Results
Situation
In the heartland of America, a well-known beef processing plant embarked on a journey toward operational excellence. Founded in the mid-'90s, this company had quietly grown, acquiring a substantial processing plant in the early 2000s. However, beneath the surface lay maintenance savings challenges that threatened to hinder its progress.
Maintenance operations were a reactionary maze, lacking a systematic approach, vital tools, and a culture of accountability. Engaging POWERS for a transformative intervention, they sought to chart a new course and achieve significant maintenance savings.
The story of this transformation serves as a testament to the power of strategic intervention and the boundless potential within every organization for growth and excellence.
Analysis
Due to the absence of daily metric tracking, this processing giant operated reactively. Supervisors spent a significant amount of time on mechanical work due to a lack of trained mechanics, leaving inadequate supervision of the crews. Work assignments were inconsistent, and crews were on standby for crisis work after completing startup checklists.
Before engaging POWERS, this beef processing plant faced several maintenance performance issues:
- Existing Preventive Maintenance (PM) procedures were rudimentary, resembling startup and shutdown checklists.
- The maintenance environment operated in a reactive “run to fail” mode with no root cause analysis after equipment failures.
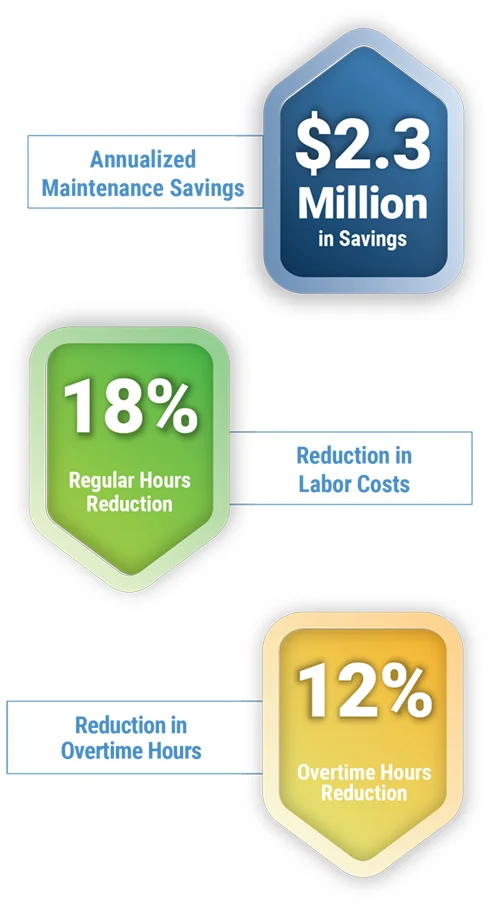
- The absence of a Computerized Maintenance Management System (CMMS) hindered PM, Corrective Work Orders (WO), and Crisis WO tracking.
- Key Performance Indicators (KPIs) were absent, leading to a lack of visibility for the leadership team.
- R&M (Repairs and Maintenance) spending had been increasing, with no management at the Superintendent level and poor budget communication.
- Survey results revealed a need for training and development across all levels, including Superintendents (29%), frontline Supervisors (56%), and Leads (80%). Fundamental responsibilities for successful leadership were often misunderstood or overlooked, leading to a culture of "waiting until directed."
- The company lacked a defined Maintenance MOS. Only 46% of fundamental MOS elements existed, with 40% requiring enhancements for utility. Key indicators, such as the percentage of PM completion and backlog, were missing and not all team members understood the purpose of these tools.
The Plan
A 26-week project was devised to establish foundational MOS elements within the Maintenance department. Here's a detailed breakdown of our approach:
- Interim Work Management System: While selecting and implementing a CMMS, we introduced an interim work management system to maintain order and efficiency.
- Value-Added Work: We assigned value-added tasks to each mechanic, ensuring their contributions aligned with organizational goals.
- Right-Sizing Staff: We carefully adjusted staffing levels to match workload demands, optimizing resource allocation.
- Strategic Communication: Introducing strategic communication points throughout the day and week enhanced coordination and information exchange.
- KPI Development: We developed critical Key Performance Indicators (KPIs) and tracking methodologies to measure and improve performance.
- R&M Spending Management: Implementing systematic management of Repairs and Maintenance (R&M) spending ensured cost control and efficient resource allocation.
- Effective PMs: We created effective Preventive Maintenance (PM) plans for critical equipment, reducing downtime and enhancing reliability.
- Proactive Culture: We instilled a proactive culture among Supervisors and Superintendents, emphasizing accountability, problem-solving, and planning.
- Root Cause Analysis: Promoting Root Cause Analysis (RCA) allowed us to identify and eliminate downtime triggers systematically.
Additionally, we rolled out 24 weeks of Advanced Maintenance Practices (AMP) training, covering Mechanical Concepts and Electrical Power, equipping the team with the skills and knowledge needed for sustainable improvement. This comprehensive approach ignited a remarkable transformation in maintenance operations.
The Solution
POWERS devised a multifaceted solution to address the maintenance challenges and set the stage for sustainable improvement. This comprehensive approach encompassed the following key components:
- Interim Work Management System: Recognizing the immediate need for better work organization, POWERS implemented an interim work management system. This system ensured that maintenance tasks were tracked, assigned, and completed efficiently until a long-term Computerized Maintenance Management System (CMMS) could be selected and integrated.
- Resource Optimization: To maximize the utilization of resources, POWERS worked on right-sizing staffing levels to align with the actual workload. This adjustment helped eliminate inefficiencies and reduced labor costs.
- Strategic Communication: Introducing strategic communication points throughout the day and week facilitated real-time information exchange and coordination among team members. This improved collaboration and responsiveness to maintenance needs.
- KPI Development: POWERS developed critical Key Performance Indicators (KPIs) and tracking methodologies tailored to the maintenance department's specific needs. These KPIs provided the leadership team with the necessary visibility to monitor and manage performance effectively.
- R&M Spending Management: A systematic approach to managing Repairs and Maintenance (R&M) spending was established. Budgets were communicated, and actual spending was reviewed regularly. This approach ensured better financial control and allocation of resources.
- Effective PMs: POWERS collaborated with the maintenance team to create and implement effective Preventive Maintenance (PM) plans for critical equipment. This proactive approach reduced unplanned downtime and enhanced equipment reliability.
- Proactive Culture: A significant focus was placed on instilling a proactive culture among Supervisors and Superintendents. POWERS emphasized the importance of taking ownership, problem-solving, and planning to improve overall departmental efficiency.
- Root Cause Analysis: Promoting Root Cause Analysis (RCA) became a cornerstone of the solution. The goal was to systematically identify the root causes of downtime events and implement corrective actions to prevent their recurrence.
In essence, POWERS' solution was a holistic approach that tackled operational inefficiencies from multiple angles. By addressing resource allocation, communication, performance measurement, and proactive practices, the company was poised to transform its maintenance operations.
The Results
Embarking on a journey to redefine their maintenance operations, our anonymous company
joined forces with POWERS to bring about substantial improvements. This collaborative effort
delivered tangible value across various facets of their maintenance department:
- Total Annualized Maintenance Savings of $2.3 Million: The cumulative result of these accomplishments was a complete metamorphosis of maintenance operations.
- R&M Spend Improvement (13%): By meticulously managing Repairs and Maintenance (R&M) spending, this achievement translated into cost savings, affording the company financial flexibility to invest in growth and innovation.
- Reduction in Regular Hours (18%): Aligning staffing levels with workload not only optimized resource allocation but also reduced labor costs significantly, bolstering the bottom line.
- Reduction in Overtime Hours (12%): The systematic reduction of overtime hours through Overtime Authorization and weekend planning not only curbed expenses but also improved employee work-life balance.
- Planned Hours (108%): Transitioning from no planned hours to exceeding planned hours instilled visibility and accountability, ensuring tasks were aligned with objectives.
- PM Hours Completed (Over 1,800 weekly): With over 1,800 hours of Preventive Maintenance (PM) work accomplished weekly, equipment reliability soared, minimizing unexpected downtime and bolstering operational efficiency.
- Start-Up Score (Consistent 80%+): Consistent Start-Up scores of over 80%
underscored the reliability and efficiency of maintenance processes. - Number of PMs Created by Department: Creating and meticulously tracking Preventive Maintenance (PM) schedules for various departments elevated equipment reliability and overall performance.
The focus shifted from reactivity to proactivity, from inefficiency to optimization, and from uncertainty to a culture of continuous improvement. This transformation not only enhanced operational efficiency but also positioned the company for sustained growth and competitiveness in their industry, making the project a huge success