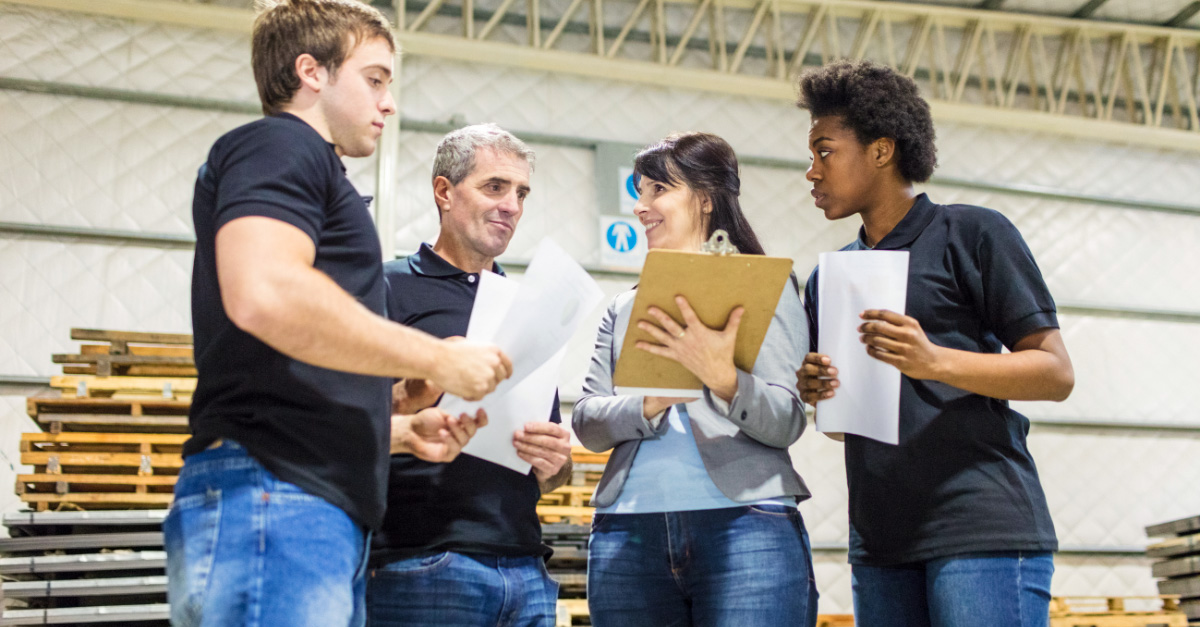
When a crisis hits, whether it’s a breakdown in your supply chain, a critical equipment failure, or a sudden labor shortage, frontline leaders are the ones who feel it first. They’re the face of the organization to the workforce and the first line of defense for keeping operations on track.
At POWERS, we’ve worked shoulder-to-shoulder with manufacturing teams navigating real-world operational crises. We’ve seen what derails production, and more importantly, what keeps it moving. Here’s what effective frontline leadership actually looks like when everything’s on the line.
🔧 1. Get Grounded in the Facts, Not the Fire
When things start going sideways, it’s easy for leaders to get caught up in the noise, especially when everyone’s asking questions and jumping to conclusions. But strong frontline leaders resist the urge to react to every spark. They slow down just enough to verify what’s really happening.
- That means:
Walking the floor and checking with operators directly, not just relying on what’s passed through three layers of hearsay. - Reviewing production data or shift reports before escalating issues.
- Focusing on what’s happening now, not just who to blame.
In a crisis, reacting without clarity often leads to the wrong fix or worse, more damage. Getting grounded in the facts helps leaders prioritize correctly and model steady leadership under pressure.
📣 2. Communicate with Calm Urgency
Crises breed uncertainty, and uncertainty breeds anxiety. When people don’t hear from leadership, they fill in the blanks themselves, and usually with worst-case scenarios.
The best frontline leaders don’t go silent. They step in and communicate clearly, even when they don’t have all the answers. The goal is to reduce confusion, focus the team, and keep people moving forward.
That includes:
- Holding brief, frequent huddles to give status updates, even if it’s just “Here’s what we know right now.”
- Repeating the message across shifts so nobody’s left in the dark.
- Being honest about what’s unknown while reinforcing what the team can control.
A calm, steady voice becomes a stabilizing force. And consistency in the message builds trust fast.
👣 3. Model the Right Behavior
Your team will mirror what you do. In high-pressure situations, frontline leaders set the tone more than any corporate memo ever could. If a supervisor cuts corners, blows up over delays, or ignores safety protocols, it gives silent permission for others to do the same.
But when leaders stay composed, follow the standard work, and keep holding the team to clear expectations, that discipline cascades throughout the shift.
What it looks like:
- Following PPE rules even when nobody’s watching.
- Sticking to the escalation process instead of improvising under stress.
- Checking in with individuals, not just barking orders.
Your crew doesn’t need a superhero. They need someone consistent, predictable, and present.
⚖️ 4. Prioritize Ruthlessly
Crisis means chaos. Everything feels urgent. But if everything is a priority, nothing gets done. Effective leaders learn to triage quickly and decisively.
Ask:
- What’s going to stop production next?
- What creates a safety hazard if left unresolved?
- What can wait an hour, or a day?
Prioritization isn’t just about production, it’s about preserving team focus and avoiding burnout. Frontline leaders who can quickly sort noise from necessity are the ones who keep their teams productive, even under pressure.
They also push back when upper management throws too much at once, protecting the team’s ability to execute rather than just react.
🔄 5. Keep Accountability Tight
One of the biggest issues during a crisis isn’t lack of effort, it’s lack of clarity. Who’s doing what? When? With what authority? That fog slows down response time and opens the door to mistakes.
Effective frontline leaders:
- Assign names, not departments.
- Use checklists or visual boards to track real-time progress.
- Follow up and close loops quickly, “Did we fix it?” is just as important as “Who’s fixing it?”
In moments of stress, teams don’t need micromanagement, but they do need structure. A tight feedback loop between assignment and action makes all the difference.
🔍 6. Reflect After, Not During
While the crisis is active, your job is execution. But when it settles, whether in a few hours or a few days, that’s the moment to learn.
Debriefs don’t need to be formal to be effective. A 10-minute review with the team can uncover key takeaways:
- What worked well?
- What slowed us down?
- What gaps in training or tools were exposed?
Capturing those insights helps build a more resilient operation. It’s how you turn a crisis from a fire to put out into a learning moment that strengthens the team going forward.
Where POWERS Comes In
We help manufacturing teams turn leadership from a title into a daily behavior, especially in high-pressure environments. Whether it’s a line stoppage or a plant-wide emergency, consistent habits and clear expectations are what drive performance.
At POWERS, we don’t teach leadership in the abstract. We coach supervisors in real time, on the floor, aligning their actions with the operational goals that matter most. From improved shift execution to faster recovery from disruptions, we help frontline leaders lead with purpose and clarity.
And with our DPS, our digital production system, teams get real-time visibility and structured workflows that reduce confusion and support accountability, crisis or not. It’s leadership, supported by data, built into daily routines.
Ready to make your shop floor more resilient, more agile, and more productive, even under pressure?
- Speak to an Expert: Call +1 678-971-4711 to discuss your specific challenges and goals.
- Email Us: Get tailored insights by emailing info@thepowerscompany.com
- Request an Assessment: Use our online contact form, and one of our expert manufacturing consultants will reach out to schedule an in-depth analysis of your operations.