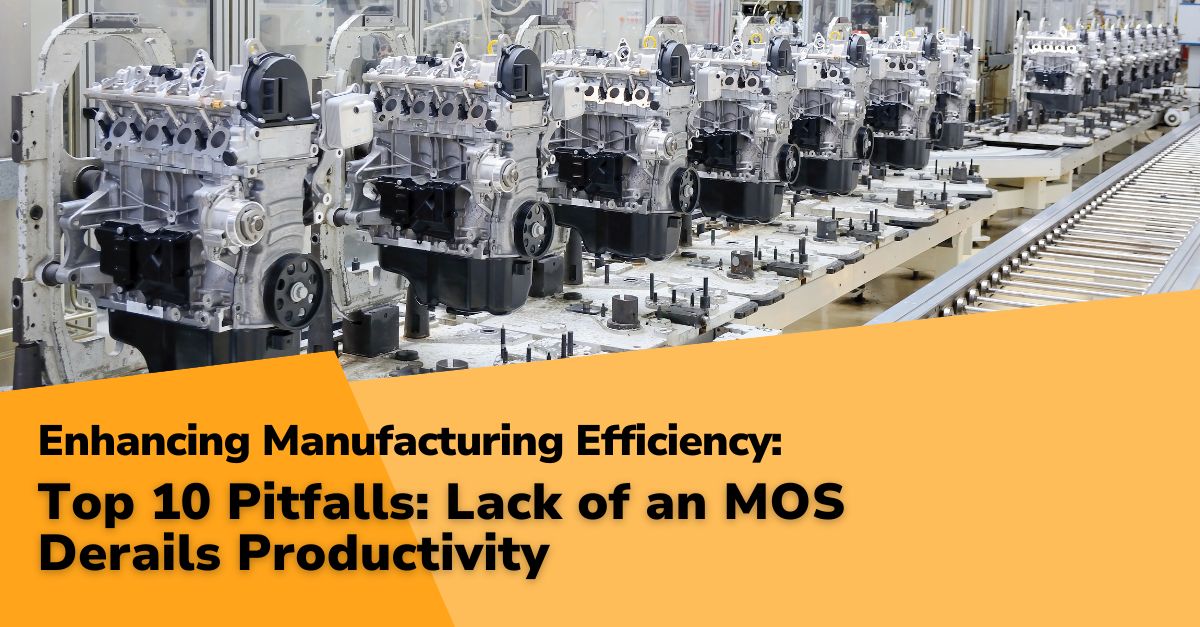
In the complex and dynamic world of manufacturing, an absent or poorly implemented MOS can lead to significant productivity pitfalls, often unnoticed until they manifest as major operational challenges.
A fully optimized Management Operating System is the backbone of manufacturing processes, providing the necessary structure and guidance to navigate the intricate landscape of production, resource allocation, and workforce management. Without it, companies risk falling into detrimental traps that can severely hinder their operational effectiveness and bottom line.
These pitfalls vary in nature but commonly stem from systemic issues such as unclear roles and responsibilities, inefficient resource allocation, and poor communication channels.
The consequences are far-reaching, impacting everything from day-to-day operations to long-term strategic planning.
The absence of a well-structured MOS can lead to a reactive rather than proactive management style, where decisions are made in response to immediate problems rather than being part of a well-thought-out strategy. This often results in a perpetual cycle of firefighting, where short-term solutions are applied to long-term problems, further exacerbating inefficiencies.
In the following sections, we will explore the top 10 productivity pitfalls we’ve found that are caused by the absence or poor implementation of an MOS, providing insights into how each issue arises and its impact on the manufacturing process.
1Unclear Roles and Responsibilities:
Without a Management Operating System, there’s a significant lack of clarity regarding roles and responsibilities. This ambiguity can make employees uncertain about their specific tasks and goals, decreasing productivity. The confusion can also lead to duplication of efforts or critical tasks being overlooked, as employees are unsure of their accountability, which can further delay project timelines and disrupt workflow.
2Inefficient Resource Allocation:
An effective MOS facilitates the optimal allocation of resources, including staffing, machinery, and materials. Without it, there’s a risk of misallocation, leading to resource wastage or shortages at critical times. This inefficiency not only impacts current projects but also affects the organization’s ability to plan and execute future projects effectively, potentially leading to increased costs and reduced competitiveness.
3Poor Communication and Coordination:
A structured MOS ensures streamlined communication and coordination across various departments. In its absence, information silos can develop, obstructing the flow of vital information. This communication breakdown can cause delays in decision-making and misaligning team efforts, which can even lead to critical errors in operations, directly impacting productivity.
4Inadequate Performance Tracking:
Monitoring and managing performance is a critical component of an MOS. Without it, tracking progress, identifying improvement areas, or recognizing and replicating successful strategies becomes challenging. This lack of oversight can lead to repeated mistakes, unaddressed inefficiencies, and missed opportunities for optimization, all detrimental to productivity.
5Delayed Decision Making:
In manufacturing, the speed and accuracy of decision-making are crucial. An MOS provides a framework for making quick, data-driven decisions. Its absence leads to prolonged decision-making processes, negatively impacting production timelines and the organization’s ability to swiftly respond to market changes and opportunities.
6Limited Continuous Improvement Initiatives:
Continuous improvement is vital in maintaining competitiveness. Without an MOS, structured initiatives for continuous improvement are more challenging to implement and sustain. This stagnation affects current productivity and hampers the organization’s ability to innovate and stay ahead in an evolving industry.
7Ineffective Problem-Solving:
Without a structured MOS, problem-solving efficiency is significantly reduced. This can lead to prolonged downtime and reduced output, as issues are not addressed systematically. Moreover, without an MOS, organizations often lack the necessary tools to perform root cause analysis, leading to repetitive problems and inefficiencies.
8Low Employee Engagement and Morale:
An MOS typically includes elements that enhance employee engagement and morale by providing clear expectations and recognizing achievements. Without it, employees may feel directionless and undervalued, leading to decreased motivation and productivity and higher turnover rates.
9Suboptimal Scheduling and Planning:
Effective scheduling and planning are crucial for maintaining productivity. Without an MOS, these processes become haphazard, leading to production bottlenecks, underutilization of capacity, and missed deadlines, which lower overall productivity and negatively impact customer satisfaction and business reputation.
10Hindered Innovation and Adaptability:
Innovation and adaptability are key drivers of long-term success in manufacturing. Without an effective Management Operating System, organizations often struggle to foster an environment where innovative ideas and adaptive strategies can thrive. This limitation affects current productivity levels and impedes the company’s ability to evolve with changing market demands and technological advancements. The absence of a structured system for capturing and implementing innovative ideas results in missed opportunities for process improvements and technological integrations, ultimately leading to stagnation in a highly competitive industry.
Conclusions for Manufacturing Operations Leaders
The critical role of a Management Operating System in manufacturing cannot be overstated. As we have explored in detail, the absence of such a system can precipitate a cascade of inefficiencies and productivity challenges that can have far-reaching impacts on a manufacturing organization’s operations and its bottom line.
From the misalignment of roles and responsibilities to the stunted potential for innovation and adaptability, each aspect of these top 10 issues reveals a facet of operational vulnerability that can hinder a company’s growth and competitiveness in the market.
Understanding these pitfalls is more than an exercise in identifying operational weaknesses; it’s about recognizing the significant potential that a well-implemented and optimized MOS holds for transforming manufacturing processes.
An effective MOS acts as a framework for efficiency and a catalyst for continuous improvement, innovation, and strategic agility. It enables organizations to harness data-driven insights for informed decision-making, fosters a culture of accountability and engagement among employees, and streamlines processes to maximize resource utilization.
The POWERS Difference
At POWERS, we understand a Management Operating System’s critical role in driving manufacturing productivity. Our approach is distinct in several key ways:
1Customized Solutions:
We recognize that every manufacturing environment is unique. POWERS tailors its MOS solutions to meet each client’s needs and challenges, ensuring maximum impact and sustainability.
2Holistic Integration
Our strategy goes beyond the mere implementation of an MOS. We integrate it with your organization’s culture and processes, ensuring it complements and enhances existing operations.
3Focus on People and Process:
At POWERS, we believe true efficiency comes from the synergy of people and processes. Our MOS implementation emphasizes employee engagement and process optimization, driving both productivity and morale.
4Data-Driven Insights:
Leveraging the latest in data analytics, we provide insightful, actionable intelligence that forms the backbone of our MOS strategies. This ensures that decisions are informed, timely, and effective.
5Sustainable Change:
Our goal is not just to implement an MOS but to instill a culture of continuous improvement. We provide tools and training that empower your team to maintain and evolve the MOS long after our engagement ends.
6Proven Track Record:
With years of experience and a portfolio of successful MOS implementations, POWERS has demonstrated its capability to enhance productivity in a variety of manufacturing contexts, setting us apart from competitors.
For manufacturers determined to excel, optimizing an MOS is not just a strategy but a transformational tool that can redefine your business trajectory. The POWERS team is primed to facilitate this transformation, equipping you with the tools to thrive.
Embrace the full potential of a robust Management Operating System with POWERS. Begin your journey toward operational excellence today. Connect with our experts at +1 678-971-4711 or reach out via email to info@thepowerscompany.com.
Continue Reading from this Mastery Series
- Part 1 - Identifying Key Inefficiencies in the Absence of a Management Operating System
- Part 2 - Top 10 Pitfalls: Lack of an MOS Derails Productivity
- Part 3 - Top 10 Quality Issues at Risk Without a Robust Management Operating System
- Part 4 - The High Cost of an Ineffective Management Operating System
- Part 5 - Without an Optimized Management Operating System, Decision-Making is Severely Impaired
- Part 6 - Scaling Challenges of an Inadequate Management Operating System
- Part 7 - The High Price of Low Engagement: Unpacking the Operational Impact of Employee Discontent
- Part 8 - Safeguarding Success: Decoding the Impact of Compliance and Safety Issues
- Part 9 - Examining the Cost of a Slow Response to Market Shifts
- Part 10 - Charting Success: Understanding the Costs of Losing Competitive Advantage