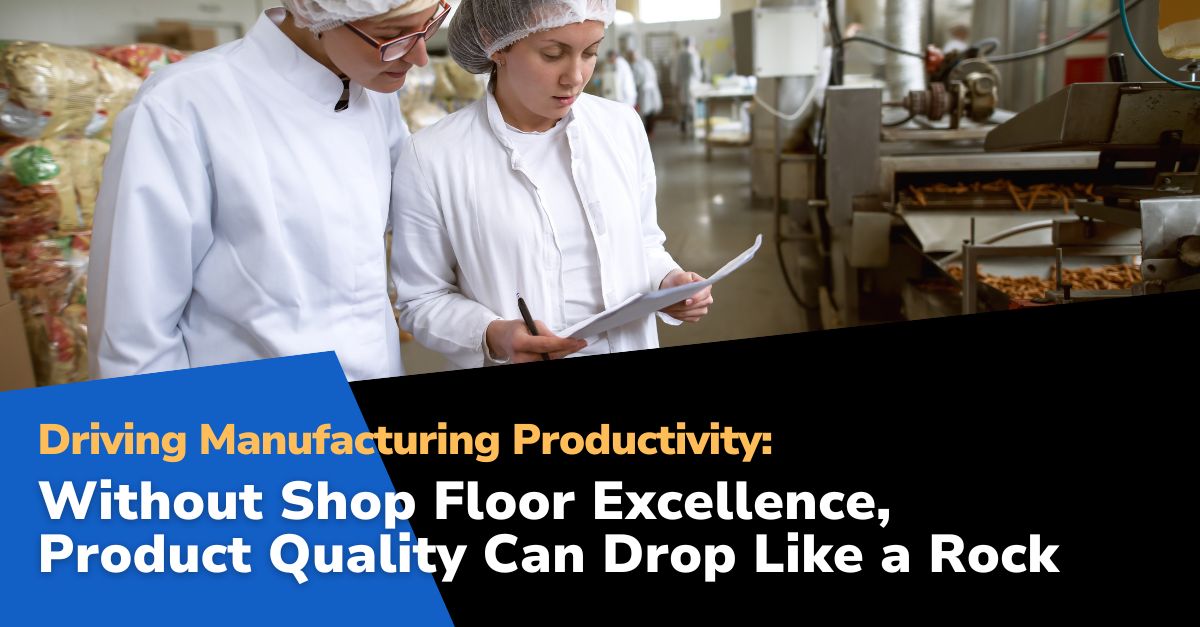
Controlling product quality is a cornerstone in the vast and complex manufacturing world. It’s not just a mere checkpoint in the production process but a critical element that shapes manufacturing operations’ overall success and sustainability. In this context, Shop Floor Excellence (SFE) is pivotal. SFE isn’t just about maintaining product quality; it’s about embedding a culture of excellence right at the heart of the manufacturing process.
The absence of a robust SFE framework can lead to systemic weaknesses in quality control, manifesting in various detrimental ways. These weaknesses affect the immediate product line and can have far-reaching consequences on a company’s market position, competitive edge, and financial health.
In this fourth installment of our insightful series, we delve deeper into understanding the multi-faceted challenges arising from inadequate quality control processes without strong SFE principles. We aim to unravel the complexities of these challenges, offering a clear perspective on their implications and how they intertwine with various aspects of manufacturing operations.
1Increased Defect Rates:
Product defect rates can skyrocket in environments lacking rigorous quality checkpoints and high standards. This increases wastage and necessitates extensive rework, disrupting production schedules and inflating costs.
Solution: Introduce continuous, automated monitoring systems alongside real-time quality inspections to identify and address defects early in production.
2Inconsistent Product Quality:
Product quality can fluctuate significantly without consistent quality control measures, leading to batches of products that fail to meet the required standards. This inconsistency can harm customer trust and lead to the rejection of products in the market.
Solution: Standardize production processes across all lines and apply rigorous, consistent quality benchmarks to ensure uniformity in product quality.
3Customer Dissatisfaction:
Deficiencies in product quality can lead to widespread customer dissatisfaction, evidenced by increased complaints, negative reviews, and a decline in repeat business and brand loyalty.
Solution: Implement a robust system for collecting and analyzing customer feedback and use this data to improve quality control processes.
4Increased Costs:
Poor quality control can escalate costs significantly due to the need for additional materials, labor for rework, and increased warranty claims. These costs can drastically reduce profit margins and affect the company’s financial health.
Solution: Adopt a proactive approach focusing on preventive measures and thorough root cause analysis to reduce the frequency and extent of rework.
5Delayed Time-to-Market:
Quality issues can lead to production delays as teams scramble to fix problems, causing missed deadlines and delayed product launches, leading to lost market opportunities and revenue.
Solution: Seamlessly integrate quality checks into the production timeline, ensuring they do not cause bottlenecks but enhance the process.
6Non-Compliance with Standards:
Failing to comply with industry-specific standards and regulations can result in legal issues, financial penalties, and loss of certifications, which can harm a company’s standing in the market.
Solution: Regularly update and rigorously align manufacturing processes with current industry standards and regulatory requirements.
7Reduced Market Competitiveness:
Inferior product quality can significantly weaken a brand’s position in the market, making it less competitive against rivals who maintain higher quality standards.
Solution: Implement ongoing benchmarking against industry leaders and embrace continuous improvement practices to maintain a competitive edge.
8Higher Return and Recall Rates:
An uptick in product returns and recalls can strain a company’s financial resources and damage customer trust, which is often hard to rebuild.
Solution: Strengthen pre-market testing and implement rigorous quality validation processes to identify and mitigate potential issues before products reach the market.
9Waning Employee Morale:
Persistent quality issues can demotivate employees, leading to decreased productivity, increased turnover, and a culture that does not prioritize quality.
Solution: Foster a workplace culture that values quality and involves employees at all levels in quality improvement initiatives, recognizing and rewarding their contributions.
10Brand Reputation Damage:
Continual quality failures can lead to a long-term negative perception of the brand, affecting customer loyalty and the ability to attract new business.
Solution: Ensure consistent delivery of high-quality products and actively communicate these quality standards to rebuild and maintain a strong brand reputation.
Addressing these challenges head-on with SFE principles enhances product quality and contributes to the overall health and success of the manufacturing operation.
Elevating Quality with The POWERS Approach
At POWERS, we recognize that quality control is the linchpin of manufacturing success. Our approach to integrating Shop Floor Excellence in quality control processes is designed to systematically identify and resolve quality issues, ensuring that your products consistently meet or exceed customer expectations.
Transform your approach to quality control with POWERS.
Our team is ready to guide you through implementing effective shop floor excellence strategies, elevating your product quality, and enhancing your market position.
Contact us at +1 678-971-4711 or info@thepowerscompany.com for a comprehensive solution that aligns your quality control processes with the highest standards of Shop Floor Excellence. Let’s work together to build a legacy of quality in your manufacturing operations.
Continue Reading from this Mastery Series
- Part 1 - The Perils of Overlooking SFE in Assembly Line Setup
- Part 2 - A Lackluster Approach to Shop Floor Excellence Impacts Workforce Engagement
- Part 3 - The Consequences of Sidestepping Data-Driven Decisions in Shop Floor Excellence
- Part 4 - Without Shop Floor Excellence, Product Quality Can Drop Like a Rock
- Part 5 - A Lack of Commitment to Shop Floor Excellence Can Lead to These 10 Safety Issues
- Part 6 - Shop Floor Excellence Makes Your Operation More Agile, Flexible, and Adaptable to Market Changes
- Part 7 - Bridging the Gap with Effective Communication in Shop Floor Excellence
- Part 8 - How Ignoring Shop Floor Excellence Undermines Continuous Improvement
- Part 9 - Tackling Inefficient Energy and Material Use with Shop Floor Excellence
- Part 10 - Enhancing Customer Focus Through Shop Floor Excellence