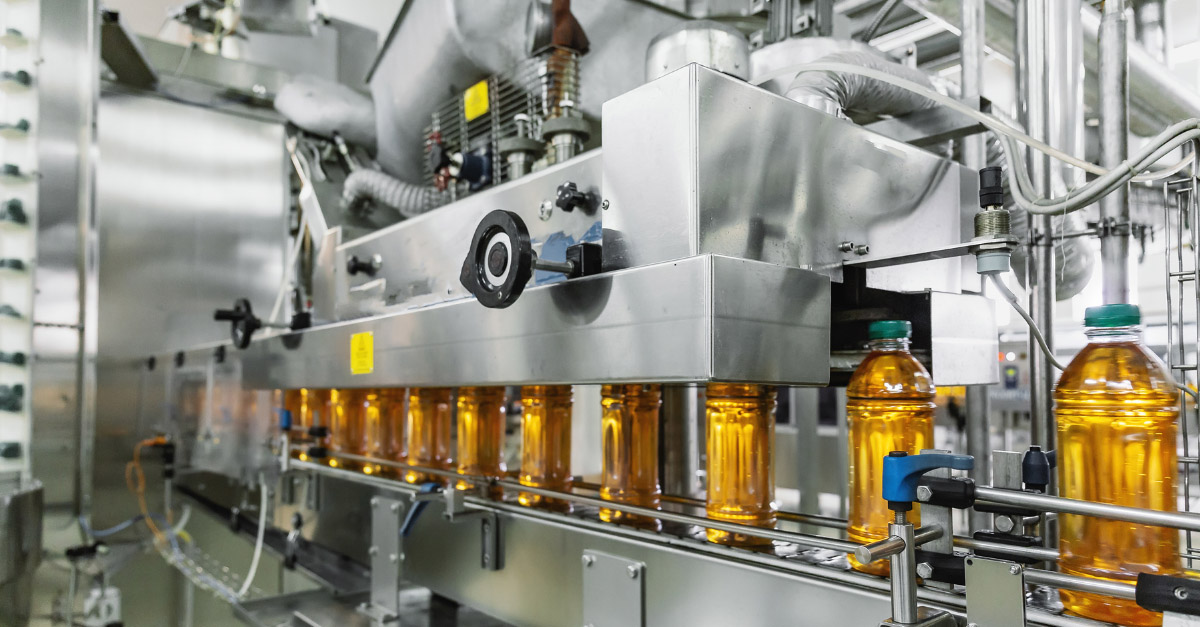
In a large-scale manufacturing ecosystem, every process, system, and behavior is interwoven to create the final output and satisfy customers. At the center of this intricate web is Maintenance, Repair, and Operations (MRO).
MRO isn’t merely about fixing what’s broken—it’s about proactively optimizing every asset, from tools to equipment to expansive infrastructure. Yet, it’s often relegated to the sidelines until something goes wrong.
The consequences of neglecting maintenance touch every part of a manufacturing business, affecting essential metrics such as downtime, quality, scheduling, and more.
Let’s dive deep into the top 10 ways poor maintenance processes, standards, and behaviors can lead to these detrimental outcomes in large-scale manufacturing.
1Impact on Overall Equipment Effectiveness (OEE)
One of the most significant metrics impacted by poor maintenance is Overall Equipment Effectiveness (OEE).
OEE is a comprehensive metric combining equipment availability, performance efficiency, and product quality to present a holistic view of production efficiency.
Each component of the OEE is directly influenced by maintenance:
- Availability: This component captures the actual run time of equipment compared to the planned production time. Every unplanned downtime due to equipment failure directly reduces the availability score, making proactive and predictive maintenance essential.
- Performance: Even if equipment is available, it might not be running at optimal speeds due to wear and tear or suboptimal conditions—another area where maintenance comes into play.
- Quality: The quality score in OEE reflects the products manufactured without defects. Poorly maintained equipment can lead to quality issues, increasing the rate of defective products.
Given its comprehensive nature, a dip in OEE due to inadequate maintenance can have a profound impact on a manufacturer’s bottom line..
2Compromised Production Quality
Beyond OEE, equipment not operating optimally can lead to more frequent product defects. Reworks, recalls, and wasted materials all contribute to direct losses, while the long-term effects can include tarnished brand reputation and reduced customer loyalty.
3Unpredictable Production Schedules
When equipment breaks down unexpectedly, sticking to production timelines becomes a challenge. This unpredictability can result in late orders, contractual penalties, and lost business opportunities.
4Strained Supply Chain Dynamics
Every bottleneck in production, often a consequence of poor maintenance, sends a ripple effect across the supply chain. It can lead to inventory build-ups, increased warehousing costs, or missed opportunities in fast-paced markets.
5Lower Return on Assets (ROA)
Each piece of equipment is an investment. When its lifespan is shortened due to inadequate maintenance, the return on that investment diminishes. Effective maintenance not only extends the life of assets but optimizes their operation, directly enhancing ROA.
6Increased Operational Costs
Emergency repairs, especially those needed during off-hours, can be significantly costlier than scheduled maintenance. Furthermore, the ripple effects of unplanned downtimes—like rushed deliveries and overtime wages—add to operational costs.
7Safety and Compliance Risks
A manufacturing floor with poorly maintained equipment is a breeding ground for accidents. This not only jeopardizes the safety of the workforce but can also lead to regulatory fines and increased insurance premiums.
8Management’s Strategic Oversights
A singular focus on production numbers without accounting for equipment health can backfire. This oversight reflects a gap in management’s strategic planning, emphasizing a more integrated approach where maintenance is part of the broader business strategy.
9The Inevitability of Technological Evolution
The fourth industrial revolution brings with it tools like the Computerized Maintenance Management System (CMMS), IIoT, and Digital Twins. Not adapting to these technologies means manufacturers miss out on data-driven insights and predictive maintenance capabilities, which are fast becoming industry standards.
10The ‘Reactive’ Pitfall
Many organizations fall into the trap of a reactive approach—addressing issues as they arise. This shortsightedness often leads to more extended downtime, higher costs, and compromised product quality. Shifting the mindset from reactive to proactive can be transformational.
To truly appreciate the importance of maintenance, it’s essential to recognize its ripple effect. Just as a tiny pebble can create expansive ripples in a pond, so too can poor maintenance touch every facet of manufacturing.
A proactive, data-driven, and strategic approach to maintenance doesn’t just prevent losses—it can catalyze unprecedented growth. In an industry that’s constantly evolving, it’s those who prioritize and innovate in the realm of maintenance that will emerge as leaders.
Unlocking Maintenance Excellence with POWERS’ AMP Program
In the demanding realm of manufacturing, maintenance is the cornerstone of sustainable productivity. Recognizing gaps in your maintenance processes is just the beginning.
For genuine optimization, manufacturers need a comprehensive approach. Enter POWERS and its innovative AMP (Advanced Maintenance Performance) program.
POWERS’ 3-Step Maintenance Discovery Process provides a robust approach to enhance maintenance:
1 Maintenance Performance Assessment:
POWERS conducts a detailed OEE analysis, scrutinizing equipment maintenance effectiveness. Along with this, the current maintenance management systems and processes are evaluated, and the maintenance team’s training and proficiency undergo an in-depth review.
2Action Plan Development:
With the understanding that unplanned downtime costs the manufacturing industry billions annually, POWERS formulates actionable strategies tailored to the organization’s unique challenges. The goal? Seamless integration of new protocols and best practices to boost productivity.
3MMOS and Technology Update:
Emphasizing the need to move away from outdated tracking methods, POWERS advocates for upgrading your Maintenance Management Operating System (MMOS). Integration of systems like the Computerized Maintenance Management System (CMMS) is advised, streamlining maintenance processes, and reducing downtime.
The journey to enhanced maintenance practices is transformative. POWERS, leveraging its vast experience in manufacturing maintenance, offers a holistic solution with the AMP program. From in-depth analysis to providing improvement blueprints, the AMP program stands unparalleled.
Dive into the POWERS difference. Embark on a journey of maintenance excellence with a detailed OEE analysis, address skill and training gaps, create an actionable plan, and seamlessly implement it. Elevate your maintenance workforce and boost performance.
For a deeper understanding, download the FREE Maintenance Assessment Guide. Jumpstart your journey to optimized maintenance by contacting the POWERS team at +1 678-971-4711 or email info@thepowerscompany.com.