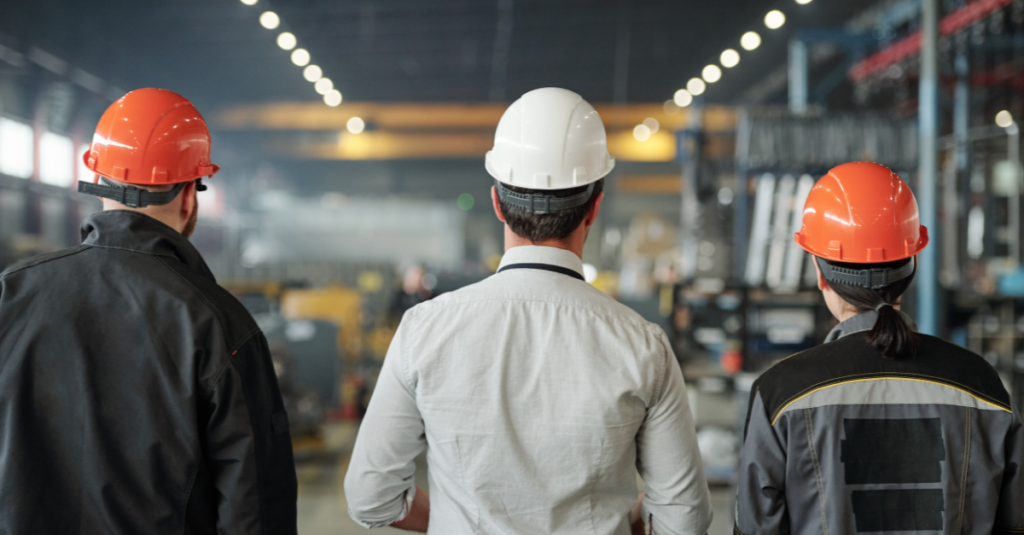
No matter which way the econonomic winds blow, belt-tightening across the value chain is here. Manufacturers need to foster a culture of peak performance and efficiency to lowers costs now.
As the U.S. economy continues to try and normalize to a new post-pandemic standard, there is little doubt that costs continue to rise for manufacturers. Prices are still up nearly across the board from vital raw materials for production, energy to operate facilities, or fuel for transporting goods throughout the supply chain and to the end consumer.
Although the PPI (Produce Price Index) dropped slightly recently (due mainly to slight relief in fuel prices), it continues at historic levels, according to the Bureau of Labor Statistics. However, opinions are mixed on whether consumer spending will ultimately be affected by surging prices as consumer confidence enjoyed a recent rebound.
With a still-tight jobs market, labor costs remain high. According to a recent report, the employment cost index rose by 1.3% in the second quarter.
Whether we see demand pushing producer and consumer prices even higher or flagging demand due to continued inflation concerns, belt-tightening across the value chain is here. As a result, finding every way to lower costs, operate more efficiently, yet perform at ever-higher standards, continue to be hot topics with our clients.
So how can you meet increased demand while the prices you pay for everything seem to be going up with no end? How, for example, do you balance a just-in-time (JIT) inventory control system with rising fuel prices affecting the cost of more frequent deliveries? And with rising costs producing the specter of inflation as a real threat to the economy, will the potential weakening demand require intensive cost reductions, shifting suppliers, or product line overhauls?
No matter how this year goes, there is no room to wait for optimizing, finding efficiencies, implementing best practices, and reducing costs across your entire value chain. This means your organization can do plenty right now to address rising costs.
So, let’s talk about the key strategies we typically discuss with our clients:
- Optimizing processes to improve efficiency and productivity
- Reducing waste and cutting costs (internally and throughout the supply chain)
- Improving maintenance performance
- Empowering your frontline leaders to operate at peak performance
Through each of these strategies, our approach is to align your stated company culture and core values with your desired performance outcomes to create a culture that operates at peak performance and efficiency.
1. Increase Productivity at Start-up, First-hour, and Shift Changes
Focus on and optimize the segments of your production process that traditionally put a strain on capacity: start-up, first-hour, and shift changes. There’s been a long-standing and somewhat accepted view that there will always be some drop-off in performance during these production phases. The bottom line? There doesn’t have to be. Nor should you allow it to continue. Start-up, first hour, and shift change processes are often some of the first places we look for immediate capacity utilization increases.
2. Identify and Eliminate Production Bottlenecks
Another critical step to increasing productivity is evaluating your entire production process flow, identifying the capacity bottlenecks, and formulating a plan to address and eliminate them. Again, it comes down to a simple fact. Your line’s actual capacity and overall productivity are determined by your least productive process along your value chain, from inputs to outputs. In the simplest terms, if your production phase produces 100 units (per hour/shift/day, doesn’t matter), but your packaging stage is only able to complete only 85, then your capacity is 85.
Throttling back completed unit production to 85 may risk revenue, ROI, satisfying customer demand, and more. Adding costs (labor, equipment) to increase packaging to 100 units may threaten the overall profitability of the product line. Again that’s an elementary example of a very complex manufacturing issue, but it illustrates the problem. Line balancing and analyzing process flow to identify and eliminate bottlenecks and maximize capacity and throughput is vital to increasing productivity.
3. Reduce Wasteful Processes
Focus on what it means to be lean! Eliminating the lost time and waste contributors inside your organization from the shop floor to the top floor is the fundamental tenet of lean manufacturing practices. Organizations can reduce waste by zeroing on these seven critical areas identified in lean practices.
- Transport – Optimize transport functions to reduce or eliminate unnecessary relocation, handling, and motion of materials, tools, and people. Waste occurs with inefficient movement between workstations, along production lines, or across the factory floor.
- Inventory – Balance raw material and production against customer demand to reduce excess inventory. This can free up the valuable plant and warehouse space, reduce invested capital, and reduce damage and obsolescence.
- Motion – Eliminate unnecessary reaches, grasps, pick-ups, or moves. This action applies to your people, machine operations, and move distances. Modify or adjust equipment to minimize the travel distance of the product, raw material, or packaging materials.
- Waiting – Eliminate wait times for material, people, or equipment in the production process. These add unnecessary costs. Balance process flows to reduce wait times, optimize output from one operation for the subsequent operation, and match total customer order fulfillment rates.
- Over-processing – Analyze your production process for opportunities to eliminate any steps that do not add value. These steps typically add unnecessary costs and represent waste.
- Overproduction – Eliminating excess work-in-process and finished goods inventory resulting from overproducing a part, sub-assembly, or finished product can drastically reduce waste. Eliminating overproduction is especially important in food processing, where the product can quickly spoil or be damaged.
- Defects – Work to eliminate all defects throughout the process flow and to achieve “perfect” product quality. Defective products that require rework or must be discarded add cost. Ensure that all quality control limits are set correctly to prevent rejection of a good product or acceptance of a defective product. Analyze all process flows, control limits, and operating procedures to set correct limits and ensure each step is necessary to add value.
4. Don’t Stop at the Shop Floor
Waste reduction in manufacturing doesn’t begin and end on the factory floor. Look to other areas of your organization to reduce waste and lower costs. Unnecessary administrative steps, communication, and meetings can all add overhead costs and should be evaluated. Taking a lean approach means leading by example. If you’re cutting costs out on the factory floor but leaving the corporate offices untouched, that can send the wrong message across your enterprise.
Look outside your organization to your supply chain partnerships for further waste reduction. Can you develop relationships with suppliers closer to your production facilities to reduce transportation costs? Is there an opportunity to commit to a longer-term with a supplier to secure lower prices? Examining and optimizing your supply chain is a subject matter unto itself. You should never actually stop streamlining your supply chain to increase efficiencies and lower costs.
5. Increase Your Maintenance Effectiveness
Nothing hurts production capacity like equipment failure or poorly implemented maintenance practices. An operation that poorly utilizes its maintenance staff, has no daily work plan, preventive maintenance schedule, or well-established priorities can create a reactive, emergency response culture and increase costs dramatically.
Another tenet of lean manufacturing practices, Total Productive Maintenance (TPM), is a holistic approach to equipment maintenance that strives to achieve zero breakdowns, small stops, slow running, defects, and accidents. A TPM approach emphasizes proactive and preventative maintenance to maximize the operational efficiency of the equipment. It empowers operators to help maintain their equipment working in concert with maintenance staff.
Implementing a TPM program creates a shared responsibility for equipment that encourages greater involvement by plant floor workers. A company culture aligned to performance outcomes can effectively improve productivity (increasing uptime, reducing cycle times, and eliminating defects).
For immediate improvement in maintenance performance, we recommend focusing on a few key areas that are a typical drag on TPM.
- Daily preventative maintenance planning and scheduling
- Equipment pre-check and inspection processes
- New equipment installation planning
- Equipment start-up preparation and execution procedures
- Start-up downtime tracking and root-cause-analysis
6. Engage and Empower Your Frontline Leaders
Your frontline leaders are the heart of your organization and one of your most valuable resources for increasing productivity and reducing waste. They help ensure that your business runs smoothly and continuously improves by delivering the daily KPIs that determine your overall performance. None of the suggestions discussed throughout this article will be effective with disengaged front-line leaders! Our findings show that organizations often underutilize or burn out this most precious asset through poor communication, lack of real engagement, unclear expectations, poor feedback, continuous firefighting, improper training, and much more.
In today’s global marketplace, you need every advantage possible to maintain and improve your organization and bottom line. By actively engaging your front-line leaders through proper training and creating a workplace culture that aligns with performance outcomes, your company will compete more effectively. When your frontline leaders are empowered with clear expectations and training on the tools to deliver on performance expectations, it can be a game-changer.
The POWERS Difference
A healthy and thriving company culture is the key to an empowered workforce willing to dig in and help reduce waste and inefficiency throughout your organization. At POWERS, our proven Culture Performance Management™ (CPM) methodology connects the dots between optimized company culture and desired operational performance outcomes. It can help break down silos, and open lines of effective communication, collaboration, and innovation. Most importantly, it can help lower costs.
Our team has helped executive leadership across many industries implement CPM to operationalize their culture for rapid and sustained performance improvement, increased competitive advantage, greater value, and a stronger bottom line.
To put our experienced team and proven track record to work for you, schedule an initial discovery and analysis by calling +1 678-971-4711, or emailing us at info@thepowerscompany.com.