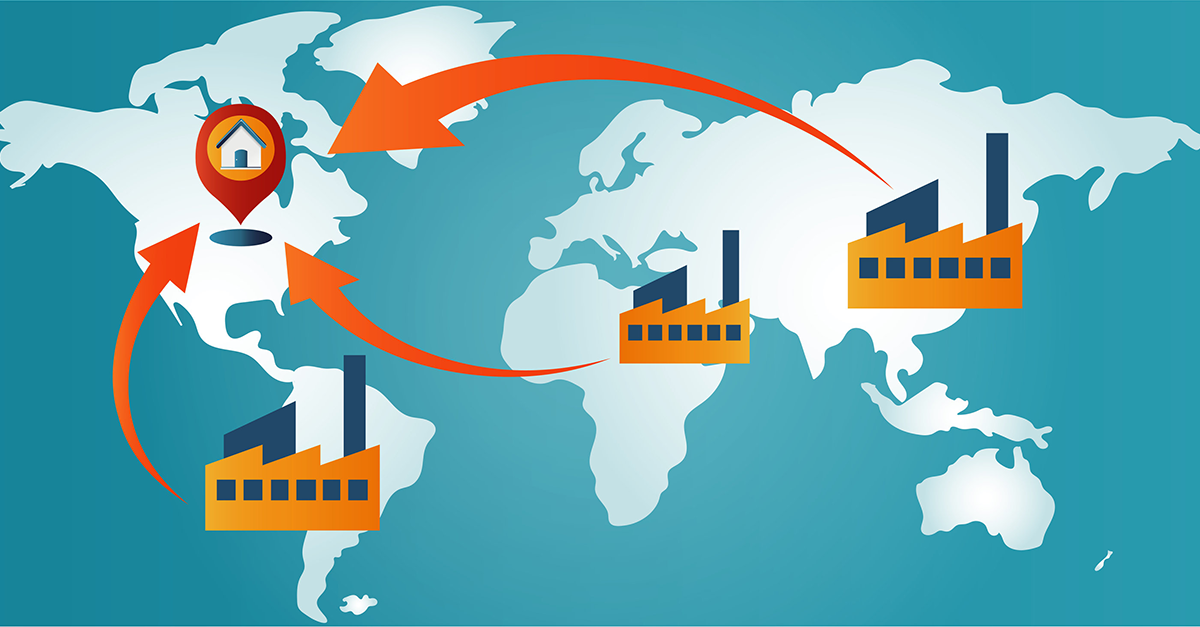
U.S. manufacturers look to onshoring to forge new, more resilient supply chain amid pandemic-induced shortages, delays, price hikes, and restrictions.
There certainly has been no greater drive toward innovation and knuckling down by U.S. manufacturers to find a way to get their products to market and overcome persistent demand shock running through virtually every product sector than the recent surge in onshoring activity.
Onshoring, also known as reshoring, is the opposite of offshoring and involves returning the production and manufacturing of goods to the company’s country of origin. Onshoring isn’t a new concept. It was widely debated during the global economic downturn, or “Great Recession” in 2008, for example, and at other times in our nation’s history.
However, as a direct response to pandemic-induced shortages, delays, price hikes, restrictions, and even outright embargoes, U.S. manufacturers are again looking to onshoring to forge new, more resilient links in their supply chains.
According to Thomasnet’s most recent annual survey of 709 manufacturers, as many as 83 percent of respondents said they are likely or highly likely to onshore their production operations and plan to add U.S suppliers to their supply chains. The ongoing reshoring trend is reflected in $204 billion in RFQ sourcing requests over the past 12 months, compared to only $69 billion in 2018.
There Are Distinct Advantages and Some Disadvantages to Onshoring. Let’s Look at Both.
Onshoring means bringing your supply chain closer together, adding greater resiliency, agility, and sustainability. Although global supply chains will continue to be a significant part of manufacturing’s future, organizations must combat the massive increases in shipping costs, lead times, and other disruptions.
That’s where onshoring becomes a factor. By shortening the distances between links in the supply chain and removing costly overseas sourcing, manufacturers improve resiliency, allowing them to endure any disruptions, no matter the cause, more capably. Onshoring also enables manufacturers to increase their market agility, responding to ever-changing consumer needs and demands more effectively.
Better still, manufacturers can reduce emissions, enhance sustainability, and ultimately decrease their environmental impact by reducing the distance between suppliers and their final points of arrival. These factors can significantly improve the firm’s adherence to ESG (Environmental, Social, Governance) standards.
There Are Major Benefits to Onshoring Critical Materials Suppliers and Other Significant Elements of Your Supply Chain.
- Onshoring has had a positive effect on the manufacturing labor market. According to wealthmanagement.com, onshoring is bringing higher-paying jobs to many areas of the country, including communities that were economically devastated when factories closed during the push for offshoring decades ago.
- Onshoring offers the opportunity to modernize aging operations. By building new U.S.-based facilities to meet demand, onshoring pushes firms reluctant to embrace new technologies to modernize their operations and streamline their processes.
- Logistics becomes more straightforward for the finished goods; they are unlikely to get stuck on the water, for example, holding up your inventory for months while insurance companies fight it out.
- Forecasting can be simpler and more responsive to changes. You would not need to factor six weeks at sea, which directly impacts the value of inventory you need to secure ahead of time.
- Introducing new products can be faster and more responsive to marketplace demand fluctuations.
- Managing quality is streamlined, without the need for third-party inspections or permanent staff in the factory. With the travel restrictions constantly changing at short notice, factory auditing overseas is becoming more and more outsourced and distanced.
Manufacturers Also Face Some Challenges with Onshoring.
The burgeoning reshoring of manufacturing is critical in driving up industrial real estate demand and, therefore, prices. According to a January 2022 article from WealthManagement.com, a massive demand surge for industrial properties has maxed out coastal areas. It is driving into cities in the Sunbelt and the Midwest in proximity to rail and port facilities.
Manufacturers compete for the same square footage as warehouse and distribution sectors. They have similar basic needs: access to labor, reliable and affordable utilities, proximity to a central transportation hub, and land to build on.
There are also tax and regulatory challenges with onshoring. The tax code is not currently neutral and is more biased against productivity-enhancing investments. According to a recent in-depth article from taxfoundation.org, the track record of industry-specific tax policy in the United States is mixed at best.
And of course, labor costs, land prices, regulations, fees, and more can be significantly higher in the United States than in other parts of the world. Factoring in these increases may not be possible for some manufacturers that have built their entire business model and competitive advantage around offshore sourcing.
Onshoring May Not Be an Immediate Solution for Some Manufacturers or Industries with Specialized Supply Needs.
Some materials such as rare earth elements (REE), minerals, raw materials, and other country-specific resources preclude their availability anywhere else on the planet.
Replacing vital REE input sources, for example, consumed domestically in the automotive industry and oil refineries, as well as in metallurgical alloys and applications, ceramics and glass, polishing, and more, may simply not be possible domestically without significant policy shifts, according to csrreports.congress.gov.
This Time Around, the Push to Onshore is Stronger.
As mentioned earlier, onshoring is not a new concept for U.S. manufacturing. There have been major pushes for this at times of economic upheaval in our nation’s past. The “Made in the USA” industry initiative from the 1970s comes to mind, as well as the push for onshoring at other times when the U.S. has overcommitted our supply chain overseas. But maybe this time is different.
For example, The Onshoring Project, a “consortium of North American innovators, practitioners, and supply chain experts from across the manufacturing industry,” was launched in late 2021. Its mission is to “facilitate a shift in OEM executive’s behavior toward a holistic approach to sourcing and the sounder and more financially beneficial strategy of using lean-performing North American suppliers.”
There are a handful of major manufacturing industry players behind this initiative. Its stated goals of better customer fill rate, lower finished goods on hand, less work-in-process and inventory in transit, reduced inspection, lower safety stock, lower risk, innovation at a faster pace, and shorter lead times are ambitious.
Perhaps this time around, manufacturing can overcome some of the challenges of onshoring and reap the significant market advantages and financial benefits of a more resilient, agile, and sustainable supply chain.
The POWERS Difference.
POWERS management consulting’s unique Culture Performance Management™ methodology connects the dots between optimized company culture and your desired operational performance outcomes.
POWERS has helped global leaders across many industries operationalize their culture for rapid and sustained performance improvement, increased competitive advantage, greater value, and a stronger bottom line.
To put our experienced team and proven track record to work for you, schedule an initial discovery and analysis by calling +1 678-971-4711, or emailing us at info@thepowerscompany.com.