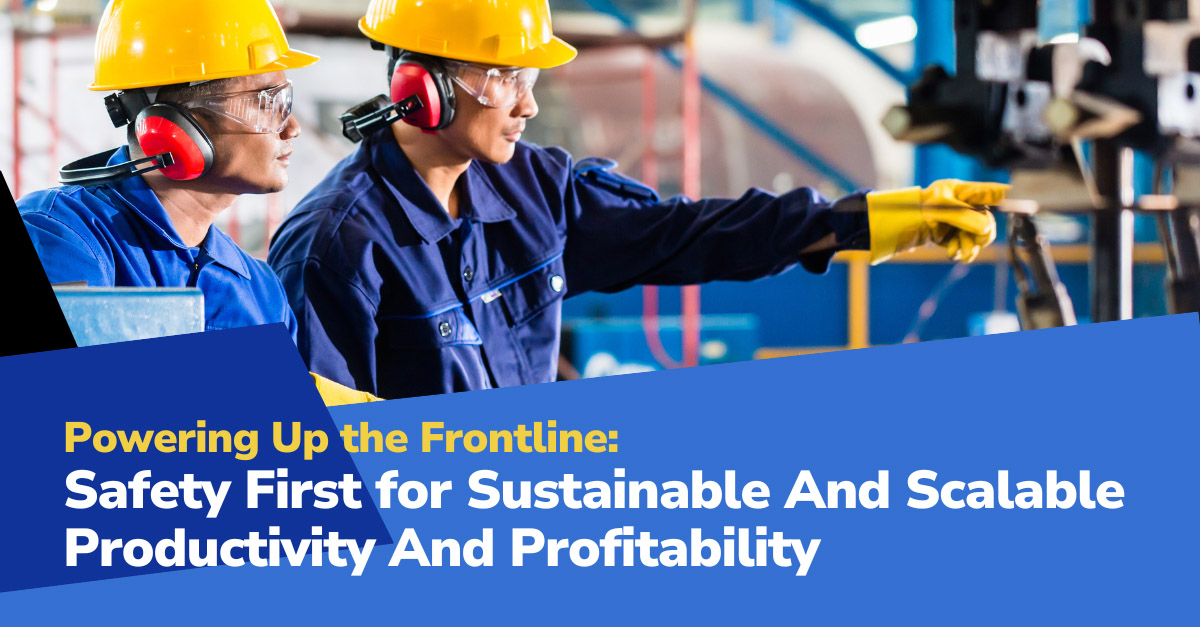
In manufacturing, safety isn’t just about avoiding injuries. It’s about protecting your people, your equipment, and your bottom line.
Every time a frontline leader reinforces safe behavior, every time a team follows protocols correctly, and every time a hazard is addressed before it becomes a crisis, that’s productivity in action. It’s also profitability preserved.
Too often, safety is treated as a siloed initiative, owned by a single department or viewed only through the lens of compliance. But when safety becomes part of the daily rhythm on the floor, led by trained and accountable supervisors, it unlocks powerful operational gains across the board.
Here are 10 ways your operation benefits when safety takes the front seat:
1Reduced Downtime:
Injury-related disruptions and shutdowns don’t just delay schedules, they ripple through your entire operation. A strong safety culture reduces the frequency and severity of these incidents, helping teams maintain continuity across shifts and avoid costly delays. When frontline leaders actively monitor for risks and proactively respond, they keep production lines moving and capacity stable.
2Cost Savings from Fewer Accidents:
Accidents are expensive. From direct costs like medical treatment and equipment repair to indirect hits like lost productivity, missed deliveries, and insurance increases, the financial impact adds up fast. A proactive safety environment helps protect margins by reducing both the frequency and severity of these incidents, cutting costs before they appear on the balance sheet.
3Improved Equipment Lifespan:
Improper machine use, rushed setups, and skipped inspections all take a toll on equipment. But when teams follow proper procedures, powered by clear training and safety-minded leadership, equipment lasts longer and performs more reliably. Preventive safety behaviors are often the key to avoiding early breakdowns and maximizing asset value over time.
4Enhanced Workforce Morale:
People work harder, and smarter, when they know leadership is looking out for their well-being. A visible commitment to safety creates a sense of trust and professionalism that encourages teams to take ownership of their work. Workers feel more valued, more engaged, and more willing to speak up when they see something wrong.
5Reduced Legal and Compliance Costs:
Regulatory fines, OSHA investigations, and safety-related lawsuits can derail even the most efficient operations. But most of these issues are preventable. When frontline leaders are well-versed in compliance requirements and empowered to reinforce standards, they help the entire organization stay ahead of risks and out of the penalty zone.
6Higher Quality Production:
There’s a strong link between safe processes and consistent product quality. Teams that are trained to follow proper procedures, inspect their workstations, and slow down to do it right tend to produce fewer defects and rework. Quality control starts with safe, stable conditions and a workforce that’s focused, not fearful.
7Increased Trust and Brand Reputation:
Safety performance isn’t just tracked internally, it’s noticed by customers, vendors, investors, and future employees. A clean record builds confidence and shows that your company runs a disciplined, reliable operation. In a competitive market, reputation matters, and strong safety leadership is one of the fastest ways to enhance it.
8Streamlined Training Processes:
When safety protocols are embedded into daily routines, training gets easier and more effective. Standard work becomes easier to teach, and new hires are brought up to speed with fewer gaps. Clear expectations, visual cues, and well-practiced procedures create a safer, smoother onboarding process for every role on the floor.
9Operational Efficiency:
Every unexpected stop cuts into your OEE. Every missed hazard increases cycle variability. Teams that make safety a routine part of shift startup meetings, walk-throughs, and reporting workflows reduce these disruptions and improve flow. Safety isn’t a distraction from productivity, it’s the foundation of it.
10Attracting Top Talent:
Skilled labor is in high demand. Workers increasingly look at safety records when choosing where to apply, and where to stay. A visible commitment to safety, backed by training, follow-through, and leadership support, helps manufacturers compete for the best people in a tight labor market.
How POWERS Helps You Turn Safety Into a Strategic Advantage
At POWERS, we don’t just encourage safer behavior, we build leadership systems that make safety a core part of how productivity happens.
The result is not only fewer incidents, but also better communication, faster responses to hazards, and more empowered teams at every level.
We also provide our clients with DPS, our enterprise productivity platform, to drive consistent execution. With DPS, your supervisors and managers can track safety KPIs, document corrective actions, and close the loop on incident trends, all from a centralized dashboard that aligns safety goals with operational performance.
Turn Safety from a Cost Center into a Performance Driver
When safety is owned at every level, not just enforced from the top down, it becomes one of your most reliable performance levers. With the right leadership support and tools in place, you can improve safety outcomes and boost throughput, reduce costs, and strengthen your workforce.
To put our experienced team and proven track record to work for you, schedule an initial discovery and analysis by calling +1 678-971-4711 or emailing us at info@thepowerscompany.com.
Continue Reading from this Mastery Series
- Part 1 - Strategic Alignment that Bridges Daily Tasks with Broader Visions for Unified Organizational Success
- Part 2 - Crafting Clarity through Effective Communication and Active Listening
- Part 3 - Sharpening Decision-Making Prowess for Seamless Operations and Minimal Downtimes
- Part 4 - Championing Lean Principles for Streamlined Success and an Ever-Evolving Workplace
- Part 5 - Mastering Performance Management for Optimal Team Output and Growth
- Part 6 - How Leaders Well-Trained in the Soft Skills Transform Manufacturing Teams
- Part 7 - Strengthening Conflict Resolution Skills for Peak Productivity and Profitability Gains
- Part 8 - Unleashing Potential with Precision Time and Resource Management
- Part 9 - Safety First for Sustainable And Scalable Productivity And Profitability
- Part 10 - Equipping Your Shop Floor Leaders to Be Effective Change Managers