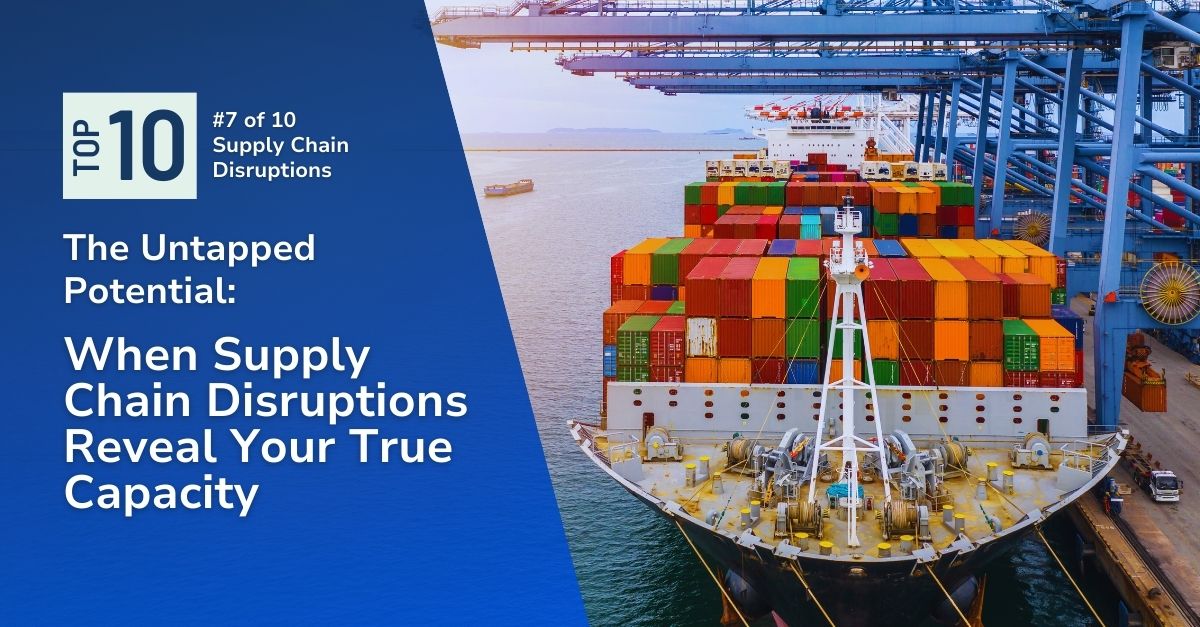
Navigating supply chain disruptions has become synonymous with modern manufacturing. Yet, amidst the scramble to adapt, these turbulent times expose a deeper structural issue – underperforming capacity utilization.
When established production systems designed for predictability fail to deliver, it often signifies that manufacturers have not maximized their true output potential.
When the usual flow of resources is disrupted, the vulnerabilities within your manufacturing operation become glaring. Production lines are designed for a predictable pace of sputter and stalling.
Inability to meet demand highlights a hidden truth: you haven’t truly maximized the potential output of your facilities, equipment, and people.
Blaming supply chains for missed production targets or unmet customer expectations is easy. However, gaining true mastery in manufacturing means going deeper. In this entry, we’ll examine 10 secondary symptoms that signal your operation hasn’t fully optimized its capacity despite the turmoil of supply chain challenges.
By understanding these telltale signs, you’ll embark on a transformative journey. You’ll learn to unlock your untapped potential, bridging the gap between what you’re producing now and what you’re truly capable of. This knowledge is the key to building a resilient manufacturing operation – one that survives disruptions and thrives because of them.
1Unexpected Scrap Rate Increases:
Negative Impact: When your trusted supplier suddenly can’t deliver the usual raw materials, you might be forced to find an alternate source. While specs may seem identical on paper, subtle variations in materials’ composition, purity, or consistency can significantly affect your manufacturing process. This may lead to higher waste, increased defects, and unanticipated delays.
Positive Step: Implement a rigorous Material Qualification Process (MQP) for new material sources. Establish baseline testing for critical properties, develop comprehensive material acceptance criteria, and maintain robust documentation for traceability.
2Inconsistent Product Finishes:
Negative Impact: Switching to a new supplier of coatings, plating, or other finishing treatments can be disastrous if the process controls aren’t mirrored exactly. Inconsistencies in color, texture, or durability negatively impact customer perception and can even affect product functionality.
Positive Step: Work closely with new suppliers to meticulously define specifications. Perform thorough testing on sample batches, obtain formal certifications when relevant, and ensure that quality control (QC) procedures are aligned and monitored.
3“Rogue” Workarounds:
Negative Impact: Faced with shortages, production teams on the front lines may feel pressured to improvise. While their intentions are good, these workarounds can introduce hidden risks. Unauthorized substitutions, undocumented process changes, and shortcuts might temporarily alleviate bottlenecks but can also lead to defects, safety issues, and traceability problems down the line.
Positive Step: Encourage open communication channels for proactive problem-solving. Invest in cross-training to equip your workforce with broader skillsets and foster greater adaptability. Implement a formal change management system to track and review any deviations from standards.
4Unforeseen Assembly Issues:
Negative Impact: Even minor changes in component dimensions, tolerances, or material properties can throw a wrench into established assembly processes. Parts that “should” fit may not, requiring time-consuming adjustments, re-work, or even design changes. This creates production stalls and can significantly hinder on-time delivery.
Positive Step: Develop collaborative solid partnerships with your suppliers. Share engineering drawings, detailed specifications, and critical quality characteristics upfront. Conduct pre-production runs with alternate components to identify and resolve potential assembly problems early.
5Logistical Challenges:
Negative Impact: When usual transportation lead times are unreliable, the production schedule derails. Unexpected delays, increased costs, and last-minute rescheduling take resources away from value-added activities. Bottlenecks and backlogs emerge, adding to overall chaos.
Positive Step: Build redundancy into your logistics network. Explore alternative carriers, consider diversifying your supplier base geographically, and negotiate contract flexibility for expedited shipping when needed.
6Packaging Woes:
Negative Impact: Changing packaging suppliers or materials might seem like a minor adaptation, but unforeseen challenges can arise. Protective packaging designed for one component format may be insufficient for another. New packaging might not integrate well with automated systems, creating slowdowns and errors.
Positive Step: Treat packaging design and validation as an integral part of the product development process. Conduct thorough testing with new packaging under actual shipping and storage conditions.
7Labeling Confusion:
Negative Impact: Regulatory requirements, customer-specific instructions, or even your internal processes might change when dealing with new materials or suppliers. Labeling errors—whether missing information, outdated data, or poor print quality—can lead to product misidentification, costly recalls, or compliance issues.
Positive Step: Invest in flexible labeling systems that can quickly adapt to changes. Implement strict label review processes before production runs. Consider adopting barcode or RFID technology for enhanced accuracy and traceability.
8Compatibility Issues with Existing Stock:
Negative Impact: Alternate components or materials sourced during disruptions may not seamlessly integrate with your existing inventory. Slight variations can lead to mismatches, performance issues, or difficulties during product assembly, causing line stoppages and re-work.
Positive Step: Maintain detailed component compatibility matrices. Utilize “first-in, first-out” (FIFO) inventory management practices for age-sensitive or version-dependent materials. Employ rigorous quality control inspection to identify discrepancies.
9Warehouse Layout Chaos:
Negative Impact: Supply chain disruptions often necessitate quick changes to your inventory mix. New materials may require special storage conditions, have different handling requirements, or simply add complexity to your warehouse layout. This can lead to inefficiencies in picking, packing, and shipping processes.
Positive Step: Regularly optimize your warehouse layout, considering product flow, storage optimization, and safety. Invest in warehouse management software (WMS) for better inventory tracking, location assignment, and picking path optimization.
10“Phantom Inventory” Issues:
Negative Impact: When substitutions and workarounds become the norm, inconsistencies creep into inventory records. “Phantom inventory” – materials or components registered in your system but physically unavailable – disrupts planning and procurement processes, leading to stockouts and production delays.
Positive Step: Prioritize inventory accuracy through regular cycle counts and audits. Enforce strict change control processes that tie into your inventory management system. Invest in technologies like barcode or RFID scanners to improve tracking throughout the shop floor.
Conclusion: Building Resilience from Within
While supply chain disruptions are undoubtedly a major obstacle, they also serve as a wake-up call. The secondary symptoms we’ve explored in this post expose areas where your manufacturing operation can be strengthened and optimized. By addressing inefficiencies, inconsistencies, and hidden vulnerabilities – laying the foundation for resilience and increased profitability.
This transformation is about more than just reacting to external forces. It’s about uncovering your manufacturing operation’s true potential by maximizing your existing resources.
How POWERS Can Help
At POWERS, we understand the complexities that manufacturers face – especially in today’s volatile environment. Our seasoned experts have decades of experience optimizing manufacturing processes, eliminating waste, and driving maximum output from existing assets.
We offer customized solutions tailored to your unique challenges, spanning:
- Capacity Utilization Assessments: We conduct in-depth analyses to pinpoint bottlenecks, underutilized resources, and areas for improvement.
- Operational Efficiency Consulting: We work with you to streamline workflows, reduce downtime, and implement lean manufacturing principles.
- Training and Development: We provide customized training programs to empower your team with the skills to drive continuous improvement.
Don’t let supply chain disruptions be the sole arbiter of your success. Optimize your manufacturing processes and achieve unprecedented efficiency. Contact POWERS today to learn how our expertise can drive your company’s success. Let’s start the conversation: +1 678-971-4711 or info@thepowerscompany.com.
Continue Reading from this Mastery Series
- Part 1 – The Price of Lost Revenue and Profit Resulting from Underutilized Capacity
- Part 2 – How Rising Production Costs Hide Your Factory’s True Potential
- Part 3 – Poorly Managing Resources is Stealing Your Profits
- Part 4 – Break the Quality Struggle Cycle to Fix This Shop Floor Frustration
- Part 5 – From Chaos to Capacity: How to Tame Turnover and Optimize Your Operations
- Part 6 – Manufacturing Nightmares: When Your Shop Floor Can’t Keep Up
- Part 7 – When Supply Chain Disruptions Reveal Your True Capacity
- Part 8 – Unlocking Efficiency When Sustainability Meets the Shop Floor
- Part 9 – Understaffed and Underperforming on the Shop Floor
- Part 10 – How Blind Spot Vulnerabilities Impact Your Shop Floor’s Efficiency