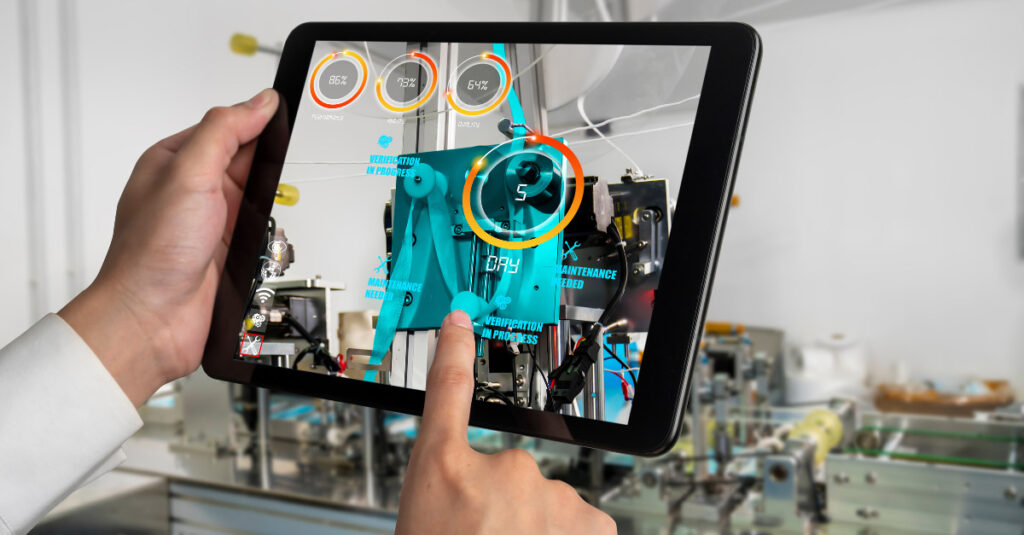
Profitability is the heart of any business's survival and growth. In manufacturing, where competition is fierce, and margins are often thin, the importance of profitability takes on even greater significance. Central to this is the role of productivity and cost reduction.
Increasing productivity and reducing costs are proven strategies for enhancing profitability in large-scale manufacturing operations. Let’s look at how these two factors can jointly optimize profitability and reveal five effective strategies for achieving this goal.
A Deeper Look into Profitability in Manufacturing
Profitability, as the term suggests, is the ability of a company to earn profits from its business operations. It’s the critical measure of a company’s success and is directly linked to both productivity and cost control.
In manufacturing, increasing productivity can result in higher output for the same input, reducing per-unit costs and maximizing capacity utilization. Meanwhile, cost reduction, achieved through improved processes and waste elimination, directly and immediately impacts a company’s bottom line.
Productivity improvements and cost reduction form a virtuous cycle. Improved productivity can lead to cost reductions, and these savings can be reinvested to boost productivity further, thereby creating a continuous cycle of profitability
The Strategic Roadmap: Five Approaches to Boost Productivity and Lower Costs
1Lean Manufacturing
Lean manufacturing, a concept originating from the Toyota Production System, is a systematic method designed to minimize waste within a manufacturing system without sacrificing productivity. Manufacturers can significantly improve their productivity by identifying and eliminating non-value-adding activities and simultaneously reducing costs.
Components such as Just-In-Time production can significantly reduce inventory costs, while automation can minimize labor expenses. Continuous improvement initiatives under the Lean framework constantly refine efficiency, leading to a more profitable operation.
2Total Productive Maintenance (TPM)
Unlike traditional reactive approaches to equipment maintenance, TPM is a proactive strategy that involves everyone in an organization, from operators to senior management. TPM aims to maintain and improve the integrity of production and quality systems through equipment upkeep.
By reducing downtime, TPM increases equipment availability and productivity while significantly lowering maintenance costs leading to improved OEE (Overall Equipment Effectiveness).
3Advanced Automation and Robotics
In the era of Industry 4.0, automation and robotics have become integral parts of advanced manufacturing operations. Robotics can perform tasks faster and more accurately than humans, and unlike humans, they can work non-stop, leading to much higher output levels.
Additionally, robots can take over tasks that are too hazardous or monotonous for humans, enhancing workplace safety and employee morale. While the upfront investment can be high, the long-term benefits of reduced labor costs and increased productivity can significantly improve profitability.
4Operational Excellence and Continuous Improvement
Operational excellence is an element of organizational leadership that stresses applying principles, systems, and tools toward the sustainable improvement of key performance metrics.
Techniques like Six Sigma and Kaizen can be utilized to reduce waste and variation in processes. When an organization cultivates a culture of continuous improvement, it can achieve consistent productivity gains and cost reductions over time.
5Strategic Sourcing and Supply Chain Optimization
Strategic sourcing is a systematic process that restructures procurement processes to effectively manage an organization’s materials, supplies, services, and vendor relationships. Similarly, supply chain optimization ensures that the supply chain operates as efficiently as possible.
These two strategies can help reduce transportation, inventory, and storage costs, significantly lowering the overall cost of goods sold.
Moreover, optimizing your supply chain with a comprehensive S&OP plan mitigates the financial risks of holding too much or too little inventory, increased delivery costs, time to market, or unmet market demand. These few examples represent tremendous potential for lost profitability.
6Invest in Developing Your People
People are the cornerstone of any successful manufacturing operation. Employees at all levels contribute to the productivity and cost-effectiveness of a business. Investing in employee development – through training, upskilling, and educational opportunities – can significantly improve productivity and reduce costs in the long term.
Workplace leadership development programs can equip employees with the latest skills and knowledge to operate new machinery, adopt advanced manufacturing techniques, and implement effective quality control processes. By upskilling your workforce, you can ensure that your manufacturing operations remain cutting-edge, increasing productivity and efficiency.
Moreover, employee development can also lead to increased job satisfaction and reduced turnover rates. When employees feel valued and see opportunities for advancement, they’re likely to stay with the company longer, reducing costs associated with high employee turnover, such as recruitment, onboarding, and lost productivity.
Furthermore, investing in your people can stimulate innovation within your organization. A well-trained, satisfied workforce is likelier to develop new ideas to improve processes, identify cost-saving opportunities, and drive productivity improvements.
While the immediate monetary benefits of employee development might not be as obvious as other cost-cutting measures, the long-term payoff regarding increased productivity, reduced costs, and an engaged, loyal workforce can be substantial.
Investing in employee leadership development can lead to improved productivity, reduced turnover, and greater innovation, significantly enhancing a manufacturing company’s profitability in the long term.
Conclusions for Business Leaders
A holistic productivity and cost reduction approach can lead to significant profitability improvements. The strategies mentioned above are interconnected, each one amplifying the effectiveness of the others.
Companies must continually seek ways to improve productivity and reduce costs to maintain their competitive edge in today’s dynamic manufacturing environment. Implementing strategies such as Lean manufacturing, Total Productive Maintenance (TPM), advanced automation and robotics, operational excellence, strategic sourcing, and investing in developing your people can significantly improve both areas, propelling profitability.
Profitability in manufacturing is not a one-time achievement but a continuous journey. It involves the persistent pursuit of process optimization, cost reduction, and enhanced productivity. By integrating these strategies into their operations, large-scale manufacturers can remain on the path to sustained profitability, even in the face of an ever-challenging and competitive market environment.
The POWERS Difference
We are a dedicated and results-driven management consulting firm uniquely positioned at the intersection of workplace culture and operational performance. We partner with growth-oriented organizations to cultivate a culture of excellence that fuels productivity, drives efficiency, strengthens competitive advantage, and fuels profitability.
Leveraging our deep industry expertise and innovative methodologies, we build synergies between people and processes, creating holistic, sustainable change that translates into measurable business outcomes.
Our team has helped executive leadership across many industries operationalize their culture for rapid and sustained performance improvement, increased competitive advantage, greater value, and a stronger bottom line.
To put our experienced team and proven track record to work for you, schedule an initial discovery and analysis by calling +1 678-971-4711 or emailing us at info@thepowerscompany.com.