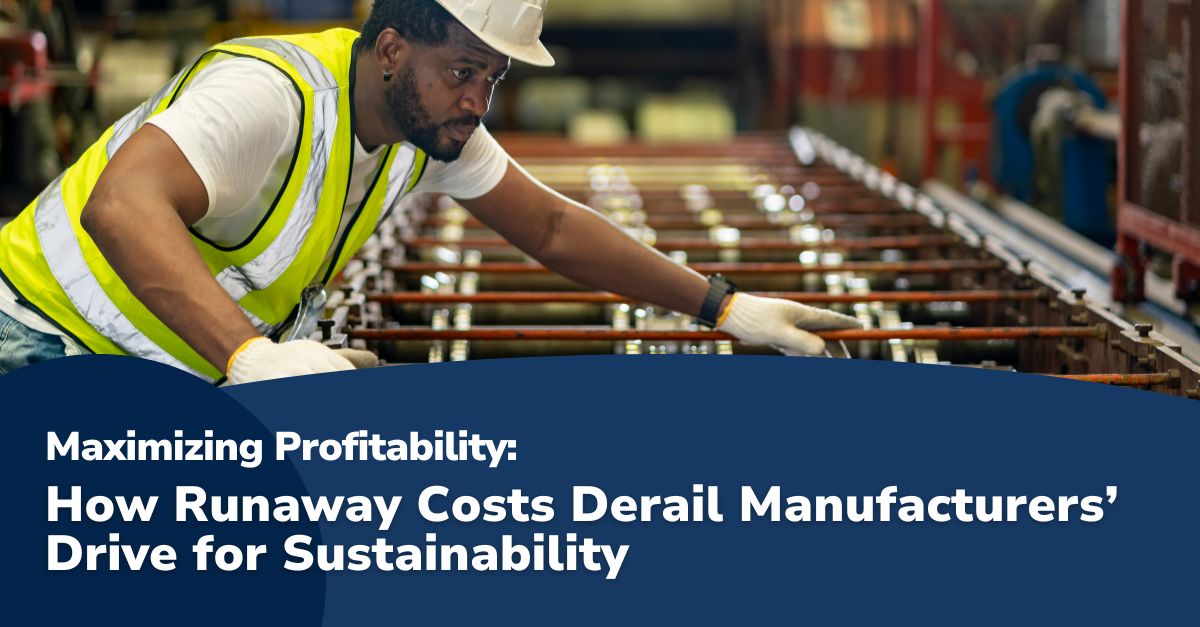
Manufacturing is a cornerstone of global economies, driving innovation, employment, and economic growth. However, companies face many challenges threatening their competitiveness, profitability, and long-term sustainability.
Among these challenges, rising operational costs are a critical hurdle that can stifle growth and dampen innovation.
From the surge in raw material prices to the increasing costs of labor, energy, and compliance with environmental regulations, manufacturers constantly battle to keep their expenses in check while striving to maintain quality and meet consumer demands.
This complex scenario is further exacerbated by global economic fluctuations, supply chain disruptions, and the push toward sustainability, which, while essential, adds another layer of operational considerations and investments. The interplay of these factors makes it increasingly difficult for manufacturing companies to achieve their financial goals and sustain growth without significantly changing their operational strategies.
In this detailed exploration, we delve into the top 10 ways increased operational costs harm or hamper manufacturing companies and provide actionable insights and positive steps manufacturers can take to mitigate each challenge. Our discussion is rooted in credible sources and factual data, offering a comprehensive guide for manufacturers seeking to navigate the turbulent waters of rising operational costs.
By understanding the nuances of these challenges and implementing the strategies outlined herein, manufacturing companies can transform operational costs from a burden into a catalyst for innovation, efficiency, and sustainable growth. This journey requires a proactive approach, where every aspect of the operation is analyzed, optimized, and aligned with the broader sustainability and profitability goals.
1Reduced Profitability:
Negative Impact: Elevated operational expenses directly affect profit margins. As costs rise, companies rely on the financial buffer for reinvestment, shareholder dividends, and rainy-day funds diminish, challenging the foundation of business sustainability.
Positive Step: Manufacturers can counteract this by adopting lean manufacturing principles to streamline production processes to eliminate waste and improve efficiency. Companies can significantly reduce their operational expenses by utilizing technologies such as predictive maintenance and energy-efficient machinery. Moreover, renegotiating supplier contracts and bulk purchasing can also lead to substantial cost savings.
2Diminished Competitiveness:
Negative Impact: Increased costs diminishes the ability to offer products at competitive prices. This impact can lead to a loss of market share as customers flock to more affordable alternatives, thereby reducing sales and profitability.
Positive Step: Companies should focus on creating value through innovation and product differentiation to mitigate this. This process can involve investing in R&D to develop unique features or improve product quality, justifying a higher market price point.
3Eroded Margins:
Negative Impact: Rising operational costs directly impact profit margins, limiting the funds available for growth initiatives, such as expansion into new markets or research and development.
Positive Step: To bolster profits, companies can explore alternative revenue streams, such as after-sales services or subscription models. Additionally, strategic partnerships can open new markets and distribution channels with lower upfront costs.
4Production Delays:
Negative Impact: Higher costs may force companies to cut budgets for crucial production resources, leading to delays and lower production efficiency.
Positive Step: Enhancing supply chain management through integrated planning and forecasting and investing in automation can significantly reduce production times and increase efficiency, offsetting higher costs elsewhere.
5Quality Issues:
Negative Impact: To reduce costs, some manufacturers may compromise on quality, leading to increased product failures and damage to the brand’s reputation.
Positive Step: Implementing robust quality control systems and investing in staff training can ensure high-quality production without significantly increasing costs. Adopting a culture of continuous improvement can also lead to cost-effective quality enhancements.
6Employee Morale:
Negative Impact: Cost-cutting often results in layoffs or reduced benefits, which can demoralize the workforce, decrease productivity, and increase turnover.
Positive Step: Open communication about the company’s financial health and engaging employees in finding cost-saving solutions can help maintain morale. Offering non-monetary benefits, such as flexible working conditions or career development opportunities, can also offset discontent.
7Supplier Relationships:
Negative Impact: Aggressive cost reduction efforts can sour relationships with suppliers, potentially leading to less favorable terms and disruptions in supply chains.
Positive Step: Building strong, collaborative relationships with suppliers through transparent communication and mutual benefit initiatives can lead to cost savings for both parties and ensure a reliable supply chain.
8Innovation Stagnation:
Negative Impact: Limited budgets may restrict spending on innovation, curbing the development of new products or technologies and hindering future growth.
Positive Step: Allocating dedicated resources to R&D, even in small amounts, can foster innovation. Collaborating with universities, research institutions, or other companies can also provide access to new ideas and technologies without the need for significant internal investment.
9Environmental Impact:
Negative Impact: Cost reductions might lead to cuts in sustainability initiatives, harming the environment and potentially the company’s public image.
Positive Step: Investing in sustainable practices, such as waste reduction, recycling, and energy efficiency, can lead to long-term cost savings and improve brand reputation. Many governments offer incentives for such investments, reducing the initial financial burden.
10Long-term Viability:
Negative Impact: Persistent high operational costs can endanger a company’s financial stability and long-term survival.
Positive Step: Developing a comprehensive cost management plan that includes regular reviews of expenses, investment in efficiency-improving technologies, and strategic planning can help ensure the company’s longevity.
Conclusions for Manufacturing Operations Leaders: Turning Challenges into Opportunities for Sustainable Growth
The rising tide of operational costs in the manufacturing sector is more than just a challenge; it’s a clarion call for strategic adaptation and innovation. As demonstrated throughout this exploration, these formidable challenges also present unique opportunities for growth, efficiency, and long-term sustainability. By implementing cost-effective measures, prioritizing innovation, and embracing sustainable practices, manufacturing companies can not only mitigate the adverse effects of increased operational costs but also enhance their competitive edge and market position.
The journey towards sustainable manufacturing is not a solo endeavor but a collective movement towards a more efficient, resilient, and environmentally responsible industry.
It involves rethinking traditional processes, adopting new technologies, and fostering a culture of continuous improvement and collaboration. The benefits of this transformation extend beyond the factory floor, contributing to a healthier planet, a stronger economy, and a more sustainable future for all.
Partnering with POWERS for Sustainable Success
As manufacturing companies navigate the complex landscape of rising operational costs, the strategic partnership with POWERS emerges as a beacon of guidance and expertise. POWERS specializes in enhancing operational efficiencies, fostering sustainable practices, and driving profitability through its unique approach to operational consulting. By leveraging their deep industry knowledge and proven methodologies, POWERS works closely with manufacturers to identify cost-saving opportunities, streamline processes, and implement sustainable solutions that reduce operational costs.
A partnership with POWERS is a step towards overcoming the challenges posed by increased operating costs and transforming these challenges into strategic advantages.
Manufacturing companies can secure a prosperous future by focusing on efficiency, sustainability, and innovation, demonstrating that profitability and environmental responsibility can go hand in hand.
Unlock the door to enhanced operational efficiency and cost-effectiveness with POWERS. Start your transformation toward operational excellence now. For a detailed discussion of how we can assist your business, contact our professionals at +1 678-971-4711 or email info@thepowerscompany.com.
Continue Reading from this Mastery Series
- Part 1 - How Runaway Costs Derail Manufacturers’ Drive for Sustainability
- Part 2 - Tackling Excessive Waste Management Issues in Manufacturing
- Part 3 - Mastering Resource Efficiency in the Quest for Manufacturing Excellence
- Part 4 - The Impact of Unmitigated High Energy Costs on Manufacturers
- Part 5 - How the Complexities of Regulatory Compliance Can Erode Margins
- Part 6 - Navigating the Challenges of Reduced Market Competitiveness for Sustained Profitability
- Part 7 - Don’t Let Preferences Pull You Under
- Part 8 - Low Talent Investment is Undermining Your Bottom Line
- Part 9 - Don’t Let Supply Chain Vulnerabilities Bleed Your Profits
- Part 10 - Outsmart the Competition and Protect Your Profits