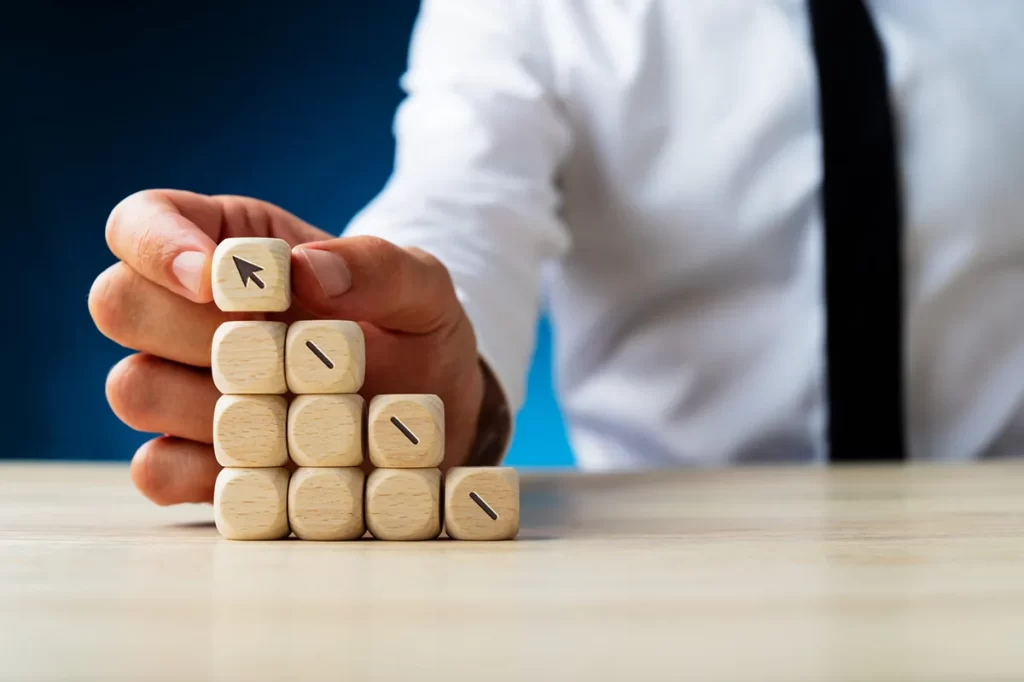
Kaizen is a Japanese term that means “continuous improvement” or “change for the better.” In the groundbreaking 35-year-old book, Kaizen: The Key to Japan’s Competitive Success, Masaaki Imai introduced the concept to the western world. Today, it’s used as a methodology to help companies improve and evolve.
What are the five principles of Kaizen?
The Five Fundamental Kaizen Principles are embedded in every tool that Kaizen uses. These principles are:
- Know Your Customer – This principle is about creating customer value by identifying their interests and understanding where they’re coming from.
- Let It Flow – The focus of this principle is targeting zero waste so everyone within the organization strives to create value and eliminate waste.
- Go to Gemba – This principle focuses on the importance of following the action. Because value is created where things happen, one should go there.
- Be Transparent – The goal of this principle is to speak with real data so that improvements are both tangible and visible.
- Empower People – With this principle, the focus is on organizing teams, setting goals for the team, and providing them with the tools and processes to achieve them.
How does Kaizen help organizations?
Organizations that are struggling with a lack of productivity, too much downtime, and ultimately losing money may turn to Kaizen for help. The main benefit of the Kaizen methodology is that it will give organizations the ability to evaluate their processes and systems so that they can ramp up productivity and make sure they are performing to capacity.
What do businesses learn from Kaizen?
Kaizen gives organizational leaders the tools to better understand their employees’ strengths and weaknesses. By using Kaizen, business leaders will learn that:
- Every employee is important.
- Employees are experts in their specialties.
- Employees can bring new ideas and improvements to the table.
- Leaders can work side-by-side with employees to find solutions to organizational problems.
What is a Kaizen blitz and how does it work?
A Kaizen event is called a Kaizen blitz, and this is a short-term project designed to improve productivity and accomplish results. A Kaizen blitz inspires commitment and dedication in employees and will typically lead to high-impact results. During this five-day process, the organization focuses on process improvement, problem solving, and approaches for continuous improvement.
How is the POWERS method different from Kaizen?
Kaizen is a valuable methodology and a tool that enables organizations to take a look at their systems and processes and improve them. Where the POWERS method differs from Kaizen is that it goes beyond the short-term, high-impact results. While Kaizen invites leaders to assess systems and processes, the focus is not on changing the behaviors of the employees engaging in those systems and processes.
While organizations will typically see short-term results from a Kaizen blitz, within a few months, everything will back to the status quo. Then they may need to have another Kaizen blitz to see the same results.
POWERS focuses more on long-term, sustainable results. At POWERS, we work side-by-side with frontline leaders to ensure both managers and employees alter the necessary behaviors for long-term process improvement. While the POWERS process is a longer process than Kaizen, it is easier to see significant process improvement over a period of months or even years.
Are you interested in seeing significant long-term improvements to your organization’s productivity and thus profitability? Contact us to learn more about how we can help.