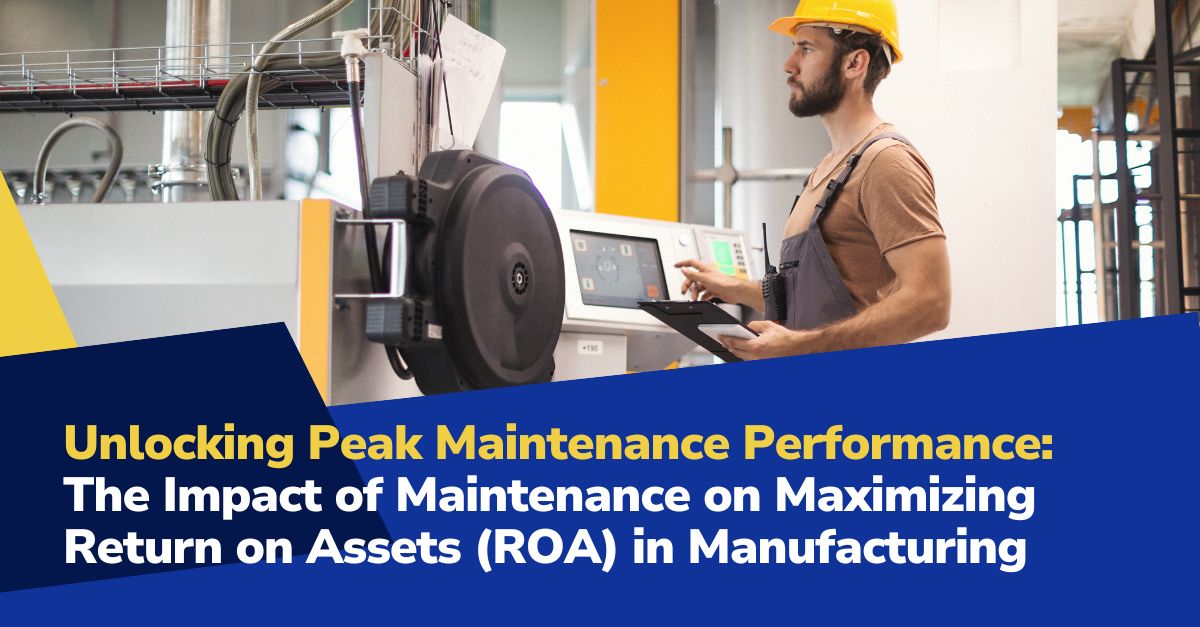
In most manufacturing environments, maintenance is treated as a technical responsibility, something to keep equipment running and avoid unplanned downtime. But in reality, weak maintenance practices silently destabilize operations far beyond the production floor. They disrupt supplier schedules, slow down transportation cycles, inflate inventory costs, and ultimately impact customer satisfaction and revenue.
When maintenance reliability breaks down, so does the consistency of your supply chain. And that inconsistency shows up everywhere.
In this post, we walk through 10 specific ways poor maintenance erodes supply chain performance and how our team at POWERS helps manufacturers strengthen operations at the intersection of equipment reliability and end-to-end fulfillment.
1Supplier Downtime Contagion:
Production equipment that can’t run reliably doesn’t just affect your team it creates upstream bottlenecks. When machines go down, incoming raw materials can’t be processed on schedule, leading to delayed receipts, extra storage costs, or order changes that frustrate suppliers. Over time, this undermines procurement rhythm and damages supplier trust. One plant’s breakdown becomes another plant’s backlog.
2Increased Lead Times:
Extended changeovers, rework, and inconsistent cycle times are common results of poor maintenance. These issues stretch your production lead times by days or even weeks. Procurement and planning teams then struggle to align capacity with demand, often compensating with buffer stock or rescheduling commitments both of which drive up cost and reduce agility.
3Transportation Tangles:
Late-stage maintenance failures often mean missed truckload appointments, delayed shipments, or half-filled containers. These issues add friction to your logistics operation and strain relationships with carriers. When production readiness can’t keep pace with shipping schedules, you wind up paying premiums for last-minute freight or missing delivery windows altogether especially damaging in seasonal or high-volume markets.
4Quality Quarrels:
Equipment that isn’t properly maintained tends to produce more scrap, inconsistencies, and downstream quality defects. When QC teams are constantly reacting to product issues that originated with worn tooling, outdated sensors, or lubrication failures, rework becomes standard and shipments are delayed while teams scramble to correct avoidable problems. The cost? Lost time, customer complaints, and wasted materials.
5Forecasting Frustrations:
Production output should feed your planning model but maintenance instability breaks that link. If your team doesn’t know when a line will go down or how long it’ll take to get back online, production forecasts become guesswork. That guesswork travels downstream into inventory plans, customer order visibility, and financial projections, creating disconnects across departments and reducing operational confidence.
6Inventory Inaccuracies:
Maintenance failures disrupt normal material flow, which leads to reactive decisions around inventory. Teams often overproduce to compensate for downtime risk or fall behind on WIP visibility because machines are running out of cycle. This creates a mismatch between system data and physical stock levels, resulting in stockouts on fast movers and excess buildup on slow turns both of which compromise order fulfillment.
7Customer Commitment Cracks:
Shipments that miss delivery windows or arrive incomplete because of maintenance delays can quickly erode customer confidence. In high-volume or contract-based environments, even one missed shipment can trigger penalties, pricing renegotiations, or a shift in future volume to another supplier. Over time, your brand reputation starts to suffer not because of your product, but because of your predictability.
8Cost Climbs:
Unscheduled maintenance work is rarely budgeted. You’re paying for emergency parts, technician overtime, expediting services, and premium shipping. These reactive costs often don’t show up until the end of the month, but they quietly eat into margin and they’re avoidable. A facility running in reactive mode will always have higher cost-per-unit, and it only gets worse when it spreads across multiple shifts or sites.
9Warranty Woes:
Equipment that isn’t performing to spec often leads to products that don’t either. Small deviations in machine condition alignment, torque, temperature, sensor accuracy can result in premature product failures or hidden defects that customers only discover after delivery. When those problems lead to warranty claims or returns, your operations and supply chain teams get hit again, this time in the form of reverse logistics and reputational cost.
10Compliance Complications:
Industries like food, beverage, pharmaceutical, and aerospace operate under strict compliance mandates. A missed PM, incorrect calibration, or out-of-tolerance result due to maintenance gaps can trigger audit findings, fines, or in worst cases forced line shutdowns. These events don’t just hurt production; they put entire customer relationships at risk, especially when your reliability affects downstream compliance as well.
The POWERS Influence:
Bolstering Supply Chain Resilience Through Maintenance
With a clear-eyed understanding of the profound effects of maintenance on the supply chain, POWERS Manufacturing Productivity Experts have meticulously developed the Advanced Maintenance Performance (AMP) program. This program is meticulously designed to strengthen each link in the supply chain with robust and proactive maintenance practices.
AMP is not just a vision; it is a practical, actionable framework that ensures each element in the supply chain is fortified against the unpredictability of maintenance mishaps.
Through AMP and DPS, we provide a detailed analysis identifying the critical intersections where maintenance and supply chain operations meet, offering specialized training to address these gaps and laying out a comprehensive strategic plan to ensure ongoing resilience and reliability.
It’s time to reinforce the backbone of your supply chain with proactive maintenance. With the POWERS difference, you gain a partner in analyzing the multifaceted ways maintenance shapes your supply network, ensuring each link is robust and reliable.
Are you ready to revitalize your supply chain and guard against the detriments of maintenance malpractice? OurFREE Maintenance Assessment Guide is the first step toward robust reinforcement. Contact our dedicated POWERS team at +1 678-971-4711 or info@thepowerscompany.com for a detailed consultation.
Let’s eliminate maintenance as a hidden threat to your supply chain and turn it into a competitive advantage.
Continue Reading from this Mastery Series
- Part 1 - The Critical Link Between Maintenance and OEE
- Part 2 - How Maintenance Practices Shape Product Quality
- Part 3 - How Poor Maintenance Standards and Practices Impact Schedule Adherence
- Part 4 - How Maintenance Practices Echo Along the Supply Chain
- Part 5 - The Impact of Maintenance on Maximizing Return on Assets (ROA) in Manufacturing
- Part 6 - Poor Maintenance Practices Lead to Out-of-Control Operational Costs
- Part 7 - Navigating the Safety and Compliance Minefield in Manufacturing
- Part 8 - The High Cost of Overlooking Maintenance in Manufacturing Strategic Planning
- Part 9 - Poor Maintenance Practices Are a Hindrance to Technological Innovations
- Part 10 - Overcoming the ‘Reactive’ or ‘Run Till it Breaks’ Pitfall