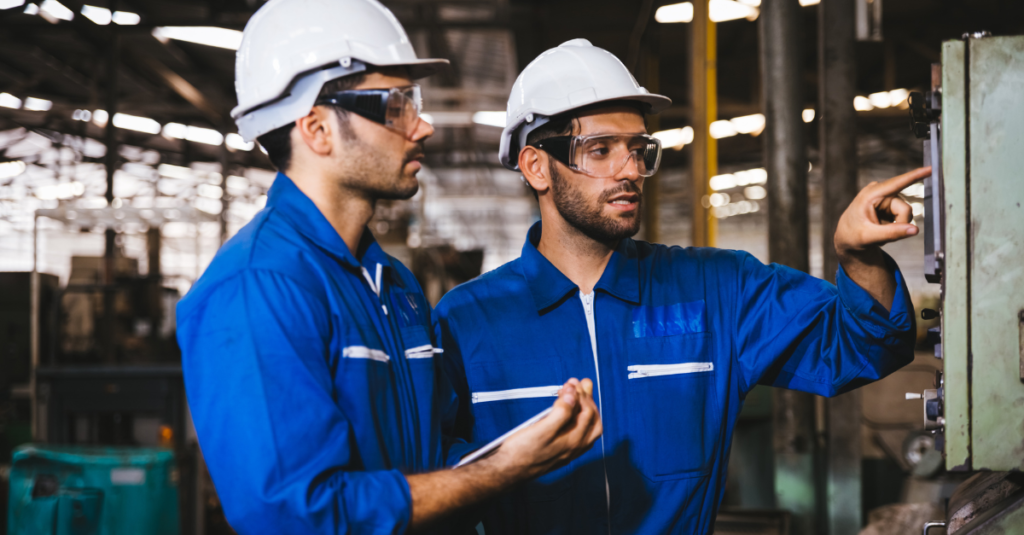
Going beyond a Total Productive Maintenance (TPM) approach to maintenance, manufacturers can increase uptime, lower costs, and improve the bottome line.
For manufacturers to produce quality goods, run efficiently, and remain profitable and competitive, it’s imperative that they focus on improving their maintenance performance. The quality of an organization’s maintenance performance contributes significantly to its overall performance as well as pushing higher Return on Assets (ROA).
Conversely, a poorly developed or implemented maintenance plan can be incredibly costly. For example, deferring maintenance or running a piece of equipment to the point of failure can cost be extremely costly. Deferred maintenance costs alone can be devastating to companies because their budgets rarely take unexpected breakdowns into consideration.
Deferred maintenance costs can include:
- Downtime costs
- Repair costs
- Rushed parts delivery costs
- Bringing in outside specialized labor
- Potential overtime costs
If organizations can implement predictive maintenance, they will see a great deal of savings and efficiency. Predictive maintenance can save 8% to 12% over preventive maintenance and nearly 40% more than corrective maintenance.
The types of maintenance management are:
- Corrective maintenance – Replace components upon failure. Only repair when there are errors.
- Preventive maintenance – Replace components before failure. Repair equipment before the date of expected failure. Prevent errors before they happen.
- Predictive maintenance – Monitor components, and when problems are detected, take corrective action.
- Proactive maintenance – Identify and correct root causes of failure to help avoid maintenance issues.
What is Total Productive Maintenance?
Many manufacturers implement a Total Productive Maintenance (TPM) approach. TPM is a holistic approach to equipment maintenance. The goal of TPM is to achieve perfect production where no breakdowns, small stops, accidents, or defects will occur.
There are eight supporting activities in TPM:
- Autonomous maintenance – Placing the responsibility for routine maintenance on the operators.
- Planned maintenance – Scheduling maintenance tasks based on measured and/or predicted failure rates.
- Quality integration – Integrating detection and prevention into production processes.
- Focused improvement – Encouraging small groups of employees to work together proactively to achieve regular, incremental improvements in the operation of equipment.
- Early equipment management – Directing understanding of equipment towards improving designs of new equipment to include maintenance and preventive maintenance safe access for technicians and operators, service and part replacement safe and efficient accessibility, ease of cleaning, lubricating, diagnostics, etc.
- Training and education – Filling in knowledge gaps to achieve TPM goals.
- Safety, health, environment – Maintaining a safe working environment.
- TPM in administration – Applying TPM techniques to functions of administration ensuring that your current or future CMMS system can track and generate equipment life history and prompts.
What Are the Benefits of a TPM Approach to Maintenance?
Total Productive Maintenance empowers employees to take responsibility for productivity and equipment maintenance. This can be incredibly helpful to manufacturers, particularly in the areas of:
- Efficiency – It requires manufacturers to look at quality over quantity and prioritize efficiency over output.
- Morale – By empowering employees to be responsible for upkeep of equipment, employees are able to have more pride in their work.
- Safety – Focusing on preventive and proactive maintenance can bring more order to the workplace, which increases safety for employees.
- Satisfaction – By increasing quality, efficiency, and employee morale, manufacturers will see more customer satisfaction.
How We Go Beyond TPM
At POWERS, we implement the principles of TPM, which can be incredibly effective at increasing uptime and lowering maintenance costs. However, we also take these principles a step further in our maintenance performance improvement processes. Here’s what we add to TPM:
- We make sure what the operators are doing is tied to certain qualifications and skills. There are some maintenance jobs that need to be done by qualified workers (electricians, in the case of electrical work). We identify which parts of the work the operators should perform and provide training as necessary. This would include capturing work in the CMMS, as well as providing them prompts to conduct timely.
- We maximize the utilization of maintenance technicians, and we maximize equipment availability as planned maintenance has to be performed when equipment is available.
- We go beyond equipment uptime to ensure that equipment is not only running smoothly but making quality products.
- We analyze equipment history and link that information to timing so that we can predict how long equipment will last, such as tracking mean time between failures driving root cause and elimination.
- We go beyond skills, training on the concept of preventive maintenance so that equipment is so reliable, maintenance workers can be used to do other things.
The POWERS Difference
POWERS management consulting’s unique Culture Performance Management™ methodology connects the dots between optimized company culture and your desired operational performance outcomes. One of our areas of critical focus is Maintenance Performance Improvement.
POWERS has helped global leaders across many industries operationalize their culture for rapid and sustained performance improvement, increased competitive advantage, greater value, and a stronger bottom line.
Put our experienced team and proven track record to work in your organization. Schedule an initial discovery and analysis by calling +1 678-971-4711, or emailing us at info@thepowerscompany.com.