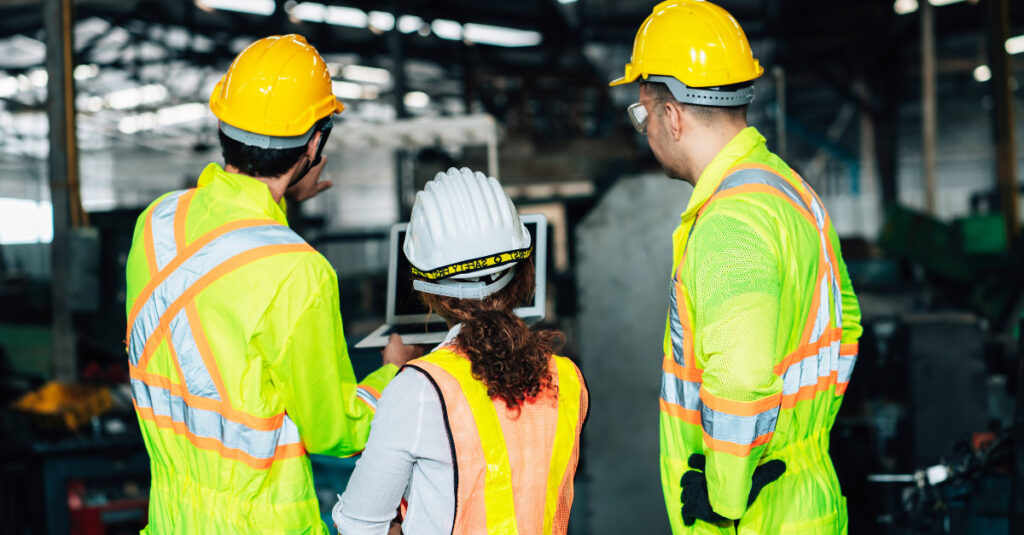
As manufacturers face uncertain economic times, they must consider various short-term and long-term cost cutting strategies to increase efficiencies while improving productivity and the bottom line. Here's our take on what steps manufacturers can take now and over the long haul, to reduce costs.
Manufacturing is a crucial industry that drives economic growth, job creation, and innovation across the globe. However, manufacturing is also a highly competitive industry where businesses must continuously strive to reduce costs, increase efficiency, and remain competitive in a constantly evolving marketplace.
This is particularly true in today’s world where supply chain disruptions, global trade uncertainties, and changing consumer demands are all contributing factors that make manufacturing cost-cutting an essential business strategy.
While short-term cost-cutting measures such as reducing labor costs or optimizing inventory management can provide immediate relief, they may not be sustainable in the long term. Sustainable cost-cutting requires a long-term strategic approach that focuses on developing a culture of continuous improvement, reducing waste, and improving efficiency across all aspects of the manufacturing process.
This approach involves investing in advanced technologies such as automation, artificial intelligence, and the Internet of Things (IoT), optimizing supply chain management, and improving employee training and development.
As manufacturers face increasing pressure to reduce costs and improve efficiency, they must consider a variety of strategies to achieve these goals. In the short term, manufacturers can implement several cost-cutting measures to achieve immediate results.
These strategies include implementing cost reduction measures, increasing workforce productivity, implementing lean manufacturing practices, and optimizing inventory management.
Short-Term Strategies for Reducing Manufacturing Costs
Short-term strategies are essential for manufacturing companies to achieve immediate cost savings and improve their bottom line. Below, we will elaborate on each of the short-term strategies for manufacturing cost-cutting.
1 Implement Cost Reduction Measures
The first step in implementing cost reduction measures is to identify areas where costs can be cut without negatively impacting product quality or customer satisfaction. This can include reducing the cost of raw materials, identifying cost-saving opportunities in the supply chain, negotiating better pricing with suppliers, and reducing overhead costs.
To reduce the cost of raw materials, manufacturers can look for alternative suppliers or renegotiate pricing with existing suppliers. They can also explore alternative materials that are more cost-effective but still meet the same quality standards.
Identifying cost-saving opportunities in the supply chain can involve optimizing transportation routes, reducing inventory levels, and streamlining logistics. Negotiating better pricing with suppliers can involve leveraging purchasing power, bundling orders, and developing long-term relationships. To reduce overhead costs, manufacturers can look for ways to streamline administrative functions, reduce energy consumption, and optimize production scheduling.
Once cost-saving opportunities have been identified, manufacturers can implement strategies to reduce costs. This can include optimizing production processes to reduce waste, implementing cost-effective inventory management practices, and improving labor productivity.
For example, manufacturers can implement just-in-time inventory management practices to reduce inventory costs, or implement total productive maintenance (TPM) practices to reduce equipment downtime and maintenance costs.
2 Increase Workforce Productivity
To increase workforce productivity, manufacturers can implement a range of measures. One way is to provide regular training to employees to improve their skills and knowledge, which can enhance their performance and efficiency. This can include training in new manufacturing processes or equipment, as well as training in leadership skills, teamwork, problem-solving, and communication.
Another way to increase workforce productivity is to implement performance metrics and incentives. By setting clear performance targets for employees and incentivizing them to meet or exceed those targets, manufacturers can motivate employees to work more efficiently and productively. This can include providing bonuses, promotions, or other rewards for achieving targets, as well as providing feedback on employee performance and encouraging continuous improvement.
Manufacturers can also use technology to increase workforce productivity. For example, automation can help streamline production processes and reduce the need for manual labor, which can reduce labor costs and increase efficiency. Robotics and other forms of automation can be used to perform repetitive or dangerous tasks, freeing up employees to focus on higher value-added activities.
Lastly, manufacturers can improve workforce productivity by optimizing production scheduling and workflow. By identifying bottlenecks and inefficiencies in the production process, manufacturers can improve production flow and reduce idle time. This can include implementing lean manufacturing practices or using software tools to optimize production scheduling and sequencing.
3 Implement Lean Manufacturing Practices
There are several key principles of lean manufacturing that manufacturers can implement to achieve cost savings in the short term. One principle is to identify and eliminate non-value-added activities. Non-value-added activities are any activities that do not add value to the product or service and can include overproduction, waiting time, transportation, and excess inventory. By eliminating non-value-added activities, manufacturers can reduce waste and improve efficiency.
Another principle of lean manufacturing is to optimize the flow of materials and information. This involves identifying bottlenecks and inefficiencies in the production process and implementing strategies to improve the flow of materials and information. This can include using visual management tools, optimizing production scheduling, and improving communication between departments.
A third principle of lean manufacturing is to empower employees to identify and solve problems. This involves giving employees the tools and training they need to identify inefficiencies and waste in the production process and empowering them to come up with solutions. This can include using continuous improvement tools like Kaizen, which involves making small, incremental improvements to the production process over time.
Finally, lean manufacturing involves implementing a culture of continuous improvement. This involves creating a work environment where employees are encouraged to identify inefficiencies and waste in the production process and are given the tools and resources they need to make improvements. This can include regular training, feedback, and incentives for identifying and implementing cost-saving measures.
4 Optimize Inventory Management
To optimize inventory management, manufacturers can implement a range of measures. One way is to implement just-in-time (JIT) inventory management. JIT involves producing and delivering products just in time to meet customer demand, thereby reducing the need for excess inventory. By reducing inventory levels, manufacturers can reduce the cost of holding inventory, including the cost of storage, handling, and obsolescence.
Another way to optimize inventory management is to implement inventory control systems. Inventory control systems involve using software tools to monitor inventory levels and automatically reorder products when inventory levels fall below a certain threshold. This can help ensure that manufacturers have the right amount of inventory on hand to meet customer demand without holding excess inventory.
Manufacturers can also optimize inventory management by implementing effective forecasting and demand planning. By accurately forecasting demand, manufacturers can ensure that they have the right amount of inventory on hand to meet customer demand without holding excess inventory. This can include using data analytics and machine learning to analyze past sales data and forecast future demand.
Finally, manufacturers can optimize inventory management by improving supply chain management. By working closely with suppliers and customers to improve visibility and coordination in the supply chain, manufacturers can reduce lead times and inventory levels, which can lead to significant cost savings.
Short-term strategies are critical for manufacturing companies to achieve immediate cost savings and improve their bottom line. By implementing cost reduction measures, increasing workforce productivity, implementing lean manufacturing practices, and optimizing inventory management, manufacturers can achieve significant cost savings and increase efficiency over the short term.
Long-Term Strategies for Cost Reduction
While short-term strategies are effective for achieving immediate cost savings, long-term strategies are necessary for sustainable cost-cutting and growth. Below, we will elaborate on each of the long-term strategies for manufacturing cost-cutting.
1 Invest in Automation and Technology
There are several ways that manufacturers can invest in automation and technology to reduce costs. One way is to automate repetitive tasks in the production process. This can include using robots and other automated systems to handle tasks like assembly, packaging, and quality control. By automating these tasks, manufacturers can reduce labor costs, increase efficiency, and improve product quality.
Another way to invest in automation and technology is to implement data analytics and machine learning tools. These tools can help manufacturers analyze production data and identify inefficiencies in the production process. By identifying these inefficiencies, manufacturers can make targeted improvements that can help reduce costs and improve efficiency over time.
Manufacturers can also invest in advanced sensors and monitoring systems to improve quality control and reduce waste. These systems can help detect defects and other quality issues in real-time, allowing manufacturers to make corrections quickly and efficiently. By reducing waste and improving quality, manufacturers can achieve significant cost savings over the long term.
Finally, manufacturers can invest in technologies that enable them to produce more customized products. This can include using 3D printing and other advanced manufacturing technologies to produce products on demand, reducing the need for excess inventory and reducing the cost of holding inventory.
2 Implement Lean Manufacturing Practices
There are several principles of lean manufacturing that manufacturers can implement to reduce costs. One principle is to minimize inventory levels. By reducing inventory levels, manufacturers can reduce the cost of holding inventory, including the cost of storage, handling, and obsolescence. This can be achieved through just-in-time (JIT) inventory management, as discussed in the short-term strategy section.
Another principle of lean manufacturing is to optimize production flow. This involves eliminating bottlenecks and other inefficiencies in the production process to ensure that products move smoothly through the production process. By optimizing production flow, manufacturers can reduce lead times and increase efficiency, reducing costs and improving customer satisfaction.
Manufacturers can also implement continuous improvement programs to identify and eliminate waste in the production process. This can involve using tools like value stream mapping and root cause analysis to identify inefficiencies in the production process and make targeted improvements to reduce waste and improve efficiency over time.
Finally, manufacturers can implement a culture of continuous learning and improvement. This involves training employees on lean manufacturing principles and encouraging them to identify and implement improvements in their work processes. By empowering employees to take ownership of the production process and make improvements, manufacturers can achieve significant cost savings over the long term.
3 Improve Supply Chain Management
One way to improve supply chain management is to optimize supplier relationships. This involves working closely with suppliers to develop long-term partnerships and negotiate favorable terms for the purchase of raw materials and other inputs. By working with suppliers to reduce costs and improve efficiency, manufacturers can achieve significant cost savings over the long term.
Another way to improve supply chain management is to implement supply chain visibility tools. These tools enable manufacturers to track the movement of goods through the supply chain, identify bottlenecks and inefficiencies, and make targeted improvements to reduce costs and improve efficiency.
Supply chain visibility tools can also help manufacturers respond quickly to disruptions in the supply chain, reducing the risk of delays and other disruptions that can increase costs.
Manufacturers can also implement demand forecasting tools to improve supply chain management. Demand forecasting involves using historical data and other information to predict future demand for products. By accurately predicting demand, manufacturers can optimize production schedules, reduce inventory levels, and improve efficiency, reducing costs and improving customer satisfaction.
Finally, manufacturers can implement sustainability practices to improve supply chain management. This can include using eco-friendly materials, reducing waste and energy consumption, and promoting ethical labor practices throughout the supply chain. By implementing sustainable practices, manufacturers can reduce costs, improve efficiency, and enhance their reputation with customers and other stakeholders.
4 Focus on Employee Training and Development
Manufacturers can implement training programs to improve employee skills and knowledge. This can include training on the latest manufacturing technologies and processes, safety procedures, quality control methods, and other areas relevant to the production process. By improving employee skills and knowledge, manufacturers can reduce errors, improve quality, and increase efficiency, reducing costs over time.
Another way to focus on employee training and development is to encourage continuous learning and improvement. Manufacturers can implement programs that encourage employees to identify areas for improvement in their work processes and develop solutions to address them. By empowering employees to take ownership of their work and make improvements, manufacturers can achieve significant cost savings and improve efficiency over time.
Manufacturers can also implement incentives and recognition programs to reward employees for their contributions to cost-cutting and efficiency improvement efforts. This can include bonuses, promotions, and other forms of recognition that motivate employees to work harder and smarter.
Finally, manufacturers can create a positive work environment that fosters teamwork, collaboration, and open communication. By creating a culture that values employee input and encourages innovation, manufacturers can create a workforce that is engaged, motivated, and committed to improving efficiency and reducing costs over the long term.
5 Implement Energy Efficiency Measures
One way to implement energy efficiency measures is to conduct an energy audit. This involves identifying areas of the production process where energy is being wasted and developing solutions to address them. Energy audits can help manufacturers identify opportunities for improvement and prioritize investments in energy efficiency measures that will deliver the greatest return on investment.
Another way to implement energy efficiency measures is to invest in energy-efficient equipment and technologies. This can include upgrading lighting systems, HVAC systems, and production equipment to more energy-efficient models. While these investments can be costly upfront, they can deliver significant cost savings over the long term through reduced energy consumption.
Manufacturers can also implement energy management systems to monitor and control energy consumption throughout the production process. These systems can help manufacturers identify energy-intensive processes and implement solutions to reduce energy consumption in those areas. Additionally, energy management systems can help manufacturers track energy usage over time and identify opportunities for further improvement.
Finally, manufacturers can implement renewable energy sources, such as solar or wind power, to generate energy on-site. While these investments can be costly upfront, they can deliver significant cost savings over the long term through reduced energy costs and improved sustainability.
Long-term strategies are essential for sustainable cost-cutting and growth in the manufacturing industry. By investing in automation and technology, implementing lean manufacturing practices, improving supply chain management, focusing on employee training and development, and implementing energy efficiency measures, manufacturers can achieve sustainable cost savings and improve efficiency over the long term.
Conclusions for Business Leaders
Cost-cutting is a critical business strategy for manufacturers looking to improve efficiency, reduce costs, and drive growth. While short-term measures can provide immediate relief, long-term strategies are necessary for sustained success.
By implementing short-term strategies such as cost reduction measures, increasing workforce productivity, and optimizing inventory management, manufacturers can achieve immediate cost savings.
However, to achieve long-term success, manufacturers must also invest in advanced technologies such as automation and the IoT, implement lean manufacturing practices, improve supply chain management, focus on employee training and development, and implement energy efficiency measures.
By adopting a strategic approach to cost-cutting that balances short-term needs with long-term sustainability, manufacturers can achieve sustainable success. Such an approach requires a focus on developing a culture of continuous improvement, reducing waste, and improving efficiency across all aspects of the manufacturing process.
By investing in advanced technologies, optimizing supply chain management, and focusing on employee training and development, manufacturers can not only reduce costs but also improve product quality, enhance customer satisfaction, and drive growth in a highly competitive marketplace.
The POWERS Difference
At POWERS, we focus on Leadership Engagement and Development to transform operational performance and prepare your leaders for the future. We help you build a performance culture that operates at peak levels to lower costs, increase productivity, build agility, and sustain that performance over the long haul.
Our team has helped executive leadership across many industries operationalize their culture for rapid and sustained performance improvement, increased competitive advantage, greater value, and a stronger bottom line.
Find out about our new AMP (Advanced Maintenance Performance) Program and put our experienced team and proven track record to work for you. Schedule an initial discovery and analysis by calling +1 678-971-4711 or emailing us at info@thepowerscompany.com.