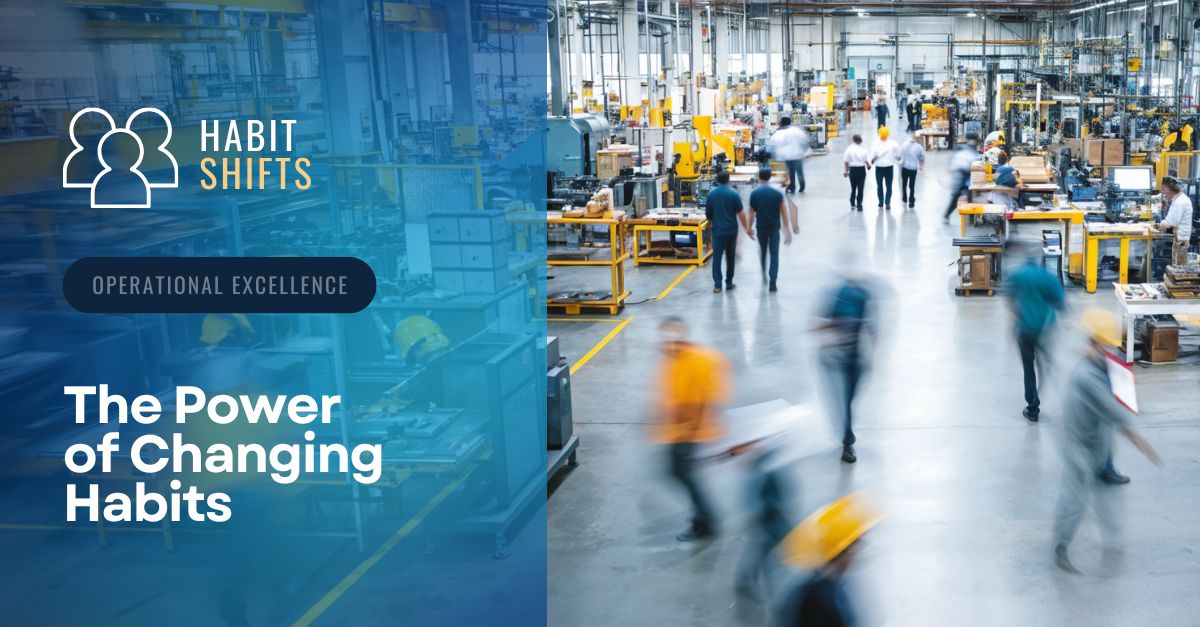
Sean Hart, Chief Executive Officer And Managing Partner, POWERS
Manufacturing leaders, you steer complex operations where every decision shapes output, margins, and morale.
Your teams are chasing ambitious goals—tighter processes, more intelligent systems, sharper skills—but here’s the unyielding truth: no improvement endures without changing habits. Those entrenched “we’ve always done it that way” routines are your toughest opponent, quietly eroding productivity and smothering innovation. Operational excellence demands more than new tools or plans; it requires rooting out counterproductive practices and forging habits that stick. Let’s confront this challenge and build a stronger operation.
Why Habits Define Success
Improvement is seductive—new technology, streamlined workflows, or intensive training promise big gains. But without new habits, those efforts fade. Habits are the unseen engine of your plant. They’re what operators, supervisors, and managers do instinctively when deadlines loom or machines hum. If those habits are flawed—an overlooked maintenance check, a rushed setup, a skipped debrief—you’re not just losing efficiency. You’re sacrificing thousands in output, quality, and team trust.
Industry research underscores this:
Studies show that disciplined habit-building reduces waste by 30% more than temporary fixes. The “we’ve always done it that way” mindset isn’t a badge of tradition—it’s a barrier to progress and costs you more than you think.
The Hidden Enemy: Counterproductive Routines
The most challenging aspect? These counterproductive habits are often invisible, deeply ingrained in the fabric of your operation, and disguised as ‘just how we do things.’ Consider the setup that consistently takes 10 minutes longer than necessary or the maintenance routine that over-services low-risk assets while critical ones are neglected. These are not isolated incidents but rather ingrained habits that accumulate into significant daily losses.
We’ve seen it across decades on shop floors.
One plant lost 15% of its overall equipment effectiveness because operators habitually dismissed a vibration alert as "normal." Another burned $200,000 annually on changeovers because "speed" trumped precision.
These aren’t glaring errors; they’re subtle, embedded practices that only surface when you challenge assumptions. Your mission as a leader is to inspire your team to hunt these ‘productivity drags’ relentlessly—because accepting them is conceding defeat.
How to Win: A Disciplined Approach
Changing habits isn’t easy, but it’s how you separate good operations from great ones. Here’s how to start:
- Expose the Weak Links: Engage your team to identify one habit holding you back. Is it a setup shortcut that causes defects? A maintenance check skipped for "efficiency"? Track performance metrics—time, quality, output—to pinpoint where habits falter. One operation uncovered a 20-minute daily delay just by analyzing setup logs. Find your weak spot.
- Build Better Routines: Don't tweak bad habits—replace them. If operators skip critical checks, establish a mandatory 30-second pre-shift inspection. If changeovers are sloppy, train a standardized sequence and measure it. Research shows that new habits need 66 days to take root, so consistency must be enforced.
- Lead by Example: Your team watches you. If you tolerate old routines or skip performance reviews, they will too. Commit to new habits—daily metric checks, pre-shift huddles, tough conversations. Industry data shows that plants with disciplined leadership habits gain 12% more uptime. Be the standard, not the exception.
The Reward: Lasting Excellence
Changing habits is about more than incremental gains—it’s about forging a resilient, efficient, and innovative operation. One new habit, like a predictive maintenance check, can save hundreds of thousands of dollars in output annually. Another, like structured shift handoffs, can cut errors by 25% and boost morale. These are not just numbers; they are the potential for significant gains that can motivate your team. Layer these habits, and you’re not just running a plant—you’re redefining what’s possible.
At POWERS, our approach—rooted in decades of boots-on-the-ground experience driving productivity and profit, and tools like DPS, our Digital Production System—helps manufacturers break old habits and build new ones that drive results. Start now: question one routine, test one change. What’s the first habit you’ll reshape this month?
About POWERS
At POWERS, we partner with manufacturing firms to tackle tough challenges—like changes in systems, processes, and behaviors that stick—with practical solutions. Our approach sharpens operations through process improvements, boosts productivity with leadership and workforce training, optimizes supply chains, and drives maintenance performance to keep OEE climbing. We’re all about results: higher efficiency, less downtime, and stronger teams.
To take it further, we created DPS, a digital production system that puts real-time data in your hands. DPS streamlines workflows, tracks critical KPIs like downtime and capacity utilization, and keeps your team aligned for sustainable gains—no fluff, just tools that work—for better decisions and better outcomes every shift.
Ready to change the habits that are holding you back? Reach out to POWERS to explore how our experience and DPS can help you push your operations to a new standard of excellence.
- Speak to an Expert: Call +1 678-971-4711 to discuss your specific challenges and goals.
- Email Us: Get tailored insights by emailing info@thepowerscompany.com
- Request an Assessment: Use our online contact form, and one of our expert manufacturing consultants will reach out to schedule an in-depth analysis of your operations.