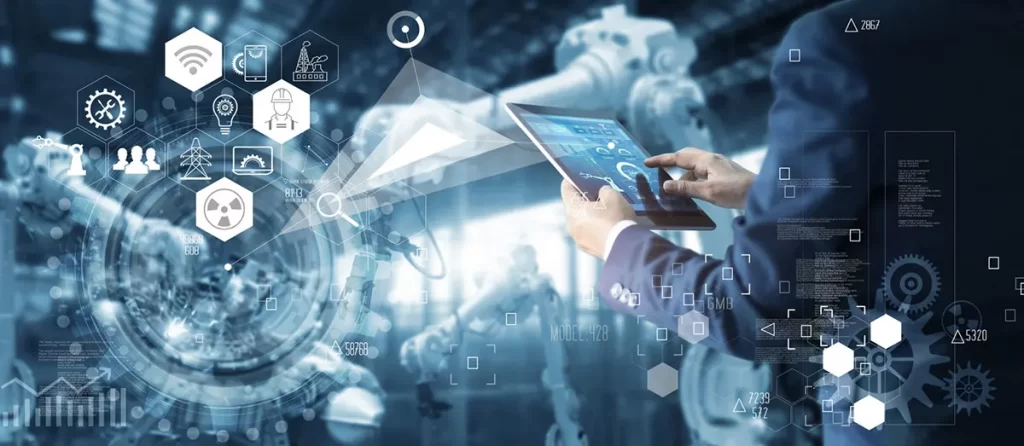
Over the past few months, we have explored how the COVID-19 pandemic has affected the manufacturing industry as well as how a reopened economy could impact manufacturing. While the world hasn’t gone back to what things were like pre-pandemic, we’ve entered into a new phase one might call “adjusting for the long, unfolding road ahead.”
There are many examples of manufacturers adapting during the crisis to produce in-demand safety items outside their usual scope, like how Honda and GM joined together to manufacture hand sanitizer, and employees skilled in additive manufacturing ramped up their production of face masks. Even in the midst of the greatest economic disruption since The Great Depression, manufacturers are stepping up and helping out where they can.
The pandemic has affected manufacturers across all industries. According to a recent survey from the National Association of Manufacturers, 78 percent of leaders in manufacturing expected a major financial impact to their businesses. We have yet to see the full significance of that impact, but this disruption has left many manufacturers wondering how they can plan for what happens next. Here’s how manufacturers can continue to meet this chaotic and uncertain time.
Perform a business model analysis
There’s nothing like a public health emergency to illuminate aspects of your business that aren’t working as smoothly as they should be. Many organizations had issues before the pandemic, but COVID-19 really put operational shortcomings in the spotlight.
Before you can find solutions that will help your organization to be more productive and efficient, you need to have a comprehensive understanding of the day-to-day operations of your business. Perform a complete analysis of your business including an audit of all your vendors and suppliers, your e-commerce capabilities, and your management of the supply chain.
Be prepared for disruption to the supply chain
Global supply chains have been significantly affected by the COVID-19 pandemic, and it may take years for them to completely normalize. Manufacturers need to be aware of this so that they can make necessary adjustments and preparations to manage inventory. Because your supply chain may be affected in ways beyond your control, now is a great time to cut expenses and eliminate any inefficiencies in your operations.
Value the health and safety of your employees
Follow the safety guidelines given by the Centers for Disease Control and Prevention. Make sure you don’t have too many employees working one shift so that your staff can avoid coming into contact with a lot of other employees. If an employee does become ill, follow the proper procedures to clean the facility and ensure the safety of all of your employees.
You may have to make some adjustments to the layout of your space to accommodate the proper health protocols. You may want to set up handwashing or hand sanitizer stations. Consider installing touch-free technology for clocking in and out.
Most importantly, by taking these measures, you’ll be showing your employees that you value their health, which contributes to morale, engagement, and therefore productivity and success.
One positive thing that has come out of this pandemic is that it has forced many organizations to take a look at the way they are running their business. Many companies have had to make adjustments for the pandemic, but some of them may lead to more productivity in the long-term.
It can be helpful to have an objective team evaluate your organization to ensure that your business is running as smoothly as possible. At POWERS, we can perform a full analysis of your organization, and work alongside your front-line leaders to implement the necessary solutions. We have a wealth of experience and a long track record of saving organizations millions of dollars; take a look at our case studies.
If you are interested in learning more about us, please get in touch. We would love to hear from you.