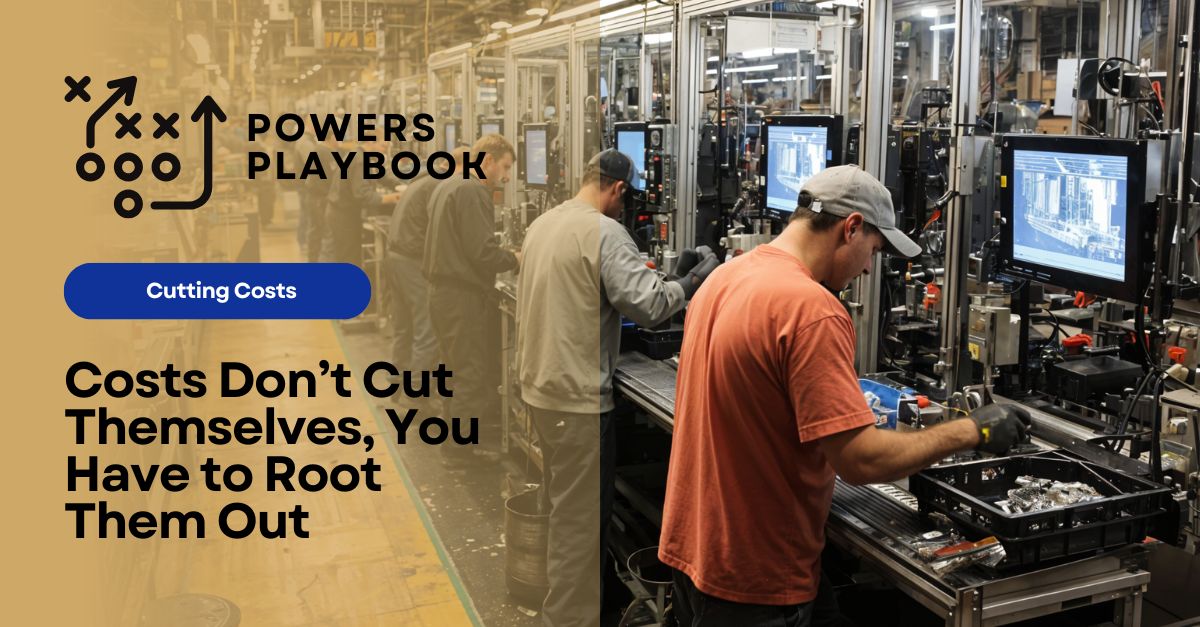
Lowering costs isn’t just a finance department job. It’s something every supervisor, manager, and frontline leader can tackle, every single day.
The good news? You don’t have to sacrifice output to get overtime under control. Small adjustments to how you plan, communicate, and track production can make a big difference fast. This playbook lays out proven tactics you can put into practice right away.
Why Overtime Costs More Than You Think
Even a couple of hours here and there can quietly stack up over a week or month. Overtime isn’t just expensive because of higher wages. It also leads to:
-
More mistakes
Tired employees make errors and cause rework. Quality issues pop up that take even more time to fix. -
Equipment wear
Machines run longer hours without a break, increasing breakdowns and unplanned downtime. -
Frustration
Teams get burned out and morale drops when extra hours become the norm. -
Hidden costs
Extra materials, more utilities, and extra time for supervisors to oversee extended shifts all eat into margins.
If you don’t keep an eye on it, overtime can quietly pull thousands of dollars a month off your bottom line. In many plants, it becomes a habit instead of an exception and that’s when it does the most damage.
Quick Wins to Start Using This Week
Here are five areas where you can take action today to get control of overtime without slowing production.
-
Review overtime daily.
Don’t just approve it—ask why it keeps happening. Look for recurring reasons and work with your leads to plan better. -
Walk the floor.
Watch for idle time, repeated material movement, and unfinished jobs waiting in queues. Just 10 minutes a day observing can reveal a lot of waste you can act on quickly. -
Check the schedule.
Look ahead a couple of days for any jobs that could trigger rushed shipments if they fall behind. A little planning goes a long way. -
Talk to maintenance.
Make sure preventive tasks are planned and not slipping through the cracks. Ask about machines showing early signs of trouble so you can schedule repairs before they fail. -
Set clear cut-off times.
Agree on when changes to orders or schedules must be locked in to avoid last-minute chaos and expensive fixes. -
Track contractor use.
Review where you’re using outside help and whether it’s really necessary. If you see the same contractors doing routine work repeatedly, look for ways to train your own team or plan ahead.
A Real Example
One supervisor noticed the forklift was running all day between a storage area and the line, sometimes making more than a dozen trips per shift. By moving the staging area just 30 feet closer to where materials were used, they eliminated over 14 unnecessary trips every day. Over the course of a year, that small change saved thousands of dollars in labor, equipment wear, and lost production time.
Keep Building the Habit
Hidden costs don’t go away on their own. They’re not always obvious, and they won’t fix themselves. You have to train yourself and your team to look for them. When everyone takes responsibility for controlling costs, small improvements stack up quickly into big results.
This is just the start. Throughout this month, we’ll share more playbooks that dig deeper into specific strategies, like:
- Cutting Overtime Without Sacrificing Output
- Planning Maintenance to Avoid Costly Breakdowns
- Improving Layout to Reduce Movement Waste
- Strengthening Communication to Avoid Rework
If you’d like a simple checklist to help you spot these hidden costs or want to talk about ways to reduce waste on your floor, let’s connect.
Remember: costs don’t cut themselves. But you can. And it starts today.
Ready to Start Lowering Costs and Recovering Lost Time?
POWERS specializes in helping manufacturing teams uncover hidden costs, reduce waste, and improve productivity without adding unnecessary complexity. From overtime creep and reactive repairs to excess material movement, our proven approach equips supervisors to see where time and money slip through the cracks.
By aligning frontline leaders and daily habits with operational goals, we help you build a workplace culture where controlling costs isn’t an afterthought it’s part of how work gets done.
To make this even easier, POWERS developed DPS, our next-generation production management system. DPS combines the right set of digital tools and real-time performance data to equip your team with the right information to accelerate decision making and boost production.
Whether you’re looking to cut overtime, reduce rework, or simplify how you track daily performance, POWERS and DPS can help you get there.
Ready to lower costs and unlock your operation’s full potential?
Contact POWERS today to learn how our expertise and DPS solutions can help you maximize output, drive sustainable savings, and recover time that’s too valuable to lose.
- Speak to an Expert: Call +1 678-971-4711 to discuss your specific challenges and goals.
- Email Us: Get tailored insights by emailing info@thepowerscompany.com
- Request an Assessment: Use our online contact form, and one of our expert manufacturing consultants will reach out to schedule an in-depth analysis of your operations.