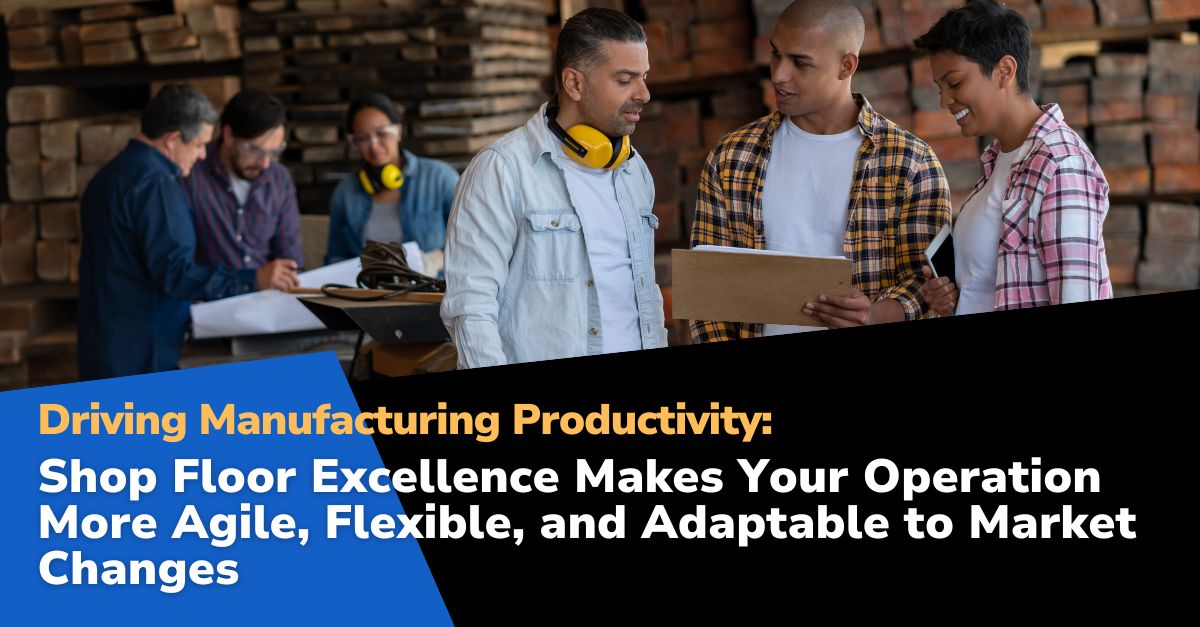
Adaptability and innovation are critical for success in the rapidly evolving manufacturing world where market changes are an everyday fact. However, a common barrier to progress is resistance to change, particularly in environments where Shop Floor Excellence (SFE) isn’t fully embraced.
This resistance, often rooted in a preference for the status quo and apprehension about new methodologies, can significantly hinder a manufacturer’s ability to stay competitive and responsive to market changes.
In this sixth installment of our series, we tackle the top 10 manifestations of this resistance in manufacturing and demonstrate how applying SFE principles can effectively overcome these challenges.
We aim to show that by integrating SFE into their operations, manufacturers can transform their approach to change, fostering an environment ripe for innovation and growth. This exploration is about identifying obstacles and unlocking the potential for dynamic, forward-looking manufacturing practices.
1Reluctance to Adopt New Technologies:
Manufacturers may avoid new technologies due to costs, perceived complexity, or disruption fears, risking obsolescence and inefficiency.
Solution: Introduce a phased technology adoption plan, beginning with pilot programs. Provide comprehensive training and support, and communicate the long-term efficiency gains and ROI to encourage buy-in.
2Inflexible Production Processes:
Fixed production lines may be unable to accommodate product variations, limiting responsiveness to customer demands and market changes.
Solution: Invest in flexible manufacturing systems (FMS) that can be quickly reconfigured for different products. Apply lean manufacturing principles to streamline changeovers and reduce downtime.
3Slow Response to Market Trends:
Delayed reactions to market shifts can result in missed opportunities and eroded market share.
Solution: Establish a dedicated team for market analysis, integrating insights into strategic planning. Use agile project management to enable rapid deployment of resources in response to market changes.
4Limited Product Development:
A lack of innovative product development can render a manufacturer’s offerings outdated, failing to meet evolving consumer needs.
Solution: Foster a culture of innovation through regular brainstorming sessions, encouraging cross-departmental collaboration. Allocate resources for R&D and prototype development.
5Inefficient Problem-Solving:
Traditional problem-solving methods might not effectively tackle complex modern manufacturing challenges, leading to persistent issues.
Solution: Implement systematic problem-solving methods like Six Sigma and root cause analysis. Encourage employees to think outside the box and propose innovative solutions.
6Low Employee Engagement in Innovation:
Employees may lack motivation to innovate, resulting in a stale and uncreative work environment.
Solution: Create an innovation incubator program where employees can submit and develop their ideas with organizational support. Recognize and reward innovative contributions.
7Poor Adaptation to Regulatory Changes:
New or changing regulations can be one of the harshest market changes. Failing to adapt to new regulations quickly can lead to legal issues and operational disruptions.
Solution: Form a compliance task force to monitor regulatory changes and assess impacts. Train employees regularly on compliance matters and integrate adaptive processes.
8Inadequate Training and Skill Development:
Employees without skills in new technologies and methodologies hinder a company’s ability to evolve and innovate.
Solution: Offer continuous learning opportunities, including workshops, seminars, and online courses—partner with technology providers for specialized training.
9Failure to Leverage Data Analytics:
Underutilization of data analytics results in missed insights and suboptimal decision-making.
Solution: Invest in advanced data analytics platforms and train staff in data interpretation. Establish data-driven decision-making as a standard practice.
10Conservative Organizational Culture:
A risk-averse culture can inhibit innovation, preventing the organization from taking necessary leaps to stay ahead.
Solution: Promote a culture that values calculated risks and learning from failures. Set up a system for managing and rewarding innovative risks, even if they don’t always succeed.
By addressing these issues by applying SFE principles, manufacturers can break down barriers to change and innovation, paving the way for a more agile, forward-thinking, and competitive manufacturing environment.
Embracing Innovation with The POWERS Approach
At POWERS, we recognize the importance of embracing change and fostering innovation in the manufacturing sector.
Our strategic approach integrates the principles of SFE to help manufacturers overcome resistance to change, promoting a culture of continuous improvement and innovation.
Transform your approach to change and innovation with POWERS. Our team is equipped to guide you through implementing effective strategies that align with SFE principles, ensuring your operations stay ahead in a rapidly evolving industry.
Contact us at +1 678-971-4711 or info@thepowerscompany.com for a comprehensive solution that aligns your manufacturing processes with the forefront of innovation and change management. Let’s work together to drive your manufacturing productivity to new heights.
Continue Reading from this Mastery Series
- Part 1 - The Perils of Overlooking SFE in Assembly Line Setup
- Part 2 - A Lackluster Approach to Shop Floor Excellence Impacts Workforce Engagement
- Part 3 - The Consequences of Sidestepping Data-Driven Decisions in Shop Floor Excellence
- Part 4 - Without Shop Floor Excellence, Product Quality Can Drop Like a Rock
- Part 5 - A Lack of Commitment to Shop Floor Excellence Can Lead to These 10 Safety Issues
- Part 6 - Shop Floor Excellence Makes Your Operation More Agile, Flexible, and Adaptable to Market Changes
- Part 7 - Bridging the Gap with Effective Communication in Shop Floor Excellence
- Part 8 - How Ignoring Shop Floor Excellence Undermines Continuous Improvement
- Part 9 - Tackling Inefficient Energy and Material Use with Shop Floor Excellence
- Part 10 - Enhancing Customer Focus Through Shop Floor Excellence