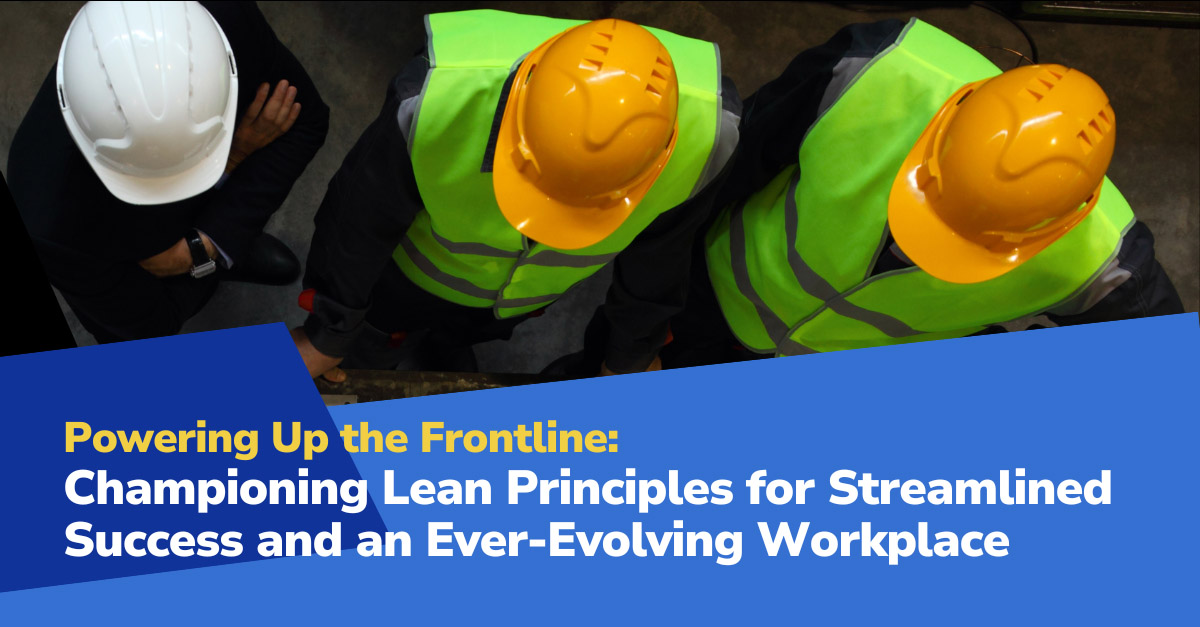
Lean thinking has stood the test of time, but too often, manufacturers treat it as a one-time training exercise instead of a system of ongoing improvement. At POWERS, we don’t teach Lean from a whiteboard, we bring it to life on the factory floor.
We translate Lean principles into practical actions that drive performance, reduce unnecessary costs, and give supervisors and frontline teams the tools to operate at their best. From stabilizing workflows to eliminating routine friction points, we help teams build a daily rhythm that aligns effort with measurable outcomes.
This isn’t about following a framework for the sake of compliance. It’s about putting systems in place that create consistency, control variability, and free up capacity, without adding more labor or complexity.
1Streamlined Workflow:
Production stalls when work doesn’t flow. We work with teams to analyze how materials, tasks, and decisions actually move, not how they’re supposed to move on paper. Then we remove the friction points: cross-shift inconsistencies, communication breakdowns, delays in staging, or unclear responsibilities. The result is a cleaner, faster flow from raw material to finished product, one that keeps throughput high and lead times low.
2Waste Reduction:
Waste takes many forms: scrap, excess motion, overprocessing, idle time, underused talent, and more. We help identify where time, energy, and materials are being spent without adding value, and then implement practical routines to eliminate those losses. That could mean simplifying changeovers, refining machine setups, or improving shift-to-shift coordination. Less waste equals more capacity.
3Improved Quality:
The true cost of poor quality isn’t just rework, it’s missed deadlines, unhappy customers, and lower margins. POWERS helps teams build in quality at the source by embedding standard checks into the process, training operators to recognize issues early, and creating clear escalation paths. We also focus on reducing variation, because repeatable outcomes are the backbone of consistent performance.
4Enhanced Employee Engagement:
Lean fails when it becomes a management-only initiative. We build frontline engagement by giving operators and leads ownership of the process, through visual controls, routine team huddles, and simple tools that provide real-time clarity. When people understand their impact on performance and feel equipped to improve it, they take more initiative and execute with more consistency.
5Just-In-Time Production:
JIT is more than minimizing inventory, it’s about aligning materials, labor, and production timing with actual demand. We help manufacturers move from reactive to responsive by tightening communication between planning and operations, improving demand visibility, and reducing the gap between what’s scheduled and what’s possible. Fewer surprises. Fewer stockouts. Less waste.
6Standardized Work:
Inconsistent work leads to unpredictable outcomes. We partner with teams to document, train, and reinforce best practices, turning tribal knowledge into shared knowledge. This creates stability, simplifies onboarding, and lays the foundation for continuous improvement. Standardized work doesn’t make things rigid, it frees teams to focus on solving problems, not re-learning routines.
7Greater Flexibility:
Market conditions shift. Customer needs evolve. Equipment goes down. The most resilient operations are the ones that can pivot without losing productivity. POWERS helps build flexibility into both processes and people, cross-training teams, simplifying setups, and reducing lead time variability. When the unexpected happens (and it always does), flexibility is your competitive edge.
8Continuous Feedback Loops:
Lean thrives on data, but only when it’s timely and actionable. We help install simple feedback mechanisms at every level: hourly performance boards, daily management walks, and escalation routines that close the loop between problem detection and resolution. These systems don’t just track performance, they shape it.
9Improved Resource Utilization:
Labor, machines, and materials often sit idle, not because of lack of demand, but because of poor planning or misaligned processes. We dig into how resources are being used across shifts, how demand signals are interpreted, and where gaps in utilization can be closed. The goal isn’t just efficiency, it’s getting the most out of what you already have.
10Sustainable Cost Savings:
Anyone can cut costs once. The challenge is keeping them down while maintaining output. POWERS focuses on the systems and behaviors that drive consistent execution, so the savings you see in month one don’t vanish by quarter two. Our clients don’t just see reduced labor hours or fewer defects, they see year-over-year improvement that sticks.
The POWERS Difference
POWERS is a results-driven manufacturing productivity consulting firm uniquely positioned at the intersection of operational performance and frontline execution. We don’t just teach Lean—we embed it into the daily rhythms of your plant floor.
We partner with forward-focused manufacturers to unlock capacity, reduce unnecessary costs, and strengthen leadership behaviors that drive productivity at scale. Our proven approach helps teams move beyond one-time initiatives and create systems that produce real, sustainable outcomes.
A key area where we consistently generate impact is in developing frontline leadership and equipping supervisors with the tools they need to manage resources, lead people, and execute Lean principles with discipline.
By combining deep industry experience with practical routines and measurable KPIs, we help align people, processes, and priorities—translating Lean from a philosophy into a tangible performance system.
To support this, we’ve developed DPS, our next-generation manufacturing operating system that puts Lean data and decision-making directly in the hands of supervisors. With DPS, plant leaders can track performance in real time, eliminate bottlenecks, and sustain continuous improvement—without adding complexity or cost.
POWERS has helped executive leadership across multiple industries activate their frontline workforce, accelerate throughput, and build a stronger bottom line—one shift at a time.
Continue Reading from the Mastery Series
- Part 1 - Strategic Alignment that Bridges Daily Tasks with Broader Visions for Unified Organizational Success
- Part 2 - Crafting Clarity through Effective Communication and Active Listening
- Part 3 - Sharpening Decision-Making Prowess for Seamless Operations and Minimal Downtimes
- Part 4 - Championing Lean Principles for Streamlined Success and an Ever-Evolving Workplace
- Part 5 - Mastering Performance Management for Optimal Team Output and Growth
- Part 6 - How Leaders Well-Trained in the Soft Skills Transform Manufacturing Teams
- Part 7 - Strengthening Conflict Resolution Skills for Peak Productivity and Profitability Gains
- Part 8 - Unleashing Potential with Precision Time and Resource Management
- Part 9 - Safety First for Sustainable And Scalable Productivity And Profitability
- Part 10 - Equipping Your Shop Floor Leaders to Be Effective Change Managers