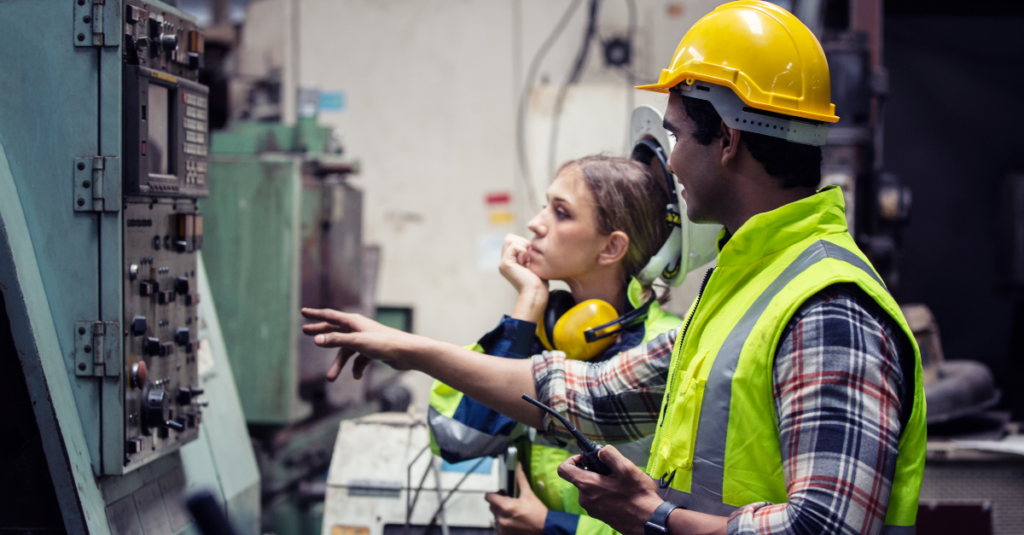
Manufacturers must be proactive in addressing the scarcity of technically skilled maintenance technicians. Investing in training your people and providing the resources they need to be successful has never been more critical.
American manufacturers are becoming increasingly concerned about the lack of technically trained maintenance personnel. The shortage of well-trained, experienced maintenance technicians can seriously impact uptime, capacity, quality, and ROA (return on assets). According to Industry Today, the so-called ‘talent gap’ is due to technological advances, changing demographics, and new priorities for younger generations of workers. A survey in Manpower found that 69% of employers struggle to fill positions requiring technical skills such as maintenance.
What Role Does Maintenance Play in Creating Value
Maintenance is a vital area for manufacturers to produce at the highest value throughout their value chain. One of the most critical variables impacted by maintenance is uptime because it directly affects a manufacturer’s capacity to produce goods and satisfy client needs.
Equipment failures can result in expensive downtime if maintenance technicians don’t step in and fix them immediately. This unplanned downtime can result in missed production deadlines, lost revenue, and decreased customer satisfaction.
A lack of sufficiently trained and available maintenance technicians can also inhibit overall business growth and increased capacity. Inadequate or poorly executed maintenance can result in equipment breakdowns and decreased efficiency, eventually limiting a business’s capacity to satisfy client demands.
Another area where the lack of qualified technical maintenance professionals has a negative effect is quality. When equipment is not maintained correctly, it may not run as optimally as it should, resulting in low-quality output. This may result in expensive rework, or even product recalls, which can substantially harm the company’s brand and bottom line.
The lack of technically qualified maintenance technicians also impacts return on assets and OEE, two critical performance metrics in manufacturing. Equipment’s lifespan might be shortened, and repair costs can rise due to improper maintenance. Manufacturers may see a decline in their return on assets due to having to spend more money on equipment maintenance, parts, and more.
What Can You Do to Attract and Retain More Technically Skilled Workers?
Manufacturers must be proactive in addressing the scarcity of technically skilled maintenance technicians. Investing in training programs for current personnel is one way to ensure they have the abilities and knowledge required to maintain equipment properly. On-the-job training, apprenticeships, and technical schools are all viable options for achieving this.
Investing in technology and a robust MMOS (maintenance management operating system) that can help with planning, scheduling, and resource allocation for maintenance activities, such as predictive maintenance software, or a comprehensive CMMS system, is an additional approach. This technology can assist in predicting impending equipment breakdowns, saving downtime, increasing productivity, and OEE (overall equipment effectiveness).
Manufacturers want to think about collaborating with educational institutions to create initiatives that will aid in educating the upcoming generation of maintenance specialists. This can be accomplished through collaborations, sponsorships, or even the development of internal training programs.
Another option is to contract with outside service companies to perform maintenance work. As it eliminates the need for manufacturers to spend money on personnel training and hiring, this can be a cost-effective alternative. However, it’s crucial to confirm that the service provider possesses the abilities and knowledge required to properly maintain the machinery.
The role and obligations of the service provider must also be clearly understood, and a method must be in place for evaluating their performance.
Offering flexible hours, competitive pay, and benefit packages are additional methods manufacturers can use to solve the shortage of technically trained maintenance workers. As qualified technicians are more likely to stay with a company that values their expertise and offers them competitive pay and benefits, this can help attract and retain these skilled workers.
Finally, manufacturers ought to think about starting a mentoring program. This can aid new and inexperienced technicians by allowing more experienced technicians to mentor and support them.
Companies may consider coaxing retired maintenance workers back to establish a mentoring program and pass along their years of experience and skills to younger workers. This aids in fostering an organizational culture of learning and development as well as assisting new technicians in gaining the requisite skills and knowledge.
Manufacturers should make sure they have a strong recruitment plan in place in addition to the aforementioned fixes to attract the best people. Utilizing social media and professional networks, going to job fairs, and recruiting events, and providing internship and co-op programs are some examples of how to do this.
Conclusions for Business Leaders
American manufacturers are very concerned about the lack of highly qualified technical maintenance personnel since it has a lot of adverse effects on uptime, capacity, quality, and return on assets. Ultimately, if your maintenance department is understaffed, poorly trained, or underperforming, you’re going to take a hit on your bottom line.
Manufacturers must adopt a proactive strategy to address this issue by investing in training programs for the current maintenance workforce, technology that can help with maintenance tasks, collaborating with educational institutions to create programs that can train the upcoming generation of maintenance technicians, outsourcing maintenance tasks, providing competitive pay and benefits, putting a mentorship program in place, and having a strong recruitment strategy.
By doing this, businesses can ensure that they have the personnel that is qualified to satisfy consumer expectations, boost productivity, OEE, and boost return on assets.
POWERS AMP (Advanced Maintenance Performance) Program
Our POWERS AMP (Advanced Maintenance Performance) Program improves both the tactical and technical aspects of maintenance in your operation. On the tactical side, we focus on improving your strategic approach to maintenance and your Maintenance Management Operating System: how you manage the people and resources devoted to maintaining your assets and equipment.
We also focus on the technical aspects of maintenance and provide hands-on training in Maintenance Fundamentals, Mechanical Concepts, Electrical Power, and Electrical Control.
Nearly 60% of the current manufacturing maintenance workforce does not possess the skills and training necessary to keep the assets and equipment functioning at optimum levels. Improving your maintenance team’s skills unlocks OEE (Overall Equipment Effectiveness) bottlenecks in uptime, throughput, capacity, quality, and more.
The POWERS Difference
At POWERS, we focus on Leadership Engagement and Development to transform operational performance and prepare your leaders for the future. We help you build a performance culture that operates at peak levels to lower costs, increase productivity, build agility, and sustain that performance over the long haul.
Our team has helped executive leadership across many industries operationalize their culture for rapid and sustained performance improvement, increased competitive advantage, greater value, and a stronger bottom line.
Find out about our new AMP (Advanced Maintenance Performance) Training Program and put experienced team and proven track record to work for you. Schedule an initial discovery and analysis by calling +1 678-971-4711, or emailing us at info@thepowerscompany.com.