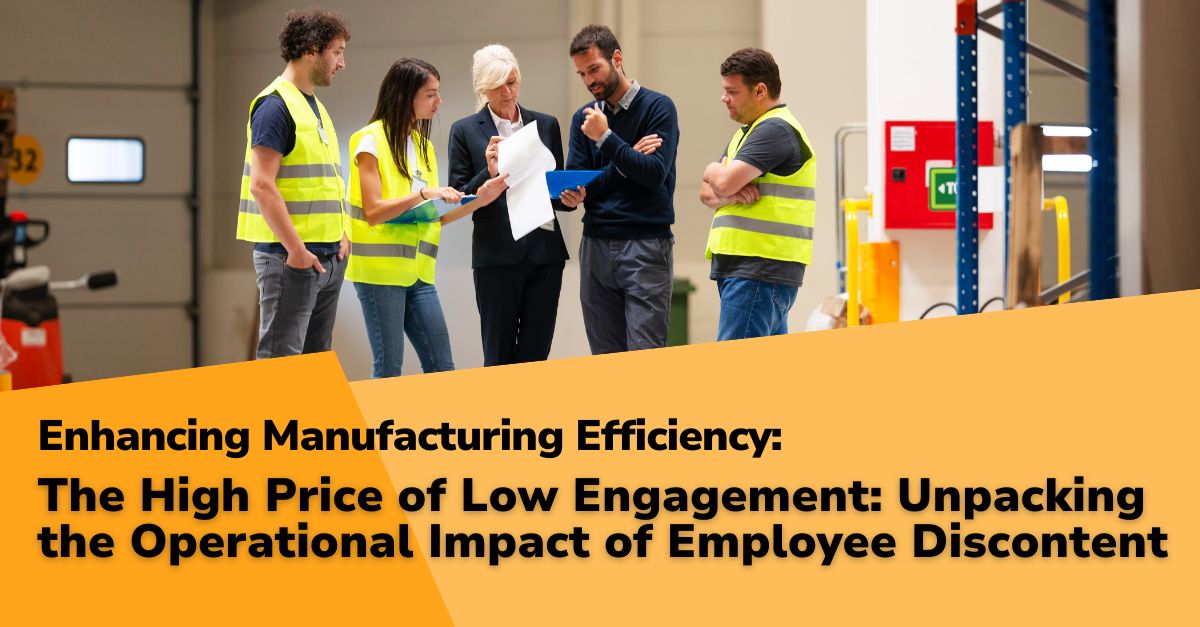
The effectiveness of a Management Operating System (MOS) can be gauged by its ability to inspire and maintain high levels of engagement among its workforce. Low engagement and morale are productivity sink holes, draining valuable resources, and cutting deeply into the bottom line.
In this seventh edition, we delve into how low employee engagement and morale manifest as operational challenges throughout the manufacturing enterprise. Ultimately, performance takes a nosedive.
From direct impacts like decreased productivity and quality compromises to more indirect effects such as resistance to change and innovation stagnation, understanding these dynamics is crucial for manufacturing leaders aiming to foster robust, efficient, and responsive operations.
Based on our experience and analysis, these are the top 10 performance-draining issues caused by low engagement and morale in the workforce.
1Decreased Productivity:
Low morale often leads to diminished employee motivation and decreased productivity. For instance, Gallup’s State of the Global Workplace report highlights that disengaged workers have 37% higher absenteeism and 18% lower productivity. This lack of engagement leads to slower production rates and operational inefficiencies.
2Quality Compromises:
Disengagement can reduce attention to detail, increase manufacturing defects, and decrease product quality. Studies indicate that companies with high employee engagement scores experience 40% fewer quality defects.
3Increased Absenteeism:
Disengaged employees are more likely to take unplanned leaves, disrupting production schedules. According to the Bureau of Labor Statistics, the average absentee rate in manufacturing sectors is around 2.9%, with disengagement being a significant contributor.
4Higher Turnover Rates:
Low morale drives employee turnover. The cost of replacing an employee can range from one-half to two times the employee’s annual salary, not to mention the loss of institutional knowledge and expertise.
5Poor Team Dynamics:
Employee disengagement affects team collaboration and communication. The Harvard Business Review highlights that good team dynamics can increase performance by over 30%, indicating the negative impact poor dynamics can have.
6Safety Risks:
Engaged employees are more vigilant about safety protocols. Industry studies report that disengaged employees have a 49% higher accident rate, leading to increased safety incidents and associated costs.
7Inefficient Resource Utilization:
Disengaged employees may not use resources efficiently, increasing waste and operational costs. Studies show that companies with engaged employees see 21% higher profitability, partly due to more efficient resource utilization.
8Resistance to Change:
Disengaged employees often resist new processes and technologies, slowing implementation and adaptation. This resistance can be a significant obstacle in keeping pace with market demands and technological advancements.
9Reduced Creativity and Innovation:
Engaged employees contribute more ideas for improvement. Adobe’s State of Create report reveals that companies encouraging creativity enjoy 1.5 times higher market share due to innovation driven by engaged employees.
10Impact on Leadership Credibility:
Persistent low morale can erode trust in leadership, making it challenging to implement strategic initiatives and drive operational improvements. Effective leadership fosters a positive work environment and maintains high employee engagement.
Conclusions for Manufacturing Operations Leaders
As we unravel the complexities of employee engagement in manufacturing settings, it becomes increasingly clear that the health of an organization’s human element is as critical as its mechanical counterparts.
The ripple effects of low engagement, or complete disengagement, reach far beyond individual performance, permeating the very core of operational efficiency and effectiveness.
For manufacturing leaders, the path forward involves recognizing the multifaceted impacts of low employee morale and actively developing strategies to enhance engagement.
By doing so, they can cultivate an environment where both employees and operations thrive, leading to improved productivity, innovation, and competitive edge.
Maximize Engagement and Performance with POWERS
At POWERS, we adeptly handle the challenges of refining systems, processes, and behaviors in today’s complex manufacturing environments.
Our approach, rooted in extensive real-world experience, focuses on enhancing Management Operating Systems with solutions that effectively boost employee engagement and operational results.
- Customized Engagement Solutions: We tailor our strategies to meet each manufacturing operation's unique needs, ensuring practical and sustainable MOS solutions that improve employee engagement.
- Data-Informed Engagement Strategies: Leveraging advanced data analytics, POWERS provides insightful, actionable strategies that transform data into a strategic asset, particularly for enhancing employee involvement.
- Holistic Methodology: Our approach encompasses more than MOS technicalities. We stress the human element, prioritizing leadership development, employee engagement, and a culture of ongoing improvement.
- Sustained Performance and Engagement: We aim to equip clients with enduring solutions that enhance operations and maintain high employee engagement, delivering lasting value.
- Expertise in Operational Efficiency: Our team's extensive experience and success in manufacturing efficiency focus on practical strategies that simultaneously boost employee engagement and performance.
With POWERS, manufacturers can navigate industry complexities more effectively, enhancing both efficiency and profitability while creating a positive, adaptable work environment.
Begin your path to superior efficiency, quality, and employee engagement with POWERS. Contact our expert team at +1 678-971-4711 or via email at info@thepowerscompany.com.
Continue Reading from this Mastery Series
- Part 1 - Identifying Key Inefficiencies in the Absence of a Management Operating System
- Part 2 - Top 10 Pitfalls: Lack of an MOS Derails Productivity
- Part 3 - Top 10 Quality Issues at Risk Without a Robust Management Operating System
- Part 4 - The High Cost of an Ineffective Management Operating System
- Part 5 - Without an Optimized Management Operating System, Decision-Making is Severely Impaired
- Part 6 - Scaling Challenges of an Inadequate Management Operating System
- Part 7 - The High Price of Low Engagement: Unpacking the Operational Impact of Employee Discontent
- Part 8 - Safeguarding Success: Decoding the Impact of Compliance and Safety Issues
- Part 9 - Examining the Cost of a Slow Response to Market Shifts
- Part 10 - Charting Success: Understanding the Costs of Losing Competitive Advantage