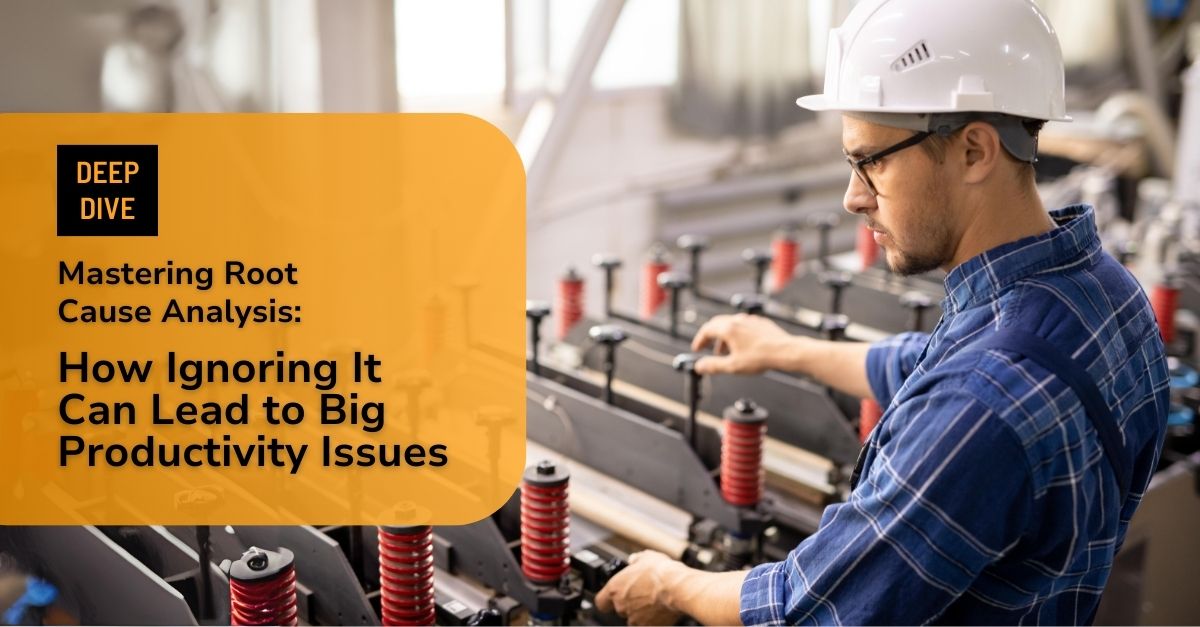
Problems are an inevitable part of the manufacturing process. Equipment malfunctions, quality defects, yield dropoffs, and production bottlenecks are just a few examples of the challenges that can arise.
However, the way you address these issues can significantly impact your overall performance. This is where Root Cause Analysis (RCA) steps in as a powerful tool to uncover the underlying reasons behind these problems and lead you to implement effective solutions.
What is Root Cause Analysis (RCA)?
RCA is a structured problem-solving methodology that goes beyond addressing surface-level symptoms. It delves deeper into the core issues that contribute to recurring problems. Identifying and rectifying the root causes can prevent future occurrences, improve operational efficiency, and enhance overall performance.
Methods for Performing Root Cause Analysis
There are several well-established methods for conducting RCA, each with its strengths and areas of application:
15 Whys:
2Fishbone Diagram (Ishikawa Diagram):
3Fault Tree Analysis (FTA):
4Failure Mode and Effects Analysis (FMEA):
5Pareto Analysis:
The Cost of Ineffective Root Cause Analysis
While RCA is a valuable tool, its effectiveness hinges on proper execution. When poorly performed, it can lead to a cascade of negative consequences:
1Poor Decision-Making:
Without the data and insights provided by an effective Root Cause Analysis (RCA) system, decision-making can be less informed, leading to suboptimal strategies and actions. Accurate data is crucial for effective RCA, which in turn informs better decision-making, particularly in a rapidly changing market environment. Ineffective RCA means critical underlying issues may remain unidentified, resulting in decisions based on incomplete or inaccurate information.
2Increased Customer Churn and Negative Brand Perception:
Repeated quality issues and product failures erode customer trust and loyalty, resulting in higher churn rates and a damaged brand reputation. Monitor customer satisfaction scores, social media sentiment, and market share changes to measure the extent of this damage.
3Missed Production Targets and Revenue Loss:
If equipment downtime or process inefficiencies are not addressed at their root, production targets will consistently be missed, leading to lost revenue opportunities. Keep a close eye on production output, on-time delivery rates, and revenue forecasts to identify the financial impact.
4Regulatory Non-Compliance and Legal Repercussions:
In industries with stringent regulations, failing to address the root cause of non-compliance issues can result in hefty fines, legal actions, or even production halts. Track compliance audit results and legal expenses to assess the risks.
5Increased Employee Turnover and Difficulty in Hiring:
A workplace plagued by recurring problems and a lack of effective problem-solving can lead to high employee turnover. Additionally, attracting top talent becomes challenging when your company gains a reputation for operational instability. Monitor employee turnover rates, time-to-fill positions, and candidate feedback to gauge the impact on your workforce.
6Stagnant Innovation and Missed Market Opportunities:
When your focus is constantly on firefighting recurring problems, it leaves little room for innovation and exploring new market opportunities. Track new product development cycles, research and development investments, and competitor analysis to see if you’re falling behind.
7Escalating Insurance Premiums and Liability Risks:
If safety incidents are not properly addressed through RCA, your company’s insurance premiums are likely to increase due to the perceived higher risk profile. Additionally, you may face greater liability risks in the event of accidents or injuries. Monitor insurance premium trends and legal consultations related to safety incidents.
8Erosion of Shareholder Confidence and Investor Concerns:
Persistent operational issues and their financial impact can erode shareholder confidence, leading to a decline in stock value and difficulties in attracting new investments. Track stock price fluctuations, investor relations activities, and analyst reports to assess investor sentiment.
9Environmental Damage and Sustainability Concerns:
In some cases, the root cause of a problem may be linked to environmental factors. Failure to address these issues can result in pollution, resource depletion, and damage to the company’s sustainability image. Monitor environmental impact assessments, waste management data, and sustainability ratings to measure the ecological footprint.
10Decreased Employee Engagement and Collaboration:
When employees feel their concerns about recurring problems are not taken seriously, it can lead to decreased engagement and a breakdown in collaboration. This can hinder problem-solving efforts and create a toxic work environment. Track employee engagement surveys, team performance metrics, and feedback from cross-functional teams to identify signs of disengagement.
By understanding these deeper consequences and tracking the relevant metrics, you can develop a stronger appreciation for the critical role of effective root cause analysis in the long-term success and sustainability of your manufacturing operations.
Make Root Cause Analysis an Integral Part of Your Process
Given the potential consequences of inadequate RCA, investing in proper training and resources is paramount. By mastering the art of root cause analysis, you can unlock a multitude of benefits, including:
- Reduced Downtime: Identify and eliminate the root causes of equipment failures and production delays.
- Improved Quality: Consistently deliver high-quality products that meet or exceed customer expectations.
- Increased Efficiency: Streamline processes, minimize waste, and optimize resource utilization.
- Enhanced Employee Morale: Empower your workforce to actively participate in problem-solving and continuous improvement.
- Sustainable Growth: Build a culture of continuous improvement that drives long-term success.
Don’t just fix problems—prevent them with the comprehensive capabilities of the POWERS Manufacturing Enterprise Productivity App. Invest in this powerful tool and watch your manufacturing performance soar.
- Speak to an Expert: Call +1 678-971-4711 to discuss your specific challenges and goals.
- Email Us: Get tailored insights by emailing info@thepowerscompany.com
- Request an Assessment: Use our online contact form, and one of our expert manufacturing consultants will reach out to schedule an in-depth analysis of your operations.