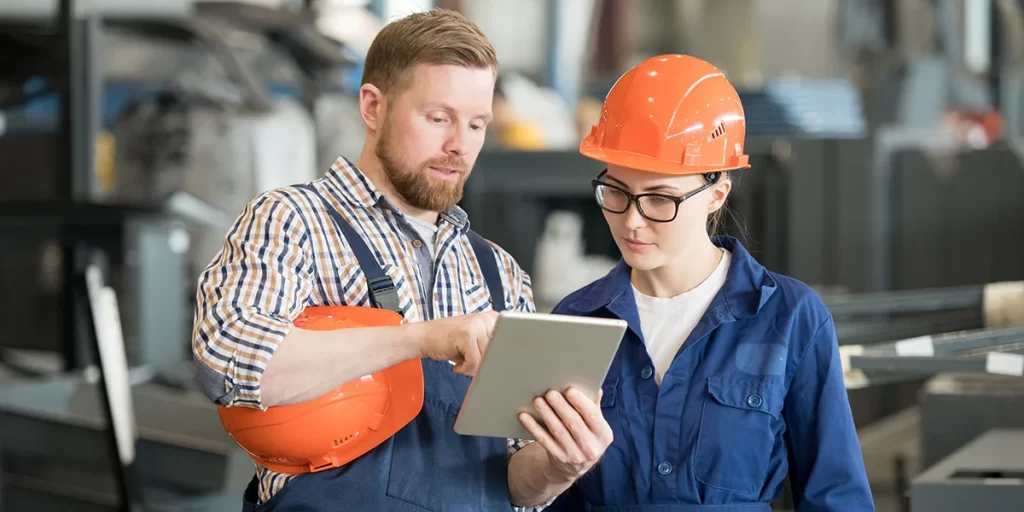
Global Potato Processor
Based in Idaho, our client supplies French fries, hash browns and other formed-potato products to global fast-food companies, restaurants, distributors and retail customers. Its highly automated plants operate 24/7 nonstop, except for a day of scheduled equipment sanitation every three weeks. Maximum equipment uptime and utilization are imperative. The client engaged The Powers Company to help it reduce maintenance expenditures; handle and control parts purchasing and inventory; schedule/ optimize maintenance resources; and reduce equipment downtime, particularly the sanitation turnaround.
The project began in Manitoba, Canada, followed by plants in Idaho and North Dakota. Initial analyses at all three revealed a complete void of planning maintenance work and zero oversight of outside contractors’ costs and activities. In addition, there was no coordination between maintenance and parts management.
Problems
Plants had a 36-hour window to clean and maintain all equipment. As soon as production stopped, sanitation started. However, startup got later and later, cutting into runtime, as cleaning was still underway. Maintenance staff didn’t begin their work until sanitation was out of the way. Lacking visibility into when all activities could take place, they just showed up to an area and hoped for the best.
The Powers Company determined how long it took for the teams to clean each piece of equipment and each area, then outlined cleaning tasks in proper sequence and in order of priority. We developed a sanitation preparation schedule that tightly orchestrates production,
maintenance and sanitation activities. Laying out the critical path identified pockets of time when maintenance could get into each area and activities that could be done concurrently. Sanitation could also see and flex around planned maintenance work.
Enabling this collaboration compressed cleaning turnaround from 36 to 18 hours. In addition, a new scorecard details all measured activities leading up to the sanitation period. For example, it ensures that all appropriate parts are ready and needed contractors are scheduled for the correct day.
Objectives
No maintenance work outside of the designated sanitation period was planned, scheduled or assigned to the skilled onsite mechanics, who were essentially there for emergencies. Yet, if something broke, a contractor would be called to repair it instead. Mechanics cherry-picked the work orders they wanted and disappeared for hours instead of tackling higher-priority jobs. This created a large backlog and contributed to downtime. What’s worse, there was an open checkbook for overtime, but no visibility into or management of the dollars spent or hours used.
Upon arrival, we had all mechanics document on a pocket card how they spent every minute of their workday. This revealed a utilization rate of just 35 percent of available hours for repairs or PMs. Next, we developed a Daily Schedule Control that shows all employees working a specific day and their available hours to schedule work. Now, each mechanic is allotted a full day’s worth of open work orders.
Companion pocket cards list mechanics’ individual assignments and allow supervisors to track progress and follow up assignments. Implementing a new daily/weekly operating report provides visibility into KPIs for individual shops and the entire maintenance department. Display boards in each shop show the mechanics’ and the shop’s performance, providing feedback. With mechanics involved in their performance, the culture has turned 180 degrees: Mechanics are more engaged, proactive and focused on doing things better. Supervisors know the status of assigned work throughout the day and can adjust resources if needed. The upshot? Utilization has jumped to nearly 80 percent.
Strategies
Unmanaged outside contractors provided a major source of rampant uncontrolled spending. In Idaho, contractors walked the floor every day identifying work for themselves. Supervisors often paid purchase orders for work performed six months earlier without anyone knowing what they were for. No one in the building knew which contractors should be on-site that day or for the week, or how much they would cost. With no structured scheduling, there was no visibility into or control over contractor use or overtime excesses, despite low utilization.
The North Dakota electrical shop consisted of on-site contractors operating under an expired contract. They were regularly billing overtime and double-time. The number working each week or day to day was unknown until managers received a report a week later. The Powers Company instituted authorization controls in both plants. Now, the use of contractors and overtime has to be justified and approved upfront. Authorized contractors have to be on an approved list to get through security. These changes delivered immediate improvement in costs and accountability.
Results
Inadequate processes and controls for managing parts led to delays, duplicated effort, unpredictable cost increases and waste. The parts kitting process was poorly defined between the storeroom and maintenance. This resulted in hours of time searching for and procuring parts, and frequently paying to expedite them. Five satellite storerooms were in disarray.
Confusion over who was doing what hindered inventory accuracy and status changes on work orders. The Powers Company visually documented and flowcharted the process; clarified and realigned roles and responsibilities; and conducted training to get everyone on the same page.
Now, each supervisor has a planner who locates and orders parts, and schedules mechanics’ work for when both parts and equipment are available. Mechanics have the parts and guidance to do their jobs, and supervisors have the visibility and tools they need to follow up and supervise.
Laying the foundation and implementing an effective Maintenance Management Operating System equips departments to plan, assign, execute, follow up, report on and review the work. Preventive maintenance and top-priority work is being identified and completed consistently, averting breakdowns and costly downtime.
Sanitation
- Created sanitation preparation schedule
- Synchronized Maintenance, Production and Sanitation
Maintenance
- Enabled scheduling of maintenance work during production using available resources/capacity
- Instituted overtime authorization
- Formalized outside contractor management
- Deployed a planning & scheduling tool
- Established pocket cards and daily schedule control
- Instituted daily/weekly operating report
- Implemented weekly review meeting process with action-item log review • Developed sanitation preparation schedule
Maintenance Purchasing
- Formalized the parts-kitting process
- Deployed purchase price variance tool
- Developed a cycle count methodology
- Cleaned up storerooms
- Implemented vendor scorecards