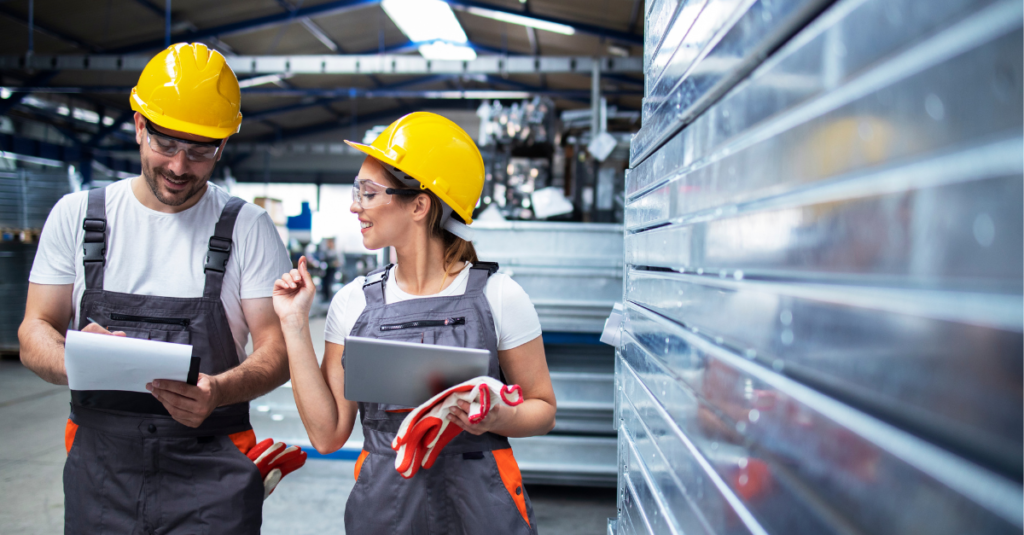
Continuous productivity improvement is the discipline of purposefully and continually uncovering and overcoming obstacles in systems, processes, and behaviors to achieve more output from an hour of work. How do you focus on the right changes to improve performance?
The old saying, “time is money,” has never been more accurate for manufacturers. So, the more production you can squeeze out in a specified time, the more revenue potential and the more profit your business can realize.
But if you’re struggling to improve production, or even if everything is operating optimally, there are several methods you can employ to continuously improve productivity without sacrificing quality, from removing production bottlenecks to reorganizing the way you work.
First, Let’s Look at What We Mean by Continuous Productivity Improvement
- Capital: Invest in facilities, software, infrastructure, machines, and more.
- Strategy and Business Model: Develop a business strategy and model more likely to yield better financial results.
- Tools and Techniques: Deploy enterprise planning and productivity software applications, workflow models, and other technical resources for employees’ successful and timely completion of tasks.
- Automation: Deploy systems and machines that automate work to boost productivity.
- Process Improvement: Uncover and reduce wasted efforts in repeated business processes.
- Time Management: Identify and reduce sources of wasted work time.
- Outsourcing: Recruit and pay individuals to do work outside your current talent.
- Performance Management: Set employee goals, monitor progress, and evaluate results.
- Organizational Culture: Develop norms, habits, expectations, standards for behaviors, and shared values as a group that are conducive to productivity.
Although we consult on all these methodologies, we zero in on those that can yield the most immediate and sustainable impact: Process Improvement, Time Management, Performance Management, and Organizational Culture. From our experience, these critical productivity areas translate across industries and transcend systems and processes.
How is Productivity Improvement Measured in Manufacturing?
Production Capacity
Production capacity is the maximum possible output of a manufacturing business, measured in units of output per period. For example, Beverage Company A can produce beverages at 20,000 cases per hour. Knowing your production capacity allows you to better plan and schedule production, give more accurate lead times, and forecast your cash flow.
There are several different ways to determine your production capacity: manual measurement, Rough-Cut Capacity Planning (RCCP), and Capacity Planning and Scheduling.
Increasing production capacity in the long term comes through better planning, improving business processes, and implementing manufacturing methodologies such as Lean, the Theory of Constraints, and Single Minute Exchange of Dies.
In the short term, you can increase production capacity by adding shifts, increasing overtime, or outsourcing some of your production.
An ERP (Enterprise Resource Planning) or an MRP (Material Requirements Planning) system for capacity management allows companies to plan production more accurately and efficiently and make better decisions by accessing better data analysis and insights.
From a productivity improvement perspective, increasing production capacity is often accomplished by additional investment in labor, equipment, and facilities, increasing the assets dedicated to production.
Capacity Utilization
The capacity utilization rate (reported as a percentage) is a critical manufacturing key performance indicator (KPI) related to production capacity. It reveals how much of a company’s production capacity is being used and how much is unused. In other words, how much of what you can make do you actually make? Therefore, the higher the percentage rate, the lower the cost per unit.
You can calculate the capacity utilization rate by dividing the actual output level by the production capacity and multiplying the result by 100.
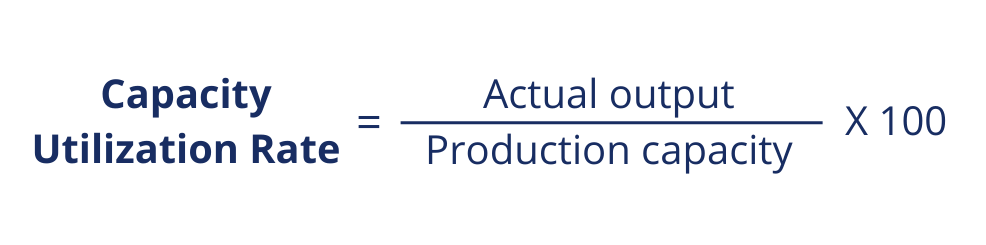
The capacity utilization rate is excellent for assessing your operational efficiency, costs, and pricing. Generally, an 85% rate is considered optimal. This is because the greater the capacity utilization rate, the lower the cost per unit, giving your organization the flexibility to increase your competitive advantage by satisfying more customer orders, lowering prices, increasing profit margin, and more.
Increasing capacity utilization up to an optimal rate is essential for productivity improvement and maximizing ROA (Return on Asset) and ROI (Return on Investment).
Throughput
Effective productivity refers to more than just capacity. It also relates to throughput. A manufacturing facility or individual production line doesn’t just contain work, it processes it, functioning more like a freeway.
Therefore, throughput is the amount of product rate-wise. For example, a production process may have a throughput of 50 tons per hour, depending on the line’s speed and volume.
Yield
Yield is the amount of ‘good product’ (the product that meets customer specifications and quality standards) that makes it to final manufacture from the raw material inputs. For example, 100 tons of raw steel, which translates into 50 tons of steel beams as it goes through the production process, has a yield of 50 percent.
Here are Six Ways to Begin Fostering a Continuous Productivity Improvement Culture in Your Manufacturing Business
1. Review Your Existing Production Workflow and Management Operating System (MOS)
- People and Behaviors – Do you have the right people, with the right skills, doing the right job in the right place? Do you have well-trained frontline leaders managing an engaged workforce? Is the critical pathway visible and on track? Are productivity objectives defined, realistic, safe, and clearly communicated? Do your frontline leaders embody your stated company values?
- Processes – Are your business and production processes defined, documented, and visible? Have you mapped out your processes and Management Operating System to identify any bottlenecks or other obstacles? Is the critical pathway visible and on track? Have you mapped your value stream to assess and plan process improvement projects?
- Equipment and Technology Systems – Is all your equipment well-maintained and in good repair? Is the technology you rely on outdated? How readily can you make production changes based on dynamic market conditions? How much of your existing technology system features do you actually use?
Before making any changes, take the time to understand how everything in your production process works fully. Production obstacles and bottlenecks will become more readily apparent. You may also uncover aspects of your production process that do not need attention. Unless there’s a pressing financial or safety reason for implementing a significant equipment or technology change, think about the value of the expected outcome and the ROI.
2. Update Processes and Technology
- Automation can be a powerful tool for increasing efficiency, reducing error, waste, and rework.
- Software solutions can assist with scheduling, inventory, and monitoring workflow.
- Equipment advancements can increase production speed and improve product quality.
When identifying new technology and equipment investments, account for the total cost of ownership and its impact on the bottom line. For example, a high initial expense may be worth it if the total cost of ownership is lower than the technology or process you are replacing and if it solves a problem, such as clearing a production bottleneck or reducing scrap or rework.
3. Commit to Maintenance Performance Improvement
- Be sure all operators are trained in the regular maintenance and troubleshooting procedures of the equipment they operate.
- Plan and perform preventive maintenance at regular intervals.
- Identify the best time for maintenance using information from your frontline leaders, workflow processes, or, ideally, a CMMS system.
- Prioritize maintenance tasks, don’t back-burner them.
Preventive maintenance (or the more effective commitment to Total Productive Maintenance) ensures that your equipment runs smoothly without unexpected downtime or work stoppages.
4. Empower Your Workforce, Especially Your Frontline Leaders
Employee education, training, and development are ongoing investments and processes. Depending on the industry, some types of training may be mandatory, such as daily safety training for all employees using PPE (Personal Protection Equipment). In addition, new equipment and technology require training to get the most value. Employee education is also an excellent retention tactic; new employees take time to become proficient, causing a slowdown in production.
- Schedule training sessions for all operators when new equipment is installed.
- Keep accurate records of training and schedule refreshers if needed.
- Offer educational opportunities for employees who wish to advance or obtain new skills.
Expand training and education beyond the requisite task, job function, safety, and equipment. Your manufacturing operation will run more smoothly if everyone is engaged in the business and inspired and motivated to perform as productively as possible.
Why Employee Productivity Matters
Naturally, a highly efficient and productive workforce generates more profit. However, there are other reasons businesses should pay attention to employee productivity. For example:
Employee Productivity and ROI
Measuring employee productivity and engagement can help a business understand its return on investment. For example, a company significantly invests in upgrading its machinery and installing new software to optimize efficiency. If this investment were worth it, the business would see an increase in employee productivity.
Lower Employee Productivity and Engagement Can Point to More Significant Underlying Issues
Take the time to uncover what low employee productivity is telling you about your business. Low productivity suggests employee disengagement, workflow interruptions, process inefficiencies, poor management, and much more.
You may discover that one manager may be sowing discontent and needs better training in managing people and better exemplify your company’s values. A problem like this can spread rapidly and significantly impact employee well-being and lead to high turnover.
Therefore, consider employee productivity and engagement as a diagnostic test within your business. Increasing engagement can directly impact productivity and, ultimately, profit!
5. Organize the Workspace
- Reducing movement and work area clutter and congestion saves time.
- Reduce movement for optimal task efficiency.
- Create the optimal layout and flow of tools and materials for the job or process.
- Remove unnecessary or unused tools and materials from the workspace.
- Create organized storage to reduce the time needed to find materials, documents, and equipment.
- Organize the manufacturing floor to maximize efficiency.
Reduce excessive movement, travel time, and distance wherever possible. For example, when moving a product from one line to another, can you shorten the distance, orient the product, or move the product more quickly and safely to the next production step?
Excessive movement indicates poor organization and can cost you significant production time.
6. Maintain Optimal Inventory
If you have excess inventory, you need a place to warehouse it and hope you will use it all. If you have too little inventory, you risk a work stoppage as you wait for more to arrive on-site. Optimizing inventory is especially important if you follow lean manufacturing principles such as the Kanban technique.
- Use inventory management software to track inventory levels, create automatic notifications to alert you of any shortages, and ultimately make better decisions. Giving vendors direct access to your inventory counts can also be beneficial to fulfilling needed supplies automatically.
- Create favored vendor relationships to increase quality and delivery timeliness accountability.
- Make predictions about the impact of particular parts shortages and put processes in place to mitigate production delays.
Monitor rejection rates, declining quality, and late deliveries so you can rectify them with the vendor or find a new one. If one of your vendors is undergoing significant management or ownership changes, secure assurances and guarantees that your deliveries will continue uninterrupted.
Conclusion
Increased productivity and continuous improvement should be driven by strategic change rather than by implementing “band-aids” or “quick fixes” that may help in the short-term “firefighting” but cause long-term issues. Also, throttling productivity on the backs of employees can result in burnout, high turnover, and create safety issues.
Thoroughly reviewing current workflow processes, your MOS, and assets can uncover hidden bottlenecks that may be easily remedied by a change in the process or new technology. Maintaining equipment in good repair reduces unexpected work stoppages and downtime. Investing in educating and engaging your people and good organization will provide a safe and productive work environment. Empowering your frontline leaders through proper training and development can tap into a vast resource for solving problems encountered on the shop floor every day.
Finally, increased productivity results in increased revenue and the opportunity to expand the business, take on more work, hire more people, increase wages, or purchase new assets and equipment. Make it a policy to review your processes regularly. New manufacturing equipment, materials, and techniques arrive all the time. By fostering a culture of continuous productivity improvement, your organization will be better prepared to adopt the improvements that provide the most value for your company.
The POWERS Difference
At POWERS, we focus on Frontline Leadership Training and Development to connect the dots between the right leadership behaviors and desired operational performance outcomes.
Our team has helped executive leadership across many industries operationalize their culture for rapid and sustained performance improvement, increased competitive advantage, greater value, and a stronger bottom line.
To put our experienced team and proven track record to work for you, schedule an initial discovery and analysis by calling +1 678-971-4711, or emailing us at info@thepowerscompany.com.