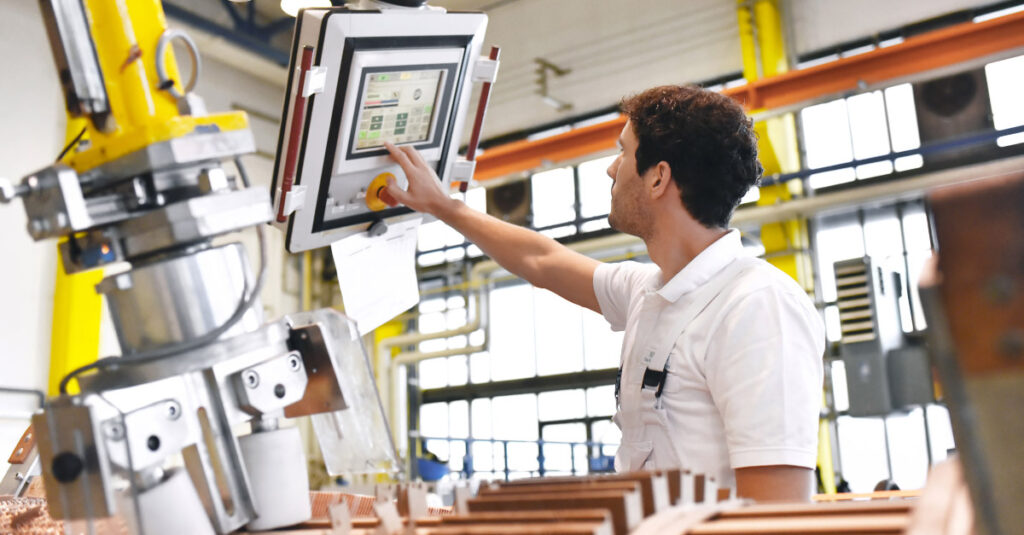
OEE, or Overall Equipment Effectiveness, is a critical measure of productivity within the manufacturing sector. 100% OEE indicates perfect production. However, a significant number of manufacturing organizations operate at a productivity rate of merely 60%, signaling a vast opportunity for improvement.
Unpacking OEE
Overall Equipment Effectiveness is a performance indicator that gauges the proportion of scheduled production time that is truly effective. An OEE score of 100% signifies flawless production, indicating that only good parts (zero defects or loss) are manufactured, at the highest rate possible, with no downtime.
OEE functions both as a benchmark and a baseline: When utilized as a benchmark, overall equipment effectiveness helps in comparing the performance of a specific production unit against industry norms, similar units within the organization, or results across various shifts working on the same equipment.
As a baseline, OEE aids in monitoring the progress made over time in eliminating waste from a particular production unit.
Defining OEE Scores
To comprehend the efficiency of an OEE score, one must be familiar with what is considered an excellent OEE score. An OEE score of 100% indicates perfect production, whereas a score of 85% is world-class among discrete manufacturers and can serve as a long-term goal for many organizations.
An OEE score of 60% is typical for discrete manufacturers but signifies a significant potential for improvement. For manufacturing companies just beginning to track and optimize their performance, an OEE score of 40% isn’t unusual.
This score is relatively low and can generally be improved effortlessly through straightforward measures, such as tracking reasons for stoppage time and addressing major sources of downtime sequentially.
The aim should always be to measure your OEE score against industry norms for discrete manufacturing and aim for world-class outcomes.
HOW TO CALCULATE OVERALL EQUIPMENT EFFECTIVENESS
Breaking Down OEE Calculations
So, how is the OEE score calculated? At its most basic, OEE is the ratio of Fully Productive Time to Planned Production Time. OEE calculation is as follows: OEE = (Good Count × Ideal Cycle Time) / Planned Production Time.
Here, ‘Good Count’ refers to pieces manufactured devoid of defects. The ‘Ideal Cycle Time’ is the fastest possible time theoretically needed to manufacture one piece. ‘Planned Production Time’ is the total scheduled production time for the equipment, and ‘Fully Productive Time’ refers to manufacturing only good parts, at the fastest rate possible, with no stop time.
The Preferred Method for OEE Calculation
The preferred method to calculate OEE provides a deeper insight into the waste generated during manufacturing by dividing it into three factors:
- Availability Loss
- Performance Loss
- Quality Loss
OEE is the ratio of Fully Productive Time to Planned Production Time. However, the OEE calculation needs to consider Schedule Loss, as production is not intended to be run during this period.
Availability, Performance, and Quality Calculations
Availability accounts for Availability Loss, which includes events that halt planned production for a considerable duration. Availability is computed as Availability = Run Time / Planned Production Time, where Run Time = Planned Production Time - Stop Time.Availability is computed as Availability = Run Time / Planned Production Time , where Run Time = Planned Production Time - Stop Time.
Reaching Perfect Production
Achieving perfect production or an OEE score of 100% means achieving a Quality, Performance, and Availability score of 100%. Real-world examples provide an excellent opportunity to master the OEE calculation.
Actionable Metrics for the Plant Floor
While OEE is a valuable tool for managers, it can seem abstract for frontline leaders and employees on the plant floor. Real-time, easily comprehensible, and highly motivational goals work best for this part of your workforce.
It’s, therefore, important to translate OEE into your organization’s daily, actionable goals and communicate them clearly to your team. At POWERS, we use the Plan, Actual, Variance, Action (PAVA) method to help determine those goals, build the daily performance metrics that will impact your OEE score, and design a customized plan to achieve them.
What is Your Plan?
‘Plan’ refers to the optimal performance target. The equipment or production line ‘Plan’ could be a higher percentage target of uptime, capacity, throughput, or more. The ‘Plan’ could be a reduced spoilage or rework target percentage. The ‘Plan’ could also be an industry or competitor benchmark, or the manufacturer’s specified capacity on a piece of equipment. Determining your target is vital to mapping performance gaps. Without it, it’s like planning a trip without knowing the destination.
What is Your Actual Performance?
‘Plan’ refers to the optimal performance target. The equipment or production line ‘Plan’ could be a higher percentage target of uptime, capacity, throughput, or more. The ‘Plan’ could be a reduced spoilage or rework target percentage. The ‘Plan’ could also be an industry or competitor benchmark, or the manufacturer’s specified capacity on a piece of equipment. Determining your target is vital to mapping performance gaps. Without it, it’s like planning a trip without knowing the destination.
What is the Variance to Plan?
Measuring and reporting performance gaps in critical KPIs is the next key to performance improvement. Just like planning a road trip, knowing how far away you are from your destination informs decisions on resources like fuel, rest stops, and important milestones along the way.
And Finally, Action!
Taking ‘Action’ to improve performance is not only a first step; it’s a daily step. If this were a road trip, you’ve now understood the starting point, destination, and distance between those two points. You have also carefully designed a plan utilizing the right resources along the way. Now, it’s time to put that plan into action, get moving toward that target destination, and build in the daily disciplines to achieve it!
The POWERS Difference
We are a dedicated and results-driven management consulting firm uniquely positioned at the intersection of workplace culture and operational performance. We partner with growth-oriented organizations to cultivate a culture of excellence that fuels productivity, drives efficiency, strengthens competitive advantage, and improves OEE.
Leveraging our deep industry expertise and innovative methodologies, we build synergies between people and processes, creating holistic, sustainable change that translates into measurable business outcomes.
Our team has helped executive leadership across many industries operationalize their culture for rapid and sustained performance improvement, increased competitive advantage, greater value, and a stronger bottom line.
To put our experienced team and proven track record to work for you, schedule an initial discovery and analysis by calling +1 678-971-4711, or emailing us at info@thepowerscompany.com