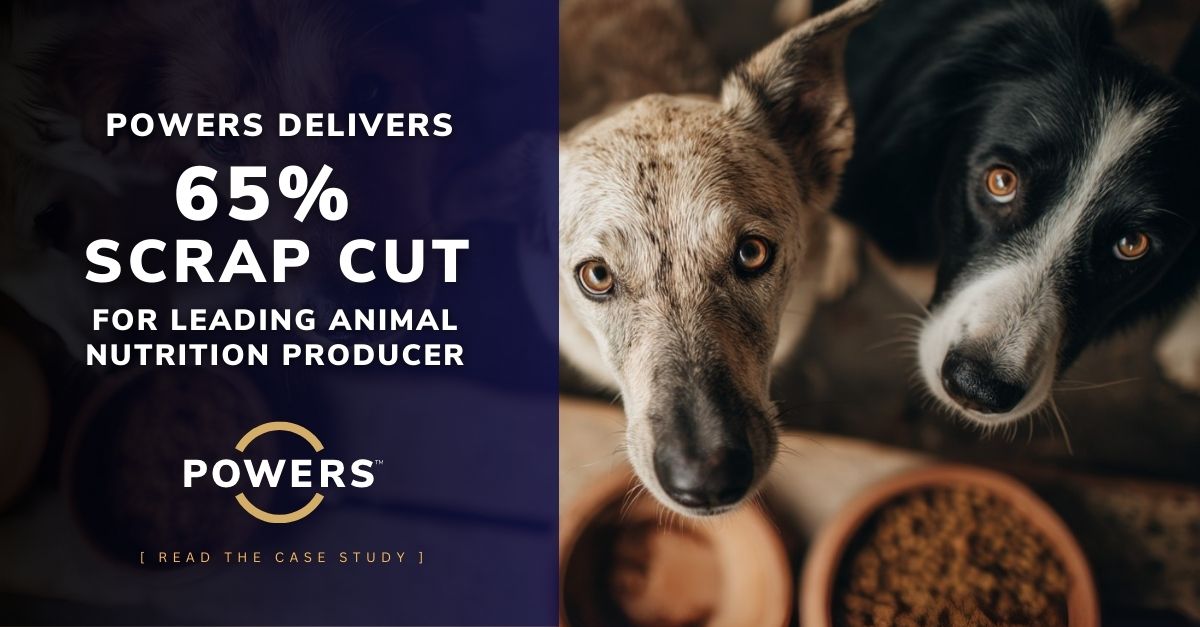
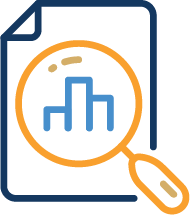
Project Overview
Overview
A leading manufacturer in the animal nutrition industry partnered with POWERS to improve quality, reduce labor inefficiencies, and establish consistent operating procedures across two facilities on a shared campus.
Facing elevated scrap rates, high Cost of Poor Quality (COPQ), and inconsistent labor utilization, the organization sought to regain control over its operations by implementing a robust Management Operating System (MOS) and strengthening cross-site collaboration.
In just 16 weeks, the company saw a 65% reduction in scrap, a 15% drop in temporary labor usage, and a 45% decrease in COPQ, each result statistically significant and sustainable through newly embedded management practices.
Challenges Identified
The organization’s challenges were rooted in both operational inefficiencies and structural gaps across leadership and communication systems:
- Excessive Scrap and Rework: Inconsistent process adherence and a lack of real-time monitoring led to significant waste in raw materials and finished goods.
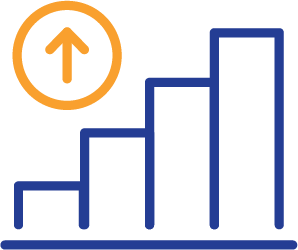
Performance Results
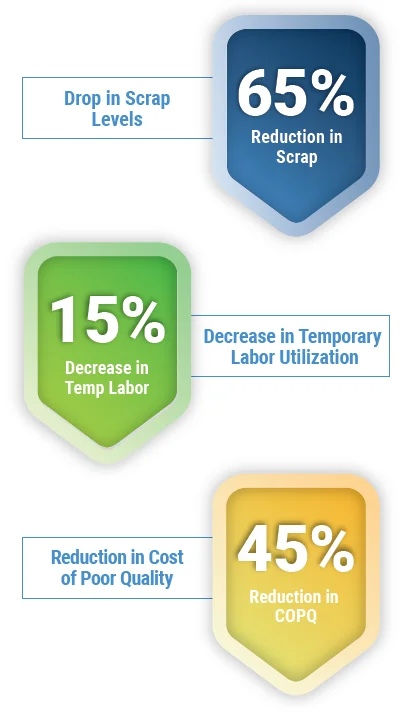
Read the Full Case Study Here
- Siloed Operations Between Facilities: The two sites on the same campus lacked coordination, resulting in duplicated efforts, underutilized resources, and labor imbalances.
- Rising Labor Costs: Over-reliance on temporary labor and inconsistent line management practices drove up costs and limited production stability.
- Quality Control Gaps: Standard Operating Procedures (SOPs) were inconsistently followed or poorly communicated, driving up the COPQ and increasing customer complaints and internal rework cycles.
To move forward, the organization needed a unifying structure that would promote accountability, enhance data visibility, and enable leadership to lead with intention and foresight.
Solutions Implemented
The POWERS team deployed a hands-on team to work shoulder-to-shoulder with frontline leaders and site supervisors. The project centered on three core strategies:
1. Installing a Robust Management Operating System (MOS)
The new MOS was designed to create real-time visibility into production line performance and reduce process variation. Key components included:
- Daily and weekly tiered meetings aligned across leadership levels
- Introduction of Plan-Actual-Variance-Action (PAVA) tracking tools
- Hour-by-hour monitoring of key process indicators
These tools enabled teams to proactively address deviations and shift from reactive problem-solving to continuous improvement.
2. Cross-Facility Communication Enhancement
By integrating daily communication protocols across both facilities, leaders established clear expectations around shared resource planning, labor allocation, and production prioritization. This improved:
- Labor control and shift coverage
- Utilization of specialty equipment between sites
- Coordination of preventive maintenance schedules to reduce downtime
This coordination contributed directly to a 15% reduction in temporary labor through more efficient deployment of existing staff.
3. Recalibrating Standard Operating Procedures (SOPs) and Driving Line Ownership
In-depth process mapping revealed that existing SOPs lacked clarity and consistency. Our team worked directly with production frontline leaders to:
- Redefine and simplify key SOPs
- Conduct training sessions with shift leaders to reinforce expectations
- Introduce accountability mechanisms tied to line-level performance
This effort helped frontline teams take ownership of quality and productivity outcomes, contributing to a 45% reduction in COPQ compared to the previous year.
Results Achieved
Within the 16-week engagement, the organization achieved measurable improvements across multiple performance dimensions:
- 65% Reduction in Scrap
A direct result of improved SOP adherence, real-time quality tracking, and empowered line leadership. - 15% Decrease in Temporary Labor Utilization
Enhanced cross-site planning allowed the organization to rely more heavily on trained, full-time staff and avoid costly temp hours. - 45% Reduction in Cost of Poor Quality (COPQ)
By tightening quality processes and eliminating rework cycles, the team reclaimed value and protected margin. - Improved Line Stability and Throughput
Through standardized management tools and PAVA routines, supervisors gained clarity on performance issues in real-time, leading to faster recovery and higher overall line efficiency. - Better Product Quality and First-Pass Yield
Improved adherence to SOPs and better line ownership meant fewer errors, less rework, and better output, especially critical in pet food production where consistency and compliance are non-negotiable.
Conclusion
This engagement demonstrated the power of structured management systems and leadership enablement in driving measurable results. By partnering with POWERS, our client transformed siloed operations into a cohesive, data-driven production network. The outcome: higher-quality products, reduced costs, and a frontline team equipped with the tools and confidence to sustain the gains.
As operational efficiency improved, so did team morale, communication, and ownership, laying a foundation for long-term performance excellence in a competitive market. Contact POWERS today to learn about DPS and take the first step toward smarter, more sustainable manufacturing.