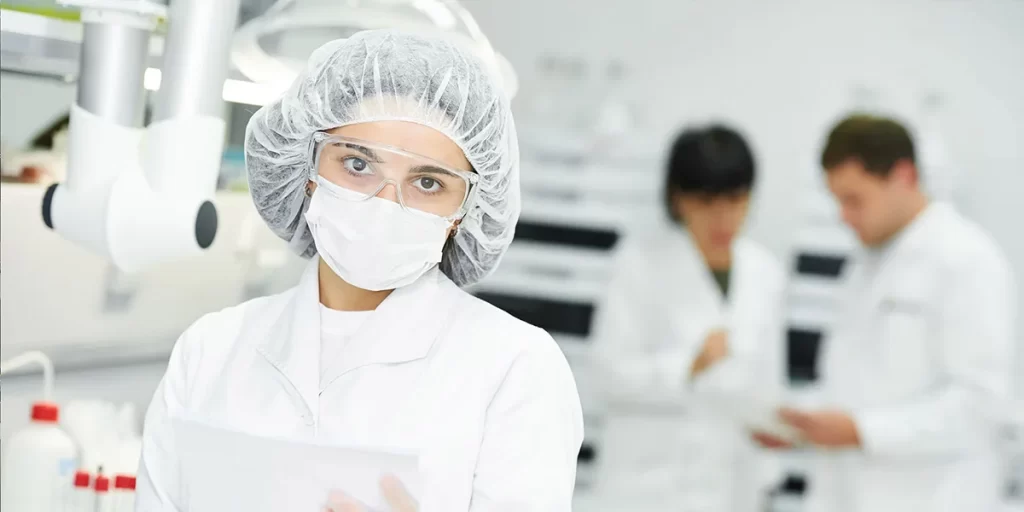
Global Specialty Pharmaceutical Maker
Our client is a global, integrated specialty pharmaceutical company that produces and markets generic, branded, biosimilar and OTC products spanning the full array of delivery formulations. Following several acquisitions, company leaders wanted to optimally leverage its investments at its No. 1 production site in the Americas. With some 76 different product families, this manufacturing facility is one of the most complex in the company – and in the industry.
The client sought to increase the plant’s throughput 30 percent using its existing technology. They needed to improve asset utilization and ensure it had the right amount of inventory to support customer needs. This would require a structured, thorough production schedule that incorporated the correct standards, operating procedures and behaviors to support planning while defining the proper sequence for the production centers. Work was currently being scheduled and performed on a 7-day schedule simply based on equipment availability. The only way to determine how much product the plant could handle was to assess its current capacity and develop an optimal – but elusive – “rhythm wheel” schedule.
Problems
At the time, there were dozens of different IT data platforms generating reports and intelligence. What’s more, they did not necessarily reflect what was happening on the plant floor. How could the company link its disparate systems to supervisory management behavior, skills, communication processes and decision-making in order to maximize value and capacity from its investments? Its leaders were intrigued by The Powers Company’s Integrated Management System approach, which takes a floor-level look to identify the gaps, then ties them back to existing information systems.
The pharmaceutical company engaged us to develop a 90-day rhythm wheel production schedule. It wanted a process that could be replicated to create similar production schedules at other high-velocity production plants. Among the complexities factored into the project:
- A full 80 percent of products produced are extended release.
- There is no one-to-one basis per batch on certain key products.
- Many product types compete for a limited number of machine groups.
- There are multiple intermediate processing stages for key product families.
- There are long individual, value-adding processing times (up to 96 hours).
- Cleaning operations were not linked to the production schedule.
- There was no defined standard work for machine set-up and cleanings.
- Cycle time expectations were either unknown or not communicated as an expectation.
There was no process to easily compare elapsed and appropriate cycle times. In addition, the standards used for planning within the ERP system didn’t match those reported by production personnel. With inconsistent data from different systems, they did not know the true capacity of their current operations, much less whether they could accommodate 30 percent higher volumes.
Objectives
In the space of just five weeks, The Powers Company delivered the desired 90-day “perfect schedule.” It accounted for 93 percent of the products by dosage volume at its Florida site and laid the groundwork for ongoing improvement and planning. This schedule delineates ideal production of certain products through a sequence of production centers. It outlines the products to be made daily and the pieces of machinery on which they should be produced.
We also:
- Established the inventory required on lowrunning products to support high-running “A” products. This freed up capacity and protected this perfect schedule.
- Performed simulations based on average weekly demand to validate that the schedule supports market requirements.
- Developed standard operating procedures and required behaviors for future master data maintenance and development.
- Modeled actual production equipment capacity to a demand timeline using the rhythm wheel, which also supported a site implementation of Infor Advanced Planning & Scheduling.
- Created asset utilization metrics at the product-line level. The scalable framework and methodology we devised includes the average cycle length/process time in hours and the average idle time/cycle-in percentag
Strategies
The Powers Group developed an implementation roadmap at the product level that focuses on meeting the defined targets. Based on input from production personnel, we created a standard work sequence for all products at all stages.
This time sequence includes:
- Setup – How to set up a machine; how long it takes; material and parts needed; labor required; process control checks
- Run – How long a machine runs; operating parameters; number of operators needed to run the machine
- Clean – Steps in the sequence; cleaning material and tools required; time needed; labor required; quality specifications; cleaning guidelines
Results
By engaging The Powers Company, the client learned the plant’s true capacity. Using the rhythm wheel to model actual production equipment capacity to a demand timeline supported implementation of its global planning software at this site. Now, the client can use the same methodology at other high-velocity production sites.
Company leaders have gained critical visibility into plant operations and asset utilization within multiple work centers. The client now knows where and when it can perform product development, and how much more product can be introduced. Because the rhythm wheel process is scalable, the model compensates for increases or decreases in the number of products or volume demands. This allows managers to plan out sequences and see which areas are affected.
On the plant floor, the added insights also enhance efficiency and utilization. Because each machine owner now knows in advance what he will run in a particular period of time, he can start preparing for it. This keeps machines running constantly instead of being idled while prepping for the next product.
- Delivered a quarterly “rhythm wheel” schedule for 93% of the products by bulk volume at the No. 1 site
- Devised a scalable rhythm wheel model to support decision-making and planning
- Provided greater visibility into plant operations, efficiency and asset utilization
- Developed a product-level implementation roadmap for standard work
- Ensured high customer service levels by defining optimal product inventory levels
- Established a blueprint for future master data maintenance and development
- Created asset utilization metrics at the product-line level based on a scalable framework and methodology