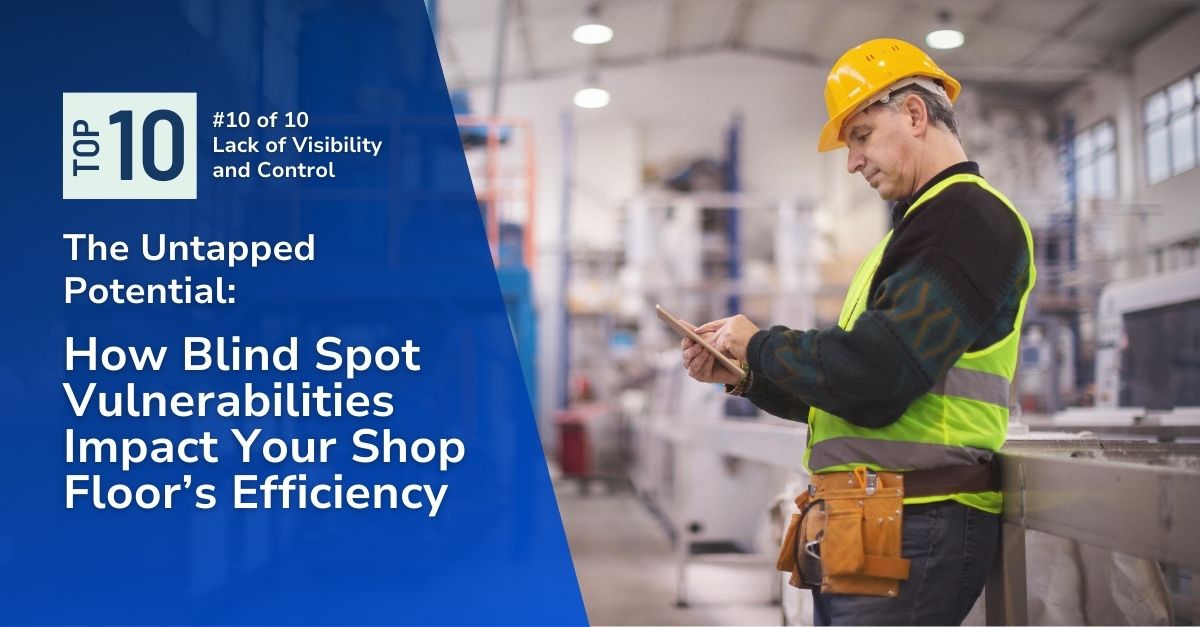
In the relentless pursuit of manufacturing efficiency, we often focus on the obvious culprits: broken machines, material shortages, and absenteeism.
But what about the unseen forces that chip away at our factories’ true potential?
Lack of visibility and control is the silent saboteur, a root cause that manifests as a thousand frustrating problems.
The surface symptoms are missing deadlines, spiraling costs, and slipping quality standards. The deeper truth is that without proper visibility, manufacturers are running blind, and their capacity is chronically underutilized. It’s like having a powerful engine constantly running below its optimal RPM.
In this final installment of our series, we’ll expose the granular, shop-floor realities stemming from this lack of insight. We’ll uncover how seemingly minor issues cumulatively create significant drag, preventing you from extracting the full potential from your existing assets and workforce.
1Inaccurate Cycle Time Estimates:
Negative Impact: Without real-time data, estimating how long a job will truly take is a guessing game. This leads to missed deadlines, overpromising to customers, and constant firefighting as schedules are thrown into chaos.
Positive Step: Implement shop floor data collection systems that track actual cycle times. This allows for accurate projections, realistic scheduling, and better customer service, as you can confidently communicate timelines.
2Invisible Quality Deviations:
Negative Impact: Quality issues slip through the cracks without real-time monitoring. This leads to defects reaching customers, costly rework, and potential damage to your brand’s reputation.
Positive Step: Use sensors and automated quality checks integrated into the production process. Real-time alerts about deviations allow you to correct issues before they become major problems.
3Root Cause Evasion:
Negative Impact: When problems occur, it’s guesswork trying to pinpoint the true cause. Symptoms get treated, but the underlying issue remains, leading to recurring breakdowns and frustration.
Positive Step: Detailed process tracking allows you to trace problems back to their source (e.g., machine malfunctions, operator error, material defects). Armed with this knowledge, you can implement permanent fixes, not band-aid solutions.
4Hidden Training Needs:
Negative Impact: Operators might struggle, but without visibility into their work patterns, those struggles go unnoticed. This leads to lower productivity, more errors, and the risk of them developing bad habits that impact output and quality.
Positive Step: Track individual operator performance against benchmarks. This reveals skill gaps and pinpoints where targeted coaching is most needed.
5Workload Imbalance:
Negative Impact: Uneven distribution of work causes bottlenecks on one end and idle time on the other. This erodes efficiency and drags down overall capacity.
Positive Step: Use real-time visibility tools to monitor job progress and workload across the shop floor. This allows you to rebalance work dynamically, maximizing the use of resources and time.
6Inability to Scale Production:
Negative Impact: Scaling up is a shot in the dark without understanding your true capacity and bottlenecks. This leads to missed opportunities, new orders stressing an already strained system, and an inability to meet demand.
Positive Step: Identify actual throughput limits and where they occur. Then, focus on targeted improvements to those areas, unlocking extra capacity without overhauling the wholesale system.
7Inconsistent Shift Handover:
Negative Impact: Crucial information gets lost between shifts in ad-hoc handoffs. This leads to delays, confusion, dropped tasks, and repeating work – all of which add up to wasted time and capacity.
Positive Step: Standardize handover protocols with digital checklists and real-time dashboards. This ensures seamless continuity and eliminates “knowledge amnesia” between shifts.
8Spiraling Miscommunication:
Negative Impact: Reliance on verbal updates creates miscommunication chains. Shop floor realities get distorted as they move up the ladder, causing bad decisions and misplaced priorities.
Positive Step: Direct shop floor data feeds into dashboards visible to all levels. This creates a single source of truth, aligning decision-makers with ground-level realities.
9Unrecognized Emerging Trends:
Negative Impact: Subtle changes in machine performance, material quality, etc., get missed without data analysis. These minor issues turn into significant problems, impacting efficiency and output.
Positive Step: Use predictive analytics tools on manufacturing data streams. These tools can alert you to emerging trends early, allowing for pre-emptive maintenance or process adjustments.
10Excess Motion and Wasted Effort:
Negative Impact: Without visibility into how operators perform tasks, inefficiencies creep in. This leads to unnecessary steps, wasted movements, poor workstation layouts, and an overall decline in worker productivity. Even small, seemingly insignificant wasted motions add up across hundreds of cycles, significantly eating into capacity.
Positive Step: Use a combination of video monitoring and sensor data to analyze worker movements closely. These insights reveal areas where streamlining workflows, optimizing tool placement, and improving ergonomics will yield significant time savings. Invest in worker training on efficiency techniques such as optimizing body movements to reduce wasted effort, which translates into more output over time.
The Path to Unlocking Hidden Capacity
The issues outlined in this article might feel overwhelming, but the truth is that every one of them is fixable. You unleash a wave of improvements by gaining granular visibility into your operations and regaining control over your processes. Cycle times become predictable, quality issues evaporate, training gaps are filled, and a steady flow of reliable data allows you to scale confidently.
POWERS: Your Partner in the Visibility Revolution
At POWERS, we understand the unique challenges that manufacturers face. Our solutions are designed to deliver the real-time insights and control you need to transform your shop floor. We combine cutting-edge sensor technology, powerful analytics, and expert guidance to:
- Illuminate Hidden Bottlenecks: Pinpoint precisely where capacity is being lost, giving you the targeted focus to break through those limits.
- Elevate Efficiency: Optimize workflows, reduce wasted effort, and maximize the output of every operator and machine.
- Drive Data-Driven Decisions: Replace guesswork and assumptions with hard data, enabling strategic choices that yield measurable results.
The End of the Blind Spot Era
In an increasingly competitive landscape, running your manufacturing operation without full visibility is simply not an option. The good news is that the journey to greater efficiency and maximum capacity utilization doesn’t have to be a solitary one. Contact POWERS today to explore how we can help you break free from the cycle of underperformance and achieve the untapped potential that lies within your factory walls.
Optimize your manufacturing processes and achieve unprecedented efficiency. Contact POWERS today to learn how our expertise can drive your company’s success. Let’s start the conversation: +1 678-971-4711 or info@thepowerscompany.com.
Continue Reading from this Mastery Series
- Part 1 – The Price of Lost Revenue and Profit Resulting from Underutilized Capacity
- Part 2 – How Rising Production Costs Hide Your Factory’s True Potential
- Part 3 – Poorly Managing Resources is Stealing Your Profits
- Part 4 – Break the Quality Struggle Cycle to Fix This Shop Floor Frustration
- Part 5 – From Chaos to Capacity: How to Tame Turnover and Optimize Your Operations
- Part 6 – Manufacturing Nightmares: When Your Shop Floor Can’t Keep Up
- Part 7 – When Supply Chain Disruptions Reveal Your True Capacity
- Part 8 – Unlocking Efficiency When Sustainability Meets the Shop Floor
- Part 9 – Understaffed and Underperforming on the Shop Floor
- Part 10 – How Blind Spot Vulnerabilities Impact Your Shop Floor’s Efficiency