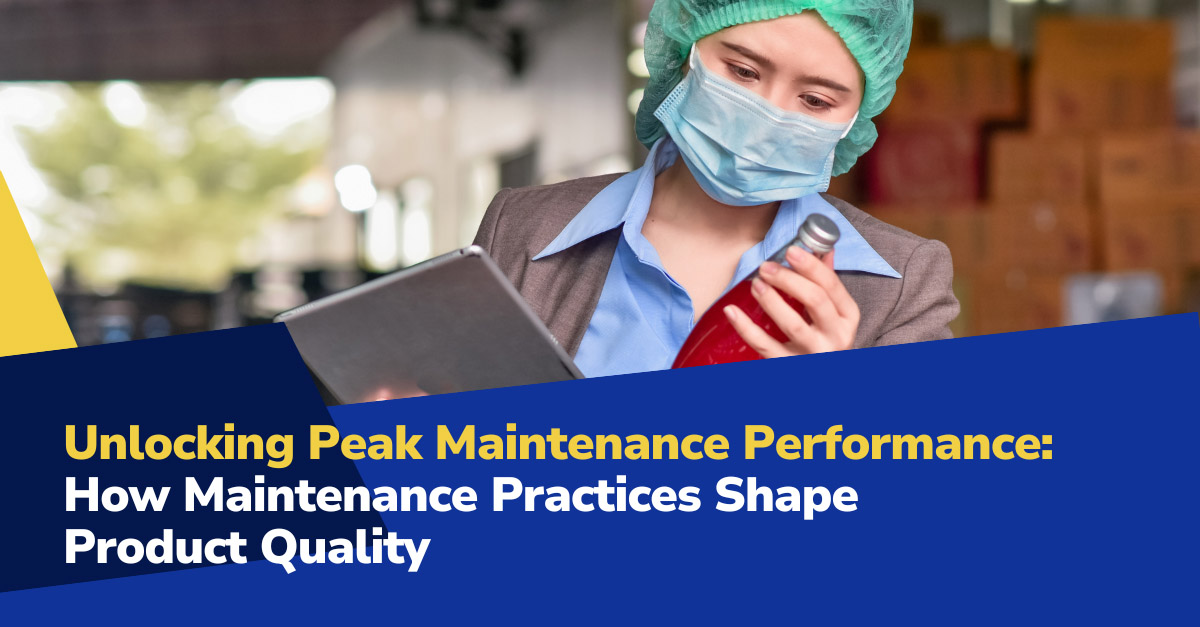
In manufacturing, the quality of the finished product is what ultimately defines your performance. You can have fast machines, high throughput, and plenty of automation, but if what you’re producing doesn’t meet standards, your customers won’t care how efficient the process was.
While Overall Equipment Effectiveness (OEE) gives you a useful view of availability, performance, and quality, it doesn’t always capture the slow creep of quality decline tied to poor maintenance. That impact often flies under the radar, until defect rates rise, complaints increase, or customers start walking away.
If you’re seeing more out-of-spec parts, rising rework, or inconsistencies in inspection data, it’s time to ask: Is your maintenance system protecting your product quality, or quietly undermining it?
Let’s break down 10 specific ways weak maintenance practices damage quality, raise costs, and put customer relationships at risk.
1Increased Defect Rates:
Precision matters. When machines aren’t properly aligned, calibrated, or maintained, tolerances slip. That leads to visible defects, burrs, warping, incorrect dimensions, or hidden problems that only show up in the field. Over time, defect rates can double, especially when wear-and-tear issues go unresolved.
And here’s the kicker: These failures often don’t show up in reports until scrap piles start growing.
2Elevated Rework Costs:
Rework might feel like a fix, but it’s expensive, time-consuming, and inefficient. When machines aren’t running right, more units need to be reprocessed, remanufactured, or manually corrected. It’s not just the cost of labor, it’s also the opportunity cost of lost capacity.
Over a year, elevated rework can silently eat into margins, drive up lead times, and keep operators in reaction mode instead of continuous flow.
3Spike in Recall Incidences:
When maintenance issues slip through and make their way into shipped products, the result can be a costly recall. Whether it’s a packaging defect, a faulty seal, or a miscalibrated blend, even a small deviation can lead to big brand damage. Recalls not only carry direct costs, they erode trust and invite scrutiny.
If your quality team is catching more issues after shipping than during production, there’s a deeper issue worth investigating.
4Material Waste Magnification:
Imprecise cuts, excess flash, double-feeds, or temperature swings from faulty equipment can drive waste up fast. Material losses from maintenance neglect aren’t always tracked clearly, but they’re happening. And they can increase scrap and waste by 10–30%, especially in high-speed or multi-step processes.
More waste means more raw material purchased for the same output, and less flexibility in your margins.
5Deterioration of Brand Reputation:
You can’t measure it easily, but it’s real: when quality drops, word spreads. Buyers talk. Distributors notice. Customer confidence erodes. Reputations built over decades can take serious hits after just a few missed shipments or product failures.
Even when issues are caught internally, repeated inconsistencies lead buyers to assume risk, and when customers lose confidence, they start shopping.
6Customer Loyalty Decline:
Quality drives retention. Even your most loyal customers will start testing competitors if your product consistency slips. Late-stage defects, cosmetic blemishes, or functional failures, especially repeated ones, can cause a 5–10% drop in return orders over time. Often, the worst part is not knowing who walked away until it’s too late.
The problem isn’t just one bad batch, it’s the pattern.
7Compounded Warranty Claims:
Products that fail in the field cost more than just repair or replacement. They drain customer goodwill, increase service workload, and often result in internal fire drills. Many of these failures are linked to upstream issues, loose tolerances, component variation, or skipped PMs that would’ve caught problems earlier.
If your warranty claim rate is rising and your maintenance program hasn’t been reviewed in over a year, it’s worth a closer look.
8Extended Cycle Times:
Poor equipment condition doesn’t just create defects, it slows everything down. Operators may be forced to reduce speeds to avoid jams. Line stoppages increase. Troubleshooting becomes routine. Even minor lags can stretch production cycles by 5–15%, putting delivery targets at risk and creating a backlog that ripples through the schedule.
What looks like a planning issue is often a maintenance one.
9Increased Operational Costs:
When defects rise, you spend more everywhere, on materials, labor, inspection, troubleshooting, and reporting. And it doesn’t stop there. Energy consumption typically increases when equipment struggles to perform. So does overtime as teams try to catch up on lost time.
Maintenance issues compound operational costs in ways financial reports don’t always isolate, but experienced plant leaders feel it every day.
10Regulatory Non-Compliance Risks:
When maintenance isn’t prioritized, audits become high-stress events. Missed PMs, uncalibrated gauges, or breakdowns in quality documentation can all trigger violations. Whether you’re in food, pharma, or general manufacturing, compliance gaps due to maintenance shortfalls put production, and credibility, at risk.
You can’t fake your way through a regulatory inspection.
How POWERS Helps Fix It
At POWERS, we’ve seen the link between maintenance and product quality play out time and time again. That’s why our Advanced Maintenance Performance (AMP) program focuses on more than just uptime, it targets the hidden ways maintenance impacts output, cost, and reputation.
We partner with plant and operations leaders to:
- Identify where maintenance gaps are creating quality risk
- Strengthen preventive maintenance schedules and skills
- Tighten alignment between maintenance, production, and QA teams
- Deliver tailored solutions that make frontline execution easier
Get Proactive About Product Quality
Waiting for a problem to show up in your defect rate or recall report is too late. If you suspect maintenance issues are affecting product quality, the time to act is now.
Eager to ensure your product quality remains uncompromised? Download our FREE Maintenance Assessment Guide to start the journey. Reach out to the dedicated POWERS team at +1 678-971-4711 or send an email to info@thepowerscompany.com for an in-depth consultation.
Continue Reading from this Mastery Series
- Part 1 - The Critical Link Between Maintenance and OEE
- Part 2 - How Maintenance Practices Shape Product Quality
- Part 3 - How Poor Maintenance Standards and Practices Impact Schedule Adherence
- Part 4 - How Maintenance Practices Echo Along the Supply Chain
- Part 5 - The Impact of Maintenance on Maximizing Return on Assets (ROA) in Manufacturing
- Part 6 - Poor Maintenance Practices Lead to Out-of-Control Operational Costs
- Part 7 - Navigating the Safety and Compliance Minefield in Manufacturing
- Part 8 - The High Cost of Overlooking Maintenance in Manufacturing Strategic Planning
- Part 9 - Poor Maintenance Practices Are a Hindrance to Technological Innovations
- Part 10 - Overcoming the ‘Reactive’ or ‘Run Till it Breaks’ Pitfall