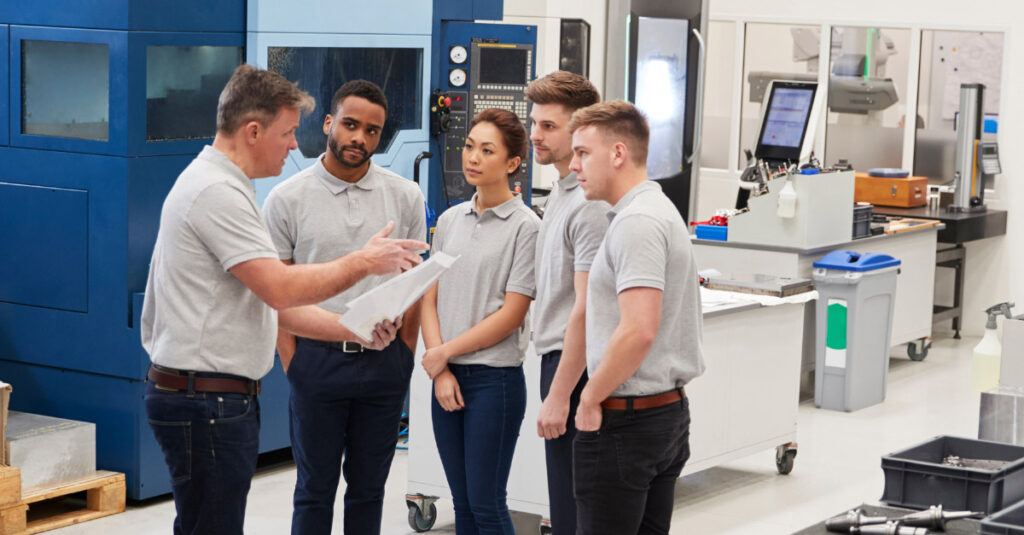
The search for new ways to improve productivity and profitability in the highly competitive manufacturing world is ceaseless. However, one area that often flies under the radar holds significant potential for boosting both: the development of leadership skills and behaviors in frontline supervisors and managers.
At POWERS, we emphasize that the value of frontline leadership skills and behaviors in manufacturing cannot be overstated. These individuals directly supervise the production process, interact closely with the workforce, and oversee the implementation of critical operational changes. By strengthening their leadership capabilities, manufacturing companies can unlock new levels of performance and efficiency.
Frontline Leadership Skills and Decision-Making
Effective decision-making is a critical leadership competency, particularly in the fast-paced manufacturing environment. Frontline supervisors and managers often have to make quick, on-the-spot decisions that can significantly impact the production process. By investing in developing their decision-making skills, organizations can ensure that these decisions are prompt but also well-informed, balanced, and strategically aligned.
When frontline leaders can make better decisions, it leads to enhanced operational efficiency, reduced wastage, and improved product quality—all contributing to increased productivity and profitability.
Leadership Skills and Change Management
Dynamic customer demands, technological advancements, and shifting market conditions constantly influence the manufacturing sector. Adapting to these changes requires effective change management—another area where strong frontline leadership can make a difference.
Frontline supervisors and managers are critical in managing change on the shop floor. They are the ones who implement new processes, adapt to changes in production schedules, and manage the workforce through periods of change.
By equipping these leaders with robust change management skills, companies can ensure smoother transitions, minimal disruptions to productivity, and quicker realization of the benefits of change. This helps maintain productivity during change and contributes to long-term profitability as improvements are implemented more effectively.
Communication: A Key Leadership Skill
Communication is an essential leadership skill for frontline supervisors and managers. Effective communication ensures that all team members understand their roles, responsibilities, and targets and are aligned with the organization’s objectives.
Frontline leaders who communicate effectively are better equipped to guide their teams, clarify doubts, and address issues promptly.
This can lead to improved morale, more significant commitment, and higher productivity. Furthermore, effective communication can reduce errors and misunderstandings, leading to better product quality and cost savings.
Developing Frontline Leadership Skills
So how can manufacturing organizations build stronger leadership capabilities in their frontline supervisors and managers? Here are some key strategies:
1Leadership Development Programs:
Provide regular training programs focusing on core leadership skills, including decision-making, change management, and communication. These programs can use various instructional methods, including workshops, simulations, and role-plays, to provide a hands-on learning experience.
2Mentoring and Coaching:
Pairing less experienced leaders with more experienced ones can facilitate on-the-job learning and skill development. Coaches can provide valuable insights, feedback, and guidance, helping new leaders navigate their roles more effectively.
3Performance Feedback:
Regular performance feedback can help frontline leaders understand their strengths and areas for improvement. Constructive feedback can encourage continuous learning and improvement.
4Encourage a Culture of Learning:
Promote an organizational culture that values learning, innovation, and continuous improvement. Encourage leaders to learn from successes and failures and share their learning with their teams.
Conclusions for Business Leaders
Strengthening the leadership capabilities of your frontline supervisors and managers can unlock significant benefits for manufacturing organizations. These leaders can drive greater productivity and profitability by making better decisions, managing change effectively, and communicating clearly. As such, investing in leadership development should be a strategic priority for any forward-thinking manufacturer.
The POWERS Difference
We are a dedicated and results-driven management consulting firm uniquely positioned at the intersection of workplace culture and operational performance. We partner with growth-oriented organizations to cultivate a culture of excellence that fuels productivity, drives efficiency, strengthens competitive advantage, and fuels profitability.
One of the critical areas in which we enhance productivity is through our focus on frontline leadership development.
Leveraging our deep industry expertise and innovative methodologies, we build synergies between people and processes, creating holistic, sustainable change that translates into measurable business outcomes.
Our team has helped executive leadership across many industries operationalize their culture for rapid and sustained performance improvement, increased competitive advantage, greater value, and a stronger bottom line.
To put our experienced team and proven track record to work for you, schedule an initial discovery and analysis by calling +1 678-971-4711 or emailing us at info@thepowerscompany.com.