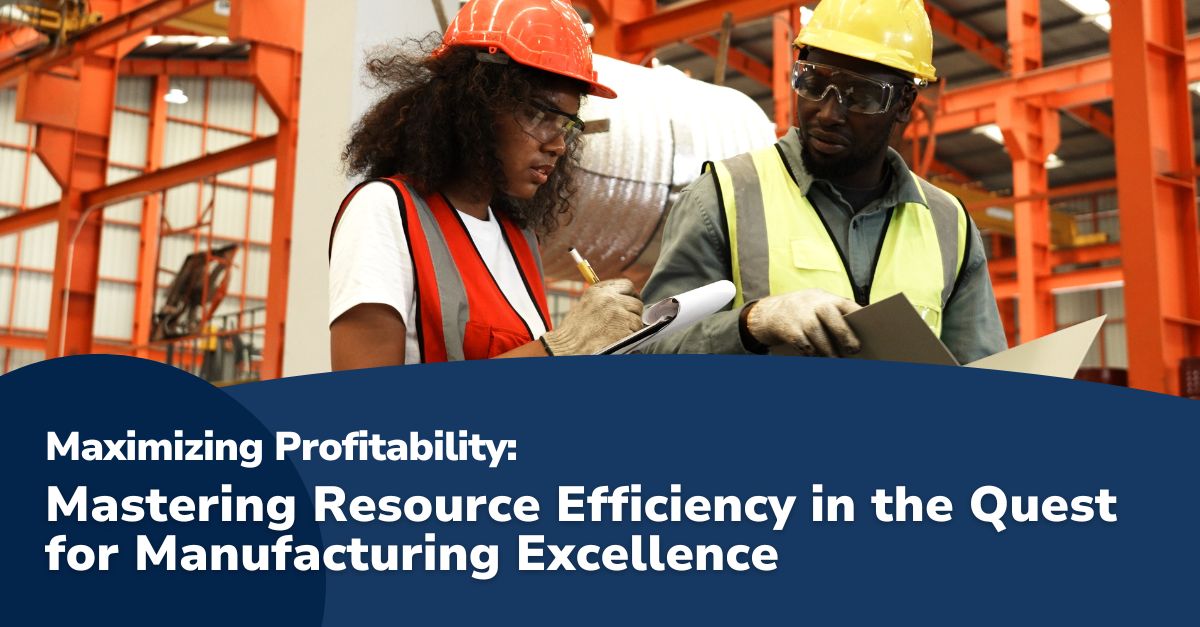
The imperative for operational efficiency and sustainable business practices has never been more pronounced in today’s rapidly evolving manufacturing landscape, where global competition is fierce, and margins are thin.
As companies strive to navigate the complexities of the modern market, the efficient utilization of resources emerges as a critical lever for achieving competitive advantage, reducing costs, and fostering sustainable growth. This pursuit, however, is fraught with challenges, as inefficiencies in resource utilization can significantly undermine a company’s operational effectiveness and long-term viability.
This third installment of the Maximizing Profitability Mastery Series delves into the heart of these challenges, uncovering the top ten ways resource utilization inefficiencies can hamper manufacturing companies.
From excessive energy consumption to underutilization of labor and machinery, these inefficiencies manifest across various dimensions, each carrying its own set of implications for operational performance and profitability.
But identifying these inefficiencies is only half the battle. The accurate measure of a company’s commitment to operational excellence lies in its ability to implement strategic solutions that address these inefficiencies head-on, transforming potential liabilities into opportunities for improvement and growth. In this context, sustainable practices respond to environmental and regulatory pressures and emerge as a strategic imperative for enhancing material efficiency, reducing waste, and improving margins.
1Excessive Energy Consumption:
Negative Impact: High energy consumption not only inflates operational costs but also raises the environmental impact of manufacturing activities, potentially compromising compliance with stringent environmental regulations and tarnishing the company’s reputation among increasingly eco-conscious consumers. It reflects inefficiencies in production processes and equipment that can significantly dent profitability.
Positive Step: Manufacturers can counteract excessive energy use by investing in energy-efficient machinery and adopting cleaner production techniques. Initiating energy audits to identify wastage hotspots and implementing renewable energy sources where feasible can further drive down energy costs. Embracing lean manufacturing principles minimizes energy wastage by streamlining operations and eliminating non-value-added activities.s offer sophisticated algorithms and data analytics capabilities to forecast demand with greater accuracy, schedule production runs optimally, and adjust operations in real time based on changing market conditions.
2Wastage of Raw Materials:
Negative Impact: Material wastage signifies direct financial loss and reflects inefficient production practices, increasing procurement and disposal costs. It strains the supply chain and exacerbates the depletion of finite resources, posing sustainability concerns that can affect the company’s license to operate in the long term.
Positive Step: Advanced planning and scheduling systems and precise demand forecasting can significantly reduce material wastage by ensuring that procurement aligns closely with production needs. Techniques like material requirements planning (MRP) and employing circular economy principles, such as recycling and reusing materials, further enhance material efficiency and sustainability.
3Underutilized Machinery and Equipment:
Negative Impact: Underutilization of machinery and equipment represents a missed opportunity for maximizing production output and efficiency. It ties up capital in assets that don’t generate proportional value, impacting the company’s financial performance and ability to invest in growth opportunities.
Positive Step: Implementing a comprehensive asset management strategy that includes regular performance assessments and leveraging IoT technology for real-time monitoring can significantly improve equipment utilization rates. This approach ensures that machinery operates at peak efficiency, identifies underperforming assets for optimization or replacement, and aligns equipment usage with production demands.
4Inefficient Labor Allocation:
Negative Impact: Inefficient labor allocation can lead to significant productivity losses and increased operational costs. It may result in overstaffing or understaffing at critical times, affecting production timelines and quality. Furthermore, it can lead to employee dissatisfaction and high turnover rates, which are costly and disruptive.
Positive Step: Adopting advanced workforce planning tools and techniques, such as skills matrix and capacity planning, ensures that the right people are in the right place at the right time. Enhancing training programs to develop multi-skilled workers can provide additional flexibility in labor allocation, allowing for rapid adjustments to changing production needs while fostering a more engaged and versatile workforce.
5Poor Supply Chain Coordination:
Negative Impact: Lack of coordination across the supply chain can lead to inefficiencies such as overstocking or stockouts, increasing holding costs, or missed sales opportunities. Poor visibility and communication between suppliers, manufacturers, and distributors exacerbate these issues, leading to inefficiencies and strained relationships.
Positive Step: Investing in integrated supply chain solutions, such as Enterprise Resource Planning (ERP) systems, enhances coordination and visibility across the supply chain. Collaborative planning, forecasting, and replenishment (CPFR) practices enable better alignment of supply and demand, reducing inventory imbalances and fostering stronger partnerships with suppliers and distributors.
6Suboptimal Production Scheduling:
Negative Impact: Inefficient production scheduling can lead to bottlenecks, idle time, and rushed work, resulting in increased costs and lower product quality. It affects the ability to meet customer deadlines, impacting customer satisfaction and potentially leading to lost business.
Positive Step: Advanced scheduling software incorporating real-time production data, capacity constraints, and customer demand can optimize production schedules, reducing bottlenecks and improving flow. Adopting flexible production systems and cross-training employees to perform multiple tasks can help address unexpected changes or disruptions, maintaining productivity and service levels.
7Overproduction and Inventory Excess:
Negative Impact: Overproduction results in excess inventory, which ties up capital that could be used more effectively elsewhere. It increases storage and handling costs and risks obsolescence, particularly for products with limited shelf lives or those subject to rapid technological advancement.
Positive Step: Implementing Just-In-Time (JIT) production and inventory management techniques aligns production closely with demand, minimizing excess inventory and associated costs. This approach requires robust demand planning and close collaboration with suppliers to ensure timely materials delivery, enhancing efficiency and reducing waste.
8Inadequate Quality Control:
Negative Impact: Poor quality control processes can lead to high levels of defects and rework, significantly increasing production costs and waste. It can damage the company’s reputation, lead to customer dissatisfaction, and result in costly recalls or legal issues.
Positive Step: Establishing a comprehensive quality management system (QMS) that integrates quality control measures throughout production can significantly reduce defects and improve product consistency. Adopting methodologies such as Six Sigma and Total Quality Management (TQM) focuses on continuous quality improvement and involves employees at all levels in quality initiatives, fostering a culture of excellence.
9Lack of Data-Driven Decision-Making:
Negative Impact: Failing to innovate and adopt new technologies can leave a company lagging behind competitors, reducing its market share and profitability. It may take advantage of opportunities to improve efficiency, lower costs, and meet evolving customer demands.
Positive Step: Creating a culture of innovation where new ideas and technologies are actively explored and integrated into the business can keep a company at the forefront of its industry. Investing in research and development, partnering with technology providers, and engaging in industry consortia can accelerate technology adoption and drive continuous improvement.
10Ineffective Communication and Collaboration:
Negative Impact: In the modern manufacturing landscape, decisions based on intuition rather than data can lead to suboptimal operational performance and missed opportunities for efficiency gains. Without leveraging accurate, real-time data, manufacturers may struggle to identify inefficiencies, predict maintenance needs, or optimize production processes, resulting in increased costs and decreased productivity.
Positive Step: Implementing a robust data analytics infrastructure can transform decision-making processes, enabling manufacturers to make informed, strategic choices. Utilizing Internet of Things (IoT) devices and sensors to collect real-time operational data and advanced analytics platforms can provide insights into every aspect of the manufacturing process.
Conclusion for Manufacturing Leaders
In embracing the strategies outlined above, manufacturing companies not only navigate the pitfalls of resource utilization inefficiencies but also embark on a journey toward operational excellence and sustainable growth. This commitment to continuous improvement and innovation is not just about mitigating risks; it’s about seizing opportunities to redefine industry standards, enhance competitive advantage, and deliver value beyond the bottom line to encompass environmental stewardship and social responsibility.
As we’ve explored these ten areas, it’s clear that the path to overcoming resource utilization inefficiencies is multifaceted, requiring a holistic approach that integrates advanced technology, strategic planning, and a culture of excellence.
By adopting these principles, manufacturers can ensure they are prepared to meet today’s challenges and poised to capitalize on tomorrow’s opportunities.
Partnering with POWERS
At POWERS, we understand that the path to operational excellence and sustainability is complex and highly individualized. Our approach is rooted in a deep understanding of our client’sclients’ unique challenges and opportunities. By partnering with POWERS, manufacturers can access
- Customized Strategies: Tailored solutions that address specific inefficiencies, operational challenges, and long-term goals.
- Expert Guidance: A team of industry experts with a proven track record of driving significant improvements in operational efficiency, cost reduction, and sustainable practices.
- Continuous Improvement: A focus on implementing solutions and cultivating a culture of constant improvement and innovation within client organizations.
- Sustainable Results: Strategies that balance short-term gains with long-term sustainability ensure that improvements are achieved and maintained over time.
Working with POWERS is more than a consultancy engagement; it’s a partnership to achieve transformative growth and build a lasting competitive advantage. Our commitment to operational excellence and a deep focus on sustainable manufacturing practices positions our clients to meet today’s challenges and lead the industry into the future.
Forge Your Path with POWERS
As we conclude this Maximizing Profitability Mastery Series installment, we invite you to consider the strategic value a partnership with POWERS can bring to your manufacturing operations. Whether addressing specific inefficiencies, enhancing overall operational excellence, or integrating sustainability into the core of your business, POWERS is here to guide and support your journey.
Open the gateway to superior resource efficiency and cost reduction with POWERS. Begin your journey towards unparalleled operational excellence today. For an in-depth conversation about how we can support your enterprise, contact our experts at +1 678-971-4711 or email info@thepowerscompany.com.
Continue Reading from this Mastery Series
- Part 1 - How Runaway Costs Derail Manufacturers’ Drive for Sustainability
- Part 2 - Tackling Excessive Waste Management Issues in Manufacturing
- Part 3 - Mastering Resource Efficiency in the Quest for Manufacturing Excellence
- Part 4 - The Impact of Unmitigated High Energy Costs on Manufacturers
- Part 5 - How the Complexities of Regulatory Compliance Can Erode Margins
- Part 6 - Navigating the Challenges of Reduced Market Competitiveness for Sustained Profitability
- Part 7 - Don’t Let Preferences Pull You Under
- Part 8 - Low Talent Investment is Undermining Your Bottom Line
- Part 9 - Don’t Let Supply Chain Vulnerabilities Bleed Your Profits
- Part 10 - Outsmart the Competition and Protect Your Profits