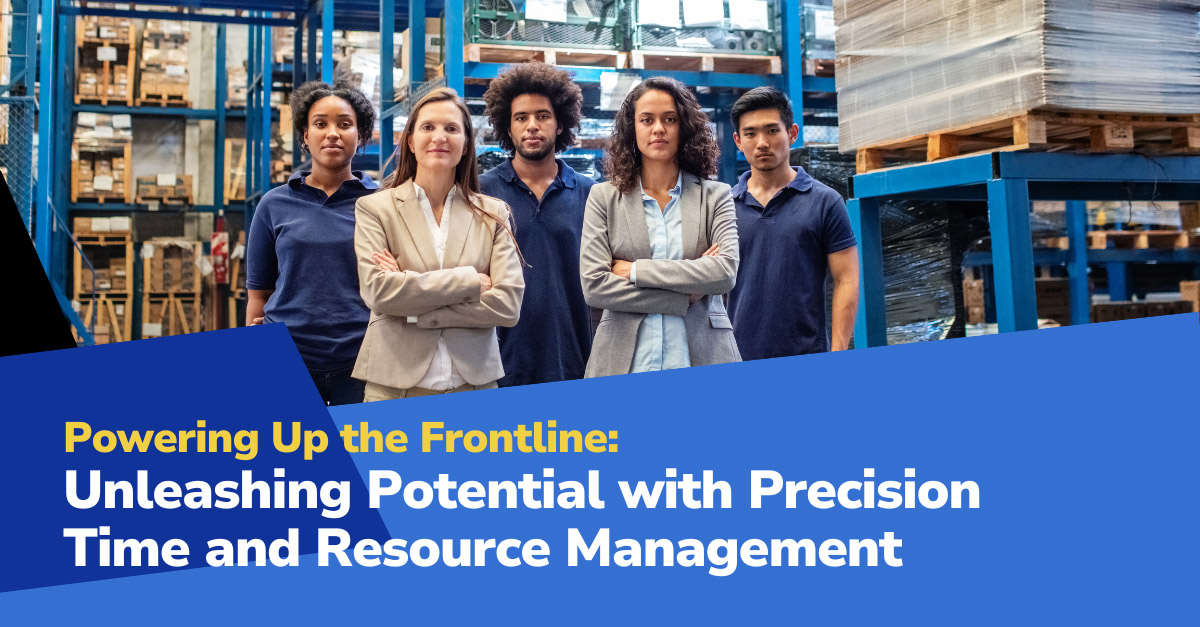
In large-scale manufacturing, small inefficiencies often go unnoticed—but they add up fast. A few minutes lost per shift, a machine sitting idle between jobs, or a delay in materials hitting the line can mean thousands in lost output every week.
And while many organizations focus on big-ticket improvements like automation or capital investment, the biggest gains often come from better managing what’s already in play: time, labor, materials, and machine availability.
That’s where frontline leadership makes the difference. When supervisors have the right visibility, tools, and decision-making authority, they can orchestrate operations in real time—balancing the flow of resources with production targets and shifting priorities. It’s not just about keeping things moving. It’s about enabling the floor to run smarter, smoother, and more profitably.
Here are the top 10 measurable ways manufacturers gain by optimizing time and resource management at the plant level:
1Increased Throughput:
When materials arrive on time, machines are staged properly, and handoffs happen without delay, more units come off the line with fewer interruptions. By addressing small inefficiencies in sequence and timing, manufacturers can dramatically increase output without changing staffing or footprint. These improvements often come from frontline adjustments—like staggering prep times or better aligning labor with demand surges.
2Cost Savings:
Underused equipment, excess scrap, and poorly timed labor shifts all drain resources. Tightening how and when resources are deployed allows leaders to cut costs without cutting corners. Frontline supervisors who are trained to spot overconsumption and underutilization can reduce waste at its source, lowering material, labor, and energy expenses in ways that are immediately felt in the budget.
3Shorter Lead Times:
When teams optimize task scheduling and eliminate hidden delays—whether in material handling, approvals, or equipment changeovers—orders move faster through production. That leads to quicker delivery timelines and fewer bottlenecks down the line. Customers notice the difference, and internal teams benefit from more predictable planning windows.
4Enhanced Machine Utilization:
Equipment is one of the most capital-intensive assets in manufacturing. But far too often, machines are underloaded, waiting on labor or materials, or used inefficiently due to scheduling gaps. With better resource coordination, supervisors can reduce idle time, increase machine load rates, and extend equipment life—all while maintaining output quality.
5Reduced Overtime Costs:
Unplanned overtime is a symptom of poor scheduling or misaligned resource allocation. When time and labor are managed proactively, teams can hit production goals without exceeding scheduled hours. This not only cuts payroll costs, it also helps avoid fatigue-driven quality issues and boosts long-term labor sustainability.
6Optimized Inventory Levels:
Holding too much inventory ties up working capital and clogs valuable space. Holding too little risks costly downtime. By aligning production pacing with real demand and improving upstream coordination, manufacturers can strike the right balance—reducing overstock, preventing stockouts, and improving overall supply chain reliability.
7Improved Quality Control:
When production is rushed or processes are out of sync, mistakes follow. Giving teams the time and tools to perform quality checks properly—and ensuring they’re not constantly playing catch-up—means fewer defects, fewer returns, and fewer warranty claims. This also improves customer trust and reduces the cost of rework or scrap.
8Enhanced Scalability:
Operations that manage time and resources effectively are better equipped to ramp up or scale down as demand shifts. Whether facing seasonal surges, market volatility, or new product launches, organizations with flexible workflows can adapt quickly—without needing to restructure or retrain. That kind of responsiveness gives manufacturers a competitive edge.
9Increased Profit Margins:
Cost reductions, improved efficiency, and increased output all contribute directly to healthier margins. But there’s more: when resource flow is optimized, revenue opportunities—like faster order fulfillment or higher line capacity—can be captured without extra spend. The cumulative impact shows up in the P&L quarter after quarter.
10Higher Employee Morale and Productivity:
A well-run floor isn’t just efficient—it’s less stressful. Workers who have access to the right materials, clear schedules, and functioning equipment can focus on doing quality work, not fighting fires. That creates a better environment, encourages retention, and boosts overall performance across shifts.
What It Means for Senior Leaders
Optimizing time and resource management isn’t just an operational tweak—it’s a strategic move. It requires investing in your frontline, equipping supervisors to make better real-time decisions, and breaking down the barriers that slow them down. It also requires aligning those everyday actions with larger performance goals.
Senior leaders who make this shift don’t just cut costs—they create organizations that run leaner, faster, and more predictably. That advantage compounds over time.
The POWERS Difference
POWERS is a results-driven manufacturing productivity firm that specializes in helping companies unlock these kinds of gains—not by adding complexity, but by sharpening the systems and behaviors already in place.
We work shoulder-to-shoulder with frontline leaders to identify delays, uncover misuse of time or materials, and streamline workflows using proven methods. Then we help organizations sustain those improvements through smart accountability systems and real-time operational insights from our proprietary DPS platform.
With deep industry experience and a track record of delivering measurable ROI, our team helps manufacturing leaders:
- Turn resource flow into a competitive advantage
- Build frontline capability for lasting change
- Drive higher output and stronger margins with existing assets
Our team has helped executive leadership across many industries engage and develop their frontline supervisors and managers for rapid and sustained performance improvement, increased competitive advantage, greater value, and a stronger bottom line.
To put our experienced team and proven track record to work for you, schedule an initial discovery and analysis by calling +1 678-971-4711 or emailing us at info@thepowerscompany.com.
Continue Reading from this Mastery Series
- Part 1 - Strategic Alignment that Bridges Daily Tasks with Broader Visions for Unified Organizational Success
- Part 2 - Crafting Clarity through Effective Communication and Active Listening
- Part 3 - Sharpening Decision-Making Prowess for Seamless Operations and Minimal Downtimes
- Part 4 - Championing Lean Principles for Streamlined Success and an Ever-Evolving Workplace
- Part 5 - Mastering Performance Management for Optimal Team Output and Growth
- Part 6 - How Leaders Well-Trained in the Soft Skills Transform Manufacturing Teams
- Part 7 - Strengthening Conflict Resolution Skills for Peak Productivity and Profitability Gains
- Part 8 - Unleashing Potential with Precision Time and Resource Management
- Part 9 - Safety First for Sustainable And Scalable Productivity And Profitability
- Part 10 - Equipping Your Shop Floor Leaders to Be Effective Change Managers