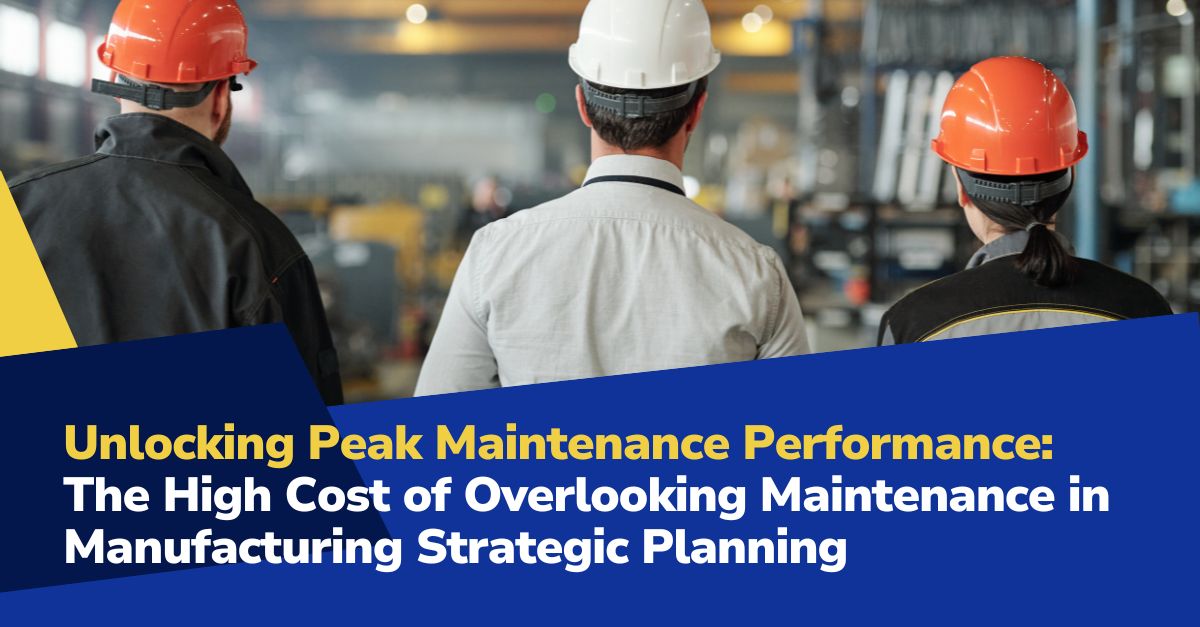
Strategic planning is the backbone of success in manufacturing. But it’s easy for management teams to get caught up in production targets, cost models, and growth objectives—while overlooking the role disciplined maintenance plays in bringing those goals to life.
When maintenance is left out of high-level planning, problems don’t stay hidden for long. They show up on the production floor, in financial statements, and in customer relationships.
This installment highlights 10 ways neglecting maintenance in your strategic plan can set your operation back—and what you can do to avoid it.
1Production Inefficiencies:
Focusing on output without considering equipment health creates a fragile process. Unplanned stoppages, inconsistent performance, and last-minute repairs can disrupt schedules and tie up skilled technicians who could be working on planned improvements. Over time, even small, repeated breakdowns drain throughput and reduce your ability to hit delivery commitments, especially during peak demand periods when uptime matters most.
2Increased Operational Costs:
It costs far more to fix emergencies than to maintain equipment on a predictable schedule. Unplanned repairs often involve premium-priced parts, expedited freight, overtime labor, and extended downtime. When maintenance isn’t budgeted strategically, teams get stuck in a cycle of reacting to problems rather than preventing them driving up costs that squeeze margins quarter after quarter.
3Quality Compromises:
Worn or poorly maintained machinery can’t hold consistent tolerances or produce the same quality output over long runs. This drives up scrap rates, increases rework, and leads to more customer complaints. Over time, chronic quality issues can damage your brand’s reputation and trigger costly warranty claims or lost contracts especially in sectors with tight specifications and compliance requirements.
4Employee Safety Risks:
Equipment failures don’t just hurt output they put employees in harm’s way. Skipping maintenance increases the chances of injuries, near-misses, and safety incidents that impact morale and can lead to regulatory investigations, insurance claims, and legal costs. When workers feel unsafe, engagement drops and turnover rises, creating further operational challenges.
5Regulatory Non-Compliance:
Most regulatory frameworks from OSHA to ISO have clear requirements for documented, scheduled maintenance. When those expectations are sidelined, manufacturers risk not only fines but also damage to certifications and operating licenses. Even minor non-compliance findings can escalate quickly if corrective actions aren’t taken, exposing the business to legal and reputational consequences.
6Technology Lag:
Today’s production technology evolves fast. If maintenance planning doesn’t keep pace, you risk falling behind competitors who regularly upgrade and optimize their equipment. Over time, outdated assets can’t match the speed, accuracy, or energy efficiency of modern alternatives. Proactive maintenance supports both uptime and innovation, helping you stay relevant in a changing market.
7Resource Misallocation:
Without integrating maintenance into your strategic plans, resources end up scattered overstocking parts no one uses, burning labor hours on repetitive fixes, and constantly shifting priorities. This lack of alignment wastes time, inflates budgets, and creates confusion across teams. Clear maintenance strategies help allocate people, materials, and budgets where they’re most effective.
8Inadequate Risk Management:
Every strategic plan needs contingencies and realistic assessments of what can go wrong. Overlooking maintenance creates hidden vulnerabilities like critical spares shortages or unsupported legacy equipment. These risks can trigger sudden, cascading failures that disrupt multiple departments and damage customer trust. Strong maintenance planning helps surface and mitigate these exposures before they escalate.
9Sustainability Setbacks:
Unmaintained equipment typically consumes more energy, generates excess waste, and emits higher levels of pollutants. For companies prioritizing sustainability and ESG goals, routine maintenance is essential for reducing environmental impact and meeting commitments to customers and stakeholders. When these practices aren’t part of the strategy, sustainability efforts lose momentum and credibility.
10Leadership Credibility Loss:
When frontline teams see leadership ignoring obvious maintenance needs, it undermines confidence and engagement. Over time, this disconnect fuels frustration, higher turnover, and skepticism about other strategic initiatives. In contrast, visible support for proactive maintenance sends a clear message that leadership understands what it takes to keep operations running safely and efficiently.
The POWERS Approach:
Integrating Maintenance into Strategic Planning
At POWERS, we know maintenance isn’t just another task on the to-do list it’s a strategic lever that directly drives productivity, safety, and profitability.
Our Advanced Maintenance Performance (AMP) program equips your teams with the structure and support to build a high-reliability maintenance culture.
We work alongside your leaders and frontline teams to:
- Assess current maintenance practices and performance gaps
- Develop realistic, actionable plans to embed maintenance into strategic planning
- Standardize preventive and predictive maintenance schedules
- Establish clear KPIs to track progress and accountability
- Train supervisors and technicians to sustain improvements long term
We also provide DPS, our enterprise productivity platform that integrates maintenance management into a single, transparent system. With DPS, your organization can:
- Consolidate maintenance schedules, work orders, and historical data in one place
- Track real-time equipment performance and downtime trends
- Generate automated reports to support compliance and audits
- Monitor critical spare parts inventory and procurement workflows
- Visualize progress toward your maintenance and operational goals
By combining AMP’s structured approach with DPS technology, we help manufacturers move from reactive firefighting to proactive, data-driven maintenance strategies that align with broader business objectives.
If you’re ready to bring maintenance to the center of your strategy and avoid hidden costs and risks, we’d welcome a conversation.
For a comprehensive assessment and tailored solutions that align your maintenance practices with your strategic goals, contact our dedicated team at +1 678-971-4711 or info@thepowerscompany.com.
Let’s redefine your manufacturing strategy to include the crucial element of maintenance, paving the way for a more efficient, safe, and sustainable future in manufacturing.
Continue Reading from this Mastery Series
- Part 1 - The Critical Link Between Maintenance and OEE
- Part 2 - How Maintenance Practices Shape Product Quality
- Part 3 - How Poor Maintenance Standards and Practices Impact Schedule Adherence
- Part 4 - How Maintenance Practices Echo Along the Supply Chain
- Part 5 - The Impact of Maintenance on Maximizing Return on Assets (ROA) in Manufacturing
- Part 6 - Poor Maintenance Practices Lead to Out-of-Control Operational Costs
- Part 7 - Navigating the Safety and Compliance Minefield in Manufacturing
- Part 8 - The High Cost of Overlooking Maintenance in Manufacturing Strategic Planning
- Part 9 - Poor Maintenance Practices Are a Hindrance to Technological Innovations
- Part 10 - Overcoming the ‘Reactive’ or ‘Run Till it Breaks’ Pitfall