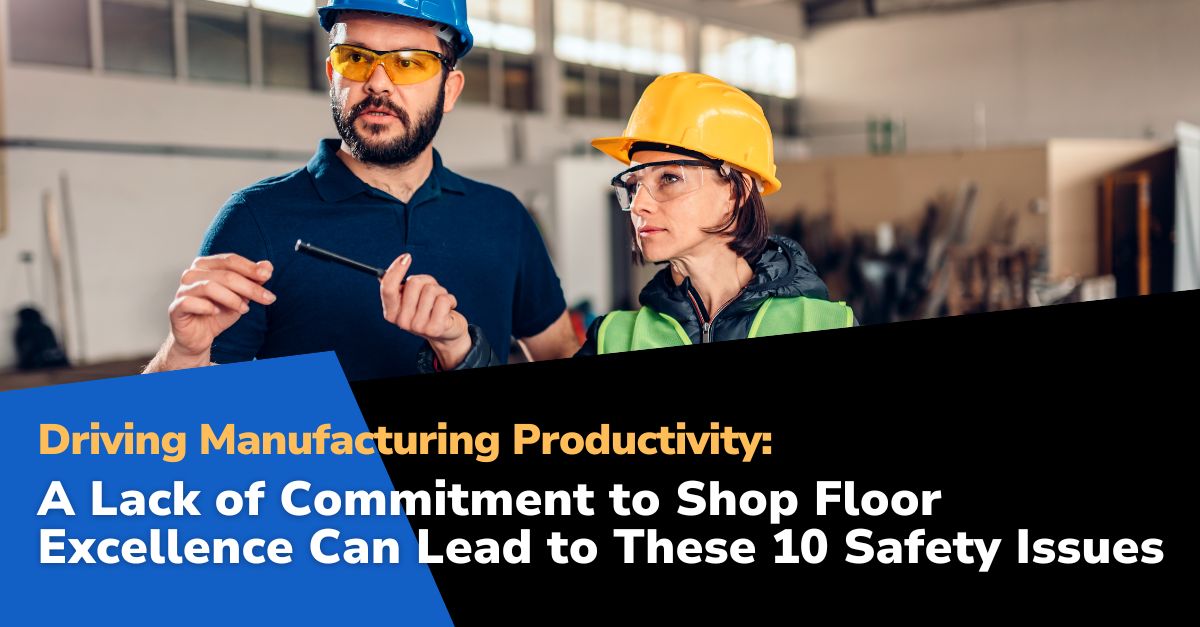
Safety in manufacturing is not just a compliance requirement; it’s a baseline for operational excellence.
The moment safety becomes a secondary concern, the shop floor becomes a liability. Whether it’s a near-miss that goes unreported or a shortcut taken to save five minutes, the cost shows up somewhere often in ways that leadership doesn’t see until it’s too late.
The shop floor is a dynamic environment: machines in motion, materials in transit, and people constantly adapting to change. Without a structured, proactive approach to safety, those moving parts can collide literally and figuratively. The result? Injuries, downtime, rework, regulatory trouble, and an erosion of trust that drags down morale and performance.
This fifth installment of our ten-part Shop Floor Excellence (SFE) series looks closely at 10 of the most common and most damaging safety failures we see when SFE is missing. These aren’t just isolated issues; they’re indicators of broader system breakdowns.
Let’s examine how these risks take shape on the floor and how embedding safety into your SFE framework can reverse the trend and restore control.
1Increased Accident Rates:
When safety protocols are weak or inconsistently followed, the data speaks for itself: injuries rise, insurance premiums increase, and employees begin to view management as disengaged. The most common causes? Rushed startups, skipped checklists, and a lack of consequence for ignoring rules.
Solution: Build routine hazard assessments into your daily operations—don’t wait for an incident. Layer in hands-on safety refreshers during shift changes and reinforce expectations with visible leadership presence on the floor. A clean-as-you-go policy is powerful when modeled consistently.
2Equipment-Related Injuries:
From pinch points to jammed sensors, equipment-related incidents are often a symptom of rushed maintenance, inadequate inspections, or lack of training. Untrained workers improvising around unsafe equipment are one mistake away from permanent injury.
Solution: Conduct frequent safety audits that include guard presence, interlock testing, and emergency stop drills. Document issues and tie corrective actions to work orders. Build safety reviews into preventive maintenance, not just reactive fixes. Every operator should be able to explain how to stop their machine safely.
3Hazardous Material Incidents:
Handling chemicals or flammable materials without clear procedures is a recipe for disaster. Whether it’s a mislabeled drum, blocked eye wash station, or expired SDS sheet, one oversight can become a crisis.
Solution: Go beyond compliance training. Build simulations into onboarding and annual refreshers. Use visual controls to label, isolate, and contain materials. PPE must be available at the point of use, and ventilation systems should be tested, not assumed to be working.
4Ergonomic Injuries:
Muscle strain, tendonitis, and back injuries rarely happen in a single moment, they build over weeks or months from poor ergonomics and excessive repetition. And when they do take someone offline, they often take years of experience with them.
Solution: Evaluate workstation layout regularly, especially after production changes. Involve employees in identifying pain points. Introduce lift-assist devices, anti-fatigue mats, and adjustable fixtures where possible. Pair these improvements with job rotation and recovery breaks that prevent overuse.
5Fire and Electrical Hazards:
It only takes one frayed extension cord or blocked electrical panel to spark a major event. Yet these issues are easy to overlook during a hectic shift, until they’re not.
Solution: Assign specific team members to inspect fire and electrical risks weekly. Require documented lockout/tagout procedures before maintenance. Flammable storage must meet code, and that includes lid closures, venting, and grounding. Create a zero-tolerance policy for unapproved electrical workarounds.
6Slips, Trips, and Falls:
Slips and trips remain one of the top causes of OSHA-recordable injuries, yet they’re often dismissed as minor or “common sense.” This mindset leads to cluttered aisles, slippery floors, and unsecured hoses or cords in high-traffic areas.
Solution: Standardize housekeeping expectations. Include a 5-minute floor check at shift change. Install mirrors at blind corners and ensure floor markings are clearly visible. Elevate spill response from reactionary to routine, every team should know who owns the mop and when.
7Inadequate Emergency Response:
Even when you’ve done everything right, things can still go wrong. The key is how quickly and effectively your team reacts. A well-practiced response minimizes harm and gets production back online faster. An uncoordinated one can magnify the damage and paralyze decision-making.
Solution: Treat drills like live events. Rotate roles so that everyone can step up when needed. Post key phone numbers, floor maps, and response roles in breakrooms and next to operator stations. Build emergency response review into your post-incident debriefs and continuous improvement cycles.
8Poor Safety Communication:
If frontline workers don’t know the latest safety updates, or feel uncomfortable raising concerns, unsafe conditions can persist unnoticed. Silence isn’t safety.
Solution: Integrate safety messaging into morning huddles and production meetings. Create anonymous channels for reporting issues and ensure every report is acknowledged. Use bulletin boards and digital displays to communicate recent incidents, near misses, and reminders in real time.
9Lack of Personal Protective Equipment (PPE):
Even well-intentioned teams fall short when PPE is hard to find, uncomfortable, or seen as optional. Repeated violations erode accountability and signal that rules are flexible depending on output targets.
Solution: Make PPE selection role-specific and user-informed. Involve workers in fit testing and material selection. Don’t just stock PPE, inspect it, track usage trends, and reinforce policies through direct coaching, not just signage.
10Compliance Issues:
When safety programs exist only on paper, you invite regulatory risk. OSHA citations and insurance audits don’t just cost money, they expose deeper gaps in leadership accountability.
Solution: Treat compliance as a floor, not a ceiling. Perform layered process audits that go beyond paperwork. Use third-party gap assessments to stay aligned with evolving standards. Create feedback loops between audit findings and frontline operations so fixes actually stick.
How POWERS Can Help
At POWERS, we believe safety isn’t a separate program, it’s a core indicator of how well your entire operation is running. Gaps in safety often point to deeper issues in execution, leadership accountability, and system reliability. That’s why our approach integrates safety directly into the foundation of Shop Floor Excellence (SFE), not as a compliance obligation, but as a driver of operational performance.
A Systematic Approach to Safer Execution
We start by assessing how safety behaviors are embedded, or missing, within your day-to-day production routines. Using our Digital Production System (DPS), we shine a light on the floor-level activities, coaching gaps, and leadership blind spots that contribute to unsafe conditions and inconsistent execution.
From there, we:
- Map existing workflows to pinpoint where safety breaks down (e.g., rushed startups, skipped inspections, poor PPE enforcement).
- Equip frontline leaders with real-time tools to identify, correct, and prevent unsafe behaviors before they result in injury or downtime.
- Build accountability systems that track safety metrics alongside production metrics, because both matter, and they’re more connected than most leaders realize.
- Coach supervisors and managers to lead safety conversations that actually land, on the floor, not just in the breakroom or training binder.
Let’s Make Safety a Strength, Not a Soft Spot
If you’re seeing too many incidents, too many close calls, or too much variation in how safety is handled from shift to shift, it’s time to act. Our team brings hands-on experience, structured tools, and industry-proven systems to help you get ahead of risk, and stay there.
Contact us at +1 678-971-4711 or info@thepowerscompany.com for a comprehensive solution that aligns your safety practices with the highest standards of Shop Floor Excellence. Let’s work together to build a safer, more productive future in manufacturing.
Continue Reading from this Mastery Series
- Part 1 - The Perils of Overlooking SFE in Assembly Line Setup
- Part 2 - A Lackluster Approach to Shop Floor Excellence Impacts Workforce Engagement
- Part 3 - The Consequences of Sidestepping Data-Driven Decisions in Shop Floor Excellence
- Part 4 - Without Shop Floor Excellence, Product Quality Can Drop Like a Rock
- Part 5 - A Lack of Commitment to Shop Floor Excellence Can Lead to These 10 Safety Issues
- Part 6 - Shop Floor Excellence Makes Your Operation More Agile, Flexible, and Adaptable to Market Changes
- Part 7 - Bridging the Gap with Effective Communication in Shop Floor Excellence
- Part 8 - How Ignoring Shop Floor Excellence Undermines Continuous Improvement
- Part 9 - Tackling Inefficient Energy and Material Use with Shop Floor Excellence
- Part 10 - Enhancing Customer Focus Through Shop Floor Excellence