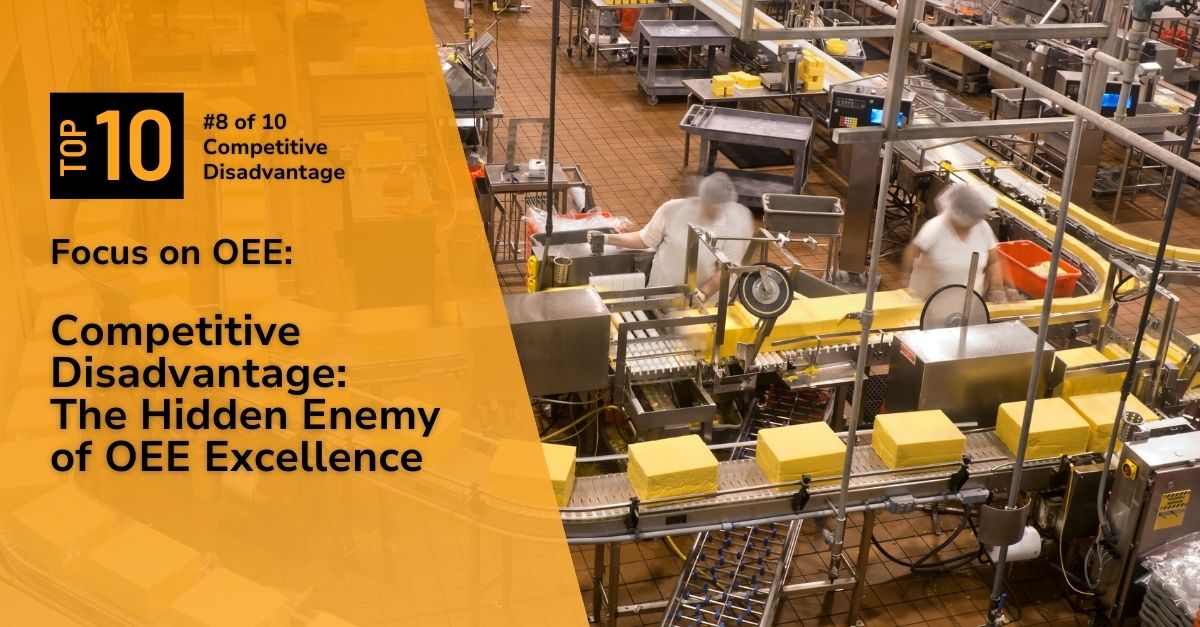
Competitive disadvantages lurk beneath the surface, stealthily eroding your Overall Equipment Effectiveness (OEE) and hindering your journey to operational mastery.
These disadvantages present themselves in subtle, seemingly disconnected issues – a machine that’s slightly slower than expected, minor quality defects that need rework, or schedule changes that happen a bit too frequently.
Consider the problem of inconsistent raw material quality. At first glance, you might be tempted to blame the supplier. However, by consistently tracking OEE and correlating it to material changes, you could uncover a hidden issue: Perhaps your existing equipment can no longer handle the subtle variability always present in a natural raw material. Fueled by data-driven OEE analysis, this realization could prompt an upgrade or modification, rather than simply battling an endless stream of supplier complaints.
This eighth installment of our Focus on OEE Mastery series will expose the top 10 manifestations of competitive disadvantage and their surreptitious secondary symptoms. We’ll provide you with the tools to address the root causes before they escalate.
1Inconsistent Raw Material Quality:
Even subtle fluctuations in raw material characteristics can create havoc on the production line. Equipment may malfunction unexpectedly, cycle times become unpredictable, and waste skyrockets as defective material needs reworking or scrapping. This is a multi-pronged attack on OEE: availability plummets due to stoppages, performance suffers from slower run speeds, and quality scores take a hit.
Mitigation: Proactive supplier management is key. Develop detailed material specifications in collaboration with your suppliers. Implement a rigorous incoming inspection process that verifies chemical composition and physical properties relevant to your processes.
2Sub-optimal Production Scheduling:
Disorganized or reactive scheduling throws your operations into chaos. Excessive changeovers become the norm, starving critical machines of materials, and causing operators to idle while awaiting the next work order. Inefficient scheduling directly lowers OEE availability, decreases performance as changeovers gobble production time, and increases the risk of quality errors in the rush to keep up.
Mitigation: Investing in advanced scheduling software is often worthwhile, especially in complex production environments. These tools help optimize batch sequencing, minimize unnecessary changeovers, and proactively identify potential bottlenecks, leading to higher OEE scores.
3Legacy Equipment with Limited Upgrade Potential:
Outdated machines, pushed beyond their intended limits, struggle to maintain output and are prone to frequent breakdowns. The precision needed for new or complex products may be impossible to achieve. This double-whammy of extended downtime (hurting availability) and poor tolerance control (lowering quality) significantly drag your OEE.
Mitigation: Don’t fall into the trap of always replacing old equipment. Start with a thorough cost-benefit analysis comparing a full replacement with the possibility of a strategic upgrade. Retrofit options, such as adding modern sensors, control systems, or precision tooling, might deliver a surprising boost to both performance and availability, delaying the need for complete machine replacement.
4Lack of Cross-Functional Collaboration:
A siloed mentality, where departments like production, maintenance, and engineering have differing priorities and poor communication channels, leads to cascading failures. Problems take longer to resolve, wasting precious uptime (reduced availability). Stopgap solutions prevail over root cause analysis, impacting machine performance in the long run. Quality can easily become an afterthought in the scramble to keep the line running at any cost.
Mitigation: Break down silos by forming cross-functional teams empowered to tackle challenges with shared ownership. Establish transparent communication channels and align performance goals –including OEE metrics – across departments. Foster a culture where collaborative problem-solving and continuous improvement are celebrated.
5Rigid Production Layouts:
Inflexible production layouts designed around legacy processes often force long travel distances, create bottlenecks that starve machines, and make rebalancing lines for new products painful. These inefficiencies eat away at performance due to wasted time in transit and extended setup times. Availability suffers as operators move materials more and wait for work to flow to their stations. In rushed situations, quality checks might be skipped or performed inadequately under pressure to compensate for delays.
Mitigation: Lean manufacturing principles offer a powerful solution. Start with value stream mapping to visualize your current material flow and identify areas for improvement. Investigate layout reconfigurations for maximum efficiency, potentially even exploring cellular manufacturing if flexibility and fast changeovers are paramount.
6Unclear Changeover Procedures:
When changeovers are poorly documented or rely on tribal knowledge, the amount of time machines sit idle explodes. Errors become more frequent, potentially harming equipment and causing defects in the product. This double-edged sword directly attacks OEE by dramatically reducing availability while opening the door to quality woes.
Mitigation: Standardization is key. Leverage SMED (Single-Minute Exchange of Die) techniques to break down changeovers into discrete steps, identify opportunities for streamlining, and create clear visual work instructions. Continuous training and reinforcement ensure operators have the knowledge to execute changeovers quickly and correctly.
7Outdated Quality Control Methods:
Problem: Relying solely on manual inspections and post-production quality checks leaves your process vulnerable. Defects may slip through undetected, resulting in costly rework, scrap, or even worse – product recalls. These quality failures harm your OEE by reducing yield (thus impacting quality scores). Time is lost to rework, further diminishing availability.
Mitigation: Modernize your quality approach. Implement in-process checks and real-time data collection, enabling you to catch deviations earlier and prevent defects. Statistical process control (SPC) tools empower operators to make proactive adjustments, safeguarding both quality and performance scores.
8Lack of Investment in Automation:
Manually laden processes are inherently less efficient and consistent than automated solutions. Operators get fatigued, leading to mistakes, slower production rates, and potential safety incidents. This translates into decreased overall performance, potential downtime from avoidable errors or accidents, and quality issues stemming from human variability.
Mitigation: Don’t shy away from automating where it makes sense. Identify repetitive, error-prone, or hazardous tasks that are prime candidates for automation. Conduct thorough ROI calculations to evaluate the potential gains in OEE and justify the investment. Start with targeted projects that have a clear and measurable impact.
9Poor Communication of Downstream Customer Needs:
If production is out of sync with true market demand, you risk the twin dangers of overproduction and obsolescence. Excess inventory ties up working capital, while unexpected shifts in demand lead to rushed production changes and potential quality shortcuts. Availability suffers as lines are rebalanced or materials are wasted, while performance takes a hit from the disruptions.
Mitigation: Strengthen your sales and operations planning (S&OP) processes. Invest in reliable forecasting tools and cultivate open channels of communication between your production team and the salesforce. By accurately understanding customer needs, you can proactively optimize your production schedule, which benefits all aspects of your OEE.
10Poor Understanding of Market Trends:
Failure to keep a pulse on evolving customer preferences, emerging technologies, and competitor moves leaves you lagging. Your equipment and processes may no longer be adequate to meet shifting demands, leading to slowdowns and missed quality targets. This directly impacts both performance and quality within your OEE calculation, with the risk of declining customer satisfaction further compounding the issue.
Mitigation: Dedicate resources to market research and competitive intelligence. Regularly assess the alignment between your current capabilities and industry trends. Don’t be afraid to invest in R&D or strategic upgrades that will keep your operations agile in the face of change, helping you maintain a healthy OEE.
Conclusion for Senior Operations Leaders
If ignored for too long, competitive disadvantages create a downward spiral that is difficult to reverse. They erode profitability, hinder growth, and make it increasingly difficult to satisfy your customers. However, the very act of identifying and addressing these disadvantages positions you for operational excellence. By understanding the granular, secondary symptoms that plague your shop floor, you can make targeted improvements that deliver tangible results.
How POWERS Can Help
The challenges associated with competitive disadvantages are multifaceted and often require a holistic approach to resolve. That’s where POWERS can be your trusted partner. Our team of experienced consultants has the deep industry expertise and process knowledge to guide you through the complexities of OEE improvement. We help you:
- Uncover Hidden Root Causes: We go beyond the superficial to pinpoint the true origins of your OEE losses, empowering you to make impactful changes.
- Develop Data-Driven Solutions: We leverage real-time analytics and benchmarking to transform your OEE data into actionable insights and strategic roadmaps.
- Drive Sustainable Change: Our tailored training and implementation support ensures lasting improvements in cross-functional collaboration, problem-solving, and proactive maintenance strategies.
- Speak to an Expert: Call +1 678-971-4711 to discuss your specific challenges and goals.
- Email Us: Get tailored insights by emailing info@thepowerscompany.com
- Request an Assessment: Use our online contact form to schedule an in-depth analysis of your operations.
Continue Reading from this Mastery Series
- Part 1 – The Hidden Costs Undermining Your OEE Score
- Part 2 - Dig Deep to Eliminate Inefficiencies that Silently Sabotage Your OEE
- Part 3 – How Guesswork Kills OEE
- Part 4 – When Nobody Takes Ownership OEE Suffers
- Part 5 – When “Pushing Production” Costs You OEE Points
- Part 6 – The Customer Connection: When Dissatisfaction Drains Your OEE
- Part 7 – Death by a Thousand Cuts: How Wear and Tear Steals From Your OEE
- Part 8 – Competitive Disadvantage: The Hidden Enemy of OEE Excellence
- Part 9 – How Missed Opportunities for Improvement Means Missed OEE Potential
- Part 10 – Is Stagnant Innovation Stagnating Your OEE Results