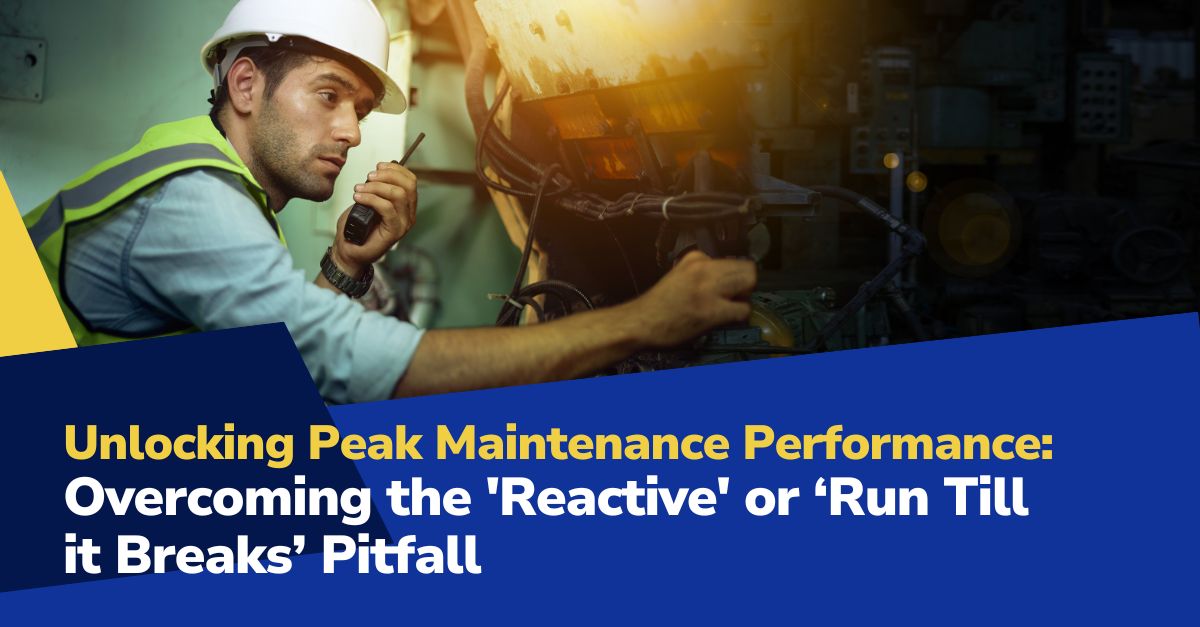
Many manufacturers still rely on a reactive maintenance model, addressing problems only after equipment breaks down. While this approach might feel easier in the moment, it quietly drains time, money, and trust from your operation—and creates avoidable headaches for everyone on the floor.
If you’re tired of costly surprises, missed production targets, and frustrated customers, it’s worth understanding why reactive maintenance is so damaging—and how a proactive and predictive strategy can change the game.
Below are ten critical ways a reactive approach holds your operation back:
The Downfalls of Reactive Maintenance
1Increased Downtime:
When equipment fails without warning, the entire production process grinds to a halt. Lines sit idle, schedules are pushed out, and teams scramble to coordinate emergency fixes. Studies show that unplanned downtime can cost thousands of dollars per hour—and sometimes far more in industries with complex machinery or strict delivery windows.
One example: a Midwest food processor faced nearly 80 hours of lost production in a single quarter due to unexpected conveyor failures. That downtime didn’t just impact the bottom line—it damaged customer confidence for months.
2Higher Maintenance Costs:
Emergency repairs nearly always cost more than planned servicing. You pay premiums for expedited parts, overtime labor, and sometimes specialty contractors. Worse, reactive repairs often create a ripple effect, where one failure stresses other components and leads to secondary breakdowns.
According to research by Caterpillar, repairs after a failure can exceed 65% of the equipment’s value, compared to just 5–25% if you catch problems proactively. Over time, that cost difference can drain budgets meant for innovation and growth.
3Reduced Equipment Life:
When equipment is only fixed after it fails, wear and tear build up unnoticed. Lubrication dries out, seals crack, bearings deteriorate. The result? You replace machinery years earlier than planned, tying up capital in avoidable replacements and upgrades.
For many facilities, proactively maintaining equipment can extend lifespan by 20–40%, translating into millions saved over the long term.
4Safety Risks:
Breakdowns don’t just disrupt schedules—they put employees at risk. When technicians have to rush repairs under pressure, safety protocols can slip. A seized hydraulic system or an overheating motor can trigger serious injuries or near-miss incidents that damage trust and morale.
Unplanned maintenance is consistently linked to higher accident rates and more frequent OSHA recordables. If you’re serious about protecting your workforce, a reactive approach simply isn’t sustainable.
5Quality Compromise:
Unexpected failures mid-production can quickly lead to defects. A malfunctioning press may stamp out hundreds of flawed parts before it’s caught. An unstable mixer could ruin an entire batch of product.
These quality issues drive up scrap rates, increase rework, and erode customer confidence. Even if you catch problems before shipping, the hidden costs still pile up in wasted materials and time.
6Inefficient Use of Resources:
Reactive maintenance ties up skilled technicians in constant firefighting mode. Instead of focusing on continuous improvement, training, or preventive inspections, they spend their days responding to emergencies. That imbalance leads to fatigue, disengagement, and uneven workloads.
It also creates supply chain headaches—because spare parts are ordered ad hoc and often at premium prices rather than being stocked strategically.
7Lower Productivity:
Every unplanned breakdown cuts into throughput. Even small interruptions add up over time, reducing output and pushing your team further behind schedule. In high-volume operations, these delays can mean missing critical targets and disappointing key accounts.
Many manufacturers find that reactive maintenance alone can reduce overall equipment effectiveness (OEE) by 10–20%, enough to impact margins and growth.
8Energy Inefficiency:
When equipment isn’t maintained properly, it often has to work harder to deliver the same output. Motors overheat, bearings drag, belts slip. Over time, this inefficiency drives up energy bills—sometimes by double-digit percentages—and puts extra stress on systems, increasing the likelihood of further breakdowns.
9Compliance Issues:
Regulated industries face unique risks when maintenance is reactive. If an emergency repair disrupts inspection records, calibration logs, or scheduled validations, it can trigger non-compliance penalties or failed audits.
10Customer Dissatisfaction:
Frequent delays, inconsistent quality, and late shipments all chip away at customer trust. Over time, buyers lose confidence in your ability to deliver. They may start exploring competitors who can promise more reliability and consistency.
Rebuilding that trust takes far longer—and costs much more—than maintaining it in the first place.
Making the Shift: Proactive and Predictive Maintenance
Moving away from a reactive approach isn’t easy, but the benefits are undeniable. Proactive maintenance focuses on scheduled inspections and routine servicing. Predictive maintenance goes further, using data, sensors, and analytics to spot problems before they happen.
Here’s how to start:
- Cost Savings: Predictive maintenance, in particular, offers significant cost savings. Regular condition assessments and monitoring can prevent costly breakdowns and extend equipment life.
- Improved Safety and Quality: Regular maintenance ensures equipment operates within safety standards and maintains consistent product quality.
- Resource Optimization: Proactive and predictive maintenance allows for better planning and use of resources, including workforce and spare parts.
- Energy Efficiency: Regularly maintained equipment operates more efficiently, reducing energy consumption.
- Compliance and Customer Satisfaction: Ensuring equipment reliability helps maintain compliance with industry standards and improves customer satisfaction through consistent product quality and on-time deliveries.
Implementing a Shift in Maintenance Strategy
1Assess Current Maintenance Practices:
Understand the proportion of reactive, proactive, and predictive maintenance in your current strategy.
2Cost-Benefit Analysis:
Conduct a detailed analysis of the costs associated with each type of maintenance.
3Tailor the Maintenance Program:
Depending on your industrial activity, choose between centralized or decentralized maintenance approaches.
4Invest in Training, Development, and Tools:
Equip your team with the necessary tactical and technical skills and tools for effective predictive maintenance.
5Monitor and Adjust:
Continuously monitor the effectiveness of your maintenance strategy and make adjustments as needed.
6Leverage Technology:
Use data analytics and IoT devices to predict and prevent equipment failures.
Conclusions for Senior Operations Leaders
Transitioning from a reactive to a proactive or predictive maintenance model requires a strategic shift in mindset and operations. By understanding the pitfalls of a reactive approach and leveraging the benefits of more advanced maintenance strategies, manufacturers can achieve peak maintenance performance, resulting in cost savings, improved safety, and enhanced product quality.
As we’ve seen from industry leaders like the Caterpillar Company, the investment in proactive and predictive maintenance pays dividends in the long run, both financially and operationally.
Embracing Total Productive Maintenance with POWERS AMP Program
The journey to enhanced maintenance practices is transformative, and the concept of Total Productive Maintenance (TPM) plays a pivotal role in this transformation. TPM focuses on proactive and preventive maintenance to maximize the operational efficiency of equipment. It integrates maintenance into the manufacturing process, aiming to eliminate unplanned downtime, increase productivity, and maintain optimal quality.
POWERS, leveraging its vast experience in manufacturing maintenance, offers a holistic solution with the AMP (Advanced Maintenance Performance) program.
This program provides tactical and technical training and development, guiding your maintenance teams from reactive strategies to predictive and ultimately to Total Productive Maintenance (TPM).
Through our Digital Production System (DPS), we provide a structured framework to operationalize your maintenance strategy. DPS makes it possible to:
- Align daily activities with long-term performance targets
- Establish clear accountability across roles and shifts
- Track progress with real-time dashboards and practical metrics
- Create a culture where everyone contributes to continuous improvement
Dive into the POWERS difference. Embark on a journey of maintenance excellence with a detailed Overall Equipment Effectiveness (OEE) analysis, address skill and training gaps, create an actionable plan, and seamlessly implement it. Elevate your maintenance workforce and boost performance with the POWERS AMP program.
For a deeper understanding, download the FREE Maintenance Assessment Guide. Jumpstart your journey to optimized maintenance by contacting the POWERS team at +1 678-971-4711 or email info@thepowerscompany.com. Transform your maintenance practices and witness the tangible impact on your manufacturing operations.
Continue Reading from this Mastery Series
- Part 1 - The Critical Link Between Maintenance and OEE
- Part 2 - How Maintenance Practices Shape Product Quality
- Part 3 - How Poor Maintenance Standards and Practices Impact Schedule Adherence
- Part 4 - How Maintenance Practices Echo Along the Supply Chain
- Part 5 - The Impact of Maintenance on Maximizing Return on Assets (ROA) in Manufacturing
- Part 6 - Poor Maintenance Practices Lead to Out-of-Control Operational Costs
- Part 7 - Navigating the Safety and Compliance Minefield in Manufacturing
- Part 8 - The High Cost of Overlooking Maintenance in Manufacturing Strategic Planning
- Part 9 - Poor Maintenance Practices Are a Hindrance to Technological Innovations
- Part 10 - Overcoming the ‘Reactive’ or ‘Run Till it Breaks’ Pitfall