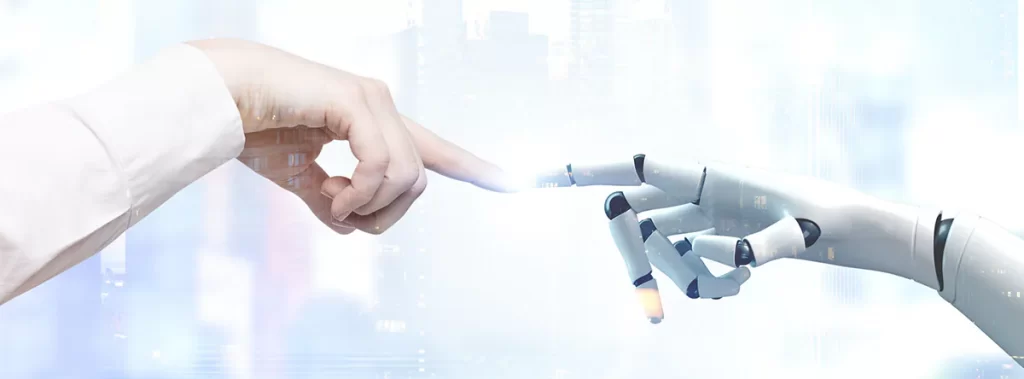
From cooperative robots to time-saving algorithms, we’re looking ahead at technology’s role in long term economic recovery
While COVID-19 has pummeled all industries, it has arguably dealt the mightiest blow to the manufacturing industry. As Artem Kroupenev wrote in Industry Week, “For the first time in modern manufacturing history, demand, supply and workforce availability are affected globally at the same time.”
To tackle these remarkable challenges, many leaders in the industry have turned their eyes toward artificial intelligence (AI) and how this rapidly evolving technology could benefit long term recovery plans.
As it turns out, the manufacturing industry may be uniquely suited to the incorporation of greater AI integration. “With the vast quantities of data available (…) due to its use of sensors and networks and the use of data being more valuable than ever before, the manufacturing industry is primed for the adoption of artificial intelligence (AI) to drive business value, during these uncertain times,” Georgia Wilson wrote in ManfacturingGlobal.com.
A global survey conducted by Forbes this year, sponsored by Intel, Accenture, and SAS, revealed that AI deployment now consists of more than just individual experiments and use cases and entered into an industry-wide level of adoption. The survey also found that many organizations are currently in the process of shifting their operations, and that AI adoption is gaining momentum quickly. While a relatively low number (26%) of manufacturing respondents reported that they were currently using AI-based technology, half (50%) of the respondents said that these new tools were under development.
So how is AI being used in manufacturing? Here are six use cases.
1. Humans and robots working together
As James Cameron predicted in the Terminator franchise: The rise of the machines is here. Thankfully, though, it’s looking a lot friendlier than it did in the dystopian Arnold Schwarzenegger films. “Cobots” (collaborative robots) are already working alongside human workers, effectively functioning as another set of hands. These cobots are able to multitask, whereas autonomous robots are typically programmed to learn and perform one particular task at a time. Cobots are also able to avoid obstacles. That elevated spatial awareness gives them the ability to work alongside human workers without causing any injury or breaking anything.
Cobots typically operate on factory assembly lines and perform tasks that require heavy lifting. For instance, in automotive factories, cobots can lift heavy car parts and hold them in place while human workers perform essential tasks on them. Additionally, the cobots are able to locate items inside large warehouses more efficiently.
2. Predictive maintenance can lower costs and improve safety
Predictive maintenance (PdM) entails intuitive, scheduled repairs designed to avoid the need for repairs only when equipment breaks down. AI-based predictive maintenance is utilized in many manufacturing plants to anticipate servicing needs.
Companies risk losing time, money, and resources with premature or irregular equipment maintenance. AI-based predictive maintenance therefore greatly benefits manufacturing plants by reliably managing the upkeep process.
3. Robots don’t get bored by tedious tasks
While cobots are more beneficial on the front lines of production, in the back office, robotic process automation (RPA) software is much more useful. RPA software can handle high-volume, repetitive tasks and transfer data across systems, calculations, queries, and record maintenance.
RPA software can also automate order processing . This eliminates workers’ need to enter data manually, which reduces inputting mistakes and saves organizations labor and time.
4. Algorithms can predict demand
AI systems can detect and predict buying patterns by using machine-learning algorithms. This can provide much-needed insights to manufacturers as they determine when and how to ramp up production. This way, manufacturers can produce highly in-demand inventory before the stores even request it.
5. Digital twins boost performance
A digital twin–a virtual model of a physical object–can be used to better understand the complex workings of specific machinery. This allows organizations to monitor equipment throughout its lifecycle, getting critical alerts before problems arise.
One common use of a digital twin is with airplane engines. Every time a plane takes off or lands, sensors attached to the engine transmit data to the engine’s digital twin. This provides the airline and the manufacturer with important information about how the engine’s holding up.
6. AI can boost supply chain management
Supply chain management can greatly benefit from the use of artificial intelligence. For example, a large manufacturer may need to process millions of purchases, orders, ingredients, or materials. Removing the need to handle these processes manually reduces the need for additional time and resources. For this reason, many manufacturers have begun to automate their supply chain processes with artificial intelligence.
Looking ahead
In May 2019, Antony Bourne of Industry Week shared three major predictions about AI in manufacturing: By the end of 2021, he posited, 50% of all manufacturing organizations will use AI in some form; and as soon as the end of 2020, pick-and-place robots will put away 25% of manufactured products.
According to SAS, a leading authority on artificial intelligence, the development and adoption of AI will vary depending on facilities’ operating environments. According to Georgia Wilson of Manufacturing Global, these factors will include process maturity, analytics, trust, and amount of oversight.
Are some manufacturers resistant to this new technology? Andrew Ng of Fortune recently pointed out that non-digital companies tend to move slowly to embrace artificial intelligence. For example, the Manufacturers Alliance for Productivity and Innovation Foundation recently surveyed 200 manufacturers, and only 5% of them stated they had a clearly defined strategy for the deployment of artificial intelligence.
But who knows: One of the results of this economic disruption may be that artificial intelligence sees its day sooner rather than later. As the manufacturing industry adapts and evolves, we’ll all stay tuned.
To receive more industry insights like this, as well as other updates and news from POWERS, please sign up for our newsletter here.