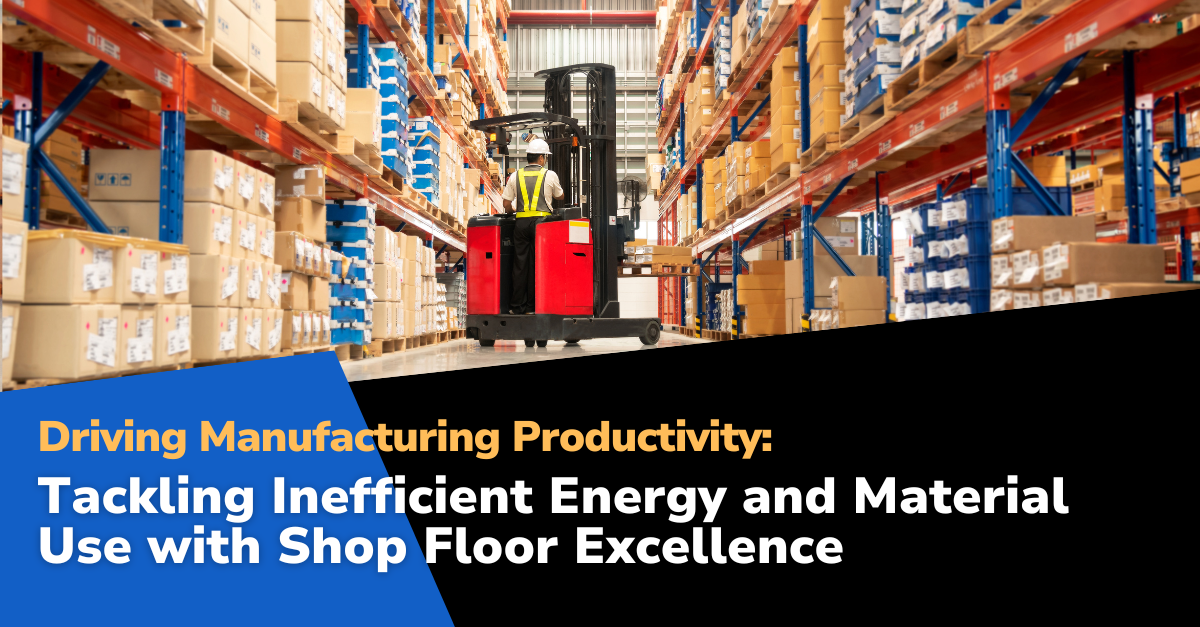
In the contemporary manufacturing landscape, inefficient energy and material use is a profit killer. Increasing resource management up and down the value chain is integral to Shop floor Excellence and a critical factor in achieving sustainable operations and maintaining competitive advantage.
However, when Shop Floor Excellence (SFE) principles are overlooked, manufacturers often grapple with inefficient energy and material use. This increases operational costs and adds to the environmental footprint, a growing concern in today’s eco-conscious market.
In this ninth entry of our ten-part series, we delve into the top 10 challenges of inefficient energy and material usage in manufacturing settings devoid of SFE principles. More importantly, we explore how adopting SFE strategies can turn these challenges into opportunities for efficiency and sustainability. This blog aims to shed light on the pivotal role of SFE in promoting economic efficiency and environmental responsibility in manufacturing operations.
1Excessive Energy Consumption:
Facilities often consume more energy than necessary due to outdated equipment, poor insulation, or inefficient operations.
Solution: Conduct energy audits to identify areas of high consumption. Upgrade to energy-efficient machinery, improve facility insulation, and optimize machine operation schedules.
2Material Wastage:
Overproduction, defects, and inefficient processes can result in significant material wastage, impacting costs and sustainability.
Solution: Implement lean practices like Kaizen and 5S to streamline production, reduce defects, and minimize overproduction, reducing material wastage.
3Underutilized Resources:
Machinery and human resources are often not used to their full potential, leading to inefficiencies.
Solution: Analyze production data to optimize machine usage and workforce scheduling, ensuring that resources are utilized effectively and reducing idle time.
4High Operational Costs:
Inefficient energy and material usage inflate operational costs, affecting profitability.
Solution: Adopt waste reduction strategies and consider alternative, cost-effective materials. Regularly review and adjust operational processes to enhance efficiency.
5Poor Process Optimization:
Existing processes may be outdated or not optimized for current operations, leading to increased consumption of energy and materials.
Solution: Regularly review and refine manufacturing processes using Six Sigma methodologies to ensure they are as efficient as possible.
6Lack of Sustainable Practices:
Neglecting sustainable practices can harm the environment and potentially lead to regulatory issues.
Solution: Integrate eco-friendly practices such as recycling, using renewable energy sources, and adopting biodegradable or recycled materials in production.
7Ineffective Inventory Management:
Poor inventory management can lead to excess stock, risks obsolescence, and wastage.
8Inadequate Employee Training:
Employees may not know the best practices for conserving energy and materials.
Solution: Provide regular training sessions on energy conservation and efficient material usage. Encourage employee suggestions for improving efficiency.
9Lack of Process Automation:
Manual processes are often less efficient than automated alternatives, leading to higher energy and material usage.
Solution: Evaluate processes for potential automation. Invest in automated assembly lines or robotics technologies to enhance efficiency and accuracy.
10Inefficient Facility Layout:
A facility layout that causes unnecessary movement can increase energy usage and time wastage.
Solution: Redesign the facility layout to streamline workflow, using lean manufacturing principles to minimize movement and enhance efficiency.
By addressing these challenges with strategic SFE solutions, manufacturers can significantly reduce their energy and material usage, leading to more sustainable operations and reduced costs.
Enhancing Efficiency with the POWERS Approach
At POWERS, we understand the importance of efficient energy and material usage in manufacturing.
Our approach integrates the principles of SFE to help manufacturers overcome inefficiencies, promoting sustainable practices and cost-effectiveness.
Transform your approach to energy and material usage with POWERS. Our team is ready to guide you in implementing SFE solutions that ensure efficient, sustainable, and cost-effective manufacturing operations.
Contact us at +1 678-971-4711 or info@thepowerscompany.com for a comprehensive solution that aligns your manufacturing processes with the highest efficiency and sustainability standards. Let’s work together to drive your manufacturing productivity to new heights.
Continue Reading from this Mastery Series
- Part 1 - The Perils of Overlooking SFE in Assembly Line Setup
- Part 2 - A Lackluster Approach to Shop Floor Excellence Impacts Workforce Engagement
- Part 3 - The Consequences of Sidestepping Data-Driven Decisions in Shop Floor Excellence
- Part 4 - Without Shop Floor Excellence, Product Quality Can Drop Like a Rock
- Part 5 - A Lack of Commitment to Shop Floor Excellence Can Lead to These 10 Safety Issues
- Part 6 - Shop Floor Excellence Makes Your Operation More Agile, Flexible, and Adaptable to Market Changes
- Part 7 - Bridging the Gap with Effective Communication in Shop Floor Excellence
- Part 8 - How Ignoring Shop Floor Excellence Undermines Continuous Improvement
- Part 9 - Tackling Inefficient Energy and Material Use with Shop Floor Excellence
- Part 10 - Enhancing Customer Focus Through Shop Floor Excellence