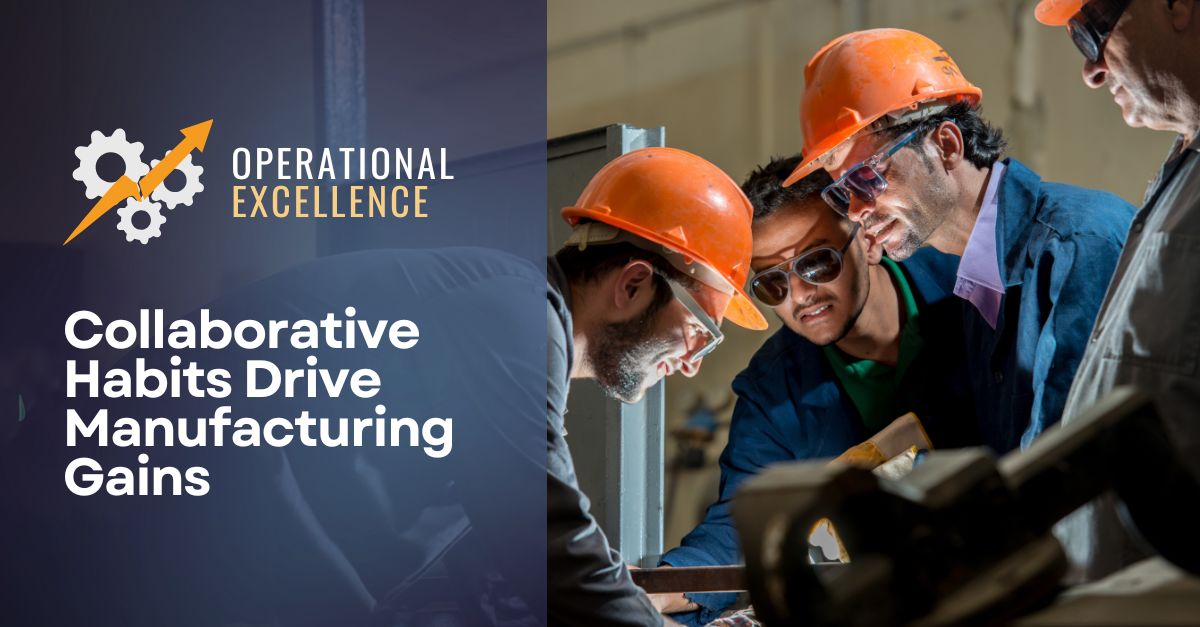
On the manufacturing floor, habits shape every outcome throughput, quality, and margins.
Yet, too many operations are held back by siloed routines: operators focused solely on their station, maintenance crews detached from production goals, and supervisors blind to cross-line bottlenecks. These fragmented habits, born of repetition and isolation, choke efficiency and cost millions in lost output.
By reshaping how your floor works together, you can unlock double-digit throughput gains and build a more resilient operation.
The Cost of Siloed Habits
Siloed habits are pervasive on the manufacturing floor. An operator tweaks a machine without signaling the next station, causing a jam. A maintenance team prioritizes their schedule over production’s urgent needs, delaying restarts. A supervisor overlooks a downstream bottleneck, assuming “it’s not my line.” These routines aren’t malicious—they’re the residue of years spent working in isolation, where individual tasks trump collective goals.
The impact is stark: one misaligned habit can slash output by 5% daily, piling up to millions annually across a plant.
Research confirms the toll. Due to coordination failures, plants with fragmented workflows lose 10–15% of their capacity. Conversely, operations that foster collaborative behaviors—where teams share real-time insights and align actions—see throughput rise up to 20%. The difference isn’t technology or talent; it’s the habits that govern how teams interact. Siloed routines breed inefficiency; collaborative ones drive results.
The Challenge: Breaking the Silo Mentality
Shifting from siloed to collaborative habits is no small feat. These behaviors are entrenched and reinforced by years of “stay in your lane” thinking. Operators may resist sharing data, fearing blame. Maintenance crews may cling to rigid schedules, missing production’s rhythm. Supervisors may hesitate to coordinate across lines, assuming it’s above their scope. These habits persist because they feel safe, familiar, and functional—until you measure the losses they create.
A maintenance tech might complete their checklist but miss a critical repair needed for uptime. Breaking this cycle requires a deliberate shift: habits that connect every role to the plant’s broader goals.
A Roadmap to Collaborative Habits
Transforming floor habits starts with small, intentional changes that yield big results. Here’s how to begin:
- Create Shared Visibility: Equip teams with real-time performance data. If operators see how their actions affect downstream output, they're more likely to signal issues early. One plant cut bottlenecks by 12% by sharing line-speed metrics across stations.
- Align Daily Routines: Build habits that link roles. Start each shift with a 5-minute cross-team huddle to flag risks—maintenance, production, and supervisors together. A manufacturer reduced changeover delays by 18% with this practice.
- Reward Collective Wins: Shift incentives from individual tasks to team outcomes. Recognize crews that solve cross-line issues, like a maintenance team prioritizing a production-critical repair. Plants with team-based rewards see 10% higher engagement.
These steps aren’t complex, but they require commitment. Collaborative habits take time—roughly 66 days to solidify—but their impact is immediate. One new routine, like a shared alert system, can boost output by 5% in weeks.
The Impact: A Unified, High-Output Floor
Collaborative habits transform more than metrics—they reshape your operation’s DNA. When operators, maintenance, and supervisors work as one, bottlenecks shrink, quality spikes, and resilience grows. A plant that adopted cross-team huddles cut scrap rates by 15%. Another that aligned maintenance with production goals lifted OEE by 10%. These aren’t flukes—they’re the result of habits that prioritize outcomes over tasks.
The “stay in your lane” mentality is a relic. Your floor thrives when every role connects to the bigger picture.
About POWERS
At POWERS, we partner with manufacturing firms to tackle tough challenges—like changes in systems, processes, and behaviors that stick—with practical solutions. Our approach sharpens operations through process improvements, boosts productivity with leadership and workforce training, optimizes supply chains, and drives maintenance performance to impact the bottom line. We’re all about results: higher efficiency, less downtime, and stronger frontline leaders.
To take it further, we created DPS, our Digital Production System that puts real-time data and analysis in your hands. DPS streamlines workflows, tracks critical KPIs like downtime and capacity utilization, and keeps your team aligned for sustainable gains—no fluff, just tools that work—for better decisions and better outcomes every shift.
Ready to change the habits that are holding you back? Reach out to POWERS to explore how our experience and DPS can help you push your operations to a new standard of excellence.
- Speak to an Expert: Call +1 678-971-4711 to discuss your specific challenges and goals.
- Email Us: Get tailored insights by emailing info@thepowerscompany.com
- Request an Assessment: Use our online contact form, and one of our expert manufacturing consultants will reach out to schedule an in-depth analysis of your operations.