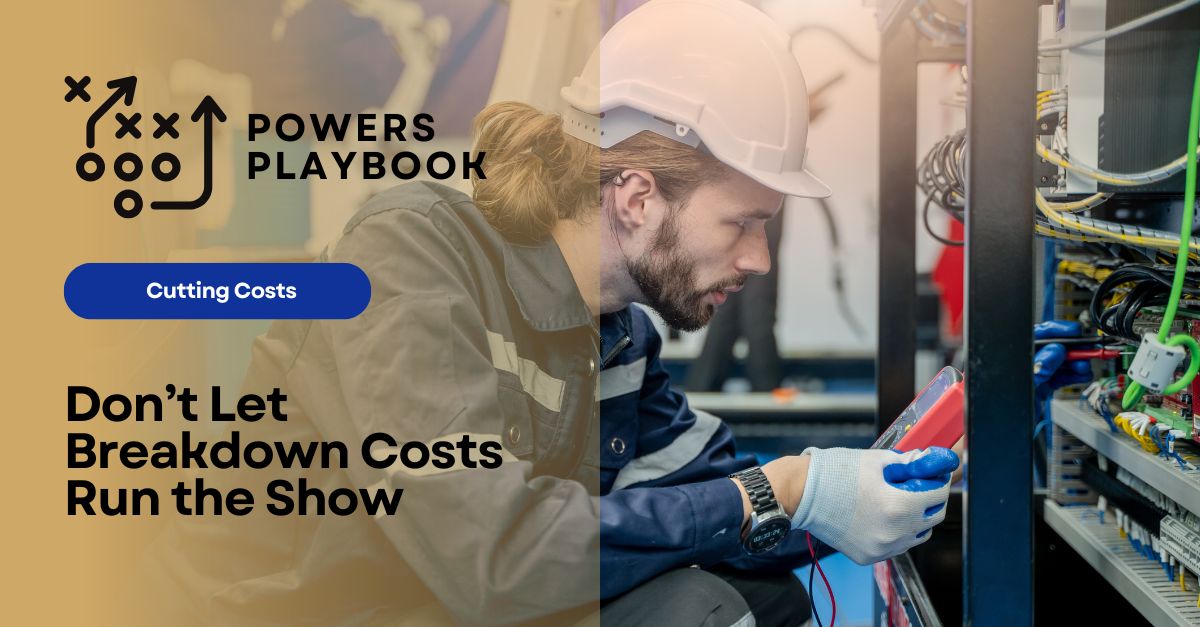
When machines break down, the real cost isn’t just the repair, it’s everything that happens around it. Production grinds to a halt.
Labor stands still. Schedules fall apart. And if it keeps happening, customers start losing trust. The frustrating part? Most breakdowns don’t come out of nowhere. The signs were there. We just didn’t catch them in time.
What Today Looks Like on the Floor
Let’s be honest: most plants are running hot.
Machines are pushed for output. Maintenance teams are buried in reactive work. And supervisors? They’re stuck putting out fires, just trying to make it to the end of the shift without something falling apart.
Here’s what a typical day looks like without a clear maintenance rhythm:
- Operators report a machine’s acting “off” but nothing gets logged
- The same piece of equipment keeps jamming, but only gets fixed when it stops completely
- A tech shows up mid-run, trying to fix something under pressure
- Line backs up, labor costs climb, and now you’re running overtime to make up for lost time
It’s a costly cycle, and way too common.
The Real Cost of “Run Until It Breaks”
A breakdown doesn’t just mean a busted part, it sets off a chain reaction across the whole floor.
Here’s what starts adding up fast:
- Labor Waste: Workers waiting around, reassignments, and shift coverage issues
- Overtime: Paying more hours to make up lost time
- Rush Orders: Paying premiums to get parts or vendors in fast
- Quality Issues: Equipment that’s not running right leads to defects and rework
- Missed Delivery Windows: Which means unhappy customers or lost orders
It’s not just about the maintenance cost, it’s about how far that cost spreads.
Quick Wins That Cut Costs Fast
You don’t need a full PM program or a new headcount to start getting ahead of problems. What supervisors need is a few reliable habits that shift the mindset from react after to act before.
Here’s how:
🔧 Build a Weekly Check Routine
Pick one consistent time, like before Monday’s first run, and start with 5 minutes per line. Look for leaks, loose belts, slow starts, strange noises, or visible wear.
Pro Tip
Use a laminated checklist and a dry erase marker. Keep it simple. Keep it visible.
🛠 Log Issues When They Happen
Set up a basic log sheet or whiteboard near the operator station. When something doesn’t sound or feel right, get it written down, don’t rely on memory or word of mouth.
Even small notes like “motor whining at startup” or “product misfeeds occasionally” help maintenance teams get ahead of bigger issues.
📅 Use Natural Downtime Smarter
During changeovers, meal breaks, or cleaning periods, plan small tasks like lubrication, air filter checks, or bolt tightening.
If you’re waiting for the next batch anyway, make those few minutes count.
🤝 Sync Up with Maintenance
Instead of only submitting tickets, ask maintenance leads to walk the line with you once a week. Bring your log. Ask what trends they’re seeing across equipment.
This quick connection builds trust and makes it easier to prioritize what needs real attention.
📉 Track Repeat Offenders
Start a simple list of the top 3 machines or components that are eating up time or breaking the most. Circle back every week to see if anything’s improved, or if it’s getting worse.
Example
If the bagging machine has jammed 3 times this week, that’s a red flag. It’s not “just bad luck.”
The Payoff: Less Downtime, More Control
When you get ahead of maintenance, everything runs smoother:
- Labor is better used
- Repairs are less rushed and more effective
- Production schedules are more stable
- Team stress goes down
- Costs stay under control
Most importantly, you get more confidence that your day won’t be derailed by the next unexpected breakdown.
This isn’t about being perfect, it’s about being proactive.
What to Do This Week
You don’t need a major initiative to get started. Just pick a lane and take action:
- Set up a 5-minute Monday morning equipment check
- Put up a log board near one key piece of equipment
- Call a 10-minute sync with your maintenance lead
- List your top 3 problem machines, and check the log daily
Start small. Start visible. Let the team see that staying ahead of problems is part of the job.
Take Control of Maintenance Costs, Before They Control You
POWERS specializes in helping manufacturing teams lower costs by eliminating the small, silent inefficiencies that drive up expenses over time. Our proven approach equips frontline leaders with the tools and behaviors they need to stay ahead of problems, streamline maintenance planning, and get more value out of existing resources.
To make it even easier, we developed DPS to help supervisors make smarter, faster decisions on the floor. DPS combines lean manufacturing principles with real-time data, allowing teams to:
- Pinpoint costly delays and downtime patterns
- Prioritize the right fixes at the right time
- Monitor trends across equipment and labor
- Reduce unplanned repairs and emergency work orders
- Lower total cost of ownership without increasing headcount
If you’re ready to cut waste and protect your margins, without slowing down production, let’s talk.
Contact POWERS today to learn how our team and DPS platform can help you plan smarter, run leaner, and cut costs where it counts.
- Speak to an Expert: Call +1 678-971-4711 to discuss your specific challenges and goals.
- Email Us: Get tailored insights by emailing info@thepowerscompany.com
- Request an Assessment: Use our online contact form, and one of our expert manufacturing consultants will reach out to schedule an in-depth analysis of your operations.