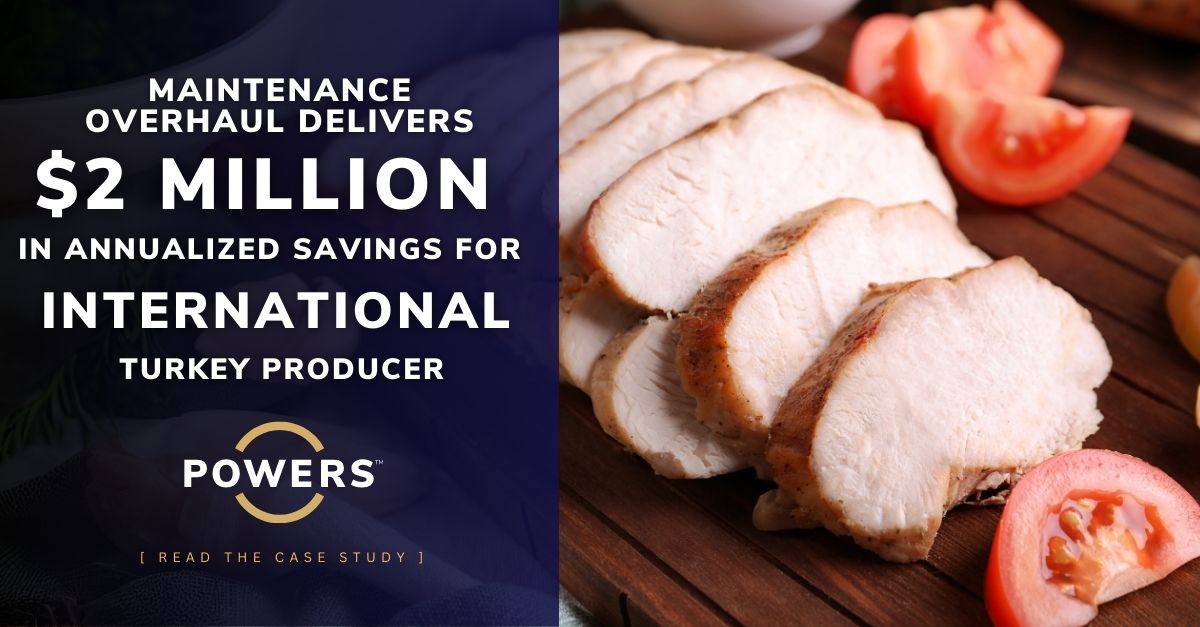
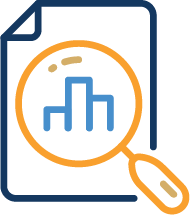
Project Overview
Overview
This Midwestern turkey producer was founded by 15 growers in 1998 and now packs for over 60 local and national brands which are distributed internationally to supermarkets and restaurants. They were challenged with equipment and line unreliability and unpredictability when it was needed to produce.
They approached POWERS to help them create a more effective maintenance system focused on uptime improvement and preventive maintenance activities. Over the course of this 22-week engagement, we focused on maintenance, repair, and operations (MRO) in two locations that were three miles apart from each other.
Problems
Maintenance work was strictly reactive. Maintenance employees would wait for a breakdown and then swoop into action to get equipment back up and running. Their Enterprise Asset Maintenance (EAM) system, was not being used to record repairs or parts costs by equipment.
Overtime was neither scheduled nor controlled. There was no approval process for purchasing parts, contracted services spend and their MRO parts inventory accuracy was low. PMs in the system were vague and not detailed, and maintenance managers did not assign work.
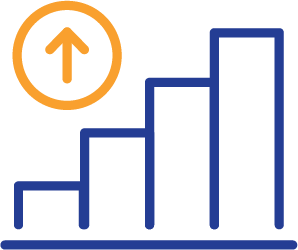
Performance Results
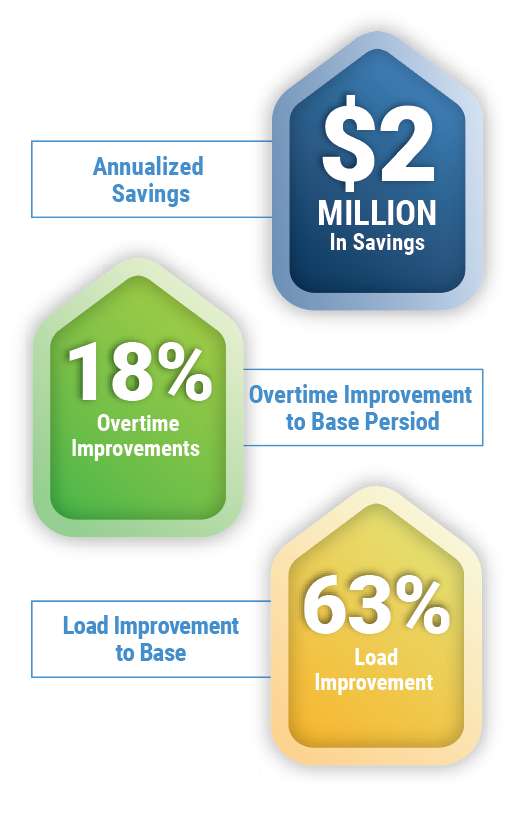
Read the Full Case Study Here
Objectives
- Create and enhance their maintenance management operating system to provide the tools to develop, manage, and sustain equipment reliably
- Drive a culture of accountability and continuous sustainable improvement
- Provide a structure to improve mechanic/technician utilization focused on preventive and predictive maintenance routines
- Create a competitive advantage for the company through improved reliability and uptime gaining needed capacity
Strategies
- Define and provide task definition to work assignment to mechanics; remove the ambiguous to reduce dependencies on tribal knowledge
- Develop daily schedules by mechanic to improve utilization and ‘ value’ work
- Managers were to assign and follow up on maintenance work performed on the floor
- Systematically capture all work being performed into EAM
- Use the system to develop maintenance history to understand ‘costs to maintain’ each asset
- Create approval process to control parts spend and contracted services
Results
Over $2 million in savings including:
- $845,000 in labor savings
- $1,225,000 in MRO savings
18% overtime improvement to base period
63% load improvement to base period
Testimonials
“I feel pride in what we have accomplished so far and see how much further we can go.”
– Director of Maintenance
“Powers brings experience at turning things around. They bring the tools and the focus needed to keep the project moving as desired.”
– Vice President of Maintenance
“Many of the people at our company had the skills and the drive to accomplish many things on their own. POWERS brought the focus, tools, and strategy that got us working in the right direction.”
– Vice President of Maintenance