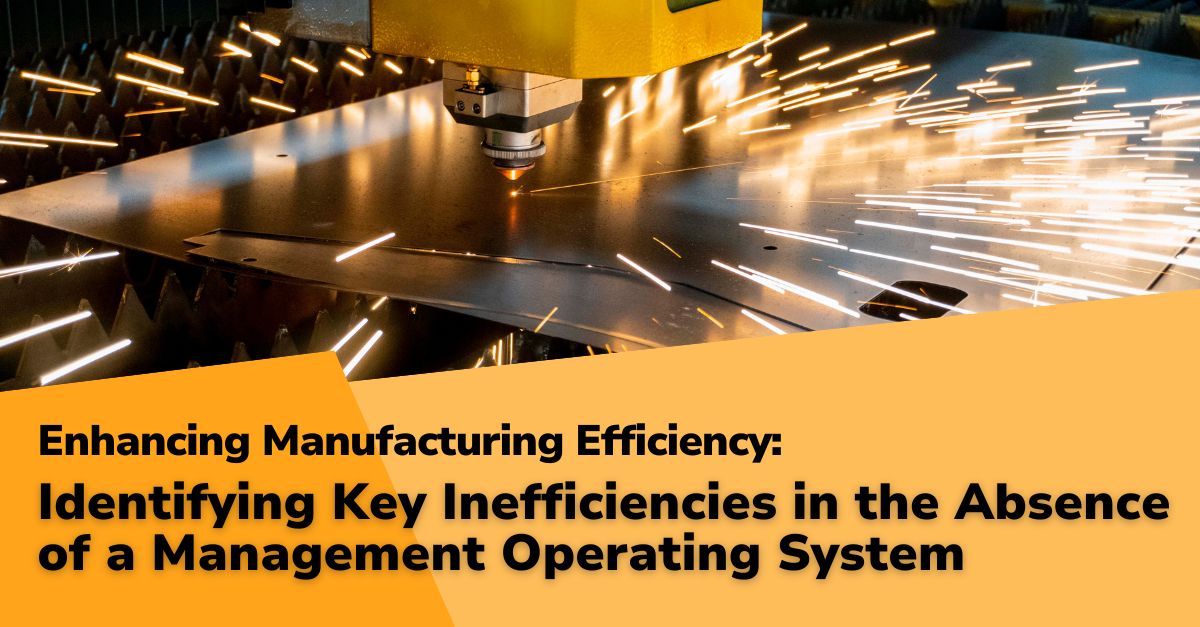
The importance of an effective Management Operating System (MOS) in manufacturing cannot be overstated. As the first installment in our 10-part Mastery Series’ Enhancing Manufacturing Efficiency,’ we delve into the critical inefficiencies that can plague manufacturing operations without a well-implemented MOS.
This series aims to highlight the pivotal role of a fully implemented and optimized MOS in driving operational excellence and sustaining competitive advantage in the manufacturing sector.
Our exploration begins with examining the tangible and often critical inefficiencies that emerge without an MOS. These issues impede the smooth functioning of manufacturing processes and have far-reaching implications for an organization’s overall health and profitability.
By identifying these specific inefficiencies, we lay the groundwork for understanding the indispensable value of an MOS and set the stage for subsequent discussions on practical solutions and best practices in the upcoming parts of this series.
10 Critical Inefficiencies Emerge Without an MOS
1Bottlenecks and Slowdowns:
Without a standardized MOS, manufacturers often face bottlenecks and slowdowns due to a lack of standardized processes, leading to inefficiencies in production and inconsistent performance and output levels.
2Delayed Procurement:
In the absence of an MOS, delays in procurement processes can disrupt production schedules, increasing costs and decreasing customer satisfaction.
3Unpredictable Inventory Management:
Without an MOS, inventory management can become unpredictable. Excessive inventory ties up capital and increases storage costs, while insufficient inventory leads to production delays and missed sales opportunities.
4Shipping and Supply Chain Disruptions:
Manufacturers lacking an MOS often struggle with shipping delays, part shortages, and transportation delays, affecting supply chains and leading to increased shipping costs.
5Equipment Breakdowns:
The absence of an efficient MOS can lead to more frequent equipment breakdowns, causing unplanned maintenance or repairs and resulting in costly production delays.
6Inefficient Workflow Management:
Lack of an MOS often results in poor communication, lack of standardized processes, and inadequate resource allocation, contributing to production bottlenecks and hindering operational efficiency.
7Lack of Employee Training:
An MOS typically includes regular training programs. Without it, workers may not receive necessary ongoing training, leading to inefficiencies and errors in the manufacturing process.
8Unclear Communication:
In the absence of an MOS, there can be a lack of clear communication regarding deadlines and tasks, leading to inefficiencies and delays in manufacturing operations.
9Faulty Equipment Maintenance:
Without a proper MOS, maintaining manufacturing machinery and its components, like electric motors, can be neglected, increasing the likelihood of equipment failure and associated downtime.
10Inefficient Labor Allocation:
An MOS helps effectively schedule labor, minimize unnecessary overtime, and manage staff shortages. The lack of an MOS can lead to poor scheduling, excessive overtime, and inadequate staffing, all of which contribute to inefficiencies in the manufacturing process.
Addressing these specific inefficiencies requires a well-implemented MOS, which can streamline processes, improve communication, ensure quality, and ultimately enhance overall operational efficiency in manufacturing.
Conclusions for Manufacturing Operations Leaders
The lack of a Management Operating System introduces a spectrum of inefficiencies in manufacturing operations, ranging from production bottlenecks to ineffective labor allocation.
These inefficiencies not only compromise the operational capabilities of a manufacturing unit but also significantly impact its financial and competitive standing in the market.
Recognizing these inefficiencies is the first step towards transforming operational challenges into opportunities for growth and improvement.
Stay tuned for the upcoming segments of this series, where we will dive deeper into the consequences of an absent or poorly implemented MOS, exploring their root causes and presenting actionable strategies to address them.
Our journey through ‘Enhancing Manufacturing Efficiency’ is designed to empower manufacturers with the insights and tools necessary for optimizing their operations, leveraging the full potential of a Management Operating System, and ultimately achieving manufacturing excellence.
Join us as we continue to unravel the complexities of manufacturing efficiency and pave the way for a more productive, profitable, and sustainable future in the manufacturing industry.
The POWERS Difference
Our approach to manufacturing productivity focuses on the critical role of a Management Operating System (MOS) in achieving manufacturing superiority.
Implementing an MOS will harmonize your people, processes, and performance, aligning your entire organization with strategic objectives.
If you have an MOS in place but need it to be more utilized or is out of compliance, we can optimize it.
Streamlining operations through an MOS optimized for your company will empower your team for unparalleled efficiency and significant cost savings.
For manufacturers aiming to lead the market, an optimized MOS is not merely a strategy but a game-changer in reshaping your business. The POWERS team is ready to guide this pivotal shift, providing the tools needed to excel in the competitive manufacturing arena.
Unlock the full potential of a comprehensive MOS with POWERS. Start your path to operational excellence now. Contact our specialists at +1 678-971-4711 or email us at info@thepowerscompany.com.
Continue Reading from this Mastery Series
- Part 1 - Identifying Key Inefficiencies in the Absence of a Management Operating System
- Part 2 - Top 10 Pitfalls: Lack of an MOS Derails Productivity
- Part 3 - Top 10 Quality Issues at Risk Without a Robust Management Operating System
- Part 4 - The High Cost of an Ineffective Management Operating System
- Part 5 - Without an Optimized Management Operating System, Decision-Making is Severely Impaired
- Part 6 - Scaling Challenges of an Inadequate Management Operating System
- Part 7 - The High Price of Low Engagement: Unpacking the Operational Impact of Employee Discontent
- Part 8 - Safeguarding Success: Decoding the Impact of Compliance and Safety Issues
- Part 9 - Examining the Cost of a Slow Response to Market Shifts
- Part 10 - Charting Success: Understanding the Costs of Losing Competitive Advantage