Culture Powers People Productivity Performance Profitability Potential
Developing your frontline leaders and building a thriving workplace culture empower your workforce to achieve critical operational performance improvements that are sustainable and scalable.
Culture Powers People Productivity Performance Profitability Potential
Developing your frontline leaders and building a thriving workplace culture empower your workforce to achieve critical operational performance improvements that are sustainable and scalable.
Trusted by More Global Market Leaders to Deliver Peak Operational Performance
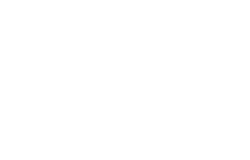
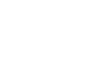
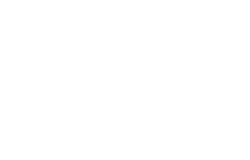
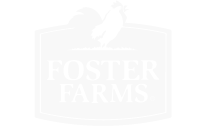

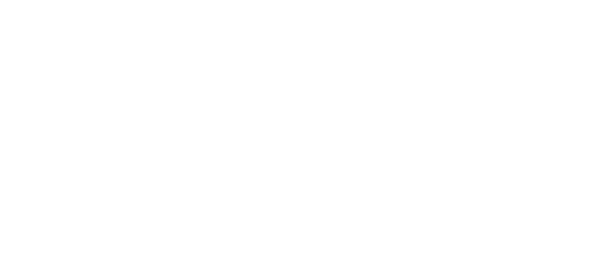
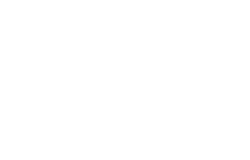
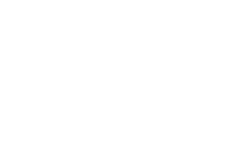

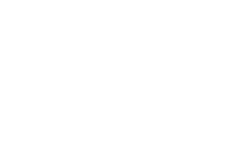
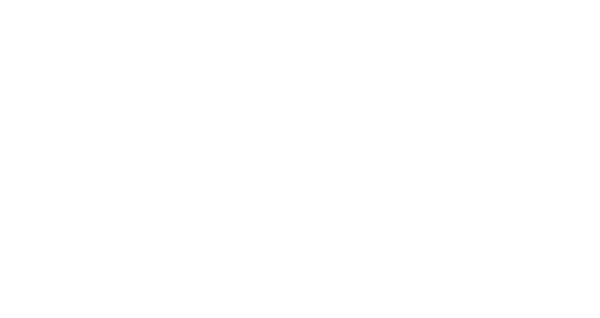
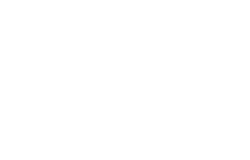
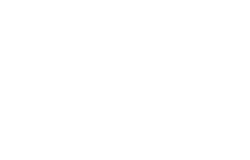

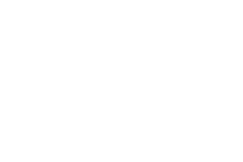
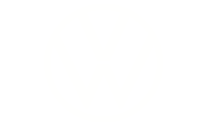
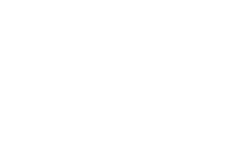
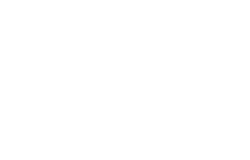
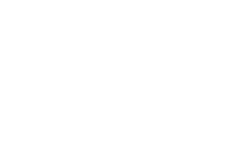
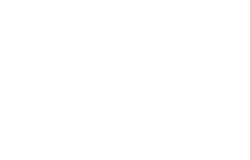
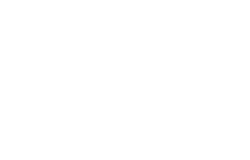
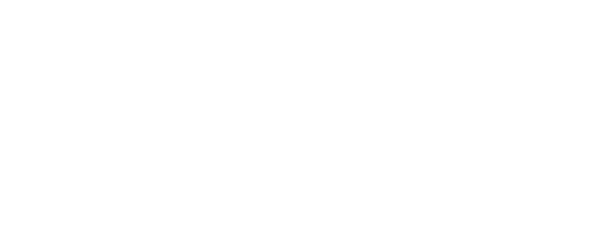
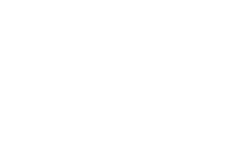
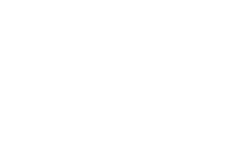
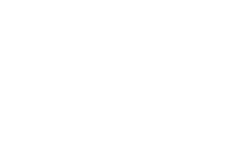
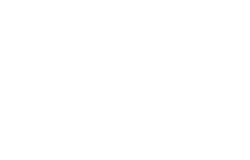
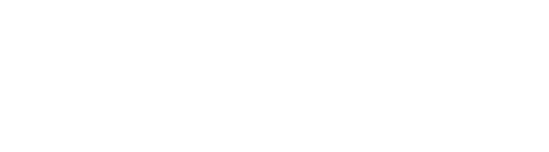
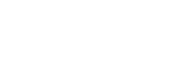
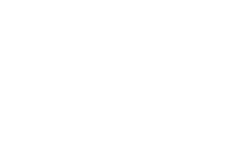
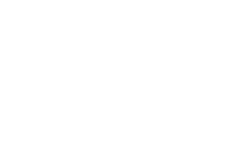
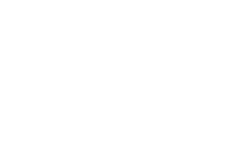
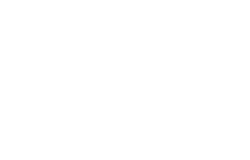
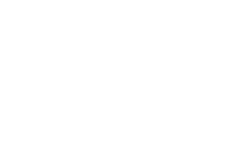
Why We’re Different
We Connect the Dots Between Workplace Culture and Peak Operational Performance
We help global manufacturing and service sector leaders uncover and leverage opportunities for measurable and sustainable operational performance improvements in critical areas of their organization’s value chain.
Our unique approach aligns your company’s leadership and workforce behaviors to your company culture and core values to achieve operational performance improvements that transform productivity, reduce costs, increase value, and build competitive advantage.
Our proven methods and expertise in management consulting can return millions to your bottom line. And through our focus on building a thriving culture that empowers your workforce, your team will reach and sustain these critical operational performance improvements in months, not years.
Our Focus on Frontline Leadership Development Transforms Operational Performance
LEADERSHIP OPTIMIZATION
Leadership Behaviors
Communication & Education
Cultural Control Points & Cogs
Cultural Connections
Cultural Cadence
Cultural Ownership & Adoption
=
OPERATIONAL PERFORMANCE
Capacity
Yield
Throughput
Uptime
Cost Management
Labor Cost
Return on Assets
Margin
What We Do
Management and Productivity Expertise Focused on Mission-Critical Areas of Your Organization
78% of top manufacturing executives list frontline leadership training and development as a key to reducing costs and improving margin. According to Harvard Business Review, frontline managers make up roughly 60% of a company’s management ranks.
Frontline managers and supervisors are the glue that holds a business together and can make or break key manufacturing metrics such as capacity, throughput, uptime, and margin. In addition, they are responsible for many of the day-to-day operations and most directly impact the health of your business and its culture.
Unfortunately, they are also typically the team members with the least amount of managerial experience and leadership training, often promoted due simply to seniority.
When training these frontline supervisors and managers to be more effective leaders and improve teamwork, companies face many challenges, including high turnover. It takes a lot today to attract and retain great people.
A recent survey from Woohoo Inc. showed that the number one reason employees have a “bad day at work” is their manager’s lack of help and support. Time again, employees leave bad managers, not employers.
So, how can POWERS help? First, we have the expertise to train your frontline personnel into the leaders you need to drive productivity and transform performance.
We work side-by-side with your frontline managers and supervisors to uncover any challenges and put the right skills and behaviors in place to transform performance. And our leadership training provides the tools and techniques to make these performance improvements trainable and sustainable. Find out more.
Supply chain systems are becoming increasingly complex, involving a global network of people, processes, resources, activities, ESG (Environmental, Social, Governance) criteria, and technologies.
As the demand for better integration becomes more challenging, so does the opportunity for growth.
As your company considers strategic growth, it's important to incorporate an SCM solution that works on every level because effective and efficient supply chain management is one of the largest contributors to increased revenue and decreased costs.
At POWERS, we conduct an extensive review of your company’s supply chain, starting with your broad sales forecasts up to procurement, forecast trends, all the way through to delivery.
Because each company has its own set of specific pressure points, our dedicated team creates a tailor-made business solution to help meet the needs of every aspect of your supply chain. Find out more.
Downtime costs most factories somewhere between 5% and 20% of their production capacity. Unplanned manufacturing downtime can cost your business millions every year.
Your maintenance team’s primary job is to maximize uptime, ensuring you’re operating at or near full capacity and product is flowing to your customers.
If your maintenance team’s performance is a drag on production, in areas like predictive and preventive practices, staffing, planning, parts inventory, and scheduling, your overall capacity, not to mention your bottom line, will suffer.
There are many maintenance philosophies, ranging from a mentality of “run until it breaks” to constant monitoring and repair of equipment.
Regular, planned maintenance is essential in preventing the failure of critical equipment, which can significantly affect productivity. In most manufacturing facilities, predictive and preventive maintenance programs ensure the best performance.
The experts at POWERS can help you develop and implement a best-practices and continuous improvement plan to maximize your maintenance program’s effectiveness.
We’ll help improve your maintenance performance, scheduling, labor utilization, and decrease overtime. Find out more.
27% of manufacturing workers are set to retire over the next ten years, taking their specialized skills and institutional knowledge with them. This statistic is already hitting the manufacturing sector hard contributing to lost productivity and efficiency.
As a matter of fact, the majority of manufacturing companies run at only 60 to 80% efficiency. Therefore, focusing on shop floor excellence best practices can be genuinely transformative for driving performance improvement and achieving full capacity. But implementing effective training programs can be challenging.
To significantly impact manufacturing shop floor excellence, everyone in the organization must be pulling in the same direction. This incremental process improvement begins with team leadership. The site leader must be dedicated to a compelling vision for organizational excellence and be able to communicate it persistently and consistently at all levels. POWERS can help your team get there and stay there with the right plan and the right training.
Our proven method of best practices ensures the highest degree of shop floor excellence in your manufacturing facility.
We look at everything from what you measure, how you measure it, to overall quality, communication, cost, and control mechanisms to optimize your processes, and improve your performance. Find out more.
Supply chain systems are becoming increasingly complex, involving a global network of people, processes, resources, activities, ESG (Environmental, Social, Governance) criteria, and technologies.
As the demand for better integration becomes more challenging, so does the opportunity for growth.
As your company considers strategic growth, it's important to incorporate an SCM solution that works on every level because effective and efficient supply chain management is one of the largest contributors to increased revenue and decreased costs.
At POWERS, we conduct an extensive review of your company’s supply chain, starting with your broad sales forecasts up to procurement, forecast trends, all the way through to delivery.
Because each company has its own set of specific pressure points, our dedicated team creates a tailor-made business solution to help meet the needs of every aspect of your supply chain. Find out more.
The most essential part of any company is the people. So, when work culture isn’t engaging your workforce, individual productivity and overall performance suffer. Essentially, people leave.
Therefore, strong workplace culture is not only the key to increased performance, but it also helps you attract and retain the right talent. Employees’ overall ratings of their company’s qualities, like collaboration, work environment, and mission and value alignment, are 20% higher at companies with strong cultures.
According to Forbes, culture has to do with “Company vision, values, norms, systems, symbols, language, assumptions, beliefs, and habits.” Company culture is essentially the personality of a company.
Culture is how your entire organization behaves, communicates, and interacts internally and externally. It’s your DNA. Most importantly, it’s how your organization creates and builds a sustainable competitive advantage.
It’s not something that employees bring with them. That’s why it’s our aim at POWERS is to train your entire organization on the behaviors that not only exemplify and embody your company culture but deliver maximum performance now and over the long haul.
This “operationalization” of your company culture is part of our Culture Performance Management™ (CPM) methodology and can be genuinely transformative to your organization. Find out more.
The most essential part of any company is the people. So, when work culture isn’t engaging your workforce, individual productivity and overall performance suffer. Essentially, people leave.
Therefore, strong workplace culture is not only the key to increased performance, but it also helps you attract and retain the right talent. Employees’ overall ratings of their company’s qualities, like collaboration, work environment, and mission and value alignment, are 20% higher at companies with strong cultures.
According to Forbes, culture has to do with “Company vision, values, norms, systems, symbols, language, assumptions, beliefs, and habits.” Company culture is essentially the personality of a company.
Culture is how your entire organization behaves, communicates, and interacts internally and externally. It’s your DNA. Most importantly, it’s how your organization creates and builds a sustainable competitive advantage.
It’s not something that employees bring with them. That’s why it’s our aim at POWERS is to train your entire organization on the behaviors that not only exemplify and embody your company culture but deliver maximum performance now and over the long haul.
This “operationalization” of your company culture is part of our Culture Performance Management™ (CPM) methodology and can be genuinely transformative to your organization. Find out more.
How We work
Our “Boots on the Ground” Discovery and Implementation
We are not typical management consultants or operations advisors. Instead, we are a team of highly experienced, boots-on-the-ground analysts, facilitators, and implementers.
We roll up our sleeves and work side-by-side with your entire team, in your facilities, out on your factory floor, and soak up your company culture.
This immersive discovery and analysis technique fuels our unique implementation process. The findings help us train and develop your frontline leaders, empower your workforce, and improve your business systems and processes to achieve years of critical productivity gains in a matter of months.
These team “wins” translate directly to improving your bottom line and strengthening your workplace culture.
We have deep-level manufacturing operations, management, finance, supply chain, facilities, logistics, infrastructure, and human resources experience to make targeted productivity improvements sustainable, delivering immediate and long-term value.
We’ve been successful for global leaders across many industries. As a result, our clients typically realize a substantial Return On Investment.
Get the latest leadership engagment and development insights delivered to your inbox every month
Get Started Now
Find Out How a Thriving Culture Can Unleash the Potential of Your Entire Workforce
Let’s tackle the critical performance improvements you’re looking for and transform your business in months, not years.
Schedule an initial assessment with one of our performance improvement experts today by calling +1 678-971-4711, emailing info@thepowerscompany.com, or by clicking the link below.
Read Our Case Studies
We Measure Our Success Through Our Clients’ Achievements
Featured
Stronger Systems and Smarter Leadership Drive 65% Scrap Reduction for Renowned Animal Nutrition Producer
Project Overview Overview A leading manufacturer in the animal nutrition industry partnered with POWERS to improve quality, reduce labor inefficiencies, and establish consistent operating procedures across two facilities on a shared campus. Facing elevated scrap rates, high Cost of Poor Quality (COPQ), and inconsistent labor utilization, the organization sought to
Library