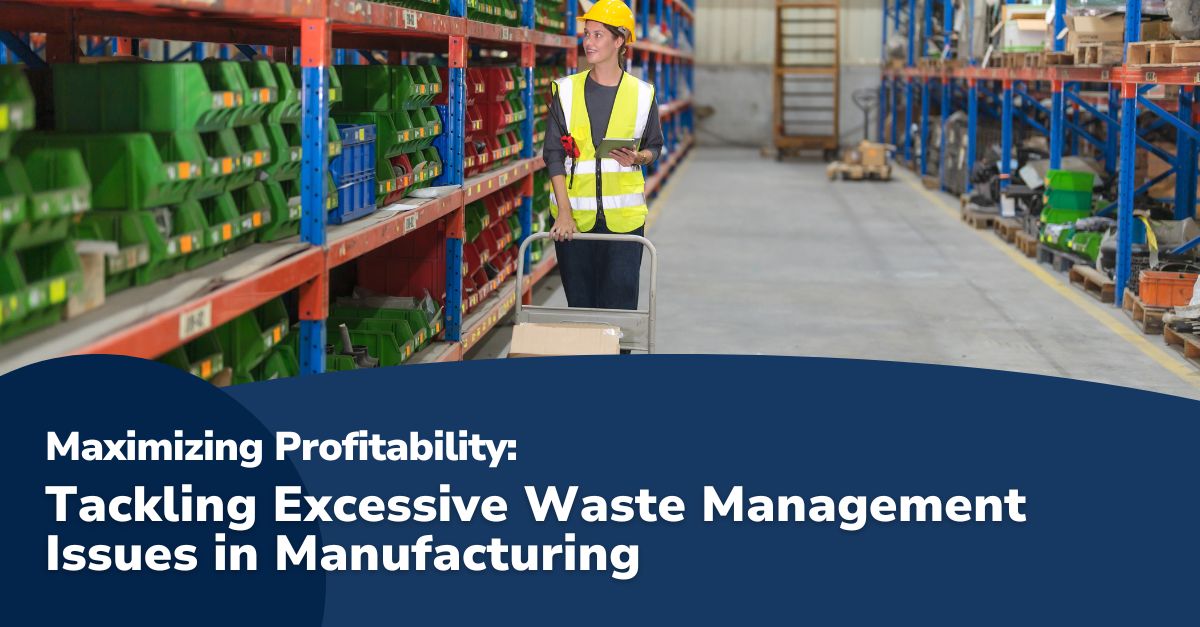
In the relentless pursuit of operational excellence and profitability within the manufacturing sector, we focus on an area critical yet often underestimated in its impact on a company’s bottom line: managing added waste.
This encompasses not only the direct costs of rejects and spoilage but also the broader implications these issues have on operational efficiency and sustainability. As part of the Maximizing Profitability Mastery Series, this second post aims to dissect the complexities surrounding added waste management expenses, highlighting their significance in pursuing financial stability and operational excellence.
The challenge of managing added waste in manufacturing is not just about dealing with the aftermath of production processes but also understanding and mitigating its wide-ranging effects.
These include increased operational costs and compromised product quality, which can significantly detract from a company’s profitability and commitment to sustainable practices. Effective waste management is thus not merely a regulatory obligation but a strategic imperative that can differentiate a company in a competitive marketplace.
Embracing lean manufacturing and waste minimization principles offers a path forward. These approaches not only aim to reduce the physical waste generated on the production floor but also seek to optimize the entire manufacturing process—minimizing inefficiencies, enhancing resource utilization, and ultimately driving down costs associated with waste management. This series of installments will explore strategic insights, actionable steps, and best practices that can empower manufacturers to transform waste management from a cost center into a lever for achieving greater profitability.
By providing a comprehensive exploration of added waste management expenses and their far-reaching implications, this post will guide manufacturing leaders looking to navigate the complexities of modern production environments. Through expert analysis and practical recommendations, we aim to equip manufacturers with the knowledge and tools needed to turn the waste management challenge into an operational refinement and competitive advantage opportunity.
1Capacity Utilization:
Negative Impact: Underutilization of production capacity not only inflates fixed costs per unit but also creates an environment where overproduction becomes likely, increasing the risk of generating excess inventory that may not meet demand.
Positive Step: By leveraging advanced production planning and scheduling software, manufacturers can achieve a delicate balance between demand and production output. These tools offer sophisticated algorithms and data analytics capabilities to forecast demand with greater accuracy, schedule production runs optimally, and adjust operations in real time based on changing market conditions.
2Resource Inefficiency:
Negative Impact: Mismanagement and overconsumption of resources such as raw materials, energy, and water lead to direct financial losses and the depletion of valuable resources. This inefficiency can be exacerbated by outdated processes, lack of awareness, and failure to adopt more sustainable practices, impacting the company’s operational costs.
Positive Step: Conducting comprehensive resource efficiency audits allows manufacturers to pinpoint areas where waste occurs, from excessive raw material use due to overproduction or defects to energy wastage through inefficient machinery and processes. Implementing targeted improvements, such as optimizing material use, upgrading to energy-efficient equipment, and recycling waste, can significantly enhance resource efficiency.
3Production Delays:
Negative Impact: Production delays often stem from various sources, including equipment malfunctions, supply chain disruptions, and inefficient workflows. These delays not only slow down production but can also lead to spoilage of time-sensitive materials, missed delivery deadlines, and a cascading effect of inefficiency throughout the organization.
Positive Step: Predictive maintenance, facilitated by the Internet of Things (IoT) technology and artificial intelligence (AI), can revolutionize equipment management by forecasting potential breakdowns before they occur. This proactive approach minimizes downtime, extends the lifespan of machinery, and ensures a smoother production flow.
4Innovation Stagnation:
Negative Impact: In a rapidly evolving market, innovation failure can leave manufacturers lagging behind competitors and stuck with outdated processes, contributing to waste and inefficiency. Companies may find it challenging to adopt new technologies or methods that could significantly reduce waste and enhance productivity without a commitment to continuous improvement.
Positive Step: Establishing an internal innovation incubator can catalyze change within the company, empowering employees to experiment with new ideas and technologies in a supportive environment. This initiative can lead to the development of breakthrough processes and products that significantly reduce waste, improve efficiency, and drive competitiveness.
5Employee Morale and Productivity:
Negative Impact: The link between employee morale, productivity, and waste reduction is often underestimated. Disengaged employees are less likely to adhere to best practices for efficiency and waste reduction, potentially leading to higher error rates, lower quality output, and increased waste. Conversely, a motivated workforce is more productive, attentive to detail, and invested in the company’s success.
Positive Step: Implementing comprehensive engagement programs that recognize and reward employees for their contributions to waste reduction and efficiency can significantly boost morale and productivity. Training programs that enhance skills and knowledge about sustainable practices further empower employees to contribute to waste reduction efforts.
6Supply Chain Disruptions:
Negative Impact: Supply chain disruptions can lead to significant waste, especially for materials with a limited shelf life or requiring specific storage conditions. Delays in receiving raw materials can force manufacturers to rush production, increasing the likelihood of errors and defects. Conversely, disruptions can also lead to overstocking materials, which may become obsolete or spoil before they can be used.
Positive Step: A resilient supply chain strategy is essential to mitigate these risks. This involves diversifying suppliers to avoid dependence on a single source, investing in supply chain visibility technology to monitor and manage the flow of materials in real time, and establishing strong communication channels with suppliers and logistics partners.
7Customer Satisfaction:
Negative Impact: The direct link between waste, product quality, and customer satisfaction cannot be overstated. Defective products, inconsistent quality, and missed delivery deadlines due to production inefficiencies can severely damage customer trust and loyalty. In today’s market, where consumers are increasingly conscious of quality and sustainability, failing to meet expectations can negatively affect a brand.
Positive Step: Strengthening the quality assurance process ensures consistent product quality and reduces waste. This includes rigorous testing at various stages of production, feedback loops that quickly incorporate customer feedback into quality control processes, and continuous employee training on quality standards.
8Market Competitiveness:
Negative Impact: In a competitive landscape, efficiency and sustainability are increasingly becoming factors that differentiate brands in the eyes of consumers. Companies that fail to address waste and inefficiency risk losing market share to more agile and sustainable competitors.
Positive Step: Leveraging waste reduction and sustainability efforts as part of the company’s value proposition can significantly enhance market competitiveness. This includes marketing the company’s commitment to sustainability, showcasing innovations that reduce waste, and highlighting the benefits of their products.
9Regulatory and Compliance Risks:
Negative Impact: The regulatory landscape for waste management and environmental protection is becoming increasingly stringent, with new laws and standards introduced regularly. Non-compliance can result in significant fines, legal challenges, and damage to the company’s reputation. Keeping abreast of and adhering to these regulations requires constant vigilance and adaptation.
Positive Step: Integrating a comprehensive compliance management system into the company’s operations can streamline compliance with current and future regulations. This system should include mechanisms for monitoring regulatory changes, assessing compliance risks, and implementing necessary adjustments to processes and practices.
10Long-Term Financial Health:
Negative Impact: The cumulative effect of waste and inefficiency can significantly drain a company’s financial resources, affecting its ability to invest in growth and innovation. Over time, this can erode the company’s economic stability and limit its potential for expansion and competitiveness. Addressing waste is not just about reducing costs in the short term but also about ensuring the long-term sustainability and growth of the business.
Positive Step: Strategic investment in technologies and processes that enhance operational efficiency and reduce waste is essential for safeguarding a company’s long-term financial health. This includes adopting automation and intelligent manufacturing technologies that improve precision and minimize material waste.
Conclusions for Manufacturing Leaders
As this installment of our Maximizing Profitability Mastery Series draws to a close, it’s evident that mastering waste management is more than a compliance requirement; it’s a strategic cornerstone for achieving sustainable growth and operational efficiency. The journey toward minimizing waste and maximizing efficiency is intricate, demanding a holistic approach encompassing lean manufacturing and waste minimization principles. These methodologies are not merely strategies but foundational elements that enable manufacturing entities to strive toward excellence in their operations.
By integrating these principles, manufacturers can do more than just alleviate the financial burdens associated with waste management.
They open doors to innovation, operational cost reductions, and a distinctive position in the competitive landscape—the commitment to operational efficiency and resource optimization.
A Partnership with POWERS for Transformation
In navigating the multifaceted landscape of waste management, the value of partnering with seasoned experts cannot be overstated. POWERS stands at the vanguard of guiding manufacturing firms through this transformative journey, leveraging lean manufacturing insights and waste reduction strategies to usher in a new era of operational excellence.
Our methodology is deeply ingrained in a comprehensive understanding of manufacturing sector dynamics, offering clients a partnership that transcends traditional consultancy.
Engaging with POWERS opens the gateway to a wealth of expertise and methodologies honed to streamline operations, curtail waste, and bolster profitability. Our collaborative ethos ensures that tailored strategies are conceptualized and executed in alignment with each client’s specific operational objectives.
In collaboration with POWERS, manufacturing companies can anticipate a partnership that addresses the pressing challenges of waste management and strategically positions them for enduring growth and market leadership. Our commitment to your success is unwavering, with continuous support to ensure the sustainable impact of our joint efforts.
Initiating a Legacy of Excellence and Sustainability
Partnering with POWERS signifies a transformative journey towards operational efficiency and a sustainable industrial future. Together, we will confront challenges head-on, unlocking new avenues of opportunity and securing remarkable achievements that resonate both within your organization and the broader manufacturing landscape.
This collaboration is an invitation to redefine what it means to be efficient, sustainable, and competitive in today’s manufacturing world. With POWERS by your side, the aspirations of achieving sustainable and profitable manufacturing operations transition from ambitious goals to achievable realities.
Take the first step towards revolutionizing your manufacturing processes and unlocking unprecedented operational efficiency and savings. Reach out to POWERS today to discover how our expertise can facilitate your company’s evolution towards excellence. Connect with us at +1 678-971-4711 or via email at info@thepowerscompany.com.
Continue Reading from this Mastery Series
- Part 1 - How Runaway Costs Derail Manufacturers’ Drive for Sustainability
- Part 2 - Tackling Excessive Waste Management Issues in Manufacturing
- Part 3 - Mastering Resource Efficiency in the Quest for Manufacturing Excellence
- Part 4 - The Impact of Unmitigated High Energy Costs on Manufacturers
- Part 5 - How the Complexities of Regulatory Compliance Can Erode Margins
- Part 6 - Navigating the Challenges of Reduced Market Competitiveness for Sustained Profitability
- Part 7 - Don’t Let Preferences Pull You Under
- Part 8 - Low Talent Investment is Undermining Your Bottom Line
- Part 9 - Don’t Let Supply Chain Vulnerabilities Bleed Your Profits
- Part 10 - Outsmart the Competition and Protect Your Profits