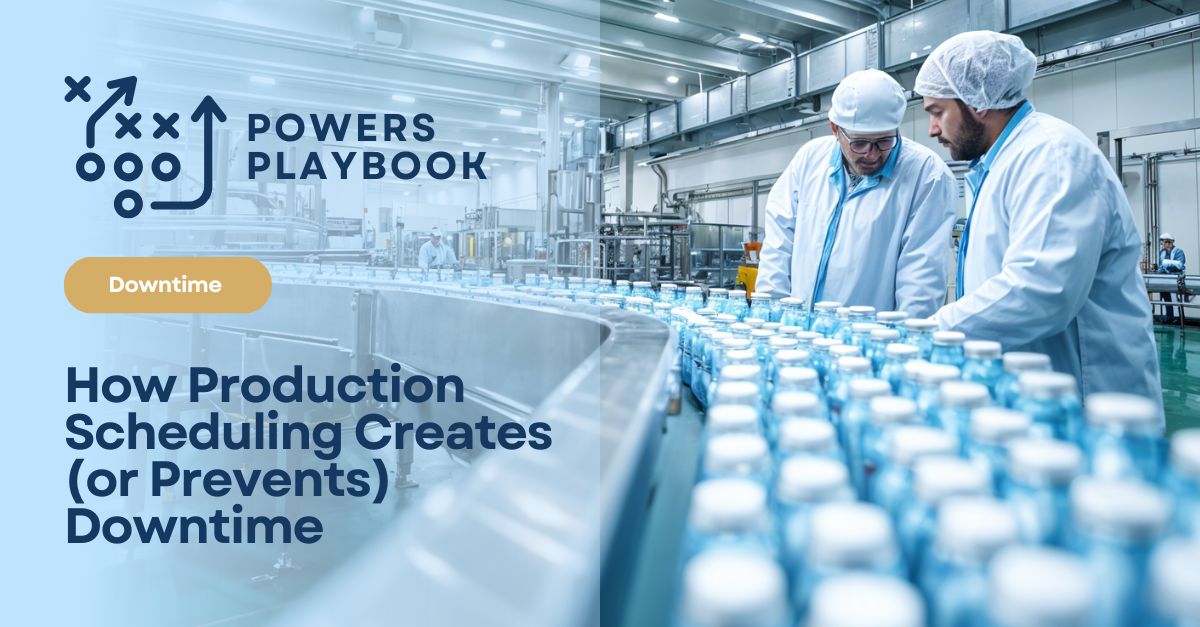
Production schedules can either keep your lines moving, or leave your crews standing around, burning payroll, and missing targets.
It’s easy to think of the schedule as “someone else’s job”, something handled by planners or corporate. But on the floor, a bad schedule shows up fast: missing parts, rushed changeovers, crews getting pulled in five directions. It turns good operators into firefighters and good equipment into bottlenecks.
A lot of it is baked into the day before the first machine even starts.
In this Playbook, we’re breaking down the real-world ways scheduling hurts, or helps, your shift, and simple moves frontline leaders can make to spot trouble before it costs you.
How Bad Scheduling Creates Downtime
If you’re seeing a lot of unplanned stops, you can’t just look at machines or operators, you need to take a hard look at the daily plan.
Here’s where poor scheduling quietly creates losses:
- Material delays: Your crew is ready, but the parts aren't. Waiting for missing material is still downtime, and it's usually avoidable if the schedule and staging match.
- Changeover chaos: If the plan doesn’t account for the real time needed to swap molds, tooling, or setup, you’ll either rush (and introduce defects) or run late and lose hours.
- Bad sequencing: Flipping between simple and complex jobs with no logic leads to confusion, setup mistakes, or work getting backed up at inspection.
You can have the best people and equipment in the world, but if the schedule sets them up to fail, you’ll still lose time and money.
Quick Win:
Many downtime events that look like operator errors or machine failures are really symptoms of bad scheduling.
What Frontline Leaders Can Do About It
You don’t have to completely rewrite the schedule, but you can work smart inside the one you’re given. Here’s how you stay in front of it:
-
Double-check critical materials.
Take two minutes at the start of the shift or before changeover. If key parts, fixtures, or tools aren’t staged, flag it fast. No one likes scrambling at the last second -
Review changeovers ahead of time.
Look for heavy setup jobs stacked too close together. If the schedule is tight, ask for extra support or flag the risk to the supervisor. Planning just 15 extra minutes for a complicated swap can save an hour of rework or re-inspection later. -
Prioritize based on risk, not just the order of jobs.
Sometimes you need to reshuffle within the shift. If a complex setup is scheduled late in the day when everyone's tired, it's better to move it earlier. Talk it through in the pre-shift meeting. -
Speak up early, not during the firefight.
If you spot gaps or risks in the day’s plan, don’t wait until you're already bleeding time mid-shift. Raise it early, even if it’s just a heads-up. Early awareness gives leadership a chance to adjust. -
Track specific issues.
If bad schedules keep causing problems, don’t just vent, document. Example: "Lost 1.5 hours waiting for parts on job 12345" gives leadership something they can act on. General complaints don't.
Quick Win:
Be the eyes on the floor for schedule risks. You can’t fix every problem, but you can stop a lot of downtime before it happens.
Red Flags You Can Spot Before They Become Downtime
Keep your eyes open for these common warning signs:
- Materials missing when you're doing pre-shift checks.
- No setup time between complicated or tooling-heavy jobs.
- Job sequence doesn’t make sense based on experience or complexity.
- Last-minute hot orders thrown on the schedule with no staging or prep.
Every one of these is a slowdown waiting to happen if no one calls it out early.
Bottom line:
If the schedule doesn’t make sense before the first machine starts, it sure won’t make sense once you’re under pressure. Catch it before it catches you.
Wrapping Up Our Downtime Series: One Lesson Across Every Shift
All month long, we’ve been digging into one big idea:
Downtime isn’t random. It’s usually preventable if you know what signs to watch for and take early action.
Here’s the full series we covered:
🔹 Don’t just track downtime, track what you do about it.
Just measuring downtime doesn’t fix anything. It’s what you change based on the numbers that matters.
(→ Read it here)
🔹 Tight startups and clean shift handoffs cut downtime before it starts.
How you start a shift (and how you hand it off) decides if you’re fighting problems all day or staying ahead.
(→ Read it here)
🔹 Root cause thinking is the only way to solve real downtime problems.
If you only patch the surface issues, downtime keeps coming back. Solve for root causes, not symptoms.
(→ Read it here)
🔹 Downtime isn’t a mystery, most of the time, the warning signs are right in front of you.
Missed cues, ignored risks, sloppy startups, downtime usually sends plenty of signals. You just have to spot them.
(→ Read it here)
Final Word: Build a Shift That Wins, Not One That Chases Problems
Downtime doesn’t just cost production, it drains resources, eats into margins, and breaks momentum. Lost minutes stack into lost shifts. Lost shifts stack into lost profits.
At POWERS, we specialize in helping manufacturing teams streamline operations, optimize daily workflows, and get the most out of their existing workforce.
Our proven approach equips frontline leaders with practical skills to spot risks early, manage smarter, and align behaviors with operational goals, so you’re not just tracking downtime, you’re eliminating it.
To push results even further, we developed DPS, a next-generation manufacturing operating system that integrates lean principles with real-time digital tools. DPS empowers factory supervisors to make faster, data-driven decisions, eliminate hidden inefficiencies, and sustain productivity improvements, without the need to add unnecessary headcount.
DPS also includes a powerful Knowledge Base designed for the shop floor, making it easier than ever to share best practices, capture lessons learned, and speed up onboarding for new hires. Because in manufacturing, lost knowledge leads to lost time, and DPS helps you keep your edge.
Ready to cut downtime, protect profits, and unlock your full operational potential?
Contact POWERS today to learn how our hands-on support and DPS solutions can help you control lost time before it controls your business.
- Speak to an Expert: Call +1 678-971-4711 to discuss your specific challenges and goals.
- Email Us: Get tailored insights by emailing info@thepowerscompany.com
- Request an Assessment: Use our online contact form, and one of our expert manufacturing consultants will reach out to schedule an in-depth analysis of your operations.