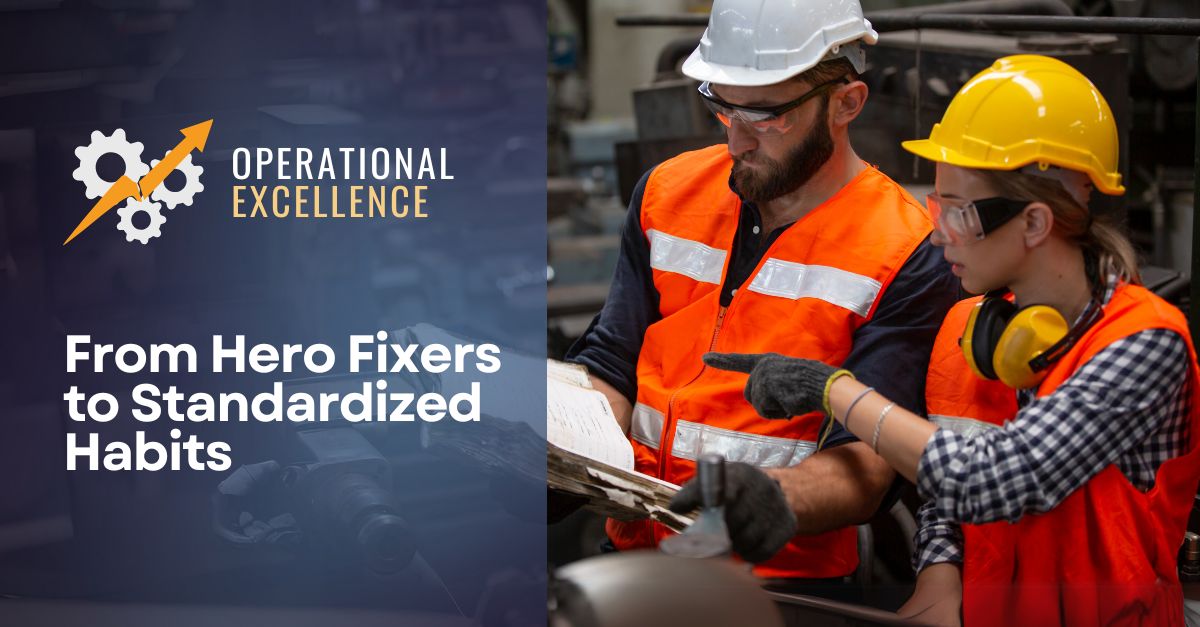
POWERS
On the manufacturing shop floor, frontline supervisors are often the unsung heroes—troubleshooting breakdowns, tweaking processes, and keeping lines running with hard-earned expertise.
With an aging workforce and rising automation reshaping manufacturing, the path to operational excellence lies in building standardized, repeatable habits that empower every team member. By codifying expertise into clear routines, supervisors can drive efficiency, ensure resilience, and deliver the scalability that executives demand.
The Trap of Hero-Driven Habits
Every plant has its go-to fixers: the supervisor who instinctively adjusts a finicky machine, the operator who knows just how to nudge a setup. These habits, honed over years, seem like strengths—until you measure their limits. When expertise lives in a few heads, training stalls, onboarding drags, and performance hinges on specific individuals. A single retirement or absence can cripple a shift. One plant saw a 12% output drop when a veteran supervisor left, taking undocumented calibration tricks with them. Another lost $150,000 annually because only one operator could handle a complex changeover.
The data paints a clear picture: operations dependent on individual expertise face 20% longer recovery times from disruptions.
Conversely, plants with standardized habits—where routines are documented and teachable—see 10–15% higher overall equipment effectiveness and 25% faster training cycles. Hero-driven habits may win battles, but they lose the war for efficiency and future readiness.
The Challenge: Scaling Expertise
Shifting from hero-driven to standardized habits is tough. Supervisors take pride in their problem-solving prowess; asking them to codify their “magic” can feel like diminishing their value. Operators may resist documented routines, seeing them as bureaucratic. Yet, the stakes are high. With 30% of manufacturing workers set to retire by 2030, irreplaceable expertise is walking out the door. Meanwhile, automation and digital tools demand consistent, repeatable processes to maximize returns. Clinging to hero habits risks bottlenecks, errors, and missed opportunities.
The deeper issue is mindset. Hero fixers thrive on autonomy, but that autonomy creates variability. One supervisor’s tweak might boost output today but confuse the next shift. Standardized habits aren’t about stifling skill—they’re about amplifying it across teams, shifts, and years. For executives, this scalability translates to lower costs, higher output, and a workforce ready for tomorrow’s challenges.
A Roadmap to Standardized Habits
Supervisors, you’re the linchpin in this shift. Your expertise is invaluable, but it’s time to make it a team asset. Here’s how to build standardized habits that drive excellence:
1Document Critical Routines:
Identify one high-impact task—for example, a machine setup or troubleshooting step—you perform instinctively. Write it down in clear, teachable steps. One plant documented a supervisor’s changeover routine, cutting setup time by 18% when shared across shifts.
2Test and Refine with Teams:
Pilot the routine with your crew, gathering feedback to ensure it’s practical. A supervisor who standardized a quality check habit reduced defects by 15% after two weeks of team tweaks.
3Train and Reinforce Daily:
Embed the habit through short, daily drills. Use visual aids or checklists to make it stick. Plants that train standardized habits daily see 20% higher adoption rates than those relying on one-off sessions.
4Measure and Celebrate Impact:
Track the habit’s effect on metrics like uptime or cycle time. Share wins with your team to build momentum. A facility that standardized maintenance checks lifted OEE by 12% and boosted team morale with public recognition.
The Impact: A Scalable, Resilient Floor
Standardized habits don’t just streamline today’s work—they future-proof your operation. When routines are teachable, new hires ramp up faster, retirements don’t disrupt, and automation integrates seamlessly. One manufacturer standardized operator troubleshooting habits, slashing training time by 30% and boosting throughput by 10%. Another company codified supervisor-led huddles, cutting shift transition errors by 20%. For executives, these gains mean millions in savings, higher returns on capital, and a workforce that scales with growth.
Relying on hero fixers is a habit your plant can’t afford.
Our decades of manufacturing experience at POWERS show that standardized habits unlock operational excellence. Tools like DPS, our Digital Production System, codify the shift into repeatable routines. Start today: document one routine that only you can do. What habit will you standardize to transform your floor?
About POWERS
At POWERS, we partner with manufacturing firms to tackle tough challenges—like codifying productive habits into sustainable and scalable systems, processes, and behaviors. Our approach sharpens operations through process improvements, boosts productivity with leadership and workforce training, optimizes supply chains, and drives maintenance performance to boost profit. We’re all about results: higher efficiency, less downtime, and stronger teams.
To take it further, we created DPS, a digital production system that puts real-time data in your hands. DPS streamlines workflows, tracks critical KPIs like downtime and capacity utilization, and keeps your team aligned for sustainable gains—no fluff, just tools that work—for better decisions and better outcomes every shift.
Ready to change the habits that are holding you back? Reach out to POWERS to explore how our experience and DPS can help you push your operations to a new standard of excellence.
- Speak to an Expert: Call +1 678-971-4711 to discuss your specific challenges and goals.
- Email Us: Get tailored insights by emailing info@thepowerscompany.com
- Request an Assessment: Use our online contact form, and one of our expert manufacturing consultants will reach out to schedule an in-depth analysis of your operations.